30/05/2021 / Milton Keynes
Blog
Faster charging: Choosing the right technology for your company
Time is money – an efficient design of the battery
charging technology is therefore crucial in intralogistics. Lithium-ion
technology is playing an increasingly important role, however, in the lead-acid
world, opportunity charging can lead to more speed. As an independent energy
expert, we support you in finding the best charging solution for your
operation.
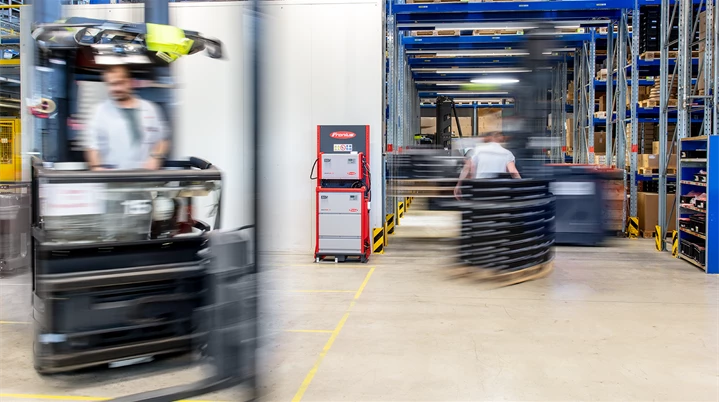
The special
features of charging lead-acid and lithium-ion batteries form the basis for our
optimisation offer, which we provide to our customers. Together with you, we
design your best possible charging solution, which is optimally matched to your
application.
Lead-acid batteries | Lithium-ion batteries |
Due to the longer charging time, back-up lead-acid batteries are required in multi-shift operations. The battery must be removed from the forklift truck in order to charge it. | The charging process in multi-shift operations is determined by frequent fast and opportunity charging of the lithium-ion battery (e.g. during the lunch break). The lithium-ion battery remains in the forklift truck. |
The charging infrastructure is centrally located at the site. | The charging infrastructure is placed in decentralised locations along the flow of goods. |
Lead-acid batteries require maintenance (e.g. the forklift battery must be regularly refilled with demineralised water). | Lithium-ion batteries are virtually maintenance-free. |
An exhaust system is required, as the electrolysis of lead-acid batteries produces oxyhydrogen gas. | Lithium-ion batteries do not produce dangerous gases. |
The charging process for lead-acid batteries is specified by the battery charger via the charging characteristic. | Lithium-ion batteries have a battery management system (BMS) - for communication between battery and charger, a CAN protocol (Fronius BatteryLink) must be implemented. |
Functions to optimise charging (such as Air Pulse, temperature-controlled charging, Power Charging, etc.) are controlled by the charger. | The BMS is responsible for monitoring all parameters in the lithium-ion battery. With our BatteryLink, we ensure optimal communication with the charging system. |
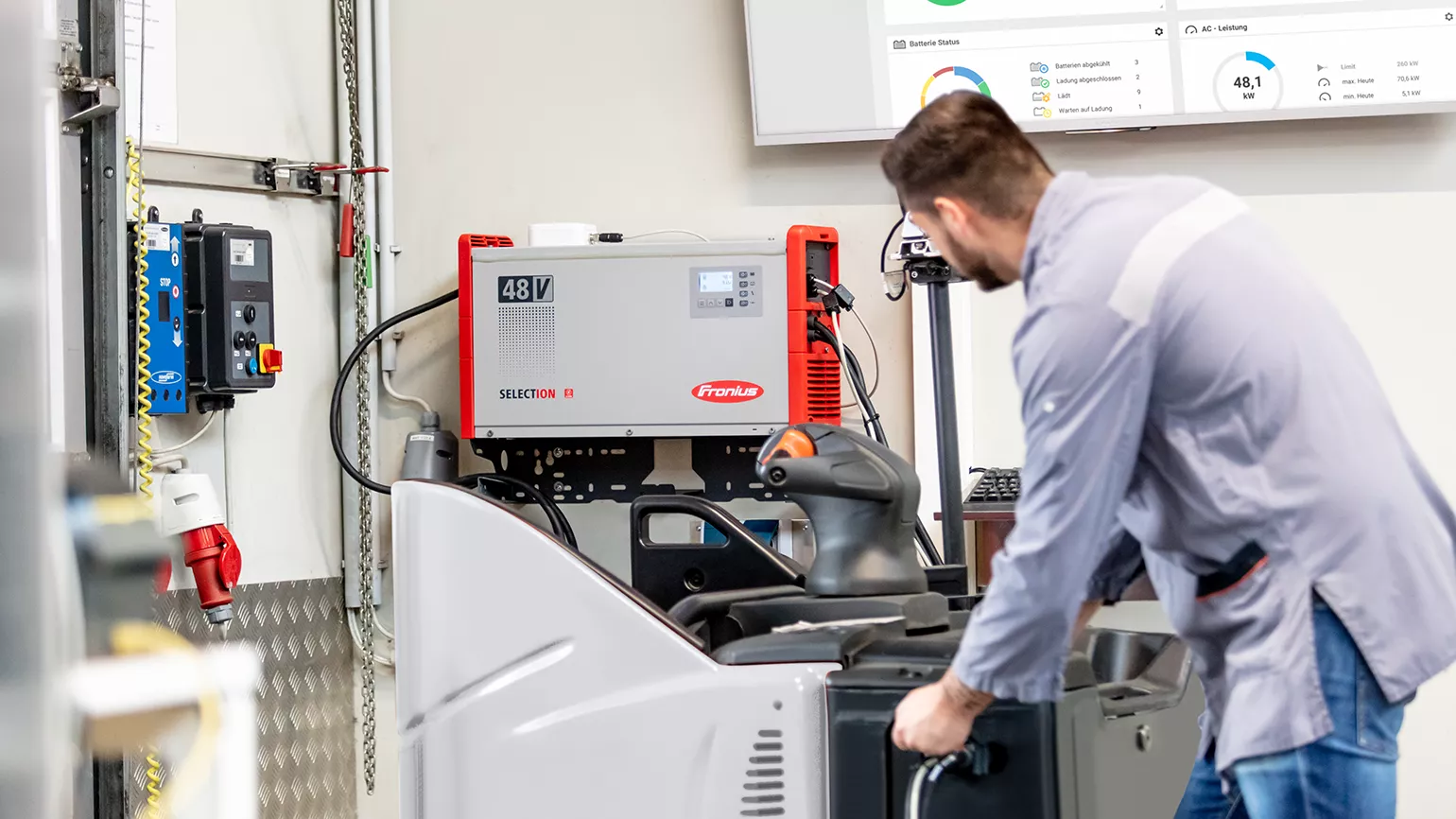
Forklift truck getting connected to the SelectION lithium-ion battery charger.
Keep charging, stop changing. Unlike lead-acid batteries, lithium-ion batteries remain directly
in the forklift truck during the charging process and are charged via a plug
connection. The charging process in multi-shift operation is characterised by
frequent fast and opportunity charging of the lithium-ion battery - for example
during the lunch break. Removal of the battery from the forklift truck - as is
the case with lead-acid batteries - is not necessary. The required charging
infrastructure for lithium-ion batteries can therefore be placed flexibly and
in a space-saving manner along the flow of goods. In combination with our
flexible EnergyHub,
you can also relocate the charging process to the outside area, thus providing
additional space and safety.
Safe and stable CAN communication. With lithium-ion batteries, the charging process is largely controlled by the battery management system (BMS). In order for the charger to communicate safely with the battery, a CAN protocol is required. The Fronius BatteryLink was developed specifically for this purpose. Operators of electrically powered forklift trucks can use it to seamlessly integrate lithium-ion traction batteries into their workflows and optimise existing processes. With Fronius BatteryLink, "plug & charge" becomes reality. After implementing the communication protocol, all you need to do is drive your forklift truck to the charging station, plug it in and start charging. Through an automatic baud rate detection, the charger adapts individually to your lithium-ion battery. The intelligent battery charger automatically detects the battery voltage as soon as it is connected, no additional settings are necessary.
Fast charging in the lead-acid world. Lead-acid batteries are particularly suitable for single-shift operations or for companies with sufficient time for charging, changing and maintaining the forklift battery. As orders increase and the forklift fleet grows, operations usually respond with adjustments and changes to the charging process (e.g., back-up lead-acid batteries can be purchased for multi-shift operations). Our Selectiva 4.0 chargers offer an innovative solution for fast or opportunity charging of lead-acid batteries. The Power Charging Option supplies lead-acid batteries with energy in a short time and thus helps you to manage temporary workload peaks or the changeover to multi-shift operation.
Depending on the
application, it should be checked whether a change of technology is reasonable
for your company. Contact us, we will support you in developing your ideal
battery charging solution!
Versatile and safe – our SelectION lithium-ion chargers
With our SelectION lithium-ion chargers we offer a safe, efficient and flexible charging solution for lithium-ion batteries.