Magna Presstec : l’avenir de l’industrie automobile
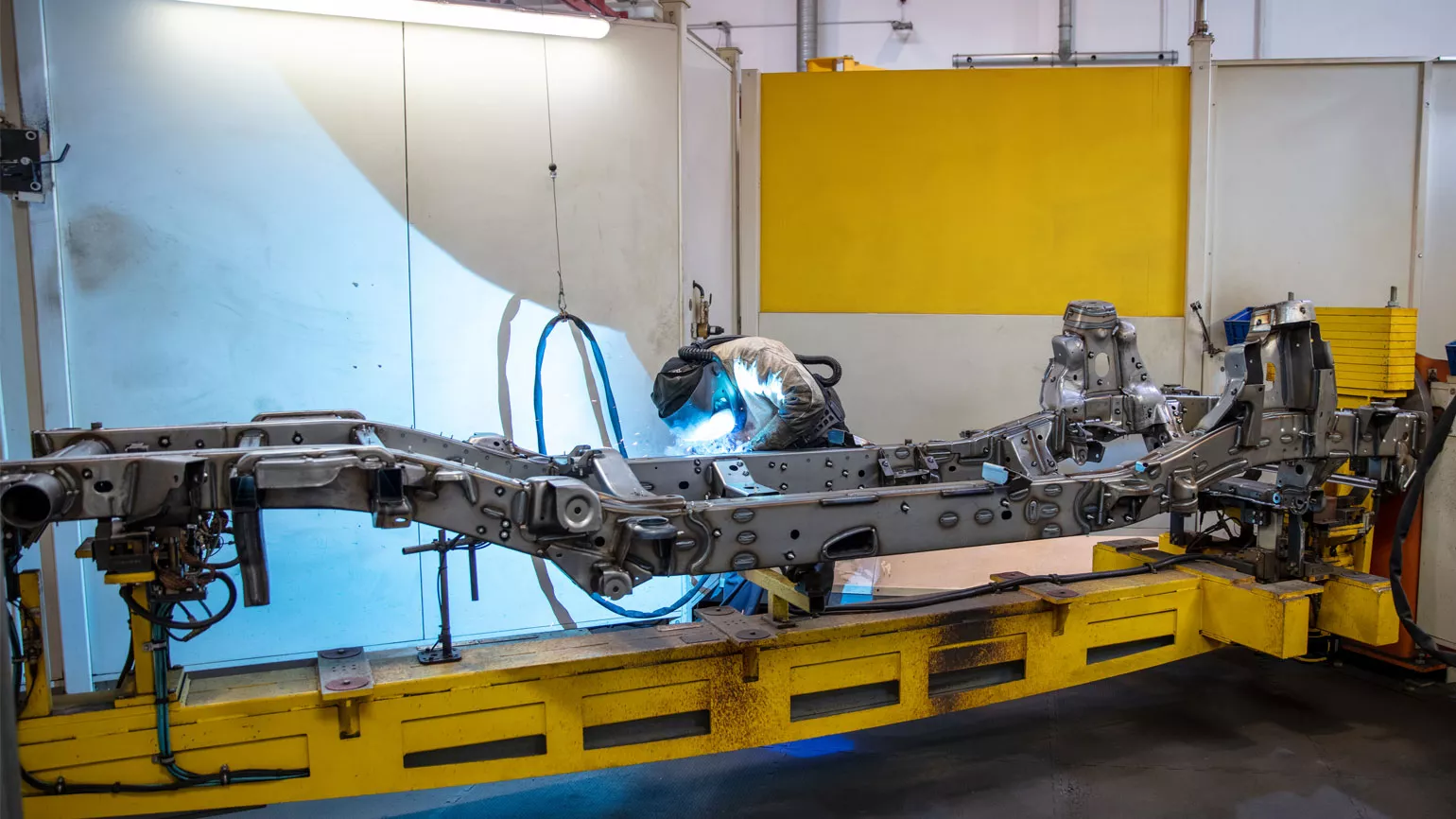
L’équipementier automobile Magna a aménagé une infrastructure de production optimale dans les environs de Graz : à Lebring, au sud-est de Graz (à une demi-heure en voiture), l’entreprise Magna Presstec GmbH fabrique la base du modèle de la Classe G. À Graz, Magna Steyr Fahrzeugtechnik AG & Co KG apporte ensuite la touche finale au tout-terrain premium
La base d’une voiture iconique
« Au sein du groupe Magna qui emploie environ 158 000 personnes à travers le monde, Magna Presstec fait partie du groupe d’entreprises COSMA (Body and Chassis) », explique Kurt Hartmann, responsable de la qualité et de la coordination en soudage de la ligne de production des cadres de châssis de la Mercedes Classe G. Presstec elle-même emploie environ 1 200 personnes, réparties entre les sites autrichiens de Weiz et Lebring ainsi que le site slovaque de Bratislava.
L’équipementier automobile fabrique des composants de châssis et des éléments de structure de haute qualité en aluminium et en acier. « Nous comptons parmi nos clients VW, Audi, BMW, Daimler et Porsche. Nous façonnons l’avenir de l’automobile avec passion et en nous impliquant personnellement », poursuit M. Hartmann.
Les véhicules tout-terrain high-tech nécessitent des soudures de qualité optimale
La Mercedes Classe G est considérée comme l’un des véhicules les plus adaptés à la fois au tout-terrain et au quotidien dans le monde entier. Comme on peut le deviner en voyant son énorme garde au sol et la profondeur de gué : le véhicule doit pouvoir résister aux conditions tout-terrain les plus difficiles. La Mercedes Classe G doit présenter une force de traction et une durabilité à toute épreuve pour pouvoir être soumise à des chocs violents à grande vitesse sur des terrains accidentés, comme lors des tests continus de longue durée sur le terrain escarpé du Schöckl près de Graz.
En effet, les véhicules sont testés sous toutes leurs coutures sur un circuit de montagne spectaculaire, c’est pourquoi la construction du cadre de châssis de la Mercedes Classe G doit faire l’objet d’une attention totale. Et il va donc de soi que la qualité des soudures doit également répondre aux exigences les plus élevées
Exigences de la Mercedes Classe G en matière de soudage
« L’acier est majoritairement utilisé sous forme de tôles d’une épaisseur de 2 à 4 millimètres, assemblées au moyen de 657 soudures. La longueur totale des soudures est de 76 mètres par cadre. Pour nous, le défi du soudage consiste essentiellement à construire le cadre de châssis de 4,2 mètres de long, couche par couche, en respectant toujours les tolérances imposées par le client et la qualité de pointe requise, » explique Kurt Hartmann. Hartmann.
Par conséquent, l’équipement de l’installation de production devait répondre à différentes exigences en matière de technique d’assemblage : une grande stabilité de l’arc électrique avec une pénétration parfaite était nécessaire pour pouvoir générer la stabilité indispensable du cadre de châssis massif. La qualité supérieure du produit exige en outre une déformation aussi faible que possible et un apport d’énergie contrôlable. En ce qui concerne la productivité, il fallait également pouvoir atteindre des vitesses de soudage élevées.
« Le process PMC (Pulse Multi Control) de Fronius est celui qui répondait le plus à nos exigences », assure M. Hartmann, lui-même expert international en soudage. « Pour cela, il nous fallait la plateforme de soudage modulaire TPS 500i. Son utilisation devait être simple et nous devions pouvoir la connecter aisément au robot. Actuellement, nous avons 36 de ces systèmes de soudage en service sur la ligne de production de la Mercedes G. En outre, quelques systèmes TPS 320i sont utilisés pour d’éventuels travaux de soudage manuel à des fins de contrôle qualité ».
Production de pointe autonome en detail
« Chaque cadre doit être absolument identique, tout écart est exclu », explique M. Hartmann. La production se déroule dans un hall d’usine de plus de 100 mètres de long, parfaitement équipé. En grande partie autonome, elle répond aux normes les plus strictes et les systèmes robotisés, parfaitement adaptés, fonctionnent parfaitement les uns avec les autres. Il est ainsi possible de voir un cadre de châssis de Mercedes Classe G, robuste et parfaitement assemblé à partir de nombreuses pièces, quitter l’atelier toutes les 10 minutes.
La fabrication se déroule en trois étapes : les structures avant et arrière sont produites simultanément. Quelques collaborateurs commencent par équiper les dispositifs de soudage. Les composants sont ensuite assemblés dans les cellules à l’aide de robots de soudage. Un robot de manutention prend les composants finis, les transporte vers la cellule suivante et les positionne. À la fin de chaque section se trouve une cellule inaccessible aux collaborateurs. Celle-ci sert non seulement à souder les longues soudures, mais elle est également utilisée comme station de refroidissement ou comme station complexe, par exemple pour le « squeezing » : étape dans laquelle les coques inférieures sont alors emboîtées avec les coques supérieures des longerons, mises en position et soudées sous pression.
C’est dans le soubassement, soit à la dernière étape de fabrication, que les parties avant et arrière sont finalement assemblées. Le cadre de châssis prend alors sa forme caractéristique. Les dernières étapes de travail comprennent ensuite le poinçonnage des points d’ancrage découplés pour le châssis et le soudage par arc tiré de 192 goujons sur le cadre. Enfin, la qualité des soudures est contrôlée, les éventuelles projections de soudure sont éliminées et, le cas échéant, les soudures sont retouchées. Pour finir, une technique laser robotisée mesure à nouveau le cadre de châssis avec précision et vérifie qu’il répond à tous les critères de qualité.
Gestion ultra professionnelle des données numériques de soudage
Le processus extrêmement complexe le prouve : chez Magna Presstec, il ne s’agit pas seulement de soudage. Afin de pouvoir garantir un haut degré d’automatisation et une qualité tout aussi élevée pour la ligne de production de la Mercedes Classe G, l’accent a été mis dès le départ sur l’intégration d’outils de surveillance et d’analyse des données de soudage. L’équipementier automobile a cherché à collaborer avec des spécialistes des techniques d’assemblage dont les systèmes et les solutions permettent une traçabilité numérique totale des processus de soudage.
With its WeldCube Premium software package, Fronius was for the first time able to install a comprehensive welding data management system in the production facilities of a Tier 1 supplier, and to demonstrate the benefits of the various software systems being used.
From quality assurance to predictive maintenance:
The WELDCUBE PREMIUM and CENTRAL USER MANAGEMENT software packages
“We've found the perfect partner in Fronius”, enthused Kurt Hartmann. “WeldCube Premium is an important pillar of our quality management system, as the complete traceability of every single weld is incredibly important to us.” Trained operators at the quality control stations are presented with the most accurate information on their terminals: Are there any dubious or real faulty welds? Locations picked out by Fronius WeldCube are subjected to a detailed visual inspection and reworked if necessary. Only then is the G frame released for the next stage in the process. The gathered data are then fed back to help optimize the automated welding processes.
WeldCube Premium charts every millimeter of the weld, making it a simple matter to analyze the cost of consumables such as gas and welding wire. Yet it has much more potential, for example Predictive Maintenance – the ability to order wearing parts and other materials in good time and in sufficient quantities.
“Predictive Maintenance with WeldCube Premium was able to uncover areas of potential savings, for example by having the welding management system specify precise maintenance intervals”, observed Hartmann. “We're always kept fully informed about the condition of contact tips, torch bodies, welding torches and wirefeeders, which means we know exactly when to service the equipment to avoid faulty welds, rework or the scrapping of components.”
Magna Presstec was already a user of the Fronius Central User Management (CENTRUM) system, which it uses in quality management. CENTRUM is where user and welding permissions are centrally managed. Welders use a smart card to identify themselves to the welding system, ensuring that only specially trained operators are allowed to work with the relevant parameters - another way of eliminating potential sources of error.
Magna Presstec has the proof: Welding data management works in the field
Christoph Pangerl, Fronius Key Account Manager for Magna, has no doubts: “The insights gained from the cooperation with Magna Presstec were extremely valuable, as we were able to feed them directly into our product development. It's also allowed us to make our software solutions accessible to a much broader customer base.” Kurt Hartmann continued the theme: “Welding data management in particular has helped us optimize our joining technology in every area. Fronius has given us a really powerful tool that has enormous potential. And with the technical support of Fronius specialists, we've meanwhile been able to deploy the system to improve our bottom line.“