Najwyższa jakość dzięki zastosowaniu inteligentnych systemów wspomagających spawanie zrobotyzowane
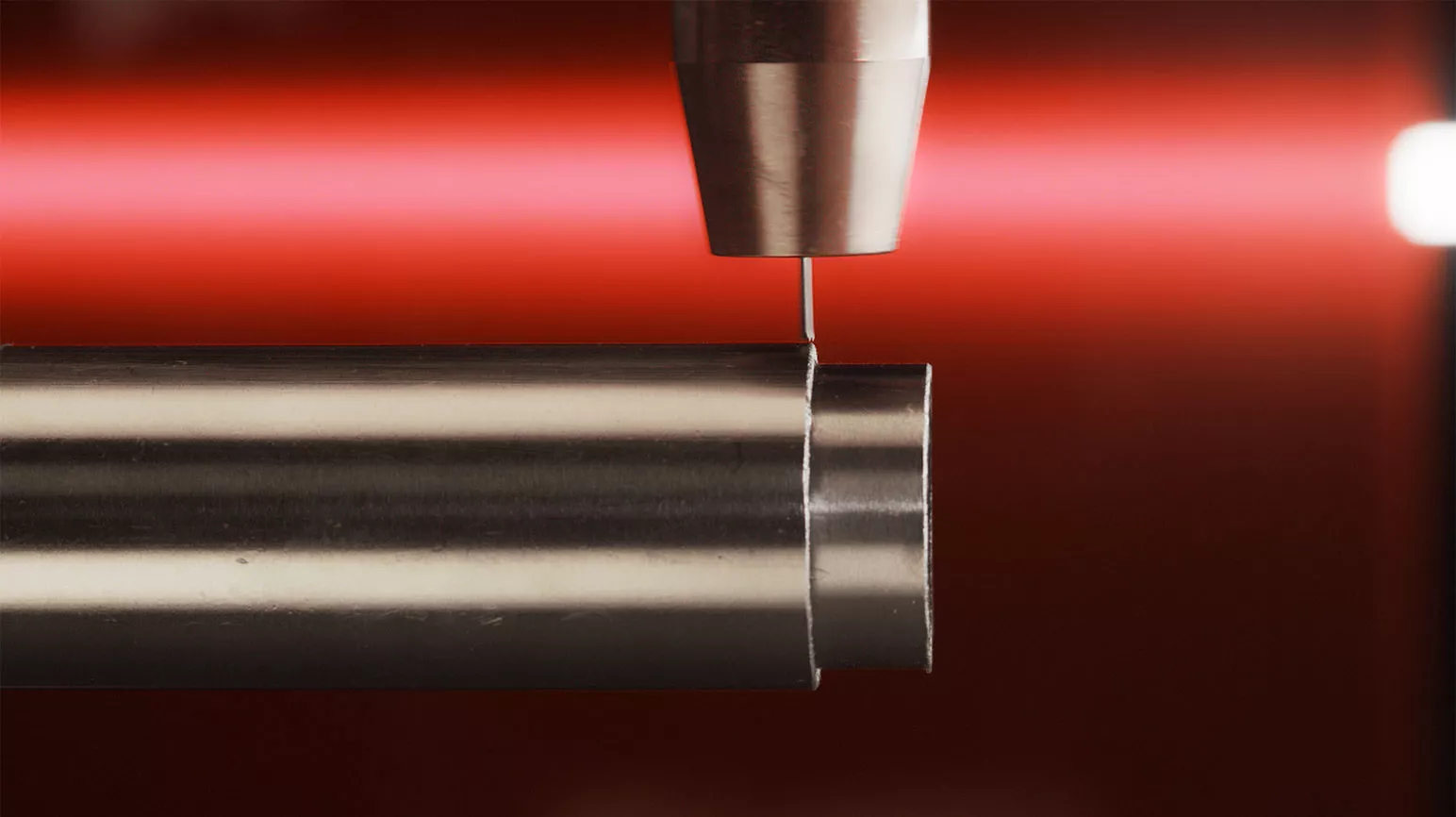
Mimo wysoce zaawansowanych rozwiązań technicznych spawania zrobotyzowanego i niemal idealnie współpracujących ze sobą systemów, podczas produkcji przemysłowej wciąż pojawiają się niedokładności i odchylenia. Już minimalne różnice materiałowe lub niedokładności zamocowania mają wpływ na rezultat spawania. Możliwymi skutkami są pracochłonne poprawki, drogie wybrakowania lub masowa utrata płynności procesów.
Dlatego aby przeciwdziałać czasochłonnym, ręcznym ingerencjom podczas korekt, integratorzy często sięgają po wizualne pomoce pomiarowe. Ale: Zakup i konserwacja systemów laserów i kamer są kosztowne, a systemy te potrzebują miejsca, przez co ograniczają dostępność do elementu. Firma Fronius znalazła właściwe rozwiązanie tego problemu i udostępnia supernowoczesne rozwiązania dla inteligentnych systemów spawania iWave, TPS/i i TPS/i TWIN, które nie wymagają ani kamer, ani ręcznej regulacji.
Seryjnie wykonywane, idealne spoiny pomimo tolerancji mocowania i elementów
System wspomagający TouchSense zaprojektowano specjalnie do spoin pachwinowych. Robot przed każdym spawaniem automatycznie dotyka łączonych blach na początku i końcu spoiny. Przy tym nieważne, co wywoła styk — drut elektrodowy czy dysza gazowa — system zawsze jednoznacznie przypisze sygnał i prawidłowo go przekaże. Podczas zetknięcia, niskie napięcie czujnika wytwarza zwarcie. Umożliwia to robotowi dokładne określenie położenia spoiny i dynamiczne dostosowanie parametrów spawania. Ponadto bardzo pomocne jest też natychmiastowe ostrzeżenie, gdyby między końcówką prądową a dyszą gazową powstał mostek z odprysków. W ten sposób można je odpowiednio wcześnie oczyścić, co zwiększa precyzję i jakość produkcji.
WireSense — wyjątkowa precyzja dzięki technologii CMT
Genialność WireSense leży w jego prostocie. „Rozbudowaliśmy nasz wysoce czuły i dynamiczny napęd CMT o specjalne oprogramowanie regulujące. W ten sposób drut spawalniczy staje się czujnikiem i może bezpośrednio wykrywać kontury lub odchylenia rowkowe bezpośrednio w elemencie”, opowiada Philipp Schlor, Strategic Product Manager, Industrial Welding Solutions w firmie Fronius International. Aby zagwarantować precyzyjną kontrolę drutu spawalniczego, wystarczy wyposażyć system spawania firmy Fronius w system CMT Ready. WeldingPackage, a więc sam proces spawania CMT (Cold Metal Transfer) nie jest do tego potrzebny.
Systemy CMT Ready składają się z podajnika drutu z zasobnikiem lub szpulą drutu i bufora drutu i zespołu napędowego CMT Robacta Drive, a więc drugiego podajnika drutu, bezpośrednio przyłączonego do uchwytu spawalniczego. Poprzez rewersyjny ruch drutu z częstotliwością ok. 100 Hz silnik elektryczny zespołu napędowego skanuje drutem powierzchnię metalu. Dopiero taki wysokiej częstotliwości kontakt z elementem spawanym zapewnia osiągnięcie potrzebnej dokładności. Nawet jeśli badana powierzchnia ma nierówności, np. w przypadku krzywo ułożonych blach, można bez problemu wykryć i zmierzyć krawędź.
Wykrywanie położenia krawędzi i wysokości rowka
„Nasza rewolucyjna technologia WireSense wykorzystuje funkcję skanowania ruchu drutu CMT w celu określenia dokładnej pozycji komponentu, a także pozycji krawędzi i wysokości szczeliny. Można szybko i dokładnie mierzyć blachy, zarówno ze stali, jak i stali nierdzewnej oraz aluminium, o grubości od 0,5 do 20 mm”, podkreśla Schlor. Względem punktu odniesienia, zdefiniowanego przy rozpoczęciu skanowania, można z najwyższą dokładnością zarejestrować każde podwyższenie i obniżenie powierzchni elementu. Błyskawicznie robot porównuje zaprogramowane położenia ze zmierzonymi — tzn. przeprowadza kompensację zapisanych danych o położeniu z obecnie stwierdzonymi danymi. Jeżeli wykryje różnice, robot odpowiednio kompensuje przebieg spoiny w układzie współrzędnych i spawanie następuje we właściwym miejscu.
„Dzięki WireSense integratorzy robotów mają do dyspozycji wiele możliwości, aby znaleźć rozwiązania zapewniające wysoką jakość dla stawiających wyzwania zadań spawalniczych”, zdradza Schlor: „Krawędź spoiny do spawania nie musi być bowiem koniecznie wykrywana. Za punkt wyjścia, od którego można spawać w określonym odstępie, może służyć każda stała krawędź odniesienia elementu, np. krawędź elementu lub wycięcie. W ten sposób można w wybranych pozycjach spawać też trudno wykrywalne części, przykładowo zaokrąglone blachy”.
Niezawodne wypełnianie rowków
W przypadku WireSense drut elektrodowy pełni też funkcję czujnika wysokości. W ten sposób można na przykład na podstawie dokładnie wymierzonej wysokości krawędzi blachy wykryć rowek w połączeniach zakładkowych. W celu uzyskania idealnego rezultatu można wcześniej dokładnie określić, które z zadań zapisanych w pamięci systemu spawania firmy Fronius system wykona, gdy wymiary rowków będą różne. Wskutek tego robot może zawsze adekwatnie zareagować i przeprowadzić spawanie z takimi parametrami, które są idealnie dostosowane do wymiarów danego rowka. Zapobiega to powstawaniu błędów spawalniczych i konieczności czasochłonnych poprawek.
SeamTracking: seam tracking during welding
This assistance system plays to its strengths when it comes to manufacturing railroad or construction vehicles. When thick sheets or long seams are being welded, the heat input can lead to component distortion. To ensure the robot still welds in the right location, a system is needed which reliably detects the welding position during welding, such as on a fillet weld or prepared butt weld.
To do so, the robot moves back and forth between the two sheets during welding. The controller converts the actual values identified into signals for the robot controller. The robot then uses these signals to identify the specified welding position, or possible deviations from it, and corrects the path automatically to ensure welding takes place reliably and in the correct location.
Program robots up to 30 percent faster
The key to high quality lies in teaching the correct welding path. The tried-and-tested TeachMode assistance system helps the welder set the weld seam positions on the robot, making the programming process extremely easy. The reversing wire movement prevents the wire from bending in the event of contact with the component and saves the user from having to remove the deformed wire or re-measure the stickout.
Wire-based assistance systems save time, money, and resources
Using the existing wire electrode as a sensor not only reduces expenditure and maintenance costs for additional sensor hardware, but also frees up space as access to the component is not restricted in any way. At the same time, the Fronius assistance systems cut rejects and time-consuming rework because welding is performed reliably at the correct location. Subsequent re-programming of robot paths is also minimized as the robot can correct the weld seam path by itself. All these factors increase efficiency in production while also reducing the amount of time spent and material used.
Video material:
WireSense: https://www.youtube.com/watch?v=C0YawfPs_Tk
TeachMode: https://www.youtube.com/watch?v=95zvimzn0s0
TouchSense & SeamTracking: https://www.youtube.com/watch?v=16rglvD8qLc&t=3s