SAG – réduire ses émissions de CO2 en toute simplicité
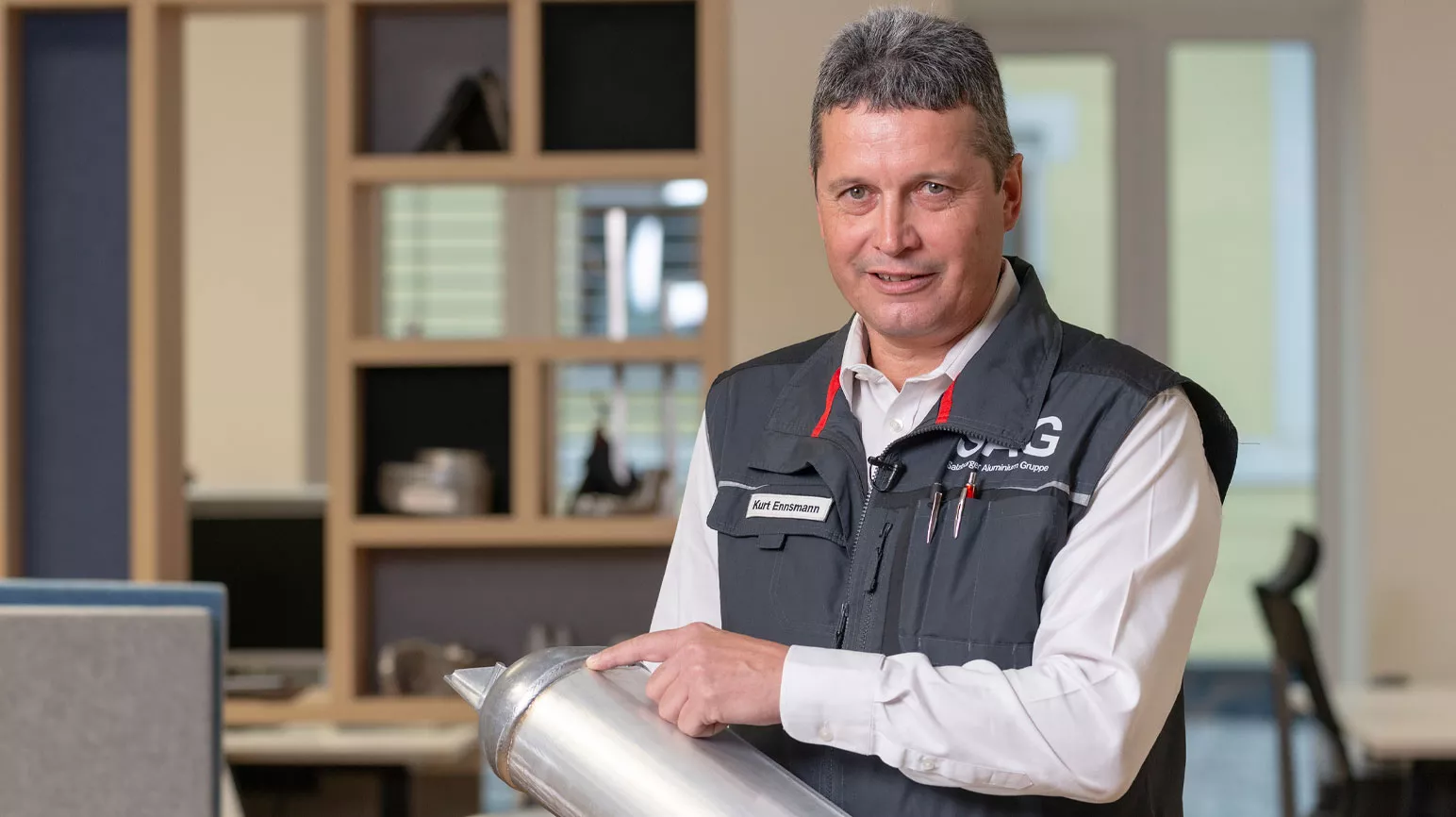
Le groupe SAG est issu de la société Salzburger Aluminium AG, fondée en 1898, et emploie aujourd’hui environ 1 100 personnes sur 9 sites en Europe, au Mexique et aux États-Unis. Les sites de production en Autriche se trouvent à Lend et Schwarzach, non loin de Salzbourg, capitale du Land, à environ 200 km de Munich. En tant que fabricant leader de réservoirs de camion en aluminium, SAG est le fournisseur mondial de nombreux équipementiers de renom. L’entreprise produit également d’autres produits comme des composants légers pour châssis, accumulateurs d’air, réservoirs d’air comprimé ainsi que des composants spéciaux pour l’industrie des voitures particulières, des véhicules utilitaires, des véhicules ferroviaires et des véhicules spéciaux.
La technologie de rhéomoulage spéciale utilisée pour la fabrication de pièces légères particulièrement robustes a fait l’objet de nombreuses années de recherche avant d’être utilisée pour la production en série par l’entreprise SAG Group. Selon cette méthode, l’aluminium n’est pas injecté sous forme liquide comme c’est la cas habituellement, mais sous forme semi-solide (semi solid) dans une machine de moulage sous pression, pour être ensuite transformé en composants légers pour l’industrie automobile. Le processus de remplissage laminaire, pratiquement sans turbulences, évite les inclusions de gaz indésirables pendant le moulage. Les cavités, appelées retassures, sont comblées par le retrait de la masse fondue qui se solidifie. Pour cette raison, les composants fabriqués par rhéomoulage sont très faciles à souder en raison de leur faible porosité.
« Le groupe SAG est un leader technologique en matière de systèmes de réservoirs cryogéniques pour gaz naturel liquéfié (GNL) et hydrogène liquide (LH2) », explique Kurt Ennsmann, Head of Engineering, avant d’ajouter : « C’est la même chose avec le rhéomoulage. Il s’agit d’une procédure de moulage sous pression à l’état semi-solide, que nous utilisons dans la production en série de composants automobiles tels que les boîtiers électroniques, les supports d’essieu ou les réservoirs d’air comprimé pour les suspensions pneumatiques. »
Ce procédé est encore unique dans le domaine de l’automobile. Les pièces fabriquées par rhéomoulage sont jusqu’à 60 % plus légères par rapport à l’acier ! Cette procédure de moulage innovante a également été récompensée par un prix de l’innovation Volvo en raison des énormes économies de poids qu’elle permet de réaliser et d’autres avantages significatifs.
« Nous sommes les seuls au monde à pouvoir assembler en série des réservoirs d’air comprimé partiellement constitués de composants fabriqués par rhéomoulage et étanches à l’hélium », explique fièrement Stefan Griesebner, Technology Expert Rheocasting. « Afin de répondre à nos exigences en matière de qualité, nous utilisons les technologies CMT et WireSense de Fronius. »
WireSense compense les variations d’écartement des bords
Avant de tester WireSense, après de nombreux essais avec divers systèmes d’assistance et capteurs, SAG ne trouvait pas de solution idéale pour compenser les imprécisions de fabrication, comme les variations d’écartement des bords pendant l’assemblage. Cela affectait le process de soudage et a eu un impact négatif sur les temps de production en raison des retouches permanentes, dont l’ampleur était inacceptable.
Les différences entre les pièces comme des écartements ou tolérances de serrage variables peuvent engendrer d’énormes problèmes lors du soudage. Dans le pire des cas, la position de soudage est modifiée et engendre ainsi des défauts dans la soudure. Pour éviter cela, de nombreuses entreprises industrielles utilisent des instruments de mesure optiques pour le soudage robotisé, appelés capteurs de suivi des soudures. Non seulement ces derniers sont chers et positionnés devant le col de cygne, mais leurs cotes d’encombrement entravent également considérablement l’accessibilité à la pièce. L’utilisation de caméras ou de lasers peut donc être problématique. De plus, ils doivent être nettoyés régulièrement et nécessitent un calibrage supplémentaire entre le Tool Center Point (TCP) et le capteur. Avec WireSense, Fronius propose une alternative plus simple et intelligente, sans contrainte.
Voici comment fonctionne WireSense
La technologie WireSense ne nécessite aucun composant matériel car elle utilise le fil-électrode comme un capteur. Celui-ci palpe la pièce avec un mouvement avant/arrière du fil à haute fréquence. Avant que le processus ne démarre, une tension de détection extrêmement faible est appliquée au fil d’apport et le courant est simultanément limité au minimum. Si le robot se déplace à la position souhaitée lors du démarrage du processus WireSense, le fil d’apport palpe ensuite la pièce et un court-circuit se produit sans amorçage de l’arc. Celui-ci est ensuite à nouveau interrompu par le soulèvement du fil. La modification de la position du fil qui apparaît au moment du court-circuit est analysée dans l’appareil de soudage TPS/i intelligent au moyen d’algorithmes d’évaluation spéciaux et préparée comme signal de mesure de hauteur. Les mouvements avant/arrière du fil s’effectuent toutes les millisecondes. L’évaluation des différentes informations de hauteur permet au robot de déterminer non seulement le tracé de l’arête et la position des tôles les unes par rapport aux autres, mais également la hauteur d’arête réelle.
S’il s’agit de cordons de recouvrement, comme dans le cas des réservoirs d’air comprimé de SAG, WireSense reconnaît la trajectoire de la soudure, réagit aux écarts éventuels et corrige le programme de soudage initialement créé. WireSense peut être employé aussi bien pour l’acier que pour l’acier inoxydable, l’aluminium et d’autres alliages. Le système d’assistance Fronius révèle notamment ses qualités avec l’aluminium, le principal matériau utilisé par le groupe SAG : les systèmes de mesure optiques atteignent souvent leurs limites en raison de la surface réfléchissante du matériau, mais ce n’est pas le cas de WireSense.
La technologie CMT : une condition de base
WireSense peut être utilisé avec tous les systèmes de soudage TPS/i de Fronius configurés pour l’utilisation du process de soudage CMT. Le mouvement précis du fil résultant de la coopération entre le dévidoir au niveau du fût de fil, le tampon de fil et la deuxième unité d’amenée de fil Robacta Drive CMT, qui se trouve directement sur le col de cygne, est ici d’une importance capitale. Dans un mouvement avant/arrière qui a lieu à environ 100 hertz, le fil balaie la surface métallique et détecte les contours de la soudure. Pour une première utilisation de WireSense, il est possible d’équiper un système de soudage TPS/i existant à tout moment.
Grâce à l’utilisation de WireSense, l’entreprise Salzburger Aluminium Group a optimisé le soudage des réservoirs d’air comprimé, réduit le nombre de retouches nécessaires et augmente ainsi la rentabilité de la production.
The science behind WireSense
WireSense technology does not require any hardware components—instead the wire electrode is used as a sensor that scans the component with a high-frequency reversing wire movement. Before this scanning process begins, an extremely low sensor voltage is applied to the welding wire and the current is simultaneously reduced to a minimum. When the robot moves to the required position and starts the WireSense process, the welding wire touches the component and creates a short circuit without arc ignition. The short circuit is then cleared by raising the wire. The change in the position of the welding wire at the instant the short circuit is created is analyzed by the intelligent TPS/i power source using special evaluation algorithms and presented as a height measurement signal. The reversing wire movements take place in milliseconds. By evaluating the individual pieces of height information, the robot not only determines the edge misalignment and the position of the individual sheets in relation to each other, but also the actual edge height.
In the case of lap joints such as those used in SAG’s air pressure tanks, WireSense detects the weld seam path, reacts to any deviations and corrects the originally created welding program.
WireSense can be used equally with steel, stainless steel, aluminum, and other alloys. It is with aluminum—the SAG Group’s main material—that the Fronius assistance system truly comes into its own: the reflective surface of this material is frequently a major obstacle for optical measuring devices, but not for WireSense.
CMT technology is a basic requirement
WireSense can be used with any Fronius TPS/i welding system configured to use the cold metal transfer welding process. The precise wire movement resulting from the interaction between the wirefeeder on the wire drum, the wire buffer and the second Robacta Drive CMT wirefeeder which sits directly on the torch body, is crucially important. The metal surface is scanned and the weld contour detected in a reversing wire movement that takes place at around 100Hz. If you want to start using WireSense and already have a TPS/i welding system, it can be retrofitted at any time.
By using WireSense, the Salzburger Aluminium Group has optimized the welding of air pressure tanks, minimized rework and thus made manufacturing more cost effective.