Torch cleaning
Fully automated welding torch cleaning
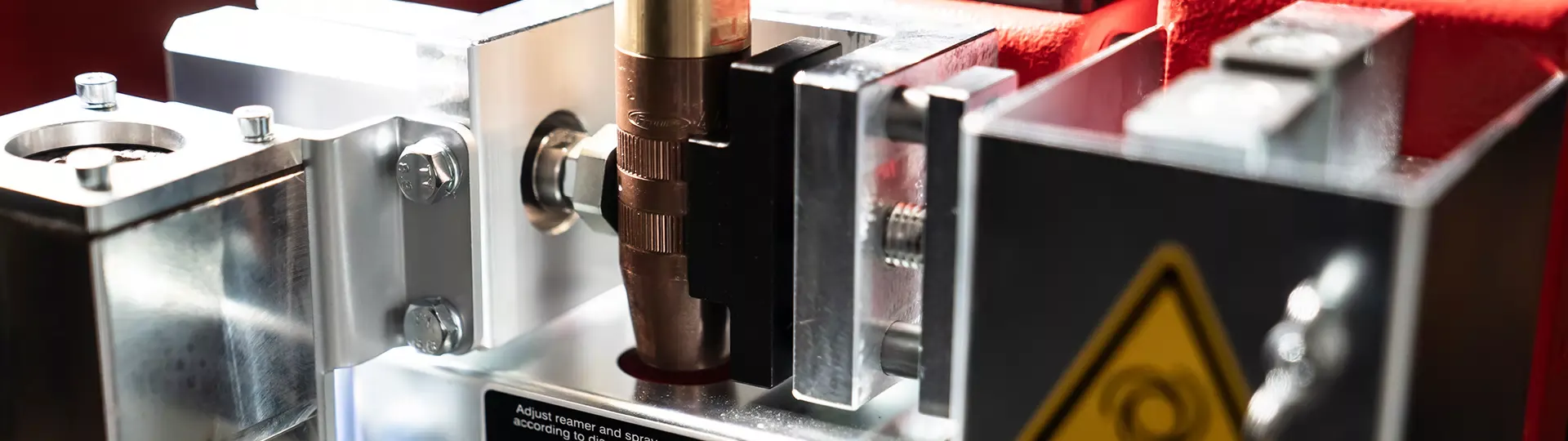
Cleaning and care for a longer service life
For today, tomorrow, and beyond: With the right cleaning, the service life of welding torch wear parts can be increased many times over. Depending on the welding material and application, we offer suitable cleaning systems to match the right welding torches and wear parts; for example, cleaning methods such as milling, brushing, or magnetic cleaning are available for steel or aluminum applications. Cleaning your welding torches ensures there is a proper gas shield and prevents unwanted contamination of the weld pool due to spatter, helping you deliver welds of flawless quality.
The advantages of our cleaning systems
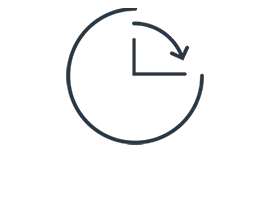
Longer service life for wear parts
Durable and sustainable: Using the right cleaning system for welding torches lets you remove debris efficiently, so you can extend the service life of wear parts.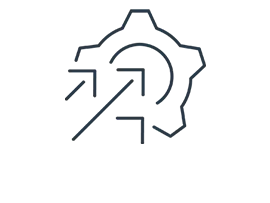
Increased system availability
An optimal, time-saving method of cleaning the gas nozzle significantly increases system availability by reducing downtimes and ensuring problem-free operation.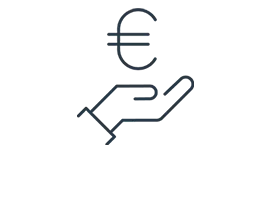
Saves costs
The extended service life of the entire system reduces the need for spare parts and maintenance work, thereby reducing costs.Cleaning for steel applications
There are two options for cleaning steel applications: mechanical cleaning using a milling cutter and magnetic cleaning.
Mechanical cleaning using milling cutter
The mechanical torch cleaner for steel applications is available in three versions: Robacta Reamer V Easy, Robacta Reamer V Comfort, and Robacta Reamer Single/Twin.
During milling cutter cleaning, the gas nozzle is cleaned of steel spatter on the end face and inside. To increase the service life, a parting agent can be used after milling to protect the gas nozzle from contamination. This supports the cleaning effect by reducing spatter adhesion during welding. As a result, the gas nozzle will be easier to clean in the future.
Robacta Reamer V Easy
- Mechanical cleaning using milling cutter
- Cleaning time of 3–5 seconds
- Milling cutter specifically targets wear parts when applying parting agent
- Saves time by cleaning and spraying in one position
- Dirt discharge into collection vessel
- Robot probe for checking the TCP
- Optional: electric wire cutter, various cleaning cutters, gas flow control
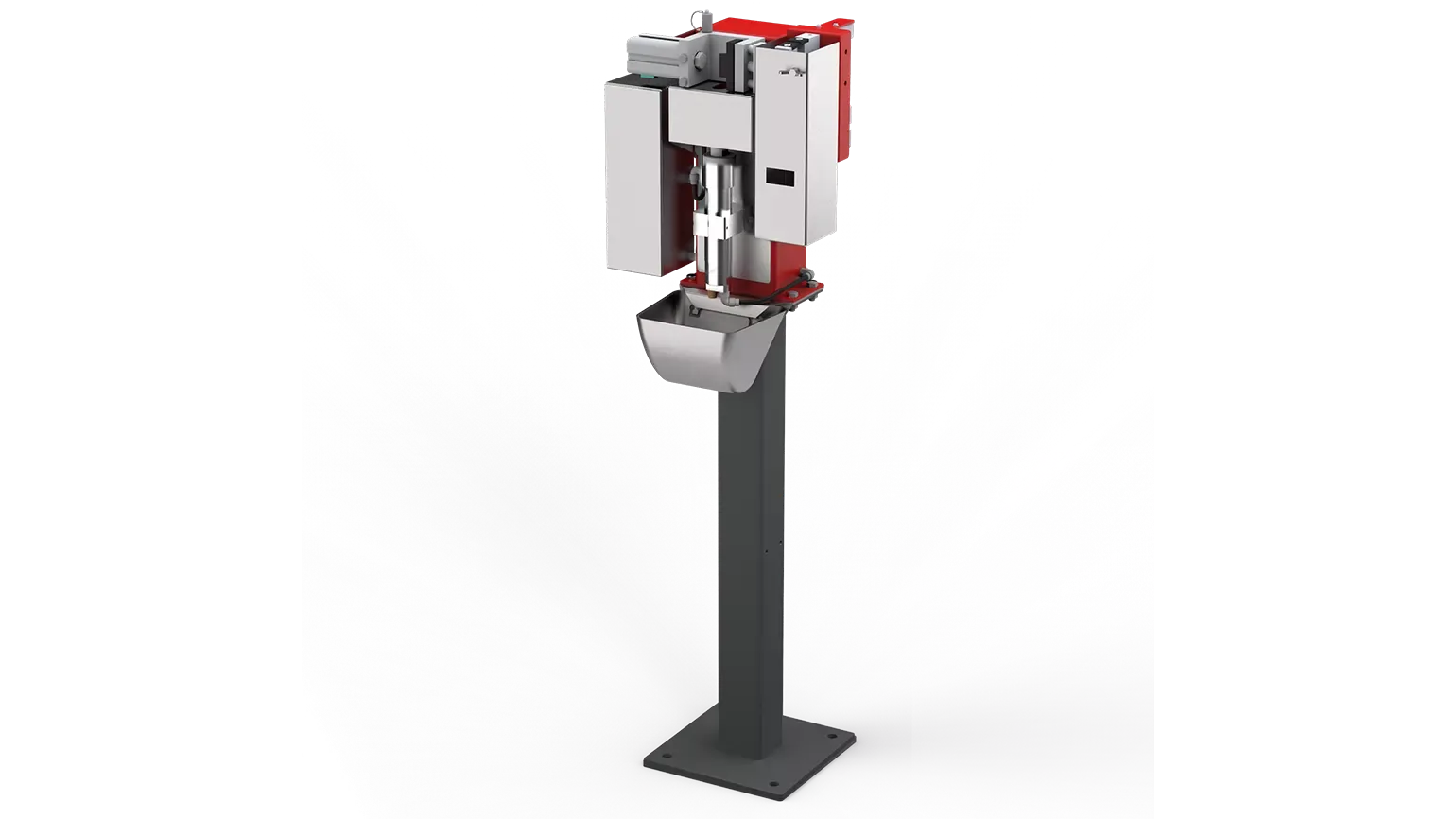
Robacta Reamer V Comfort
- Mechanical cleaning using milling cutter
- Cleaning time of 4.5–6 seconds
- Parting agent is specifically applied to wear parts via a separate, sealed unit that prevents contamination of the robot cell
- Level sensor for cleaning fluid
- Separate collecting container for parting agent residues reduces contamination in the robot cell
- Integrated TCP check: Detection of TCP displacement and contact tip wear via TCP Touch Sense
- Robot probe for checking the TCP
- Optional: electric wire cutter, various cleaning cutters, possibility of additional sensors (e.g., wire end sensor), gas flow control
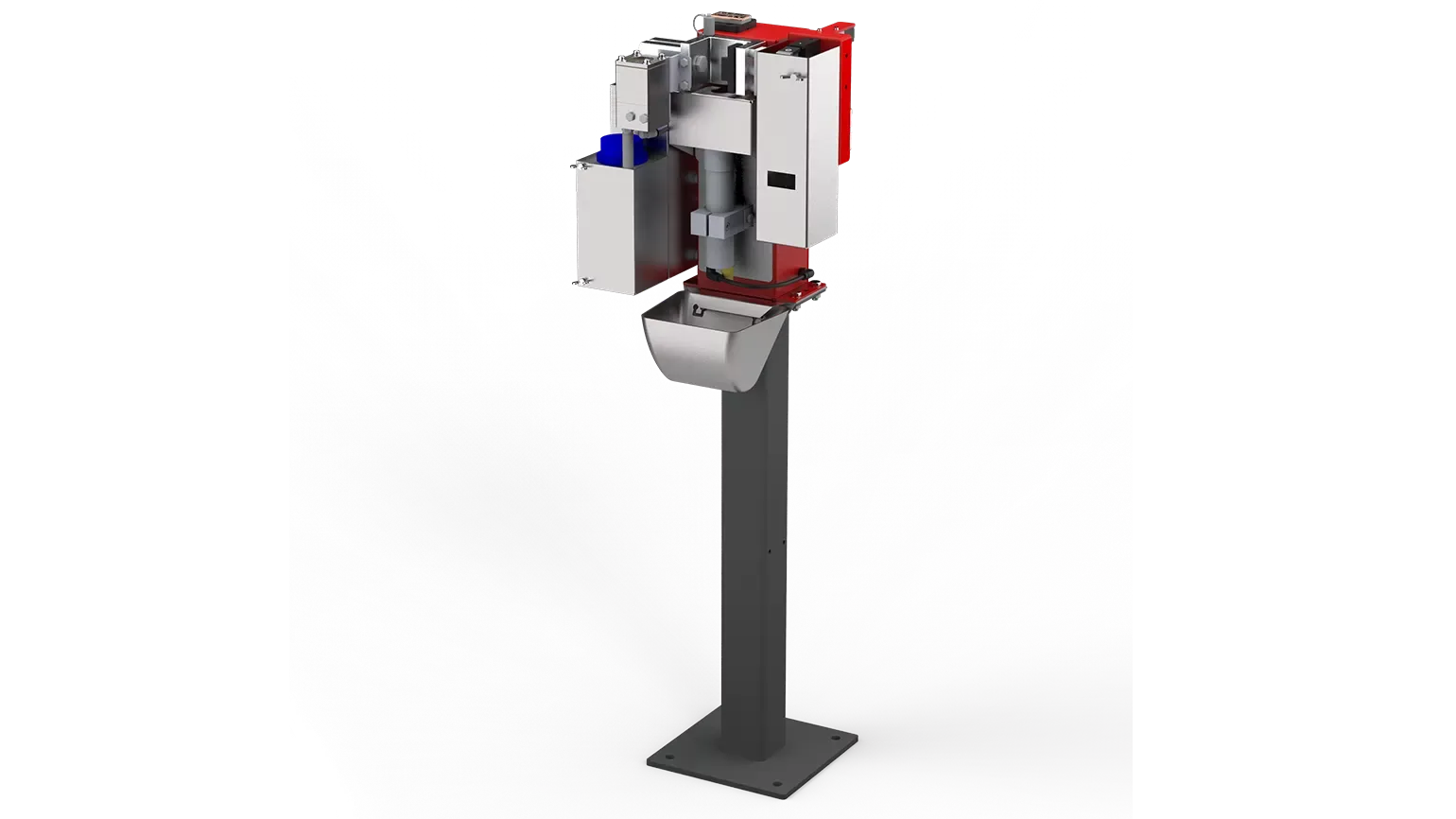
Robacta Reamer Single/Twin
- Mechanical cleaning using milling cutter
- Cleaning time of 4.5–6.5 seconds
- Clean single and twin welding torches with one device
- Suitable for torch bodies with 0°, 4°, 8°, and 11,5° contact tip angles
- Wire cutter integrated in the clamping system
- Robot probe for checking the TCP
- Optional: various cleaning cutters, gas flow control, TCP Touch Sense
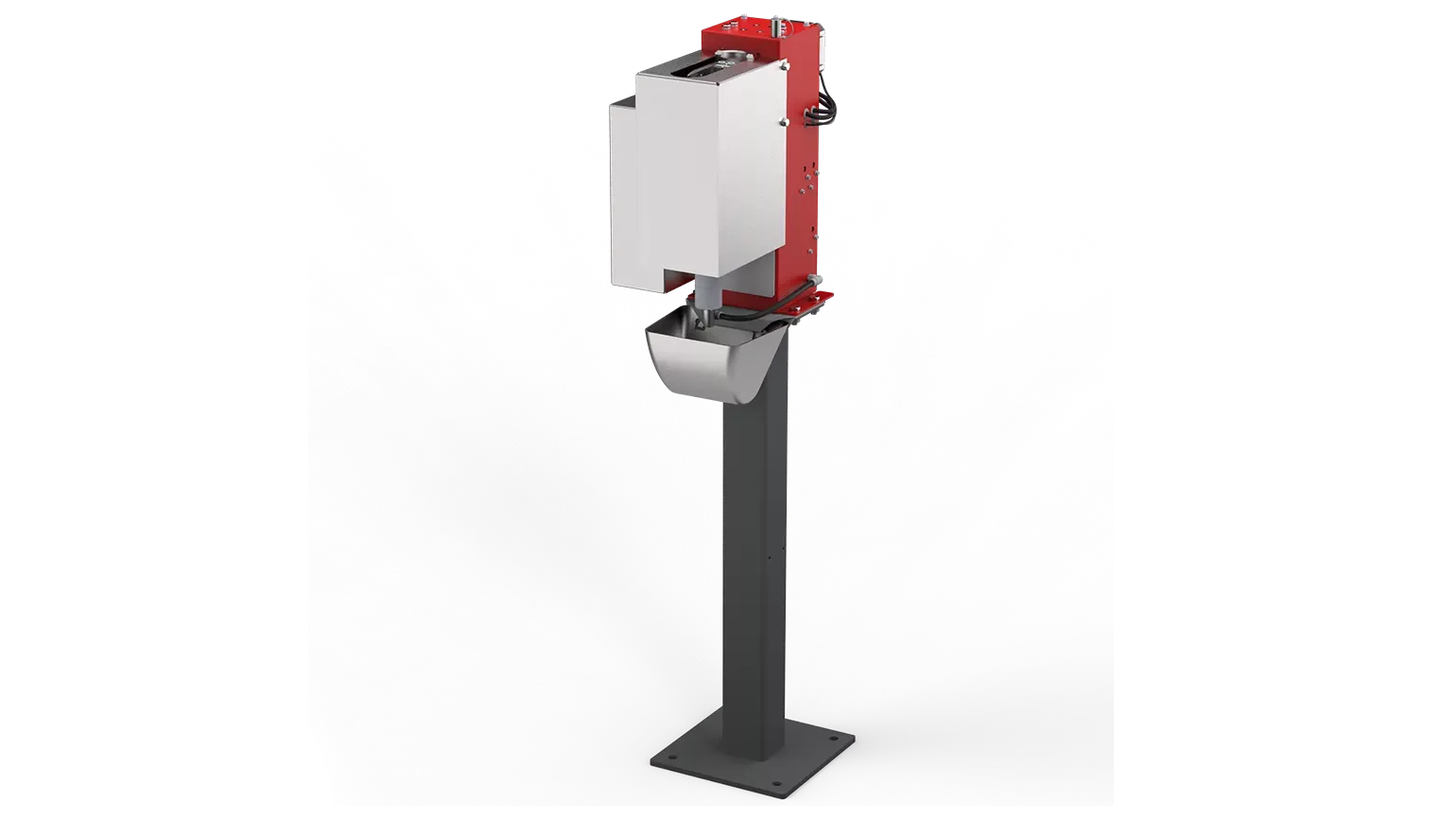
Magnetic cleaning for steel applications
No contact required: During magnetic cleaning, the welding torch is magnetically cleaned without contact. This method does not affect the TCP, ensuring that the welding wire is precisely positioned. Plus, wear part surfaces are not damaged, as any spatter that accumulates is removed electromagnetically.
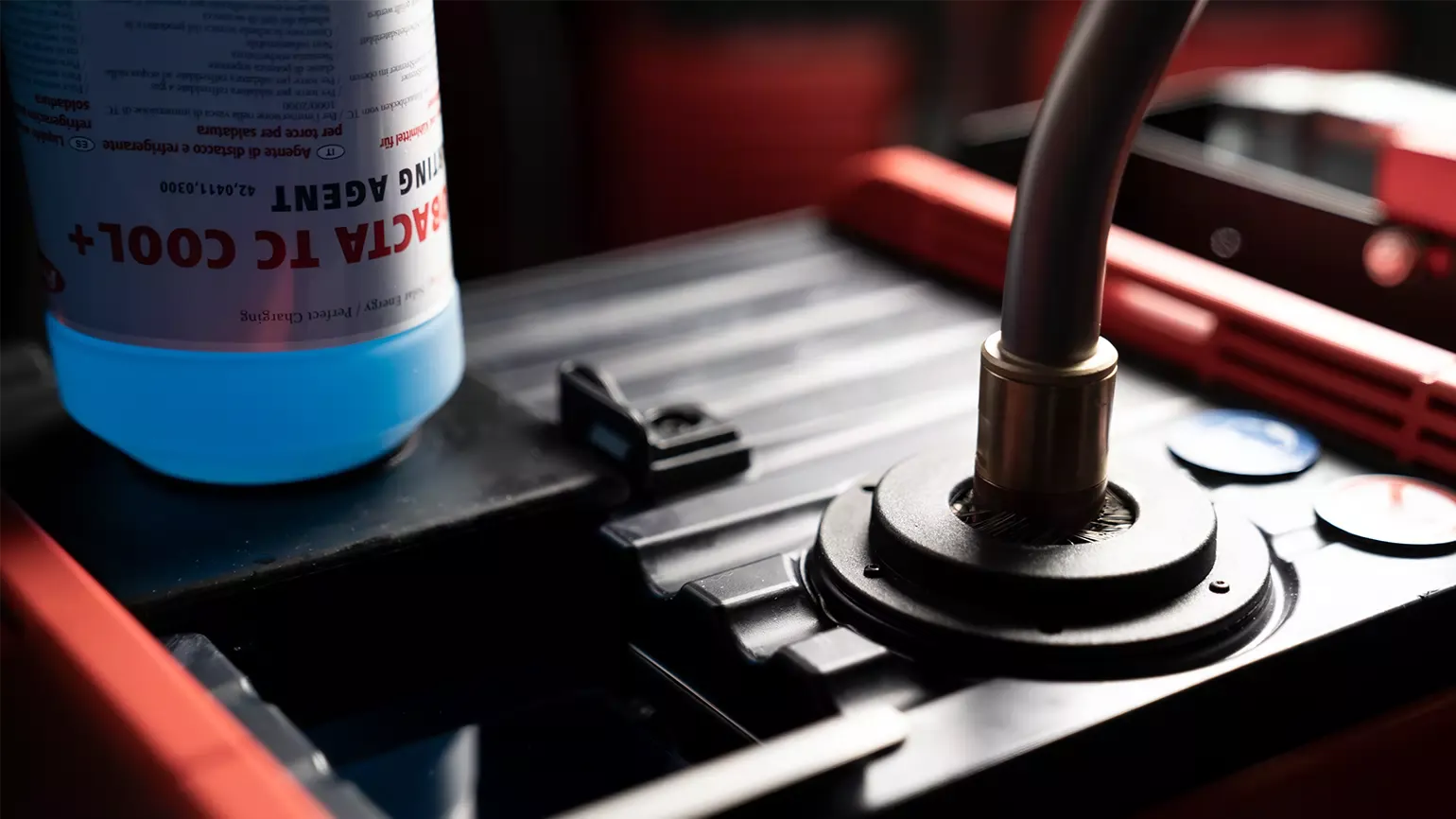
Robacta TC 2000 / TC 2000 Twin
- Contactless magnetic cleaning
- Cleaning time of 0.5 seconds
- TCP is not affected
- Service life of gas nozzle is ten times longer compared with mechanical cleaning, since wear part surfaces are not damaged
- Available for practically all torch geometries and gas nozzle shapes
- Parting agent vessel with level monitoring and automatic refilling
- Cleaning possible from 20 seconds charging time
- 50 seconds charging time until maximum magnetic flux density is available for the cleaning process
- Collecting container for welding residues
- Four different coils: 30 mm, 35 mm, Twin, LaserHybrid
- Optional: electric wire cutter
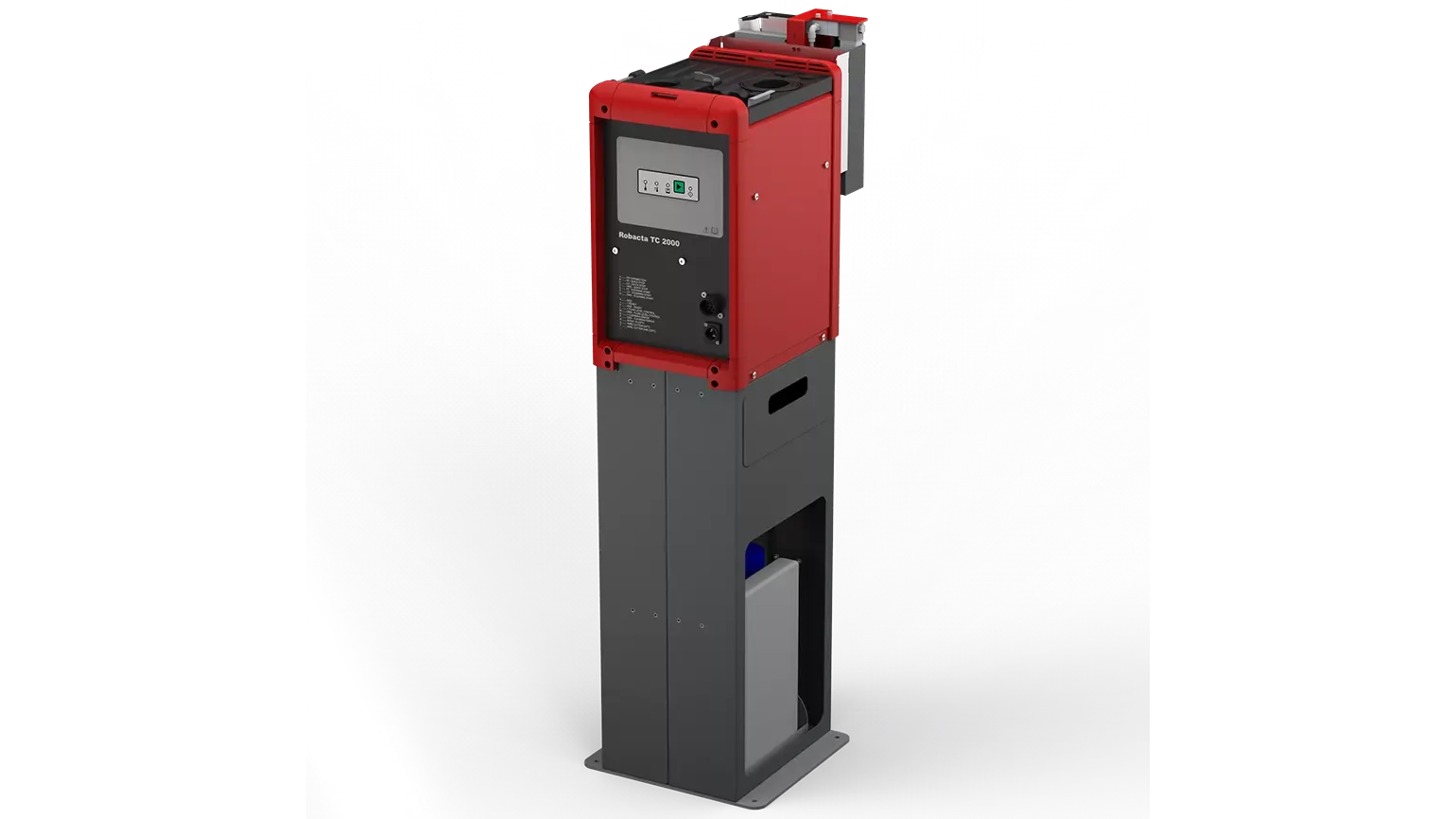
Robacta Reamer aluminum brush head
- Wear parts cleaned using a brush head on the inside and outside of the gas nozzle
- Cleaning time of 3–5 seconds
- Optimal access to gas nozzle and contact tip
- Quick, tool-free replacement of cleaning brushes
- Areas to be cleaned can be selected precisely according to the amount of soiling
- Robot probe for checking the TCP
- Optional: electric wire cutter, gas flow control