Rapporto degli utenti: Carica più fredda, guida più a lungo
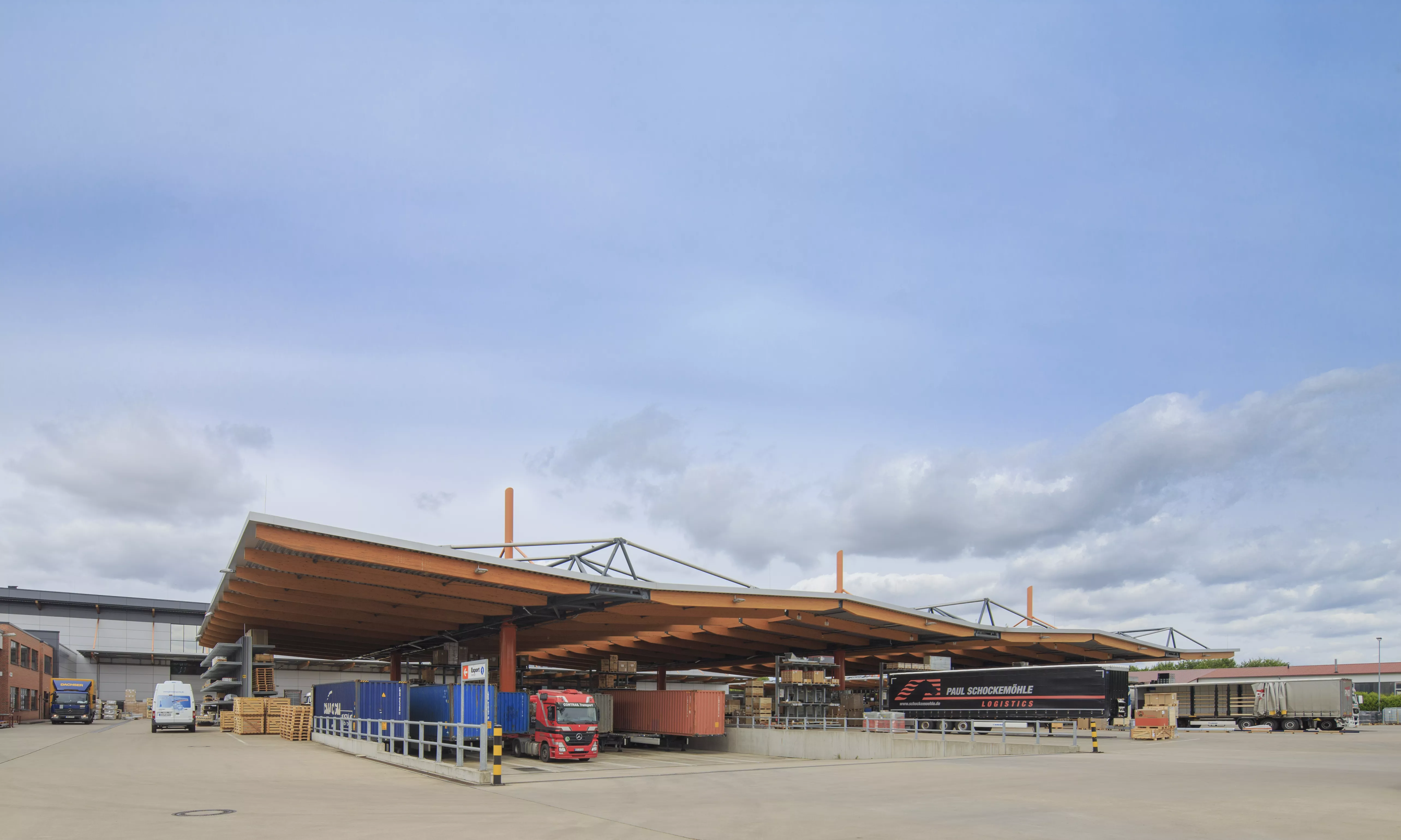
Il centro logistico di Big Dutchman è in piena attività questo lunedì mattina: grandi tapparelle automatiche si aprono e si chiudono quasi ogni secondo e carrelli elevatori di varie dimensioni, forme e colori sfrecciano tra i numerosi corridoi, generando un rumore di fondo che ricorda un alveare sovradimensionato. Nel frattempo, diversi mezzi pesanti aspettano fuori per essere caricati o svuotati. “Qui arrivano fino a 50 camion al giorno”, spiega Bernd Gürtler che, in qualità di Senior Manager dei servizi logistici, è responsabile del flusso regolare dei materiali nel magazzino. “Per gestire questo volume di merci in modo rapido ed efficiente, abbiamo bisogno di una tecnologia efficiente e affidabile”.
Big Dutchman AG è specializzata in sistemi di mangimi e allevamento per la moderna produzione di carne suina e pollame. Nel 1938, il fondatore dell'azienda inventò il primo sistema di alimentazione automatica al mondo a Holland, nel Michigan (USA). Da allora, il portafoglio dell'azienda familiare si è ampliato fino a comprendere sistemi semplici, sistemi di alimentazione computerizzati con controllo climatico, trattamento dell'aria di scarico e apparecchiature per il riciclaggio dei rifiuti, oltre a hardware e software per la gestione dell'allevamento e dell'ingrasso dei suini e della produzione di pollame e uova. Big Dutchman è presente in oltre 100 Paesi nei cinque continenti ed è leader mondiale del settore con un fatturato di 688 milioni di euro nel 2014.
Nuovo centro logistico per una domanda crescente
L'azienda ha sede a Vechta-Calveslage, nella Bassa Sassonia, dal 1985. Circa 800 dei 2.500 dipendenti globali sono impiegati qui, un quarto dei quali lavora nella logistica. “I nostri clienti vanno dagli agricoltori che ancora amano venire a trovarci con i loro trattori, alle grandi aziende con diversi milioni di animali”, spiega Gürtler. Per poter accogliere in modo rapido e flessibile una clientela in costante crescita, nel 2008 Big Dutchman ha deciso di costruire un nuovo centro logistico. “I locali precedenti erano troppo piccoli e non potevano più far fronte alla domanda”, ricorda Gürtler. Con la messa in funzione del nuovo edificio, l'azienda ha anche iniziato a convertire la propria flotta di carrelli elevatori da diesel a elettrici.
Oggi Big Dutchman utilizza 15 carrelli retrattili, 35 carrelli a caricamento frontale e nove carrelli a corsia stretta di diversi produttori nel nuovo centro logistico. Un pool di 88 batterie di trazione assicura che i carrelli elevatori siano sempre disponibili - l'azienda opera esclusivamente su tre turni. Tuttavia, inizialmente i dirigenti non erano soddisfatti della tecnologia di ricarica utilizzata per le unità di accumulo dell'energia. “I dispositivi fornitici dai vari produttori hanno dimostrato un basso livello di efficienza e un'elevata perdita di energia”, spiega il responsabile della logistica Gürtler. “Le batterie erano inoltre estremamente calde durante la carica. Questo ha avuto un effetto negativo sulla durata di vita e ha causato regolarmente dei difetti, a scapito delle nostre operazioni di magazzino”.Il motivo è apparso subito chiaro: con i processi di carica convenzionali, come la tecnologia dei trasformatori a 50 Hz, le batterie vengono caricate con una caratteristica fissa e una corrente predefinita. Ciò comporta una notevole perdita di potenza, poiché la batteria non è in grado di assorbire completamente questo elevato livello di corrente. Inoltre, alla fine del ciclo di carica si verifica un sovraccarico eccessivo, che riscalda e quindi danneggia la batteria. “Più alta è la temperatura, maggiore è il danno e più rapidamente si riduce la durata di vita”, riassume Gürtler.
L'innovativo processo di ricarica aumenta l'efficienza e la durata di vita
Durante la ricerca di una soluzione più adatta, i responsabili della logistica hanno scoperto lo stand di Fronius alla fiera LogiMAT 2013. Lo specialista austriaco in sistemi innovativi di ricarica delle batterie aveva appena presentato l'ultima generazione di sistemi di ricarica Selectiva per carrelli elevatori elettrici. Questi erano dotati di un'innovazione rivoluzionaria: il processo di ricarica Ri appositamente sviluppato, che riduce al minimo la perdita di energia durante la ricarica, riducendo così i costi energetici e le emissioni di CO2. Inoltre, la carica ultra fredda fornita da questo processo aumenta la durata delle batterie. “Una nuova tecnologia che non solo è più efficiente dal punto di vista energetico, ma offre anche una ricarica più delicata: questo ha attirato subito la mia attenzione”, ricorda Gürtler, che ha subito richiesto un dispositivo di prova a Fronius.
A metà 2013, Big Dutchman ha iniziato a condurre le prime prove con i sistemi di ricarica delle batterie Selectiva, che hanno dato risultati eccellenti: “Le nostre misurazioni hanno dimostrato che i dispositivi Fronius consentono una ricarica molto più fredda e consumano molta meno energia”, afferma Gürtler, chiaramente impressionato. Il segreto di questo miglioramento sta nel processo di ricarica Ri. A differenza delle tecnologie convenzionali, il processo di ricarica non segue una caratteristica standard. La corrente di carica è determinata dalla resistenza interna effettiva della batteria (Ri), che a sua volta dipende dall'età, dalla temperatura e dallo stato di carica della batteria. “Ogni ciclo di carica è quindi unico e ha una caratteristica individuale”, spiega Stefan Rasche, consulente tecnico per i sistemi di carica delle batterie di Fronius. “In questo modo è possibile ridurre al minimo la sovraccarica, che causa elevate perdite di energia e un dannoso riscaldamento della batteria”. Per l'operatore, questo sistema offre due vantaggi significativi: aumenta l'efficienza energetica durante la carica, riducendo così i costi energetici, e prolunga la durata della batteria. Poiché i dispositivi Selectiva offrono i migliori risultati anche nel confronto diretto con altri sistemi di carica delle batterie HF, Big Dutchman ha deciso di collaborare con Fronius.Semplice, flessibile e facile da usare
Nel febbraio 2014, l'azienda ha messo in funzione la prima stazione di ricarica con 21 dispositivi Selectiva 8120. Circa la metà delle 88 batterie di trazione in uso presso il centro logistico di Vechta viene caricata qui. Ogni dispositivo ha una potenza di otto kilowatt ed è adatto a batterie con tensione da 12 a 80 V. “Questo semplifica molto le cose per i nostri dipendenti e previene gli errori, in quanto non devono pensare a quale batteria collegare a quale sistema di ricarica”, spiega Gürtler, entusiasta della flessibilità di cui gode. Un'altra caratteristica del prodotto contribuisce a ridurre il carico di lavoro degli addetti al magazzino: una striscia LED ben visibile su ogni sistema di ricarica della batteria indica lo stato della batteria collegata. “L'arancione indica che la carica è in corso, il verde che la batteria è completamente carica e il blu che la batteria si è raffreddata ed è pronta all'uso”, spiega Stefan Rasche. Un display preciso e in tempo reale del sistema di carica della batteria mostra anche quale batteria è stata caricata completamente più a lungo. “Questo migliora l'utilizzo del parco batterie e, a sua volta, ha un effetto positivo sulla durata”, sottolinea Rasche.
I dirigenti di Big Dutchman sono estremamente soddisfatti dei sistemi di ricarica delle batterie Fronius. “Le prestazioni e la disponibilità di tutte le batterie, anche di quelle vecchie, sono nettamente migliorate”, riferisce Bernd Gürtler. “Anche i guasti e i tempi di fermo dovuti a batterie difettose sono diventati molto più rari”. In questa fase è ancora troppo presto per identificare gli effetti della conversione del sistema sui costi operativi complessivi. Tuttavia, Big Dutchman prevede una vita utile notevolmente più lunga per le batterie di trazione. “Con un costo medio di acquisto di circa 4.000 euro per batteria, questo rappresenta un enorme risparmio potenziale”, afferma Gürtler. Se la tecnologia Fronius continua a dimostrarsi così valida, è solo questione di tempo prima che vengano effettuati altri acquisti, riferisce il responsabile della logistica. “Il piano prevede di dotare di dispositivi Fronius un'altra stazione di ricarica qui a Vechta e il nostro centro logistico di Kuala Lumpur”. Da lì, Big Dutchman potrà fornire servizi ai suoi clienti nel sud-est asiatico, forse presto con l'aiuto dell'innovativa tecnologia di ricarica delle batterie austriaca.