Jak warianty regulacji procesu rewolucjonizują spawanie podzespołów układu wydechowego: Na pełnym gazie w przyszłość motoryzacji
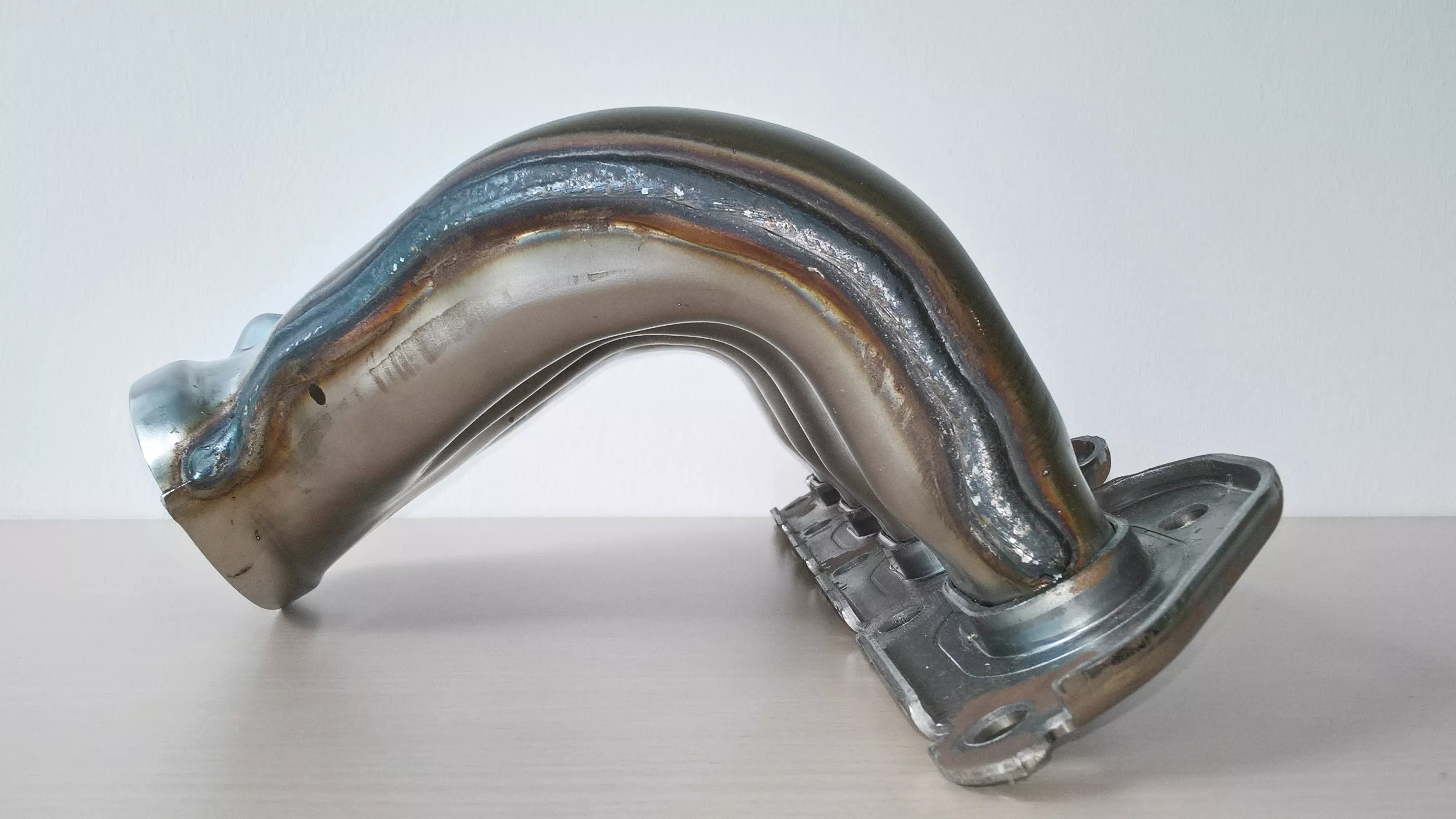
Układy wydechowe odprowadzają gazy spalinowe z silnika i poddają je oczyszczaniu. Muszą być odporne na wysokie temperatury i korozję. Wymogi stawiane poszczególnym podzespołom decydują o tym, z jakich materiałów są wykonywane.
Najczęściej stosowanym procesem podczas łączenia podzespołów układu wydechowego jest zautomatyzowane spawanie elektrodą topliwą w osłonie gazów aktywnych (MAG). Kolektor wydechowy stawia wysokie wymagania procesowi spawania: wąskie promienie elementu zmuszają robota do zmniejszenia prędkości spawania. Pomimo tego do elementu nie może trafiać zbyt wiele energii, a proces spawania musi zapewniać stabilność i powtarzalność.
Wydajna elektronika tworzy nowe możliwości
Tak jak kolektor wydechowy, tak i inne podzespoły mają swoje „humory”. Rodzaj i grubość materiału zależą od wymogów dla danej grupy elementów — dlatego konieczne jest też dostosowanie procesu spawania do danego podzespołu. Firma Fronius w swoim portfolio ma różne warianty regulacji procesu metodą MAG, umożliwiające ciągłe spawanie złożonych elementów. Dzięki wydajnej elektronice w nowoczesnych źródłach spawalniczych użytkownicy mogą w kontrolowany sposób wpływać na łuk spawalniczy i w ten sposób uzyskiwać optymalne wyniki.
Proces „Low Spatter Control” (LSC) szczególnie dobrze nadaje się do spawania podzespołów układu wydechowego. Jest oparty na spawaniu łukiem zwarciowym przy obniżonej energii i bez rozprysków. Osiąga się to przez precyzyjną kontrolę momentu zwarcia przez system spawania: źródło spawalnicze dokładnie wykrywa zbliżenie drutu elektrodowego do jeziorka spawalniczego i steruje przedostawaniem się kropli do jeziorka w taki sposób, aby odbyło się to przy niskiej mocy. Dzięki temu ciepło oddawane do elementu jest niskie i praktycznie nie powstają rozpryski. To idealne rozwiązanie w przypadku łączenia elementów o niewielkiej grubości ścianek i zmiennych geometriach łączenia — jak np. w przypadku kolektora wydechowego. Poza tym, LSC zapewnia wysoką stabilność w przypadku trudnych zmian położenia palnika spawalniczego, a przez to wysokie prędkości spawania.
Kolejnym wariantem procesu jest „Pulse Multi Control”, w skrócie PMC. Ten zmodyfikowany proces spawania łukiem pulsującym odznacza się precyzyjnie regulowanym i pozbawionym rozprysków oderwaniem kropli. Proces PMC wytwarza silny, stabilny łuk spawalniczy i w pozycjach wymuszonych zapewnia dobre wydajności stapiania, a jednocześnie dobre opanowanie jeziorka spawalniczego. Dzięki temu użytkownicy mogą unikać nieregularności, takich jak karby — i spawać w sposób stabilny oraz powtarzalny. Wariant ten nadaje się szczególnie do elementów z tolerancjami o silnych wahaniach grubości ścianek — takie warunki można spotkać w wielu podzespołach układu wydechowego. Proces PMC zapewnia wystarczające wtopienie i dobre wypełnianie szczelin. Dostawcy branży motoryzacyjnej stosują często tę metodę do spawania kolektorów wydechowych. W praktyce PMC umożliwia uzyskanie wyraźnie wyższych prędkości spawania, a przez to wzrost produktywności.
Wyżej, dalej – cieniej!
Przyszłe wyzwania w przemyśle motoryzacyjnym mogą jednak ustawić w centrum zainteresowania także inne warianty procesów. Ważnym trendem jest projektowanie coraz lżejszych pojazdów: mniejsza masa zmniejsza zużycie paliwa, a oszczędność materiałów obniża koszty produkcji. Ma to też wpływ na konstrukcję podzespołów układu wydechowego. Zastosowane materiały podstawowe i spoiwa odporne na działanie temperatur umożliwiają produkcję tych elementów z coraz cieńszych materiałów. Dlatego w przyszłości regułą może stać się zastosowanie elementów o grubości ścianek 0,8 mm. Tu stosowany jest proces CMT (Cold Metal Transfer). Proces łączy w sobie regulowane spawanie łukiem zwarciowym z drutem elektrodowym poruszającym się naprzód i wstecz. Rezultat: wyjątkowo małe ciepło oddawane i nadzwyczajna stabilność procesu spawania, dzięki czemu użytkownik uzyskuje optymalne wyniki także w przypadku łączenia bardzo cienkich elementów.