Schweisstec 2019: Fronius to present new systems and process variants: High performance welding made easy
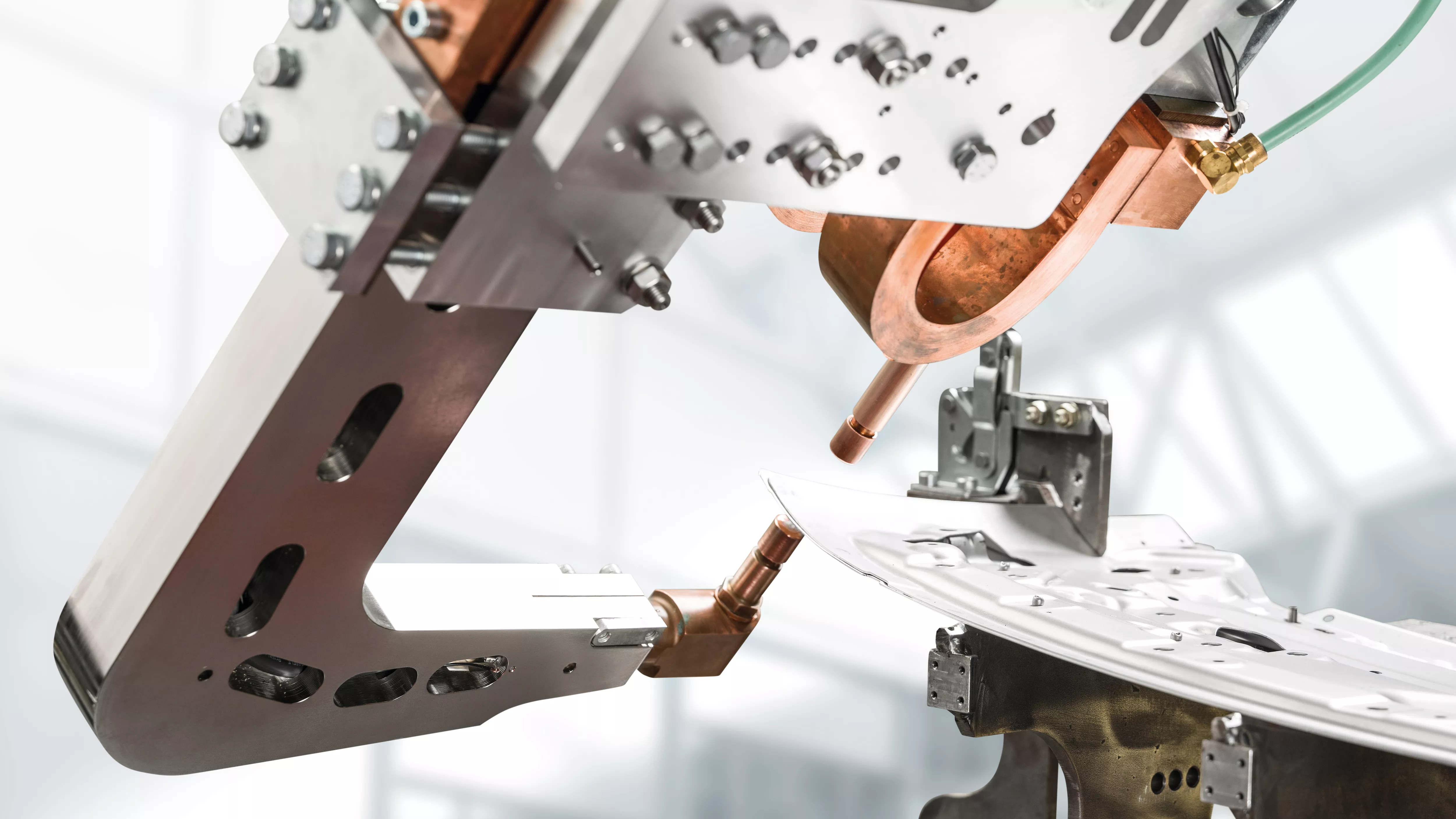
Fronius is now also offering its tandem welding process on the TPS/i platform. The TPS/i TWIN Push high performance welding system stands out due to its high deposition rates and welding speeds, user-friendliness and networking capabilities. All of this means that it is particularly suited to joining large volumes of components or long weld seams for construction machinery and commercial vehicles, or for use in the automotive and shipbuilding industries. The excellent processor performance of the TPS/i has optimised the synchronised TWIN Push tandem process, making it even more stable, precise and reliable. As the user has to spend less time on rework, production efficiency is increased considerably.
Fronius has launched a new version of its current power source platform – the TPS/i Steel Edition. It has been optimised for manually welding steel and impresses with an attractive price-performance ratio. Users benefit from a variety of characteristics for standard and pulse welding, as well as a WPS package with welding procedure specifications certified to DIN EN 1090. The TPS 600i high performance welding system will also be on show at Schweisstec. Above all, it stands out due to its long duty cycle and can continuously weld at an amperage of 500 A in mechanised applications. This not only enables high deposition rates and welding speeds, but ensures shorter cycle times and increased productivity.
Fronius will also be showcasing its comprehensive range of powerful manual welding systems for industry, trade and the DIY sector. For example, the compact TransSteel 2200 three-in-one system combines MMA welding, gas metal arc welding (MIG/MAG) and tungsten inert gas welding (TIG) in a single power source. With its wide variety of characteristics, the TransSteel 2200 is a true all-rounder that ensures users will achieve excellent results with every welding process. The MagicWave 230i TIG power source can communicate and network with other devices via Bluetooth, WLAN and NFC technology. Thanks to the USB ports, software updates can be installed and welding data can be documented with ease.
Fronius will also be presenting a compact system for automated circumferential welding in the shape of the FCW Compact. This enables users to weld components such as pipes, flanges, reducers, fittings and valves horizontally or vertically. The system is equipped with the modified ArcTig TIG welding process, which can weld components up to ten millimetres thick without extensive seam preparation, to an exceptionally high quality standard and much quicker. Comprehensive networking, remote control and data analysis functions complete the overall package.
For conventional resistance spot welding, Fronius has developed a new generation of spot welding guns – DeltaCon. These guns make spot welding aluminium sheets straightforward and cost effective. DeltaCon guns are available in a variety of different versions, both with and without welding gun adjustment. They also have a modular construction that uses the same main components in both the X-type and C-type geometries. Users are therefore able to perform a wide variety of welding tasks. The compact design ensures good accessibility, even in restricted spaces.
Welding systems from Fronius can be optionally networked with the WeldCube documentation and data analysis software, which collects data on factors such as current, voltage, wire speed and welding speed. This information is key to improving welding processes and optimising the use of materials, gas and filler metals. A customisable dashboard with a number of statistics and filter functions provides users with a clear overview on their PC, tablet or smartphone. Networking power sources makes it possible not just to document data on a machine level, but also on a component level, increasing both transparency and traceability.