SAG – proste zmniejszanie emisji CO2
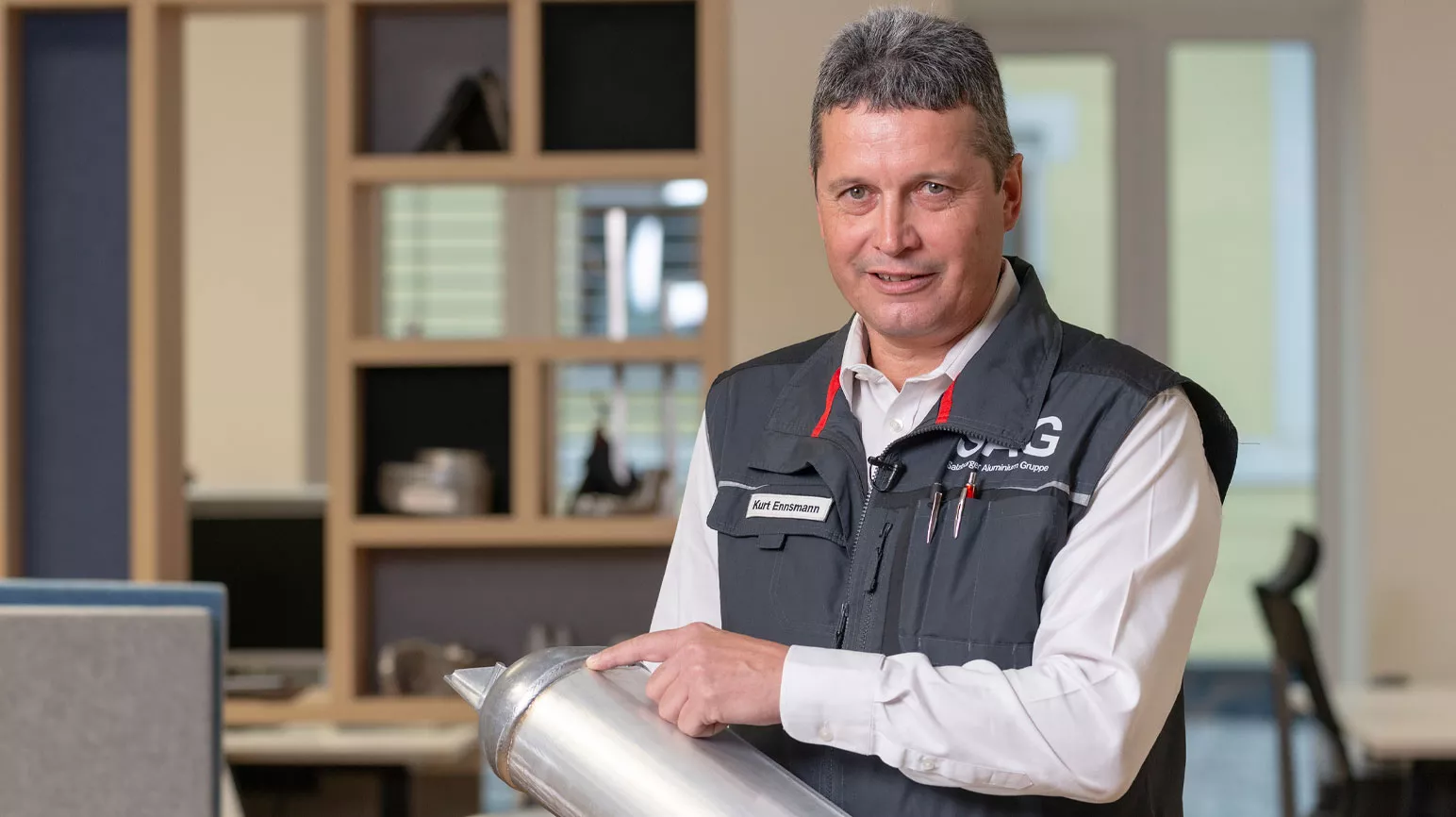
SAG Group wywodzi się z założonego w 1898 r. przedsiębiorstwa Salzburger Aluminium AG i zatrudnia obecnie około 1100 osób w 9 zakładach w Europie, Meksyku i USA. W Austrii zakłady produkcyjne znajdują się w Lend i Schwarzach, niedaleko Salzburga, i około 200 km od Monachium. Jako duży producent zbiorników aluminiowych do samochodów ciężarowych SAG jest globalnym dostawcą dla wielu znanych OEM. Ze stopów metali lekkich firma wytwarza też elementy zawieszenia, zbiorniki powietrza, zbiorniki ciśnieniowe, a także wiele specjalnych podzespołów do samochodów osobowych i użytkowych oraz pojazdów szynowych i specjalnych.
Do produkcji szczególnie wytrzymałych elementów ze stopów metali lekkich jest stosowana specjalna technologia odlewania tiksotropowego, która została dopracowana przez SAG Group w toku wieloletnich prac badawczo-rozwojowych. Metoda ta polega na tym, że aluminium jest prasowane w maszynie do odlewania ciśnieniowego nie w formie płynnej, lecz półpłynnej (półstałej), a następnie przetwarzane na elementy ze stopów metali lekkich dla przemysłu motoryzacyjnego. Laminarny, prawie pozbawiony turbulencji proces napełniania zapobiega niepożądanym wtrąceniom gazu podczas odlewania. Puste przestrzenie, tak zwane jamy skurczowe, są zalewane ze względu na kurczenie się tężejącego stopu. Dlatego odlewy tiksotropowe są ze względu na swoją niską porowatość bardzo dobrze spawalne.
„SAG Group jest liderem w zakresie technologii produkcji zbiorników kriogenicznych na skroplony gaz ziemny (LNG) i ciekły wodór (LH2)” – tłumaczy Kurt Ennsmann, Head of Engineering, i dodaje: „Tak samo jest z odlewaniem tiksotropowym. Jest to technologia odlewania ciśnieniowego z półstałego metalu, którą stosujemy do produkcji seryjnej podzespołów motoryzacyjnych, jak obudowy elektroniki, wsporniki osi lub zbiorniki ciśnieniowe do zawieszeń pneumatycznych”.
W branży motoryzacyjnej ta metoda jest nadal rzadko spotykana. A przecież w porównaniu ze stalą odlewy tiksotropowe są nawet o 60% lżejsze! Ze względu na olbrzymią oszczędność na masie i inne ważne zalety nowatorski proces odlewania został nagrodzony za innowacyjność przez Volvo.
„Jako jedyni na świecie potrafimy seryjnie spawać zbiorniki ciśnieniowe wykonane częściowo z odlewów tiksotropowych, tak aby spojenia nie przepuszczały helu” – mówi z dumą Stefan Griesebner, Technology Expert Rheocasting. „Robimy to w technologii CMT i WireSense firmy Fronius, aby sprostać naszym własnym wymogom jakościowym”.
WireSense kompensuje różnice między szczelinami
Zanim po wielu próbach z różnymi systemami wspomagania i czujnikami przeprowadzono wreszcie testy z WireSense, w SAG nie było idealnego rozwiązania na kompensowanie niedokładności produkcyjnych, jak na przykład różnice w wymiarach szczelin podczas spajania. Szkodziło to procesowi spawania i ze względu na nieustanne, nieakceptowalne w ich rozmiarach poprawki, wpływało negatywnie na czasy produkcji.
Różnice między elementami, jak odmienne wymiary szczelin i tolerancje pasowania, mogą powodować olbrzymie problemy podczas spawania. W najgorszym razie zmienia się przez to pozycja spawania i występują braki przetopu w spoinie. Dlatego w wielu zakładach przemysłowych są używane mierniki optyczne do spawania zrobotyzowanego – tak zwane czujniki śledzenia spoiny. Są one drogie, zajmują miejsce przed korpusem uchwytu spawalniczego i zasłaniają element spawany. To z kolei utrudnia stosowanie kamer i laserów. Poza tym trzeba je regularnie czyścić i wymagają dodatkowej kalibracji odległości między Tool Center Point (TCP) a czujnikiem. WireSense firmy Fronius jest prostym, inteligentnym zamiennikiem, który jest pozbawiony tych ograniczeń.
Zasada działania WireSense
Technologia WireSense nie potrzebuje żadnych elementów sprzętowych, ponieważ funkcję czujnika pełni drut elektrodowy, który skanuje element za pomocą dwustronnych ruchów powtarzających się z wysoką częstotliwością. Przed rozpoczęciem tego procesu skanowania do drutu spawalniczego jest przykładane nadzwyczaj niskie napięcie czujnika i jednocześnie prąd jest zmniejszany do minimum. Gdy po rozpoczęciu procesu WireSense robot dojedzie do wymaganej pozycji, w następnym kroku drut spawalniczy dotknie elementu, co wywoła zwarcie bez zajarzenia łuku. Zwarcie zostaje następnie przerwane przez uniesienie drutu. Zmiana pozycji spawania powstała w chwili zwarcia jest analizowana przez inteligentne urządzenie spawalnicze TPS/i za pomocą specjalnych algorytmów oceny i udostępniana jako sygnał pomiaru wysokości. Kierunek ruchu drutu jest zmieniany w cyklu milisekundowym. Na podstawie analizy poszczególnych informacji o wysokości robot nie tylko ustala przebieg krawędzi i położenie poszczególnych blach względem siebie, ale także faktyczną wysokość krawędzi.
Jeśli jest wykonywane połączenie zakładkowe, jak w zbiornikach ciśnieniowych SAG, WireSense wykrywa przebieg spoiny, reaguje na ewentualne odstępstwa i koryguje pierwotnie utworzony program spawania.
WireSense działa równie dobrze podczas spawania stali, w tym także nierdzewnej, aluminium, a także innych stopów. Ten system wspomagający Fronius jest szczególnie przydatny w przypadku aluminium, czyli głównego materiału używanego w SAG Group: odbijająca światło powierzchnia tego materiału sprawia trudności optycznym systemom pomiarowym – WireSense nie robi ona żadnej różnicy.
Technologia CMT jako warunek podstawowy
WireSense może działać z dowolnym systemem spawania TPS/i Fronius, którego konfiguracja dopuszcza proces spawania CMT. Kluczową rolę odgrywa precyzja ruchu drutu wynikająca z koordynacji podajnika drutu na bębnie z drutem, bufora drutu i drugiego podajnika drutu Robacta Drive CMT, który jest umieszczony bezpośrednio na korpusie uchwytu spawalniczego. W trakcie rewersyjnego ruchu drutu wykonywanego z częstotliwością około 100 Hz jest skanowana powierzchnia metalu i na tej podstawie jest wykrywany kontur spoiny. W przypadku posiadania systemu spawania TPS/i bez WireSense można go w dowolnym momencie doposażyć w tę funkcję.
Dzięki WireSense SAG Group udało się usprawnić spawanie zbiorników ciśnieniowych, zminimalizować ilość poprawek i w ten sposób poprawić rentowność produkcji.