Jakość jako palący problem
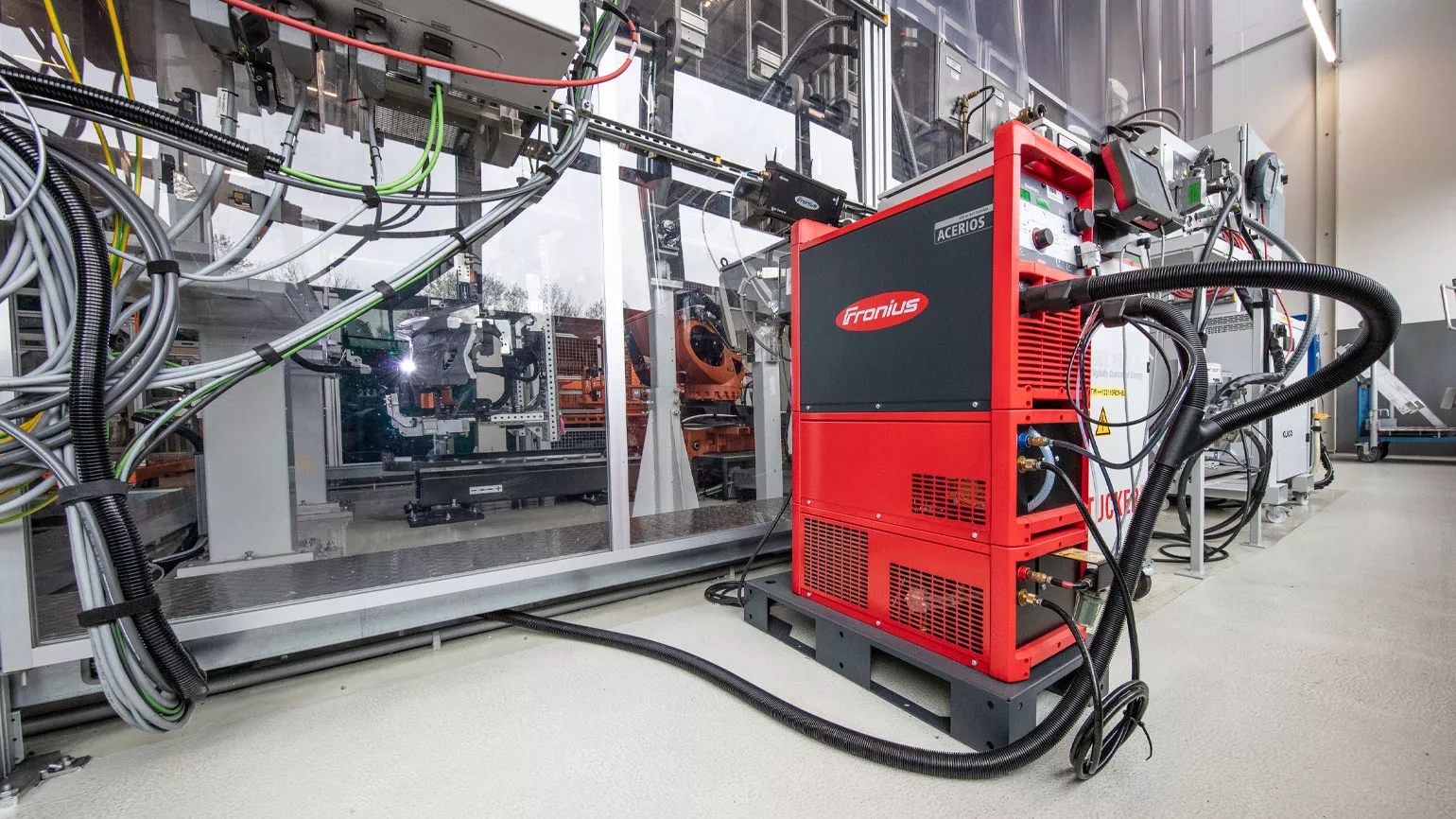
„Uszkodzenie połączenia kołków masowych w najgorszym przypadku może spowodować zatrzymanie pojazdu”, mówi dypl. inż. Daniel Rudolph, specjalista ds. rozwoju technologii łączenia i konstrukcji lekkich w AUDI AG. „W produkcji Audi A8 używamy licznych kołków masowych i musimy być pewni, że każdy z nich jest idealnie połączony. Aby sprostać wymogom jakościowym, ponosimy duże nakłady”.
Wynika to z faktu, że jakość każdego doczołowego zgrzewania kołków mocno zależy od właściwości powierzchni. Zabrudzenia olejami do ciągnienia i suchymi smarami — stosowanymi w procesach formowania metali — mogą spowodować defekty łączenia.
Clean Flash traci funkcjonalność ze względu na grubość blachy
W wielu przypadkach, problem zanieczyszczeń można rozwiązać samym urządzeniem do doczołowego zgrzewania kołków: W tym celu do właściwego procesu zgrzewania dołącza się przed nim impuls prądowy (Clean Flash), który oczyszcza powierzchnie do zgrzewania. W przypadku blach aluminiowych o grubości poniżej 2 mm nie stosuje się już tego procesu, ponieważ ciepło wprowadzane do spoiny jest zbyt duże i podczas zgrzewania blacha może ulec przepaleniu. Poza tym, w przypadku stosowania tej metody, mogą pojawić się między innymi pory, obniżające jakość spoin.
Tego typu elementem w produkcji pojazdów marki Audi jest przykładowo ściana czołowa modelu Audi A8. Składa się ona z blachy ze stopu aluminiowego (6xxx) i w każdym miejscu, w którym będą zgrzewane kołki masowe, ma tylko 1,5 mm grubości: „W pierwszych latach po uruchomieniu produkcji seryjnej, cały element musieliśmy chemicznie czyścić i impregnować, co było zarówno kosztowne, jak czasochłonne”, wyjaśnia Rudolph. „Tylko w ten sposób mogliśmy zagwarantować wymagane 100% jakości dla każdego doczołowego połączenia z kołkami zgrzewanymi”.
W roku 2017 w fabryce Audi wybudowano nową linię produkcyjną do produkcji piątej już generacji modelu A8. Audi chciało się przy okazji pożegnać z kosztownym czyszczeniem chemicznym. Jednego z możliwych rozwiązań upatrywano w technologii gorącej plazmy aktywnej (HAP), którą już od dawna intensywnie zajmował się długoletni dostawca technologii spawania i partner rozwojowy, firma Fronius. Także Audi śledziło już wyniki zastosowania technologii HAP u swoich partnerów uniwersyteckich.
Ponieważ obszary zadaniowe Rudolpha obejmują także ewaluację nowych technologii produkcyjnych oraz ich dalsze rozwijanie, aż do etapu gotowości do zastosowania w produkcji seryjnej, efektem była intensywna kooperacja specjalistów ds. technik łączenia z firm Audi i Fronius. Ten eksperyment techniczny rozwinięto następnie i zakwalifikowano do poziomu gotowości do produkcji seryjnej. Rudolph doprecyzowuje: „W firmie Fronius przebiegały prace głównie nad rozwojem techniki procesowej i linii. W naszym dziale produkcji odbywały się następnie próby oraz testy funkcji, parametrów, wytrzymałości związane z zastosowaniem tej metody. Zajmowaliśmy się także kwestią tego, jak zastosowanie tej technologii oddziałuje na dalsze łańcuchy procesów, takie jak łączenie, wytrzymałość, przyczepność lakieru i wielu innych”.
Czyszczenie plazmowe części materiału jako rozwiązanie
Zalety obróbki powierzchni technologią gorącej plazmy aktywnej (HAP) Acerios firmy Fronius są liczne. Strumień gazu osłonowego przekształca plazmę łuku spawalniczego w płomień, którego temperatura w centrum sięga 1000 stopni Celsjusza. Wywołane w ten sposób procesy cieplne i chemiczne powodują, że następuje usunięcie pozostałości zabrudzeń organicznych i powłokowych partiami i z dokładnością punktową. Jednocześnie następuje aktywacja powierzchni. Ponieważ łuk spawalniczy w technologii Acerios powstaje między dyszą plazmową i elektrodą wolframową uchwytu spawalniczego, nie jest konieczne połączenie z masą elementu zgrzewanego. W ten sam sposób gorącą plazmą aktywną można też czyścić materiały niemetaliczne.
„Sprawdziliśmy Acerios — tak jak wszystkie szczególnie brane przez nas pod uwagę technologie — pod kątem jej przydatności i określiliśmy zmienne spawania oraz możliwe okna parametrów. Następnie, wspólnie z firmą Fronius, szybko i w ukierunkowany sposób zoptymalizowaliśmy prototypy do zastosowania seryjnego”, mówi Rudolph. „Na koniec, nasi planiści linii i koledzy z działu produkcji określili dobre miejsce na montaż linii.“
Osoby odpowiedzialne za linię A8 zdecydowały się ostatecznie na montaż Acerios w celi robota, zapewniającej wystarczająco długi czas międzyoperacyjny na czyszczenie dwóch obszarów — każdego o powierzchni 12 cm². „Dlatego dostępny czas wystarczył nawet na to, by wydłużyć czas jarzenia Acerios do sześciu sekund na zgrzeinę punktową. Odstęp uchwytu spawalniczego od detalu wynosi 30 mm, a prąd bez szkody dla jakości możemy obniżyć do 120 A”, uzupełnia Jürgen Kolbenschlag, ekspert spawalnictwa z działu budowy karoserii modelu A8.
„Dzięki temu oszczędzamy części eksploatacyjne”, które początkowo trzeba było wymieniać w Audi po 10 000 punktów czyszczenia. Okazało się, że do granic zużycia było jeszcze bardzo daleko. Dlatego na bieżąco wydłużano okres wymiany. W połowie 2021 roku wciąż nie osiągnięto granicy zużycia — pomimo wykonania 25 000 punktów czyszczenia.
Niskie koszty integracji
Integrację technologii gorącej plazmy aktywnej ułatwił fakt, że planiści mogli zainstalować plazmowy uchwyt spawalniczy Acerios PCT 2000 stacjonarnie. W tym celu potrzebna była minimalna strefa robocza w promieniu działania robota. „Także zasilanie nie potrzebowało nawet metra kwadratowego powierzchni, więc mogliśmy je wygodnie umieścić poza celę, pomiędzy już zainstalowanymi zespołami zasilającymi”, relacjonuje Rudolph.
Wcześniej nieużyte czasy międzyoperacyjne robota wykorzystaliśmy do transportu ściany czołowej do uchwytu spawalniczego. Także dzięki wąskiemu uchwytowi spawalniczemu jest zapewniona doskonała dostępność do elementu zgrzewanego, wskutek czego płomień plazmy jest ustawiony dokładnie pionowo, a przez to optymalnie względem powierzchni. Także przejazd pasmowy w czasie procesu czyszczenia jest zbędny: zastosowany od wewnątrz do zewnątrz proces czyszczenia w czasie jarzenia całkowicie pokrywa wybraną powierzchnię.
Fakt, że Acerios wykorzystuje tani gaz osłonowy — argon — także jest Audi na rękę. Dzięki temu można było wykorzystać już istniejącą, pierścieniową sieć zasilającą systemy spawania MIG argonem. Pozwoliło to oszczędzić sobie dodatkowych kosztów.
Audi mogło też w bardzo prosty sposób przeprowadzić integrację źródła spawalniczego do spawania plazmowego połączonego z uchwytem spawalniczym pakietem przewodów o długości 6 m, jak relacjonuje Rudolph: „Interfejs systemu Acerios jest taki sam, jak naszych systemów spawania MIG/MAG firmy Fronius. Ponieważ jest on częścią specyfikacji interfejsów VW, w ciągu kilku dni mogliśmy bezproblemowo podłączyć system Acerios do sterowania linią”.
Także ustawienie i obsługę linii w dużym stopniu zapożyczono ze źródeł energii TIG, co potwierdza Rudolph: „Umiejętność konfiguracji źródła prądu spawania TIG umożliwia też pracę z systemem Acerios. I bez tego obsługa jest prosta, ponieważ trzeba ustawić tylko kilka parametrów, takich jak natężenie prądu lub czas jarzenia”.
Przejrzyste koszty nabycia i eksploatacji
Inwestycje w zastosowanie systemu Acerios w Audi okazały się porównywalnie niskie. Jest to efektem nie tylko możliwości podwójnego wykorzystania istniejących środków eksploatacji oraz różnego sprzętu. Decydujące były także bogate doświadczenia Audi z innymi źródłami energii firmy Fronius oraz ich niskie koszty konserwacji. W porównaniu z innymi rozwiązaniami czyszczenia partiami, system HAP firmy Fronius wyróżnia się szczególnie niskimi kosztami nabycia.
Przykładowo, systemy laserowe już na poziomie inwestycji podstawowej to koszt około miliona euro. Konfiguracja systemu Acerios jest o wiele tańsza. Razem z linią do automatyzacji, rozwiązanie firmy Fronius mieści się w środkowej części pięciocyfrowego zakresu. Do tego nie potrzeba osobnej, obudowanej celi robota — której wymaga system laserowy. Także zużycie prądu jest wyraźnie niższe niż ma to miejsce w przypadku lasera czyszczącego. Dodatkowo, system Acerios potrzebuje ok. 15 l gazu na minutę.
Także w stosunku do dotychczas typowego, kosztownego czyszczenia na mokro osiągnięte oszczędności są znaczące, co potwierdza Rudolph: „Koszty czyszczenia ściany czołowej mogliśmy obniżyć o kwotę leżącą w dolnym, jednocyfrowym zakresie euro i jednocześnie zwiększyć wydajność zasobową bez obniżenia jakości czyszczenia. Osiągnięcie porównywalnych oszczędności w branży motoryzacyjnej jest zwykle związane ze znacznie wyższymi nakładami”.
Z praktycznych doświadczeń AUDI AG można wnioskować: Wskutek niższych kosztów eksploatacji i nabycia, zastosowanie systemu Acerios opłaca się już nie tylko w przypadku małej liczby sztuk, ale także i w produkcji wielkoseryjnej. Ponadto zastosowanie technologii HAP firmy Fronius jest uzasadnione szczególnie w przypadku wąskich przestrzeni i punktualnego czyszczenia w zakresie sekundowym.
Acerios rozszerza portfolio technologiczne Audi
Dzięki tym nadzwyczaj dobrym rezultatom, Audi zintegrowało technologię czyszczenia firmy Fronius już w kolejnym miejscu: w procesie produkcji elementu tunelu, powierzchnie czterech doczołowych zgrzewań kołkowych także posługuje się technologią HAP. „Acerios optymalnie rozszerza dostępne dla nas portfolio technologiczne”, ocenia na koniec Rudolph. Gdy mówimy o zgrzewaniu kołków masowych z detalami o małej grubości, technologia HAP znajduje się w wąskim gronie potencjalnych procesów czyszczenia”.