Muldenkipper im harten Baustellen-Einsatz
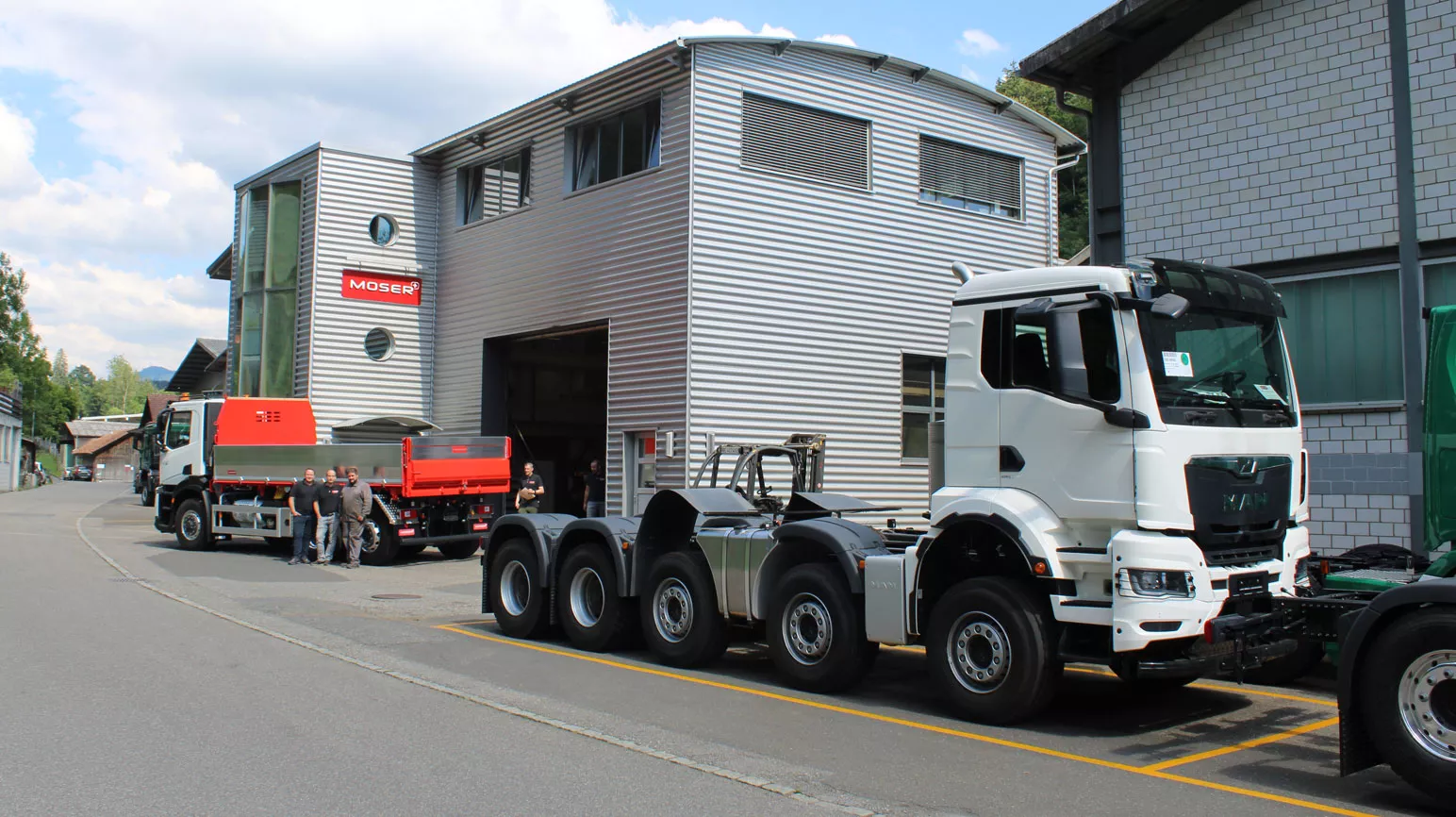
Reduziertes Eigengewicht: „Immer eine Ladung voraus“
Die Moser AG stellt Fahrzeugaufbauten für Lkw mit einem Gesamtgewicht zwischen 18 und 40 Tonnen her, wobei 40-Tonner mehr als 25 Tonnen an Nutzlast aufnehmen können. „Möglichst hohe Transportmengen pro Fahrt sind das A und O in unserer Branche. Damit unsere Kundinnen und Kunden bei einem fest vorgeschriebenen Gesamtgewicht so viel Material wie möglich transportieren können, konstruieren wir unsere Kipper und Ladesysteme so leicht wie möglich – ohne dabei Kompromisse bei der Festigkeit, Beständigkeit oder Nutzerfreundlichkeit einzugehen“, betont Stefan Rolli, Betriebsleiter der Moser AG.
Je nach Grösse und Achsenanzahl des jeweiligen Fahrzeugs wiegen die in Steffisburg erzeugten Lkw-Aufbauten meist zwischen 3 und 4,5 Tonnen. „Der Nutzlastvorteil, den unsere Kunden durch den Einsatz unserer leichteren Aufbauten im Vergleich zu Mitbewerbern haben, liegt oft zwischen 500 bis 700 kg pro Fahrt. Das bedeutet einen deutlich effizienteren Einsatz der Fahrzeuge – ganz nach unserem Motto ‚Immer eine Ladung voraus‘“, so Stefan Rolli.
Kundennähe begünstigt Massanfertigung
Die von der Moser AG individuell nach Kundenwünschen massgefertigten Aufbauten passen auf alle gängigen Lkw-Typen. Besonders stolz ist man bei dem Unternehmen aus dem Kanton Bern, dass sämtliche Kipper und Ladesysteme – ab den zugelieferten Blechen und Profilen – am Unternehmensstandort in Steffisburg produziert werden:
„Wir sind heute das einzige Unternehmen in der Schweiz, das Nutzfahrzeug-Aufbauten für den Baustellensektor in einer so hohen Fertigungstiefe herstellt. Durch die Kontrolle über alle wesentlichen Produktionsprozesse und die Nähe zu unseren Kunden können wir auf Sonderwünsche sehr rasch und flexibel eingehen“, führt Moser-Betriebsleiter Stefan Rolli aus.
Jährlich verlassen mehr als 200 Lkw das Werk in Steffisburg, die Produktionsdauer für einen neuen Kipper beträgt im Schnitt 6 bis 8 Wochen.
Produktionsprozesse im Überblick
In ihren Grundzügen gliedern sich die Produktionsprozesse bei der Moser AG in folgende Schritte: Die Lkw werden nach ihrer Anlieferung umfassend vermessen. Nach der Konstruktion der Aufbauten mithilfe von CAD und der Arbeitsvorbereitung erfolgen als nächste Schritte der Zuschnitt der Bleche auf einer CNC-Plasmaschneideanlage, das Abkanten auf einer CNC-Abkantpresse und die weitere mechanische Bearbeitung in einem CNC-Bearbeitungscenter.
In den Schlossereien der Moser AG werden die Bauteile miteinander verschweisst, also die Kipper in ihrer Rohform fertiggestellt. Anschliessend geht es für die Lkw-Aufbauten zum Sandstrahlen und zum Lackieren. Nach der Installation der Hydraulik erfolgen Vor- und Endmontage. Bevor ein Lkw mit seinem neuen Aufbau das Areal der Moser AG in Steffisburg verlässt und seiner neuen Bestimmung entgegenfährt, wird dieser noch einer gründlichen Endkontrolle unterzogen.
Schweissnähte in allen Bauteilen
„Schweissnähte kommen bei uns in praktisch allen Bauteilen vor. Im tagtäglichen Baustelleneinsatz müssen diese Erschütterungen, Vibrationen und Verwindungen standhalten – etwa, wenn tonnenschwere Felsblöcke aus der Schaufel eines Radladers auf die Kippermulde treffen. Da fehlerhafte Nähte gravierende Folgen haben, ist unser Anspruch an die Professionalität unserer Schweisser und die von ihnen verwendeten Geräte ausserordentlich hoch“, betont Stephan Zingg, Konstrukteur bei der Moser AG. Besonderes Augenmerk wird auf einwandfreie Schweissnähte in den tragenden Bauteilen wie der Muldenunterkonstruktion oder dem Hilfsrahmen gelegt.
Stahl und Aluminium bis 70 mm
Bei Moser verschweisst man bei der Herstellung von Lkw-Aufbauten herkömmlichen S355-Baustahl, Stähle von S690 bis S700 und Hardox 450 in verschiedenen Stärken von 3 mm bis 70 mm. Am häufigsten kommt dabei 4 mm starkes Hardox 450-Blech zum Einsatz.
Die in Steffisburg verarbeiteten Aluminium-Bleche weisen in der Regel eine Dicke von 2 mm auf, Warzenbleche aus Aluminium sind 3/4,5 mm oder 3/6,5 mm stark. Relativ leichte Aluminium-Legierungen kommen nicht zuletzt bei den Seitenwänden der Kipper zum Einsatz. Diese werden mithilfe einer von der Moser AG entwickelten Form stranggepresst, das Moser Aluminium Profilsystem MAP ermöglicht den modularen Bau der Seitenwände. Weitere Einsatzbereiche von Aluminiumblechen sind Kotflügel, Abdeckungen und Trittbretter.
Fokus auf MAG-Handschweissen – häufige Zwangslagen
Die überwiegende Mehrheit der Schweissnähte wird bei der Moser AG im MAG-Verfahren handgeschweisst. Neben beachtlichen Schweissgeschwindigkeiten bietet MAG-Schweissen hohe Abschmelzleistungen, gleichzeitig wird relativ wenig Streckenenergie in die zu verschweissenden Kipperteile eingebracht.
Bei Serienteilen oder immer wiederkehrenden Prozessen – wie dem Schweissen der Hilfsrahmen der Kippermulden – kommt in Steffisburg eine Portalanlage mit einem Schweissroboter zum Einsatz. Die Portalanlage ermöglicht es, den gesamten Kipper in die entsprechende Schweissposition zu drehen.
„Die Beschaffenheit der Schweissnaht gibt uns die WPS vor. Bei den Stärken der Kehlnähte halten wir uns dabei grundsätzlich an das A-Mass, also die Dicke des dünnsten Blechelements multipliziert mit 0,7“, schildert Stefan Rolli.
Um den hohen Belastungen im tagtäglichen Einsatz auf Baustellen standzuhalten, werden viele Schweissnähte mit einer Wurzellage und mit bis zu 2 Decklagen geschweisst. Neben Kehlnähten kommen sehr häufig auch Stumpfnähte – mit und ohne Spalt – zur Anwendung. Eine Aufgabe, mit der die Schweisserinnen und Schweisser der Moser AG regelmässig konfrontiert sind, ist zudem das Schweissen in Zwangslagen: Von „klassischen“ Steignähten am Rohr und am Blech bis zu Überkopf-Nähten.
4 Generationen an Fronius-Geräten
Die Moser AG verwendet seit 24 Jahren Schweisssysteme von Fronius. Heute befinden sich in Steffisburg rund 35 Geräte aus 4 verschiedenen Fronius Generationen im tagtäglichen Einsatz: die Fronius VarioSynergic 4000, die VarioStar 457, die Transsynergic 5000 und seit dem Jahr 2018 die Fronius TPS 500i.
Fronius TPS 500i: Effizienz durch präzise einstellbare Schweisskennlinien
„Gerade in der aktuellen Situation sind Schnelligkeit und Flexibilität in der Produktion für uns ein entscheidendes Thema. Mit dem Einsatz der Fronius TPS 500i und ihren Schweisskennlinien haben wir die Schweissgeschwindigkeiten in allen wesentlichen Bereichen deutlich gesteigert. Gleichzeitig ist der Aufwand für das Nacharbeiten an den Schweissnähten merkbar zurückgegangen. Insgesamt macht die TPS 500i nicht nur die Schweissprozesse, sondern auch die nachgelagerten Arbeitsschritte spürbar effizienter – was sich in der Folge positiv auf unsere gesamte Fertigung auswirkt“, so Moser-Betriebsleiter Stefan Rolli.
Häufig setzen die Schweissfachkräfte der Moser AG auf ihren TPS-500i-Geräten das Fronius Welding Package PMC in den Varianten PMC Universal, PMC Dynamic und PMC Mix ein. PMC steht für Pulse Multi Control und ist eine Weiterentwicklung des Impulslichtbogens.
„Generell zeichnen sich die PMC-Kennlinien durch einen stabilen, dynamischen und spritzerarmen Impulslichtbogen aus. Die beachtlichen Schweissgeschwindigkeiten der TPSi werden vor allem durch ihre hohe Prozessorleistung und die entsprechenden Mess- und Regelgeschwindigkeiten ermöglicht“, erklärt Fritz Loosli, der für die Moser AG zuständige Anwendungstechniker und Kundenberater bei Fronius. Die PMC-Kennlinien bieten 2 Stabilisator- und 2 Korrekturparameter: einen Lichtbogenlängen-Stabilisator und einen Einbrand-Stabilisator sowie eine Lichtbogenlängenregelung und die Pulskorrektur.
Bis zu 40 Prozent schneller bei Steignähten
Die Kennlinie PMC Mix verwenden die Schweissfachkräfte der Moser AG unter anderem deshalb, weil sich damit Steignähte ohne die sonst übliche Pendelbewegung („Tannenbaumbewegung“) schweissen lassen. Insgesamt sind im PMC-Mix-Prozess bei Steignähten um bis zu 40 Prozent höhere Schweissgeschwindigkeiten möglich. Die technische Grundlage für diese Kennlinie bildet der Prozesswechsel zwischen einem Impuls- und einem Kurzlichtbogen – also der zyklische Wechsel zwischen einer heissen und einer kalten, stützenden Prozessphase. Die Wärmeeinbringung in das Material wird durch diesen Vorgang reduziert.
Steel-Root ist eine weitere Kennlinie, die von den Schweissfachkräften der Moser AG häufig eingesetzt wird. Diese Kennlinie spielt ihre Vorteile dann aus, wenn es beim Schweissen von Kipperteilen um das Überbrücken von Spalten in der Grössenordnung von 2 bis 3 Millimetern geht. Charakteristisch für die Steel-Root-Kennlinie ist ein weicher, stabiler Lichtbogen. Durch die Ablöse von relativ grossen Tropfen wird ein zähflüssiges Schmelzbad erzeugt, mit dem sich grössere Spalten entsprechend einfach schweissen lassen.
Die Schweisskennlinie PMC Dynamic kommt bei Moser bei horizontalen Kehlnähten zum Einsatz. Sie bietet einen relativ aggressiven Lichtbogen mit hohem Druck und konzentriertem Fokus. Ihr Vorteil: Hohe Schweissgeschwindigkeiten bei gleichzeitig geringem Energieeintrag ermöglichen verzugsarme Schweissergebnisse und sparen wertvolle Ressourcen wie Gas, Zusatzmaterial und Arbeitszeit.
Davon abgesehen verwendet Moser bei vielen Schweissprozessen nach wie vor bewährte Standard-Lichtbögen. Aluminiumteile werden in der Regel mit einem herkömmlichen Impulslichtbogen verschweisst.
Nutzerfreundlichkeit am Schweissgerät und direkt am Brenner
Neben ihren Schweisskennlinien trägt auch die hohe Nutzerfreundlichkeit der TPS 500i dazu bei, dass Schweissprozesse einfacher, schneller und effizienter werden. Das grosse Klartext-Display an der TPSi ist an die Schweissumgebung angepasst. Es lässt sich auch mit Handschuhen einfach und intuitiv in der jeweiligen Landessprache bedienen.
Wesentlich in Zusammenhang mit der Nutzerfreundlichkeit ihrer Arbeitsgeräte ist für die Schweissfachkräfte der Moser AG, dass sie Einstellungen direkt am Brenner vornehmen können: „Muldenkipper sind Bauteile, die nicht gerade einfach und rasch hin- und hergeschoben werden können, also bewegen sich unsere Mitarbeiter um die Bauteile herum. Um unseren Schweissern ein Maximum an Bewegungsfreiheit zu bieten, sind alle unsere Schweissgeräte mit 10 Meter langen Schlauchpaketen ausgestattet“, erklärt Stefan Rolli.
Bei ihren TPS-500i-Geräten verwenden die Schweisserinnen und Schweisser in diesem Zusammenhang leichte Fronius PullMig-Schweissbrenner in der Ausführung Jobmaster. Die wassergekühlten Schweissbrenner sind mit einem keinen Elektromotor im Brennergriff ausgestattet, der den reibungslosen Drahtvorschub durch das 10 Meter lange Schlauchpaket sicherstellt.
Weniger Wege – höhere Effizienz
In der Jobmaster-Einstellung „Easy-Job“ haben Anwenderinnen und Anwender die Möglichkeit, bis zu 5 Schweissjobs direkt auf ihren PullMig-Brenner zu „legen“ und sehr rasch zwischen den einzelnen Jobs hin und her zu wechseln. Indem sie alle wichtigen Schweissjobs für ihre tagtäglichen Arbeiten direkt am Brenner aufrufen können, ersparen sie sich zahlreiche Wege zwischen dem Schweissgerät und dem Bauteil. Das macht den Arbeitsalltag für Schweissfachkräfte nicht nur komfortabler, sondern auch deutlich effizienter.
„Auf die Schweissgeräte von Fronius verlassen wir uns seit 24 Jahren, weil wir in Fronius einen Partner sehen, der für Qualität, Verlässlichkeit, gute Beratung und innovative Produkte steht. Die laufenden technischen Entwicklungen, wie zuletzt die TPS 500i mit ihren Schweisskennlinien, tragen wesentlich zu unserer Performance bei, vor allem in Hinblick auf die Schnelligkeit und Flexibilität unserer Produktion. Die Schweisssysteme von Fronius unterstützen uns dabei, unseren Kundinnen und Kunden aus dem Schweizer Baustellensektor jene Qualität zu liefern, die sie von uns zu Recht einfordern“, unterstreicht Moser-Betriebsleiter Stefan Rolli abschliessend.