スマートなロボット溶接技術により未来に適応
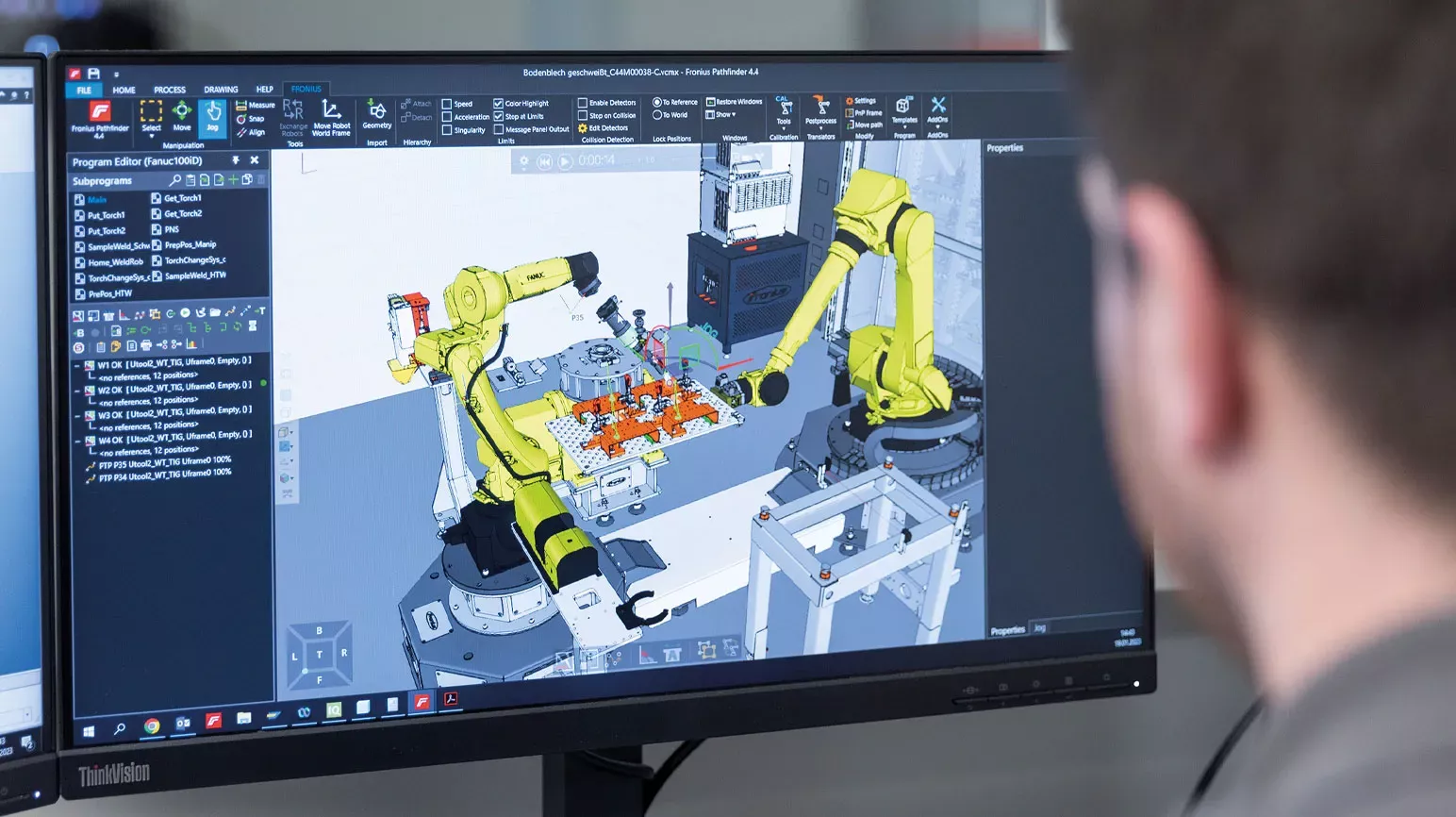
これまで、オーストリアのグラーツでアントンパール社が製造する測定および制御装置のすべての機器や部品は手作業で溶接されてきました。これは、ロボット溶接システムは1個~400個までの小バッチ規模の溶接に関しては環境負荷が高いと見なされていたからです。しかし、売り上げの増大が続く一方で国内雇用市場の熟練作業者がますます不足し、現在では小バッチでも環境に負荷をかけずに自動溶接を行えるようになった革新的なロボット技術が台頭してきたことで、ハイテク企業である同社は最先端のロボット溶接システムへの投資を行うに至りました。また、Anton Paarの測定・制御スペシャリストはライン全体で柔軟性があり、高い費用対効果も併せ持つソリューションを必要としていました。具体的には、部品の個数、形状、大きさを問わず、また位置、そしてさまざまな溶接プロセスで柔軟に使用できる必要がありました
Anton Paar GmbHのCOO、Dominik Santner氏は次のように述べています。「熟練作業者の不足と増え続ける生産量により、生産において新しいソリューションが求められています。そのため、この新しいロボット溶接セルは、当社の製造過程で自動化を進めるに当たってとても大きな一歩と言えます。プロセスセンサーを従来のように手動で溶接した場合、今後数年間に計画された数量を達成するのに大きな困難に直面するでしょう。」
自動システムでさまざまな部品を溶接可能
Anton Paarのエキスパートたちが最初から強調していたのはシステムの自動化でした。溶接システムは、設定完了後、初めから終わりまで全ての工程を一度で処理できなければなりませんでした。例えば、オシレータハウジング、主搬送波、向流冷却器など、異なるオブジェクトのバッチを溶接する場合です。また、これを完全に独自で、溶接技能者の介入なしに行える必要がありました。
エンジニアリングチームとプログラミングチームにとってデザインシステム設計を特に困難にする要素も多く存在していました。具体的には、部品の形、重さ、大きさの違い、グリップ、位置、保管容量が別々だったり、二種類の溶接プロセス(TIGおよびMIG/MAG)を一つの部品で使用できるかどうか等です。また、部品を色褪せから守るための成形ガスを使えるかどうかも、円筒形の物体を処理する上で懸念されていました。
「私たちは、精度と品質に関して同じ基準を持つ、信頼できるパートナーを探していました。私たちの声に真剣に耳を傾け、要望に応え、持続可能なソリューションを提案できる存在が必要だったのです。つまり、今後何年にわたって競合力をもたらすことのできるパートナーです。」と、溶接技術部部長であるDaniel Moik氏は説明します。「Fronius Internationalは持続可能なパートナーシップという点でこれらの基準を満たしていました。そして、Froniusの溶接自動化チームは私たちの技術者と密接に協力し、私たちの要望を全方向から叶えるロボット溶接セルを開発しました。何よりも、フロニウスには私たちと手を取り合ってシステムを進化させ、新しいニーズに応用する準備ができているのです。」
効率性の代名詞とされる: Fronius Pathfinder
溶接は一般的にはシステム上で直接作業されますが、Anton Paarでは、新しい溶接作業は溶接システムを経由せず、直にプログラミングされています。現在進行中の溶接作業を停止するのではなく、作業をプログラミング中も続行することで生産性を上げることができます。溶接工は、測定機器部品のCADデータを取り込み、Fronius Pathfinder®で溶接作業が行われるように条件を作成します。その後、さまざまな接合シナリオのテスト、溶接シーケンスの定義が行われ、シミュレーション中に最適化されます。
シミュレーション中には、開始点、溶接トーチの角度、隅部分のトーチオフセット、そして溶接ロボットの再配向もすべて考慮されます。また、Pathfinderによって、ロボット範囲がどこで超過されるか、つまり軸限界についての実例が識別されます。そして、ソフトウェアオペレータによって加工対象物の保管場所が修正され、溶接ロボットのアームが届く範囲に配置されると、トーチとさまざまな部品の角の衝突を早い段階で回避できるようになります。
エラーの原因をタイムリーに特定
工程を修正する必要が生じた場合、影響を受けるティーチング点の移動はドラッグアンドドロップで簡単に行えます。部品へのアプローチに変更が必要な場合も、「リセット」ボタンを押すだけです。すると、仮想ロボットがホーム位置に移動し、新しいアプローチランを開始します。現実の条件下では、ロボットを引き戻したり、ロボットコントローラでホーム位置に移動させたり、ティーチングプロセスを再開したりと、時間のかかるプロセスを行う必要があるでしょう。しかし、Pathfinderのオフラインプログラミングとシミュレーションソフトウェアを活用することで、Anton Paarの専門家たちは貴重な時間を溶接に集中させられるだけでなく、エラーの原因を事前に特定できます。
Pathfinderに溶接プログラムが設定されると、いわゆる「ポストプロセッサー」により、Fanuc溶接ロボットの特定のコードに翻訳されます。その後、例えばLAN接続などのデータ伝送システムによって溶接システムに転送されます。製造計画全体に効果的なサポートをもたらす主な機能として、「サイクル時間の決定」機能があります。ここでは、溶接速度、そしてガスプリフローとエンドクレーター充填回数などの要素を設定可能です。Pathfinderでは、ロボットコントローラでティーチングを行う場合に加え、最大で90%の時間を節約することができます(部品の形状と溶接要件による)。
Anton Paarのためのカスタマイズワークフロー
Anton Paarは、多種多様な部品の溶接のためのカスタムワークフローを利用することができています。具体的には3つのワークフローがあり、これは部品の範囲内で卓越した柔軟性を実証するものでした。
ワークフロー1:部品が回転傾斜ポジショナ上で溶接されます。部品を含んだパレットがパレットの棚から取り除かれ、パレット保管テーブル上で一時的に保管されます。その後、ハンドリングロボットが部品を拾うのに適したグリッパーを取り付けます。グリッパーは6種類あり、「グリッパーステーション」と呼ばれる場所に格納されています。グリッパーを装備したハンドリングロボットが部品を拾い上げ、部品別のクランプ装置(すでに取り付け済み)に固定します。ロボットが一度に取り除くことのできる部品数は一つです。取り除かれた部品は接合され、パレットに戻されます。
ワークフロー2:ハンドリングロボットがパレット棚からパレットを移動して溶接ロボットの前に配置し、部品がパレット上で直接溶接されます。溶接プロセス中、ハンドリングロボットと溶接ロボットが連帯し、動作できるようになります。これにより、単純な溶接形状のものだけでなく複雑なものまで溶接が可能になります。
ワークフロー3:部品は個々に移動され、ハンドリングロボットによって配置されます。溶接中は溶接ロボットと連帯して動作します。これは「連帯モーション」と呼ばれます。
必要な作業をシステムに認識させる
革新的な溶接技術、制御、ツールセンターポイント(TCP)測定、トーチ洗浄ステーション、エンクロージャに加え、フロニウスのロボット溶接システムは、ソフトウェア制御を基にコラボレーション可能な7つのコアモジュールで構成されます。具体的には、ハンドリングロボット、溶接ロボット、成形ガスユニット付き回転傾斜ポジショナー、2つのラック付きパレット保管場所、グリッパステーション、トーチ交換システム、パレット還納器といったシステム内モジュールがあります。これらのモジュールを作業サイクル中に正確に連帯させるには、次のステップが必要です。
まず、パレットと部品がHMI-T21 RSシステム制御内で一緒に作成され、それに伴い、担当の溶接工によって次の4種類の重要情報が提供されます。(1)パレットの種類、(2)種類、(3)個数、(4)パレット上の部品の位置。例えば、いくつのメインキャリアまたはオシレータハウジングが、どのパレットのどの位置に配置されるのかなどです。オフセットパレットの場合、部品の位置はいわゆる部品間のオフセット距離に基づいて計算されます。この際、最初の部品がマスターポジションと推定されます。例えば、オフセットがY座標において200 mmである場合、X座標でも+200 mmとなります。Anton Paarが製造するパレットは穴板で構成されており、厚さは数センチメートル規模、そしてプラグインシステムとして機能します。このパレットは2つのラックから成るパレット保管場所に配置されており、さまざまな加工対象物をそれぞれ保管できるように設計されています。個々の部品の受け取り位置や預け入れ位置は、部品の性質とハンドリングロボットのグリッパによって変わる場合があります。
ロボットコントローラには、各ワークフロータイプ用の階層的な下位ロボットプログラムが含まれています。ここにはPathfinderで作成された溶接プログラムが配置されます。ワークフロー2のパレットがHMIで作成される場合(部品がパレットに直接溶接される場合)、ロボットコントローラーは対応するロボット溶接プログラムをフィルタリングします。これにより、Anton Paarの溶接工はワークフロー2で利用可能なすべてのプログラムをスムーズに選択し、適切なものをパレットに割り当てることができます。単一の溶接プログラムを使うオプションの他、作業シーケンス全体を作成するオプションもあります。例えば、パレット用にTIGプログラムを作成し、その後に同じシーケンス内でMAGプログラム(例:CMT)を作成することが可能です。この場合、ロボット溶接システムでは2つのプログラムが順次に実行され、溶接プロセスが自動的に変更されます。さらに、Anton Paarのエキスパートは、専用の特別ステップをHMIプロセスに挿入することもできます。例を挙げると、特別な「部品回転」のステップをシステムが把握しているため、必要に応じて2つの溶接プロセス(TIGとCMT)間で使用可能です。
パレットのハンドリングで特定のグリッパが必要な場合には、ワークフロー1で説明した通り、システムオペレータはそのグリッパを選択する必要があります。グリッパには、前述のように6種類あり、すべてグリッパステーションに配置されます。
ティーチンググリッピングと預け位置
従来型のハンドリングシーケンスでは、それ自体でパレットのピックアップ、溶接用のポジショニング、元の位置への移動、デポジットを行います。これが標準プログラムとされており、オペレータが作業を行う必要はありません。これは「カプセル化」機能と呼ばれます。必要なのはグリップ位置の指定のみです。
新しい部品が「移動されてきて」いるのにもかかわらずデポジット・レシーブステーションに認識されない場合、自動ランは一時停止されます。そして、溶接技能者はロボットコントローラでティーチングプロセスを開始するよう促されます。ロボットコントローラはFanuc iPendantと呼ばれ、システムソフトウェアからステップごとの指示を受信します。システムはこれに基づいて関連するステーション(クリップボードなど)必要なグリップ/デポジットポジションを「学習」します。このポジションは記録され、ハンドリングプロセスをその地点から行う際に使用できます。その後、自動ランが次のステーションまで続行されます。部品がそこで不明な場合、位置もティーチングされる必要があります。すべてのステーションが指示通りに動作したら、ハンドリングロボットはその他の同一の部品をすべてシステム経由で中断することなく自動的に転送します。
パレットが7部品で構成されるべきであるのにもかかわらず3つの部品しかなかったとしても、システムには問題ありません。システムは「空のグリップ」を検出し、次の部品位置に自動的に移動します。
カスタムメイド:ティーチングパレット
Anton Paarでは、単純な形状の部品を好む標準のオフセット配置に加え、最大30個の金属部品をパレットの如何なる場所にもデポジットできるようにしたいと考えていました。これに対処するに当たり、フロニウスは「ティーチングパレット」機能を作成しました。この機能を選択すると、パレット上の各部品の位置を個々にティーチングすることが可能です。
「これら2つのバージョン、オフセットとティーチングパレットのおかげで、部品配置を最高レベルで柔軟に行うことができています」と、製造自動化部長のIngo Riemenschneider博士は説明しています。「オフセット距離を使って部品の位置を定義しようとするとうまくいかないことがあります。部品によっては形状の相違から別々の方向に固定する必要もあります。」
初日と同じ正確さを何か月後にも実現
溶接技能者は、溶接プロセスを開始するに当たり、携帯型のスキャナーを使って部品データシートからアイテム番号を読み取ります。
「このシステムでは、アイテム番号と部品情報が検出されると、ハンドリングと溶接プロセスが特定され、操作が開始されます。すべて、HMI-T21 RS経由で制御されています。そして、システムは、それぞれの部品でどのグリッパーとどの機器が必要なのかについて情報を保存します」と、Riemenschneider氏は述べます。「同様に、成形および溶接シーム中のアルゴンフラッシング時にも行われます。また、システムはプロセスデータの記録にどのデータが必要または不必要であるかも把握しています。」
ロボット溶接セルでは、それから数か月後も初日と変わらない精度で溶接がで可能であり、溶接シームも同じ場所に完璧な形で配置されます。これを可能にしたのはもちろん、Anton Paarがマイクロメートルレベルの精度で部品を製造し、卓越した品質レベルによって接合していることに起因しています。
たとえ成形中でも、部品を何度でも回転可能
回転傾斜ポジショナーには、4本のフロースルー線用に1つの媒体導管、そして送気管には2つ、アルゴン送気管には2つあり、最大で32件の入力/出力信号(IOs)を送信することができます。この媒体導管はプラスチック製で、Anton Paarによって3Dプリンティングを使用して製作しました。部品を成形する必要がある場合、ハンドリングロボットがまず必要な圧縮デバイスをパレットラックから取得し、特別なクランプシステムによってマニピュレータに締め付けます。それ以降、空圧式装置シリンダ用の空気ラインとアルゴンフラッシング用のガスラインの両方が接続されます。また、これによって、電子信号を圧縮デバイスによって送信できるようになりました。その後、ハンドリングロボットが部品を配置し、システムがクランプ信号を送信します。これで成形、その後に溶接を行えるようになります。システムは部品を1つの締め付けデバイス上で数回回転できるように設計されています。
「私たちにとって重要なのは、システムに実装されたすべてのプロセスとプロパティに柔軟な再現性があることです。旋盤加工が1回行われるか100回行われるかは、システムの観点からは無関係でなければなりません。部品の複雑さは常に変化しているため、Froniusと協力してできる限り柔軟なプロセス作りに力を入れています」とRiemenschneider氏は述べます。
Anton Paarが製造した残留酸素測定機器
回転傾斜ポジショナーで成形中、部品内の残留酸素は同社独自の測定機器、Oxy 5100で測定されます。Oxy 5100により、ガス流中の残留酸素のドリフトフリー測定は、溶接プロセス全体においてリアルタイムで行われます。通常、部品は1つのラインの2セクション間で固定されます。成形ガスは、供給ライン上の一端に流入し、その後片側に流れる際に排出されます。残留酸素の内容物はここで測定されます。各溶接プロセスで排出ガスホースの挿入/取外しという追加の過程がロボットに生じるため、これは自動溶接プロセスにとっては逆効果になります。そのため、測定装置を供給ラインに設置することが決定されました。望ましい残留酸素量に達したことが測定機器によって報告されると、溶接が開始され、その際にはアルゴンガスが部品に流入するまでにかかった時間分の遅延が考慮されます。この期間は、必要な残留酸素量にまだ達していないことを確認するのに必要なものです。部品の完全充填までにかかった時間、つまり遅延時間は、部品ごとに人力測定結果およびシステムに保存された結果に基づいて決定されます。部品が再度上がってくると、コントローラでは値にアクセスし、値に基づいた応答を行えるようになります。
溶接技術の頂点
Anton Paarの溶接技能者にとって特に重要だったのは、1つの部品溶接に2種類の溶接プロセスを組み合わせることです。例えば、ルートパスの溶接にはTIGを、多層溶接における表層ビードにはMAGといった要領で溶接を行う場合です。しかし、最終的にどの溶接方法を選択するかは、溶接の計算結果、そして個々の部品で必要とされる耐性次第です。
「私たちの溶接テストは、CMT(コールド物質移動)、PMC(パルスマルチ制御)、LSC(低スパッタ制御)など特殊なプロセスを使うかどうかの決定要素です。そして、どのプロセスに決定するかは、部品の壁の厚さや溶接の種類(I形突合せ溶接や隅肉溶接など)、必要な溶接深度とマイクログラフによって異なります」と、Moik氏は説明します。「シリーズ製造を始める前に約6~7回のテストが必要です。 素材の性質によって入熱が激しすぎる場合には、CMT、つまり「冷却」溶接プロセスが当然適切となります。溶接速度を上げて生産性を向上したい場合にはPMCを検討します。溶接を特に低スパッタリングで行う必要がある場合、LSCが適切な選択と言えるでしょう。なぜなら、これによってコストのかかる再作業を回避できるからです。」
溶接データはHMIに記録されます。目視検査中に溶接技能者によって欠陥が発見されると、溶接データ記録を見て制限値からの逸脱があったかどうかを確認することができます。もちろん、大原則として、部品にはすべて目視検査が行われ、また10回ごとに色浸透テスト(PT)も行われます。これはひび割れ、細孔、フュージョン溶着が1 µm以内でない場合の検出に便利です。PTテスト済みの金属部品に対してはテストサイクル後、定期的に顕微鏡撮影が行われます。
Froniusの革新的なプロセスはインテリジェントかつ柔軟なシステムコンセプトであり、またロボット溶接システムを常に進化させる現在進行形のポテンシャルを持っています。このような要素により、Anton Paarの繊細で高精度な測定機器では、今後長きにわたって最高レベルの溶接が可能になるでしょう。フェンスと抽出システムは同社の溶接工をアークと放出ガスから保護する、という安全性の向上と彼らの健康保護というメリットがあります。
品質保証、人材不足への対応、およびリソース効率化に対する新しい実証済みのソリューションを、ぜひご自身の目でお確かめください。フロニウスは、大阪市住之江区のインテックス大阪で開催される国際ウエルディングショー2024のスタンド4-01にて、私達のイノベーションを皆様にご紹介できることを楽しみにしています。