Dump trucks for tough construction site conditions
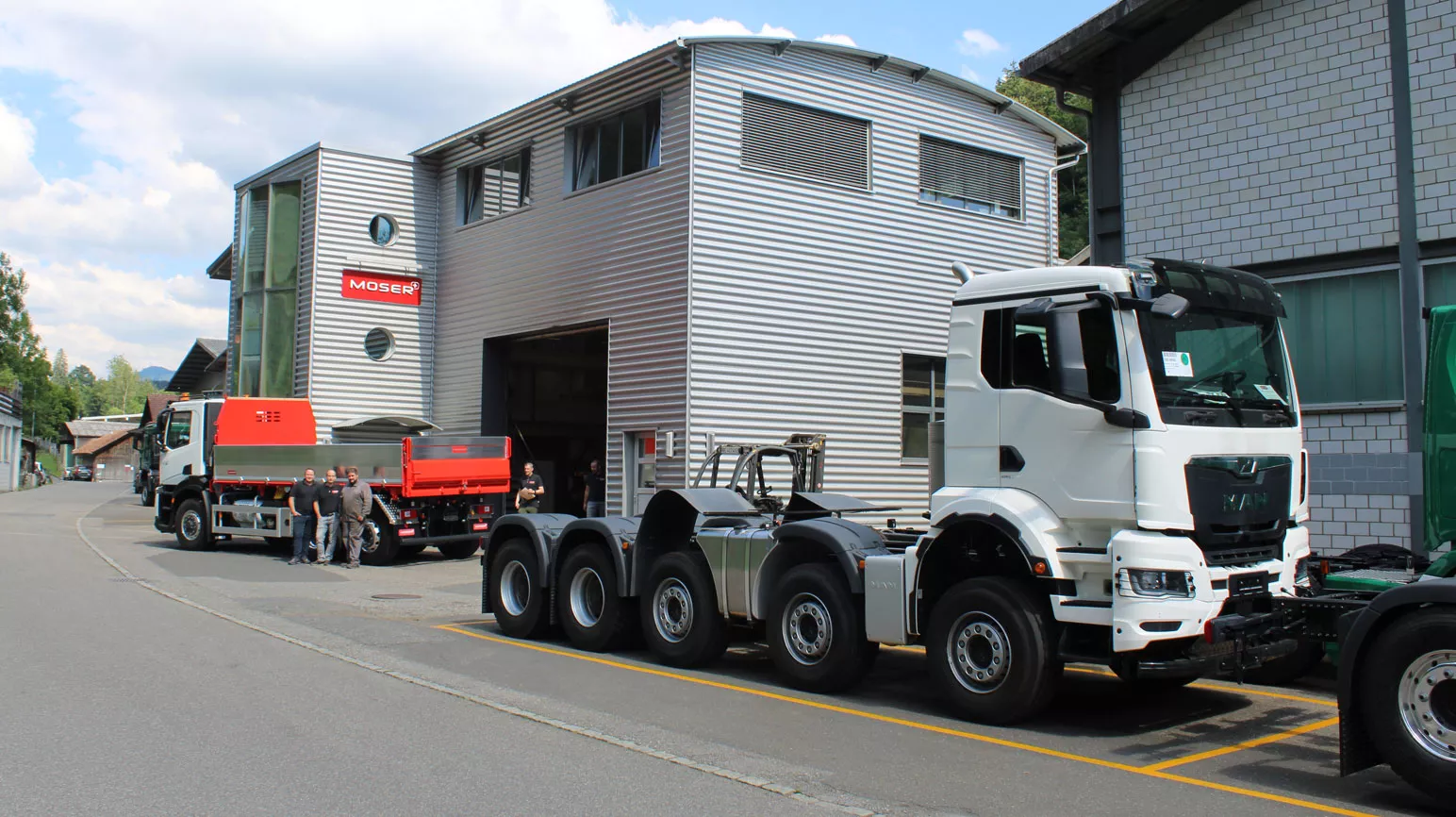
Reduced tare weight: “Always one load ahead”
Moser AG manufactures vehicle superstructures for trucks with a total weight of between 18 and 40 tons, with 40-ton trucks capable of taking more than 25 tons of payload. “The highest possible transport volumes per trip are the top priority in our industry. To enable our customers to transport as much material as possible with a specified total weight, we design our dumpers and loading systems to be as light as possible – without compromising on strength, durability, or user-friendliness,” emphasizes Stefan Rolli, operations manager at Moser AG.
Depending on the size and number of axles on the vehicle in question, the truck superstructures produced in Steffisburg usually weigh between 3 and 4.5 tons. “The benefit in terms of payload for our customers from using our lighter superstructures compared to competitors is often between 500 and 700 kg per trip. This results in much more efficient use of the vehicles in line with our motto ‘Always one load ahead’,” says Stefan Rolli.
Customer proximity favors customization
The superstructures custom-made by Moser AG to meet individual customer requirements fit all common truck types. The company, from the Canton of Bern region, is particularly proud that all dumpers and loading systems - from the supplied sheet metal and profiles onwards - are produced at the company's site in Steffisburg.
“Today, we are the only company in Switzerland that manufactures commercial vehicle superstructures for the construction site sector with such a high real net output ratio. Control over all key production processes and our proximity to our customers mean that we can respond to special requests very quickly and flexibly,” explains Moser operations manager Stefan Rolli.
More than 200 trucks leave the Steffisburg plant every year, and the manufacturing time for a new dumper is 6 to 8 weeks on average.
Manufacturing processes at a glance
The manufacturing processes at Moser AG are essentially divided into the following steps: The trucks are measured thoroughly after delivery. Once the superstructures have been designed with the help of CAD and production planning, the next steps involve cutting the sheets on a CNC plasma cutting machine, bending them with a CNC press brake, and further mechanical processing in a CNC machining center.
In the metalworking shops of Moser AG, the components are welded together, finishing the raw form. The truck superstructures are then sandblasted and painted. After installation of the hydraulics, pre-assembly and final assembly take place. Before a truck and its new superstructure leaves Moser AG in Steffisburg for its new destination, it is subjected to a thorough final inspection.
Welds in all components
“Welds are found in virtually all our components. In day-to-day construction site use, they have to withstand shocks, vibrations, and torsion – for example, when boulders weighing several tons hit the dumper from the bucket of a wheel loader. Since faulty seams have serious consequences, our requirements regarding the professionalism of our welders and the equipment they use are extremely high,” emphasizes Stephan Zingg, design engineer at Moser AG. Particular attention is paid to flawless welds in the load-bearing components such as the dumper substructure or subframe.
Steel and aluminum up to 70 mm
At Moser, conventional S355 construction steel, steels from S690 to S700, and Hardox 450 in various thicknesses from 3 mm to 70 mm are welded when manufacturing the truck superstructures. The material most frequently used is 4 mm-thick Hardox 450 sheet.
The aluminum sheets processed in Steffisburg generally have a thickness of 2 mm, and aluminum checker plates are 3/4.5 mm or 3/6.5 mm thick. Last but not least, relatively light aluminum alloys are used for the side walls of the dumpers. These are extruded using a casting mold developed by Moser AG, and the MAP Moser Aluminum Profile System enables modular construction of the side walls. Other application areas for aluminum sheets include fenders, covers, and running boards.