Wyzwanie w spawaniu cienkich blach w inżynierii mechanicznej
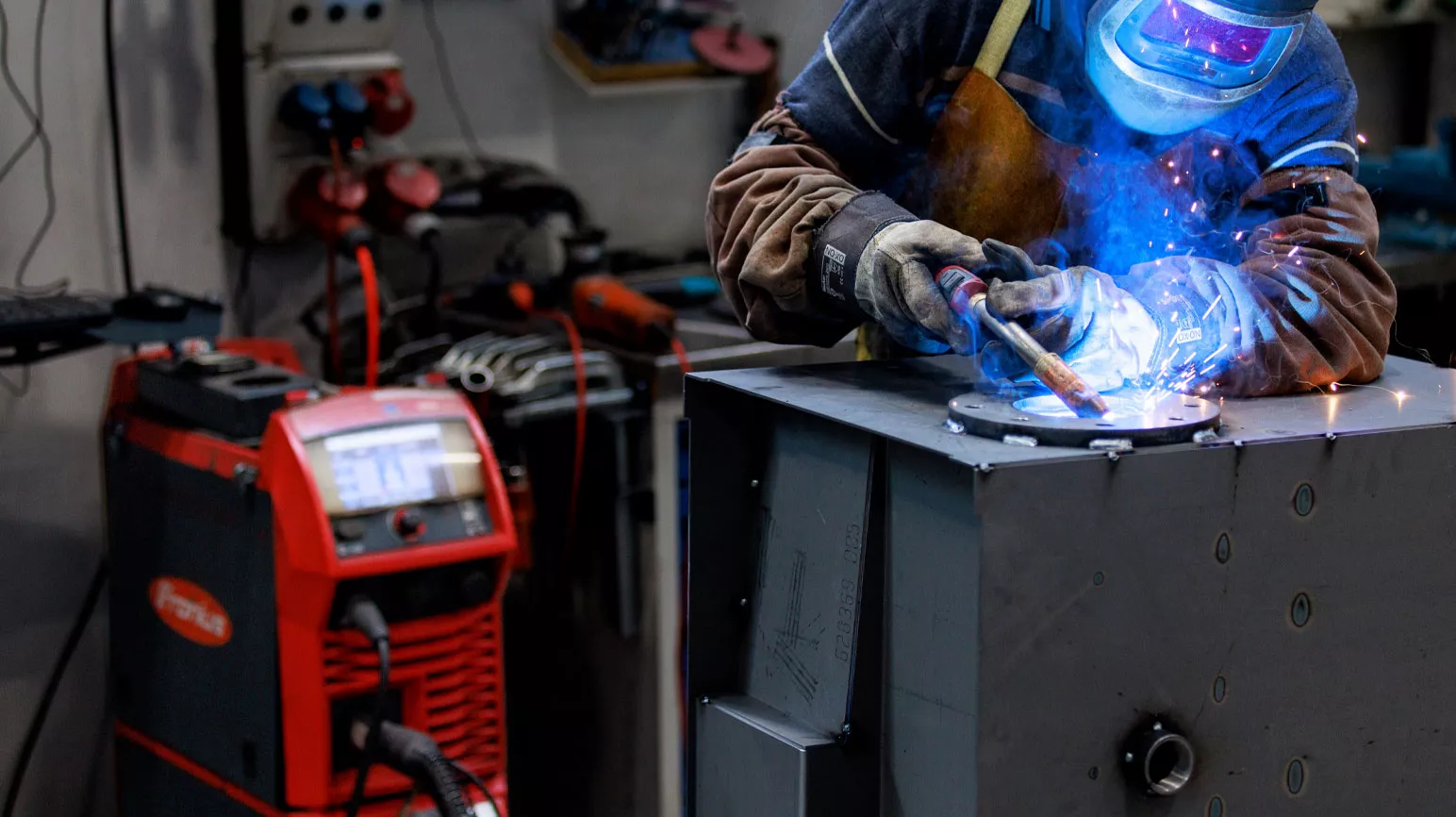
Knoll cieszy się pozycją lidera w zakresie technologii, jakości i rozpoznawalności. Niezależna ekonomicznie, rodzinna firma tworzy wartość dodaną dla wszystkich przedsiębiorstw, w których są wykorzystywane procesy obróbki skrawaniem metalu: w przemyśle motoryzacyjnym, w energetyce i technologii medycznej, w inżynierii mechanicznej i zakładowej oraz w przemyśle lotniczym.
Wysoki
rzeczywisty współczynnik wyjściowy netto
Zaawansowane rozwiązania z Bad Saulgau optymalizują działanie
wielu obrabiarek. Produkowane są oszczędzające zasoby systemy oczyszczania
środków chłodząco-smarujących, przenośniki wiórów i pompy. W asortymencie
znajdują się również systemy centralne – zintegrowane w jeden system pojedyncze
urządzenia. Są one przydatne do pełnej automatyzacji transportu wiórów i
środków chłodząco-smarujących do centralnych instalacji do obróbki. Rozwiązania
automatyzacji do linii montażowych i intralogistyki stanowią kolejny filar
działalności Knoll. Są to przykładowo taśmociągi montażowe, automatyczne
systemy transportu i coboty.
Joachim Riebsamen, kierownik produkcji konstrukcji surowych:
„Jako Solution Provider oferujemy
wszystkie wymagane usługi – od projektowania przez produkcję po
uruchamianie i serwis. Wierzymy, że dobre relacje z klientami zależą od
przejrzystości i zaufania. Dlatego posiłkujemy się nie tylko stroną
internetową, broszurami i rozmowami handlowymi. Potencjalni klienci mogą
przyjrzeć się naszym własnym procesom obróbki, aby przekonać się o zaletach
naszych produktów w praktyce”.
Ze względu na wysoki realny wskaźnik produkcji netto, Knoll
zachowuje większość wartości dodanej we własnej firmie. Redukuje ona
zapotrzebowanie na logistykę, jak i związaną z tym emisję CO2, co
przynosi korzyści zarówno w wymiarze ekonomicznym, jak i środowiskowym.
Problem
ze spawaniem cienkiej blachy
Nie wszystko w Bad Saulgau podlega produkcji seryjnej. Wiele
elementów tak zwanej konstrukcji surowej jest spawanych ręcznie. Konstrukcje te
zbudowane są z blach o różnej grubości, do 25 mm. Do budowy systemów
oczyszczania środków chłodząco-smarujących i przenośników wiórów fachowcy z
Knoll wykorzystują głównie stal S355, która spajana jest za pomocą gazu
osłonowego M21 (82% Ar i 18% CO2) oraz dodatku drutu SG3 (G4Si1).
Jako podstawa parametryzacji służy firmowa instrukcja technologiczna spawania
WPS (Welding Procedure Specification).
„Jedną z najtrudniejszych rzeczy w spawalnictwie jest obróbka cienkiej blachy” – tłumaczy Holger Kleck, główny spawalnik. „Grubość materiału naszych elementów wynosi 1–6 mm i dość szybko ulegają one wypaczeniu. Dlatego musimy pracować z niewielką ilością ciepła wprowadzanego do spoiny. Często wykonujemy widoczne elementy, których spoiny nie tylko muszą odznaczać się idealnymi właściwościami metalurgicznymi, ale także spełniać kryteria wizualne. Chcemy koniecznie zaoszczędzić sobie ich poprawiania. Dlatego tak bardzo zależy nam na bezodpryskowym spawaniu z niewielką spoiną. Urządzenie spawalnicze Fronius TPS 320i spełnia wszystkie te wymagania”.
W Knoll cienka blacha spajana jest metodą spawania łukiem pulsującym. Dzięki temu nie powstaje dużo odprysków i materiał nie jest wypaczany. Inteligentna funkcja Synergic impulsowego spawania MIG/MAG w TPS 320i oferuje fachowcom z Knoll proces łuku pulsującego ze sterowanym przejściem materiału. W tym procesie, w fazie prądu podstawowego, doprowadzanie energii jest zredukowane na tyle, że łuk spawalniczy tylko jarzy się stabilnie i podgrzewa powierzchnię elementu spawanego. W fazie prądu pulsującego, dokładnie dozowany impuls prądowy pozwala na zdefiniowane oderwanie kropli materiału spawanego. Obie te fazy składają się na precyzyjne, bezodpryskowe spawanie w całym zakresie mocy. Niepożądane zwarcia z jednoczesną eksplozją kropli i niekontrolowanymi odpryskami spawalniczymi są prawie wykluczone. Również zapłon SFI (spatter-free ignition) przyczynia się do zapobiegania niepotrzebnym odpryskom.
„Podczas spawania łukiem pulsacyjnym TPS 320i łuk spawalniczy zachowuje się bardzo stabilnie nawet przy niskim natężeniu prądu” – dodaje Kleck. „Jeśli potrzebne nam są łuskowate spoiny, możemy skorzystać z funkcji SynchroPuls, która polega na cyklicznym zmienianiu mocy spawania między dwoma punktami pracy. W sumie przez wiele lat współpracy z Fronius udało nam się mocno usprawnić nasze procesy spawania. Również w przyszłości będziemy wierni tej austriackiej firmie. Ich urządzenia spawalnicze są zaawansowane i łatwe w utrzymaniu. Jeśli potrzebujemy pomocy, nie musimy długo czekać”.
TPS
320i – urządzenie spawalnicze, które komunikuje się w zrozumiały
sposób
Ponad 70 stanowisk spawania ręcznego w Knoll jest
wyposażonych w to zaawansowane urządzenie spawalnicze. Wyróżnia się ono prostą
obsługą za pomocą personalizowanego 7-calowego wyświetlacza dotykowego,
stabilizatorami wtopienia i długości łuku oraz możliwością rozbudowy za pomocą
specjalistycznych pakietów oprogramowania – tzw. Welding Packages. Są to na
przykład LSC (Low Spatter Control), PMC (Pulse Multi Control) i CMT (Cold Metal
Transfer). Jeśli spawacz zaloguje się własną kartą NFC, zostaną automatycznie
wczytane jego osobiste uprawnienia i ustawienia.
Nawigacja w menu jest dostępna w ponad 30 językach. Biorąc pod uwagę, że ze względu na postępujący brak fachowej siły roboczej w Niemczech Knoll coraz częściej zatrudnia spawaczy z innych krajów, „znające różne języki” urządzenia spawalnicze są niezmiernie przydatne. Wyświetlacz urządzenia spawalniczego nie tylko jest wielojęzyczny, ale także komunikuje się w zrozumiały sposób. Szczegółowe opisy i animacje graficzne podpowiadają spawaczom, co mają robić, krok po krok – np. podczas wyrównywania oporności.
W ręcznie wykonywanych zadaniach spawania rewelacyjnie sprawdza się wariant TPS 320i z wbudowanym podajnikiem drutu. Bardzo łatwe zakładanie drutu w tym urządzeniu, które sprowadza się do kilku ruchów dłonią, jest olbrzymią zaletą i ułatwia codzienną pracę spawaczy.
Wszystkie parametry pod stałą kontrolą
Do obsługi urządzenia spawalniczego służy centralny przycisk obrotowy w połączeniu z wyświetlaczem dotykowym. Dużym udogodnieniem jest możliwość szybkiego przełączania (Quick Change) między charakterystykami, procesami i funkcjami. Dotknięcie danego wskazania na pasku stanu wyświetlacza powoduje natychmiastowe przejście do dostępnych parametrów.
Na centralnym wyświetlaczu TPS 320i fachowcy widzą dobrze wszystkie istotne wartości nastawcze i mogą je po kolei regulować. Podczas wprowadzania parametrów pomocą służą innowacyjne animacje. W formie graficznej jest na przykład przedstawione, jak zmieniają się synchronicznie wymiary „a” podczas korekty długości łuku, zależnie od tego, czy korekta jest dodatnia czy ujemna. Służy do tego tak zwana funkcja Synergic, która automatycznie wykrywa wpływ ustawień i korekt na inne mające zastosowanie parametry.
Easy Jobs i aplikacja WeldConnect
Urządzenie reaguje, jak należy, nawet jeśli jest obsługiwane w rękawicach spawalniczych. Często powtarzające się kombinacje parametrów do określonych zadań można zapisać jako spersonalizowane Easy Jobs – za pomocą jednego przycisku. Jeśli na przykład jest spawana blacha o grubości 3 mm, wybierane jest zadanie 1. Do spawania blachy chromoniklowej o grubości 5 mm używane jest zadanie 2. Jeśli podłączony jest uchwyt spawalniczy JobMaster, te zadania można wybierać bezpośrednio w uchwycie. Przydatnym narzędziem do ustawiania zadań spawania jest praktyczna aplikacja WeldConnect Fronius na Androida i iPhone’a. Wystarczy zeskanować kod QR z materiału podstawowego, spoiwa i gazu osłonowego oraz wybrać w telefonie rodzaj spoiny, proces spawania oraz pozycję spawania, a zostaną obliczone wartości, które mogą zostać przesłane za pomocą NFC (Near-field Communication) do TPS 320i lub telefonu komórkowego innego pracownika, aby mógł on je przesłać do swojego urządzenia spawalniczego.
Roboty podnoszą atrakcyjność spawania – także w Knoll
Spawanie nie cieszy się zbyt dobrą opinią. Wielu ten zawód kojarzy się z hałasem, dymem spawalniczym i monotonią. W dodatku jest to praca bardzo wymagająca – tym bardziej, jeśli w grę wchodzą roboty. Ponieważ wówczas oprócz posiadania samej wiedzy z dziedziny spawalnictwa, od elektrotechniki po metalurgię, trzeba także umieć programować. Spawacze, którzy umieją zaprogramować robota, są rozchwytywani i sowicie wynagradzani.
Wiele firm – w tym także Knoll – tworzy dzisiaj programy spawania offline, tzn. na komputerze lub laptopie niebędącym częścią systemu spawania zrobotyzowanego. Nie tylko pozwala to zminimalizować przestoje – dużą zaletą jest możliwość symulacji spawania na cyfrowym bliźniaku: Oprogramowanie wykrywa limity osi, oblicza punkty startowe, położenia końcowe i drogi najazdu oraz wyznacza samodzielnie wyuczone punkty. Wystające kontury są wizualizowane, aby na czas skorygować ustawienia uchwytu – jeszcze zanim zostanie zespawana pierwsza spoina.
Z cobota korzysta się już także w firmie Knoll. Jest on prosty w obsłudze i nie wymaga umiejętności klasycznego programowania. Podczas tworzenia ścieżki spawania przesuwa się uchwyt spawalniczy punkt po punkcie wzdłuż linii spojenia i kolejno je zapisuje. Oprogramowanie automatycznie oblicza ścieżkę oraz sekwencję spawania i zapisuje, aby można było z nich korzystać podczas późniejszych zadań. System, którego używa Knoll, jest wyposażony w technologię CMT. Ze względu na bardzo stabilny łuk spawalniczy i wynikające z tego zmniejszenie ilości ciepła wprowadzanego do spoiny i powstających odprysków „zimny” proces spawania MIG/MAG Fronius jest obecnie powszechnie stosowany w budowie instalacji technicznych, maszyn, elektrowni i samochodów, w przemyśle lotniczym i spożywczym oraz technice medycznej. Jego bezkonkurencyjne zalety są odczuwane zwłaszcza podczas spawania cienkiej blachy.
„Obsługa cobotów jest intuicyjna i ma nawet pewien fun factor. Podoba się to zwłaszcza młodszym spawaczom. Spawanie cobotem jest dla nich cool – również dlatego, że jest równie nieskomplikowane jak obsługa smartfona. Każdy, kto potrafi się posługiwać takim urządzeniem, opanuje obsługę cobota w ciągu kilku godzin. Jeśli jest on zabudowany i wyposażony w odciąg, spawaczom nie grozi także styczność z dymem spawalniczym” — Holger Kleck jest prawdziwym entuzjastą cobotów.
Nacisk na jakość – ale z sercem
W typowy dla Szwabii sposób, dwaj dyrektorzy zarządzający Matthias i Jürgen Knoll dbają nie tylko o rozwój społeczny miasta Bad Saulgau, które hojnie wspierają sponsoringiem, ale także o jakość w spawaniu. Do tego potrzebni im są fachowcy, którzy będą podtrzymywali wysokie standardy przyjęte przez firmę. Ze świadomością tego sukces firmy postrzega się w Knoll przede wszystkim jako sumę działań wielu kompetentnych pracowników, którzy z dużym zaangażowaniem pracują dla przedsiębiorstwa. Zyski służą rozwojowi zakładu i są reinwestowane w przedsiębiorstwo. W Knoll myśli się w kategoriach pokoleń, a nie wyników kwartalnych. Przynosi to korzyści regionowi i pracownikom.
Zdrowie i bezpieczeństwo przede wszystkim
Zdrowi pracownicy nie są wcale oczywistością – gorliwi również nie. Ponieważ jedno zależy od drugiego, w Knoll kładzie się nacisk na ergonomię miejsc pracy oraz jak najlepsze środki ochrony indywidualnej. Wszystkie stoły spawalnicze są wyposażone w regulację wysokości, a samościemniające przyłbice spawalnicze z filtrami powietrza od dawna są standardem. Ponadto powietrze w pomieszczeniu jest wymieniane cztery razy na godzinę.
„Ergonomia w miejscu pracy to ważny temat” – podkreśla Riebsamen. „Ma ona nie tylko wymiar zdrowotny, ale także ekonomiczny. Nieskomplikowana, indywidualna obsługa, krótkie dystanse między elementem a urządzeniem spawalniczym – wszystko to działa motywująco, pozwala zaoszczędzić czas i podnosi wydajność spawaczy”.
Duże znaczenie ma też oczywiście jakość i bezpieczeństwo elementów. Fachowcy z Knoll znają różne metody kontrolowania poszczególnych elementów, jak np. badania penetracyjne (PT – Penetration Testing). To szybka i skuteczna metoda, która uwidacznia rysy na powierzchni i inne wady, jak pory. Nadaje się również do skomplikowanych geometrii i można nią kontrolować wszystkie elementy spawane, niezależnie od wielkości. Nawet małe, niewidoczne gołym okiem wady są wykrywane w ramach badania PT i mogą zostać usunięte przez spawaczy.
Badanie penetracyjne polega na pomalowaniu farbą fluorescencyjną powierzchni badanego elementu spawanego. Wnika ona w rysy, pory i wady powierzchniowe. Następnie powierzchnia jest oświetlana specjalną lampą lub spryskiwana wywoływaczem. Otoczone farbą fluorescencyjną wady są natychmiast widoczne dla wykonawcy badania.Kierując się swoim credo „it works”, Knoll Maschinenbau GmbH bez problemu dostarcza niezawodne systemy i urządzenia swoim klientom.