An innovative and sustainable energy supplywith fuel cells
The future of the fuel cell as the drive system for electrically-powered forklift trucks is looking very promising.
Hydrogen as the drive technology in intralogistics
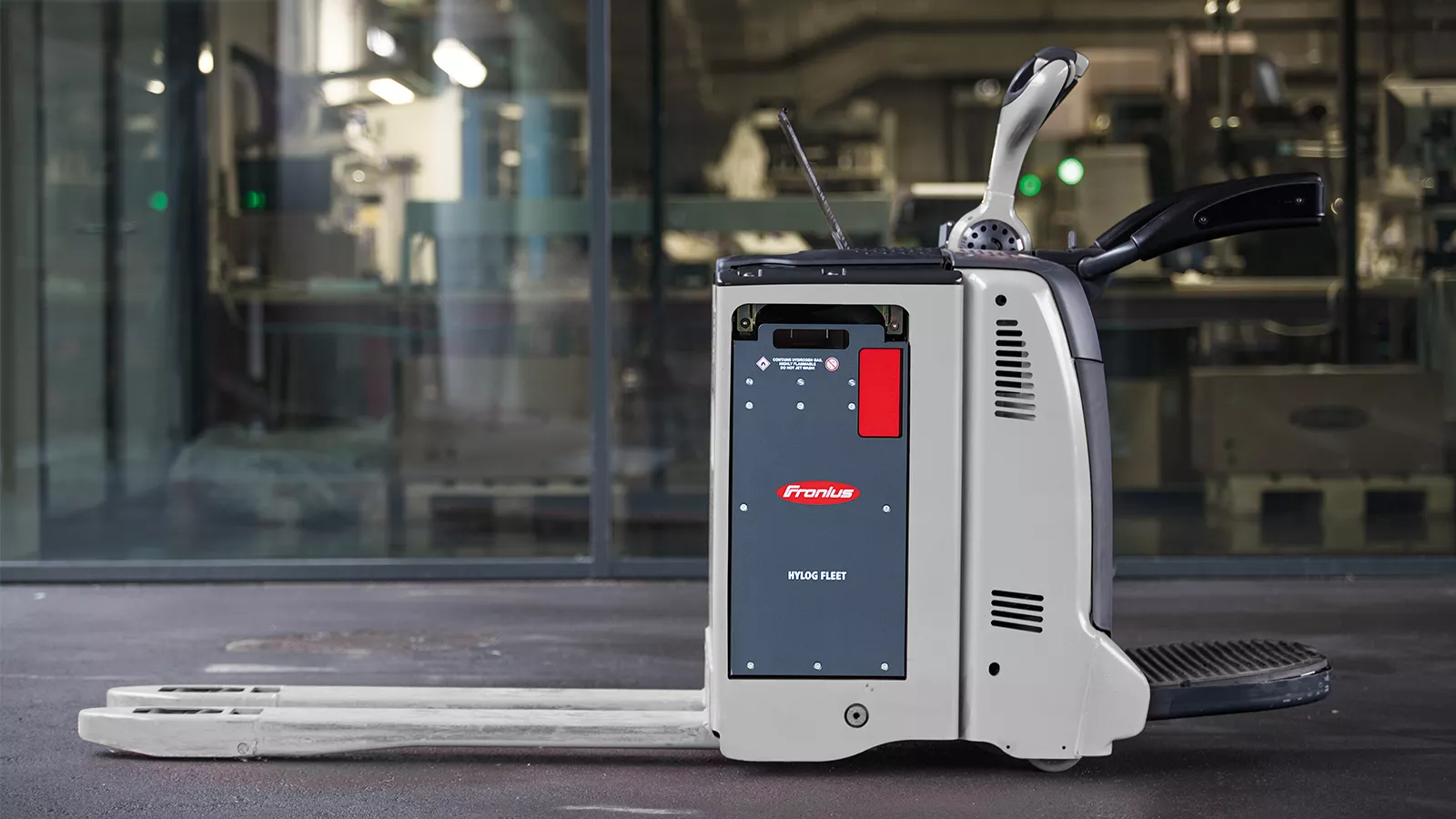
The fuel cell uses atmospheric oxygen to convert the chemical energy from the liquid hydrogen directly into electrical energy, with no intermediate mechanical step. The additional heat that becomes available makes this process extremely efficient. Fuel cells are also lighter than batteries, as well as being reliable, low-maintenance and quiet. Hydrogen can be stored decentrally over the long term in a compact form, and vehicles can refuel in just a few minutes. A further important advantage is that there are zero emissions – the waste product produced by the fuel cell is just pure water.
The fuel cell consists of two electrodes, the anode and the cathode, and an electrolyte membrane. This separates the two electrodes, as well as the gases, but does allow certain ions to be transported through it. The fuel is fed continuously to the anode, atmospheric oxygen to the cathode.
In the chemical reaction, hydrogen ions flow from the anode to the cathode, where they combine with oxygen to make water. This generates direct current with a voltage of as much as 0.7 V per cell. To generate higher voltages, a number of fuel cells are connected in series in what is called a stack. An inverter converts the direct current that is produced into alternating current. The waste heat of the fuel cell is extracted via a cooling circuit and can be used for heating purposes.
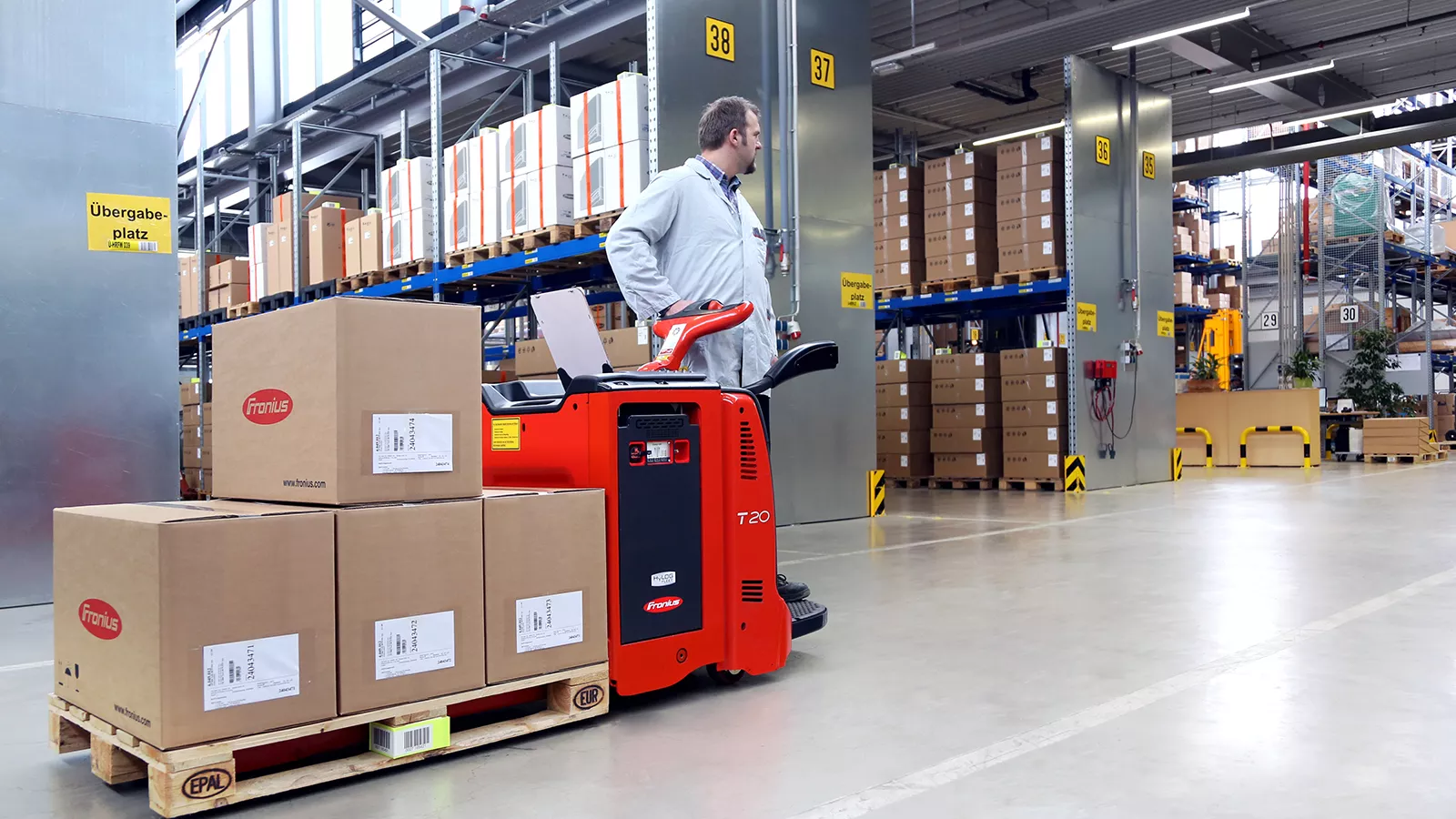
Fronius HyLOG Fleet: taking the lead in fuel cell development
Fronius has been busy developing innovative technologies to make hydrogen a usable energy source for different applications since 2001. We have already successfully implemented a number of incentive projects with major companies and research institutes – and more are planned for the future.
We have developed a fuel cell system for forklift trucks called Fronius HyLOG Fleet. We presented this for the first time in 2011, together with the forklift truck supplier and project partner Linde Material Handling. HyLOG Fleet is currently being used in class 3 forklift trucks, that is, in warehouse equipment with a seat or operator platform. The fuel cell scores highly compared to a battery, and has many advantages: it only takes a few minutes to charge rather than seven to twelve hours, there is no need to set up battery charging rooms and stations and the Fronius HyLOG Fleet also has zero emissions, making it extremely cost-effective and environmentally friendly.
Possible uses for the fuel cell range from forklift trucks for intralogistics operations to construction equipment, agricultural machinery and municipal vehicles. The many advantages of the fuel cell – energy efficiency, zero emissions, easy maintenance and high levels of availability – have already been put to the test in the field.
Reference projects
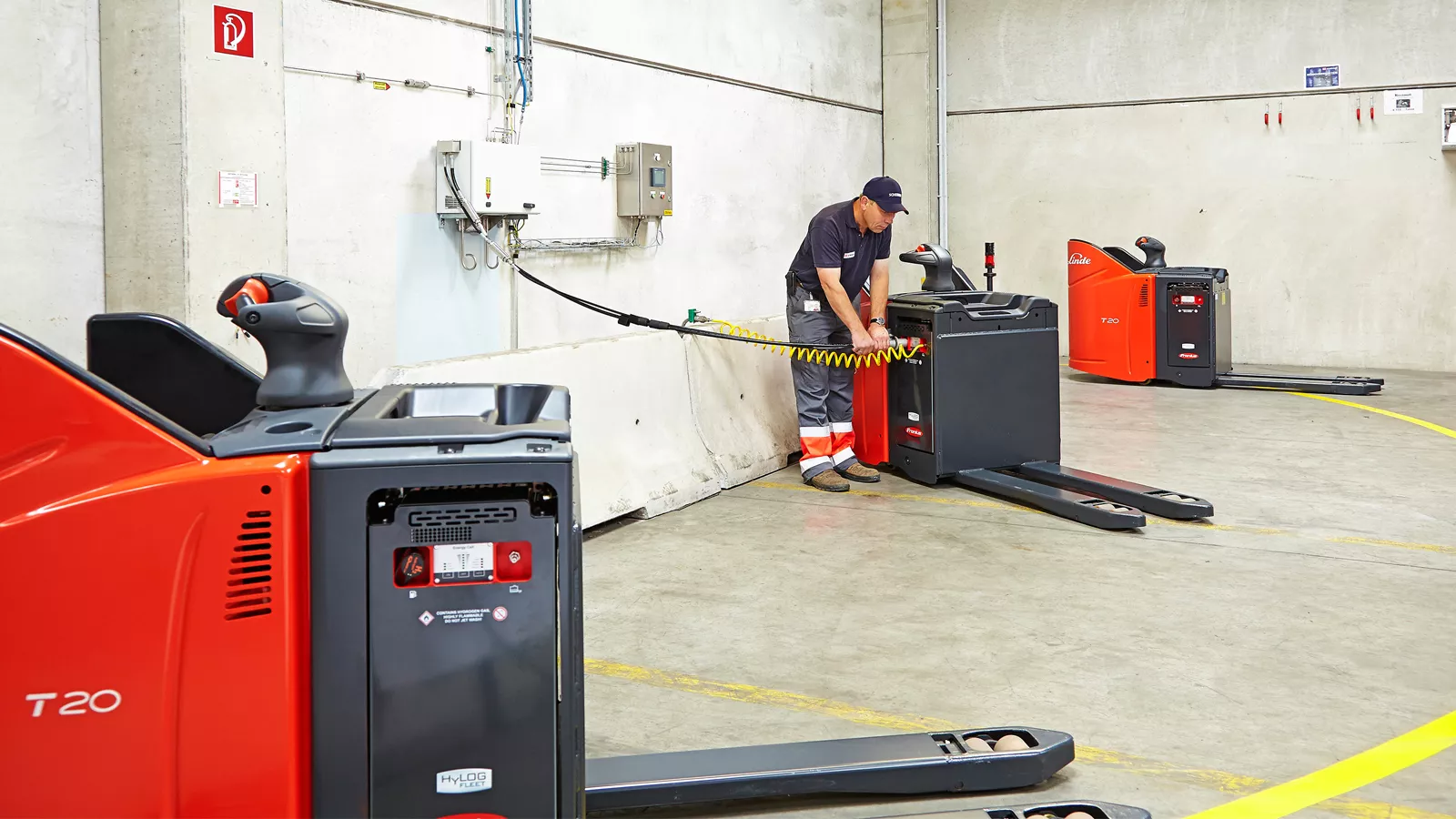
The ten Linde low-lift pallet trucks are each equipped with a Fronius fuel cell hybrid drive. This consists of a hydrogen tank, a 24 V fuel cell that converts the hydrogen into electrical energy and a lithium-ion battery, which stores the generated power and acts as a traction battery. To supply the fleet with fuel, the Austrian energy firm OMV installed the first indoor hydrogen filling station in Europe. The project receives state funding from the Austrian Federal Government’s Climate and Energy Fund.
The aim of the E-LOG biofleet is to increase productivity and cost effectiveness at DB Schenker, while also improving environmental sustainability and energy efficiency. All participants also hope to derive important knowledge from the project that can be incorporated into the development of fuel cells through to series production.
In a pilot project at the OMV site in the Lower Austrian town of Auersthal, a power-to-gas installation was implemented and a high-pressure electrolyser developed to split the water into hydrogen and oxygen by means of wind power. The sustainably generated hydrogen is fed directly into the high-pressure grid of the OMV compressor station at Auersthal. This allows flexibility in storing the gas and transporting it to the consumer.
Keeping technical and legal approval aspects in mind, all the project partners are carrying out tests to establish the best way to feed the renewable hydrogen into the natural gas network and to find the ideal transport solution for filling up with and using hydrogen. In conjunction with the legal, commercial and ecological evaluations of the Energy Institute, the companies want to create the foundations for an extended rollout of this innovative technology.
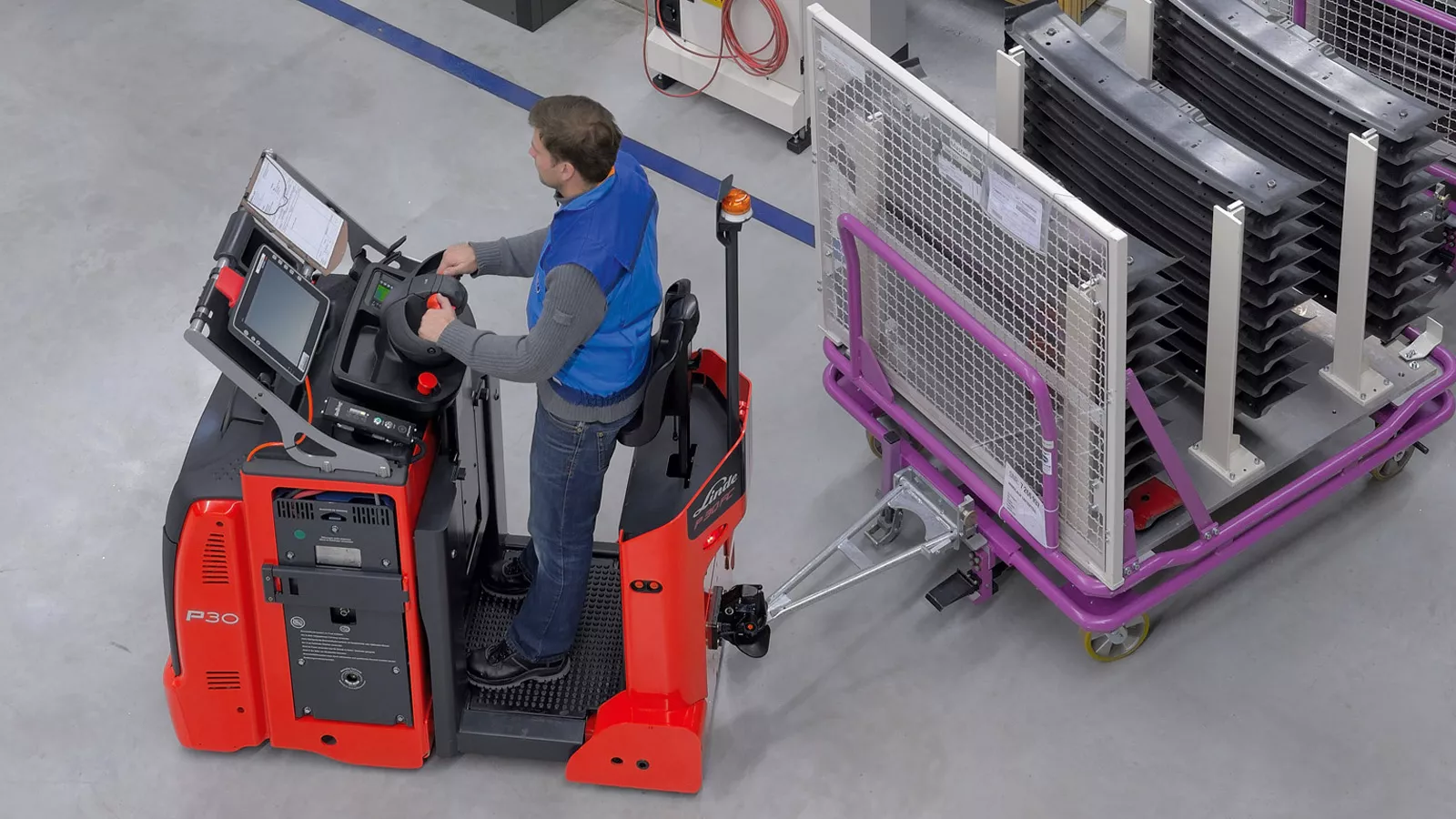
The aim of the H2IntraDrive project was to investigate the resources required for hydrogen-powered forklift trucks under real operating conditions. This was initiated by the Institute for Materials Handling, Material Flow and Logistics at the Technical University of Munich together with the BMW Group and Linde Material Handling. The automotive manufacturer had made its production facility in Leipzig available for the project. The tests involved multiple counterbalanced lift trucks and tow tractors.
For H2IntraDrive, Fronius equipped two Linde P30 tow tractors with its innovative HyLOG Fleet fuel cell technology. The system consists of a hydrogen tank, a 24 V fuel cell that converts the hydrogen into electrical energy and a lithium-ion battery, which stores the generated power and acts as a traction battery. BMW also set up the first indoor filling station for hydrogen-powered vehicles in Germany, so that the vehicles could refuel directly on the factory floor.
The company hopes that the project will lead to the long-term optimisation of its intralogistics operation. The H2IntraDrive project also allowed the scientists to collect valuable knowledge about the energy requirements, fuel range, service life and handling of the forklift trucks, which will be of massive benefit for the further development of fuel cell technology.
Together with project partners LADOG, ElringKlinger, Heinzmann and the Fraunhofer Institute for Solar Energy Systems (ISE), Fronius is developing an electric powertrain for work and commercial vehicles – ELAAN for short. Its uses include municipal logistics, horticulture, road construction, waste disposal, snow-clearing and municipal cleansing services. Here an electric motor ensures reliable, quiet, low-emission and energy-efficient operation.
The high energy requirement of the vehicles is covered by a zero-emission fuel cell range extender combined with a battery acting as a power and energy store. A hydrogen storage tank at up to 350 bar ensures the required fuel range for the vehicle and a high level of availability, as refuelling takes less than three minutes. The ELAAN project will use prototypes to collect valuable knowledge about the everyday capabilities of this innovative drive system.