Navařování má partnera: Fronius Welding Automation
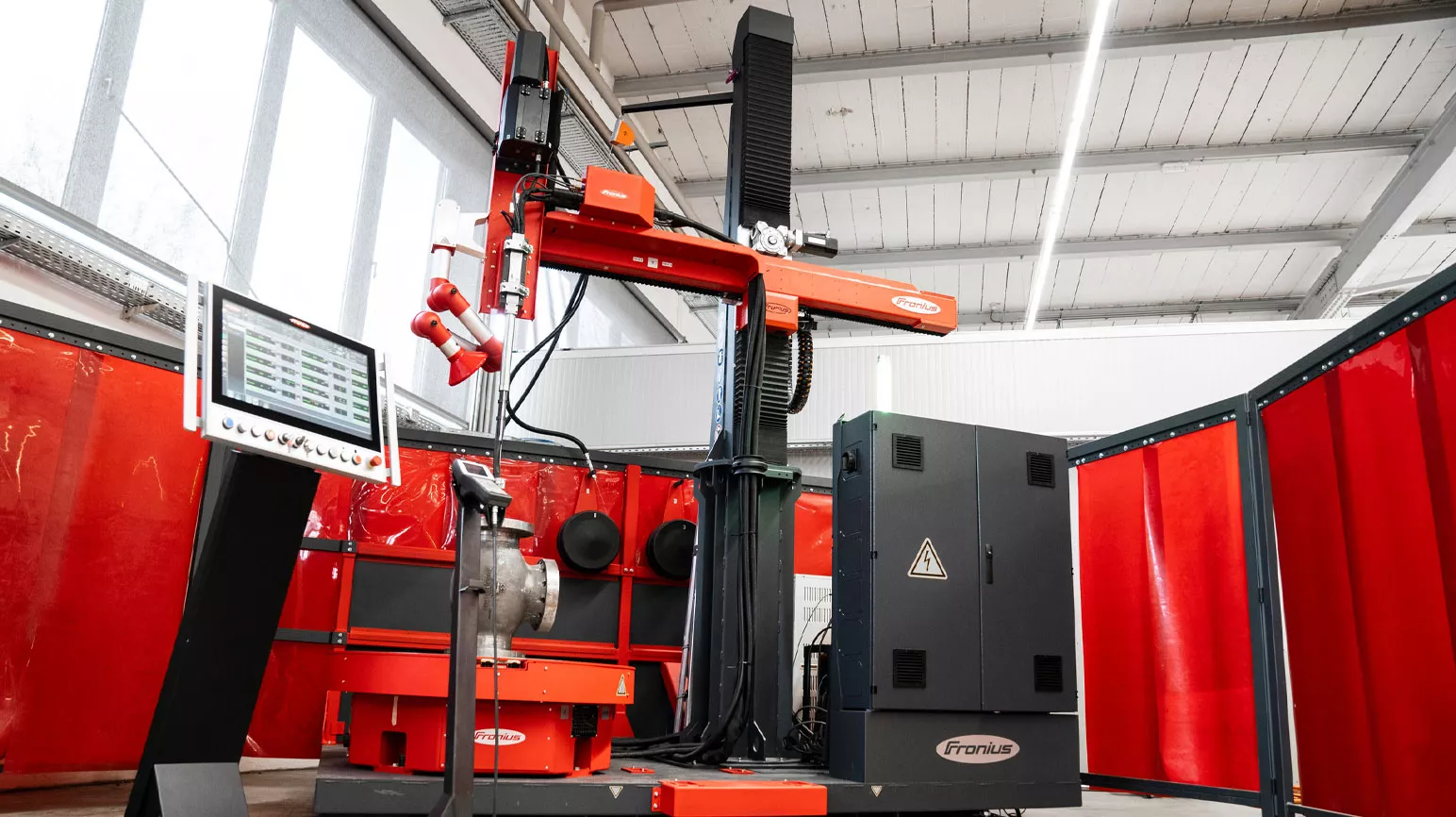
Po celou dobu životního cyklu výrobku zákazníkům po boku
Od plánování přes inženýring, výrobu a uvedení do provozu až po údržbu a servis navařovacích systémů: Díky celosvětové servisní a partnerské síti je Fronius Welding Automation spolehlivým partnerem pro své zákazníky. Důraz je vždy kladen na dokonalý výsledek navařování. Všechny systémy se z hlediska bezpečnosti zařízení vyrábějí v souladu s mezinárodními standardy shody. Technické uvedení do provozu odborníky společnosti Fronius a předběžné převzetí odběrateli z ropného a plynárenského průmyslu probíhá ve výrobním závodě v rakouském Steinhausu. Následně jsou systémy dodány, instalovány na místě – například v Saúdské Arábii, Anglii nebo USA – a poté definitivně převzaty mezinárodními zákazníky z onshore i offshore sektoru. Součástí komplexních služeb společnosti Fronius při uvedení do provozu jsou odborná školení a optimalizace procesů při zahájení výroby.
Realistické svařovací zkoušky a studie proveditelnosti
Fronius Welding Automation zahajuje nové projekty navařování studiemi proveditelnosti a svařovacími zkouškami. Navařování je velmi složité. Kromě základního materiálu potahovaných komponent hrají rozhodující roli také parametry jako velikost proudu, rychlost drátu, rychlost svařování, přídavný materiál, ochranný plyn, okolní teplota nebo vlhkost. I nepatrné odchylky mohou mít nežádoucí vliv na výsledek svařování. Zkoušky svařování by se proto měly provádět co nejrealističtěji – s díly, přídavnými materiály a ochrannými plyny, které se používají také v pozdějším reálném provozu. Pokud je to možné, za stejných klimatických podmínek, jaké později převládají v místě použití. Není-li to možné, musí se parametry svařování přizpůsobit a optimalizovat pro výrobní prostředí při uvedení do provozu. Aby nedošlo k žádným překvapením, je nejlepší nechat si poradit od odborníků společnosti Fronius.
Anton Leithenmair, ředitel Welding Automation: „Pro individuální přizpůsobení navařovacích zařízení potřebujeme od samého začátku otevřenou a důvěryhodnou výměnu informací. Existují specifikace přídavného materiálu a ochranného plynu? Jak je to s místními klimatickými podmínkami? Je obzvláště důležité, abychom mohli provádět naše svařovací zkoušky s originálními díly, a nemuseli se uchylovat k maketám. Jen tak mohou naše zařízení dosahovat požadovaných výsledků svařování i v náročném trvalém provozu.“
Kompletní řešení pro ropný a plynárenský průmysl
Zkušenosti jsou rezervoárem, ze kterého Fronius Welding Automation čerpá inovativní nápady pro nová systémová řešení. Společnost Fronius již více než 40 let vyvíjí navařovací systémy specifické pro konkrétní použití, které jsou buď standardizovány, nebo upraveny pro konkrétní požadavky zákazníků.
Compact Cladding Cell (CCC) – inteligentní a uživatelsky optimalizované řešení
S půdorysnou plochou 6 m² (64,5 ft²) je systém Compact Cladding Cell namontovaný na přepravitelné plošině „tím správným“ kompaktním řešením v oblasti navařování. Byl vyvinut pro nákladově efektivní vnitřní pokovování součástí ventilů. Maximální hloubka vrtání a největší možný průměr dílu je 1 m (0,39 in), nejvyšší hmotnost dílu je 2 500 kg (5.511,56 lb). Navzdory své kompaktnosti je zařízení extrémně výkonným navařovacím systémem. Přesvědčí snadným ovládáním, přesnými pohybovými sekvencemi a rozsáhlými možnostmi záznamu dat. Ergonomický design s uchycením cívky drátu v obslužné výšce, systém rychlé výměny svařovacích hořáků a svařovací přístroje na prodloužení kolejnice hovoří samy za sebe. Patří sem také inovativní softwarové funkce, maximální procesní bezpečnost a spolehlivost v nepřetržitém provozu. Automatická multisekvenční funkce umožňuje ukládání více svařovacích a pohybových parametrů ve formě sekvencí. Počínaje výchozí polohou se provádějí zcela automaticky jedna po druhé. Systémové řízení HMI s 21palcovým dotykovým displejem, vizualizací procesu v reálném čase, správou více uživatelů a mnoha dalšími funkcemi nabízí nadprůměrný komfort obsluhy. Pokud je požadována nejvyšší možná produktivita, stává se volitelně dostupný proces SpeedClad 2.0 nezbytností.
Systém ETR (Endless Torch Rotation) – téměř neomezené možnosti
Systém ETR byl vyvinut pro velké, složité díky a je zaveden už řadu let. Ústředním prvkem je nekonečně rotující svařovací hlava. Ta umožňuje svařovat díly s rozdílnými otvory a úhly otvorů až do vnitřního průměru 1 m (0,39 in). Svařovací hořák a podavač drátu rotují společně kolem osy otvoru. Díly se centrují plně automaticky. To výrazně zkracuje dobu přípravy a šetří výrobní náklady. Pokud existuje riziko kolize hořáku s dílem, elektropneumatická detekce kolize zastaví všechny osy pohybu a chrání svařovací hořák před poškozením. V poslední době společnost Fronius přidala ke svému úspěšnému systému ETR ještě flexibilnější systém ETR Ultimate. Toto univerzální zařízení umožňuje kromě navařovacích úloh také spojování větších dílů s náročnými geometriemi a obtížně svařitelnými svarovými spoji. Stejně jako u Compact Cladding Cell jsou systémy ETR i ETR Ultimate standardně vybavené pohodlným 21palcovým systémovým řízením s dotykovým displejem, vizualizací procesů v reálném čase a správou více uživatelů. Totéž platí pro systém rychlé výměny svařovacího hořáku, který šetří čas. V případě potřeby se svařovací hořák a polohovadlo pohybují synchronně v obou systémech – ETR i ETR-Ultimate. I zde zajišťuje SpeedClad 2.0 maximální produktivitu procesu navařování.
Přehled všech parametrů v reálném čase
Velká, intuitivně ovladatelná 21palcová dotyková obrazovka, víceuživatelské účty s individuální autorizací, vizualizace procesů v reálném čase, nastavení parametrů za chodu, inovativní funkce, jako je rentgenové zobrazení (X-Ray-View), editor komponent (Component-Editor), průměty těles (Bore-to-Bore-Advanced), monitorování aktuální hodnoty v reálném čase, import STEP souboru – to vše dělá z HMI-T21 systémové řízení Průmyslu 4.0. A samozřejmě možnost jejich vzdálené údržby. X-Ray-View zobrazuje komponenty transparentně a nabízí vynikající pohled na díl. Pokud je třeba potáhnout několik odsazených příčných otvorů s úhly jinými než 90° nebo příruby s otvory, pomůže funkce Bore-to-Bore-Advanced. Všechny relevantní parametry svařování se zobrazují živě v integrovaném systému monitorování aktuální hodnoty.
Ovládání, které plně uspokojí
V editoru komponent vytváří profesionální svářeč díly krok za krokem. Používá k tomu dotykovou obrazovku HMI-T21. Výška a průměr se definují zadáním. Jednotlivé komponenty se na obrazovce zobrazují v reálném čase jako 3D grafika. Kromě válcových tvarů jsou možné i ploché a kuželovité tvary. Lze také modelovat otvory a různá rozšíření – například příruby. Technologie CNC integrovaná ve společnosti Fronius umožňuje ještě více geometrií dílů než dosud: Na kuželových dílech jsou například možné prolínací otvory.
Svařovací procesy se programují v programovém editoru. Operátoři vybírají jednotlivé úseky dílů a určují pořadí svarů. Standardně je směr svařování stanovený zdola nahoru, ale v případě potřeby jej lze změnit. Užitečné je, že svařovací hořák lze zobrazit v bodě startu.
Všechny parametry svařování jsou definovány v editoru svařování (Weld-Editor). Systém nabízí výběr programových bloků s pevně stanovenými parametry, které lze kdykoli upravit, a to i za chodu v nabídce Weld-Adjust. AVR (Actual Value Recording) zaznamenává aktuální hodnoty svařovacího proudu, napětí, rychlosti drátu, množství plynu a svařovací polohy během svařovacích procesů v podobě tabulky. Pro grafické vyhodnocení a analýzy jsou volitelně k dispozici softwarové balíčky PC Data Logger HMI a Data Viewer HMI.
Jakmile je výchozí poloha svařovacího hořáku zkalibrovaná, hořák se při každé aplikaci navařování automaticky přesune do bodu startu. Siegfried Wiesinger, odborník na navařování ve společnosti Fronius, vysvětluje: „Bezprostředně před zapálením lze ještě prostřednictvím dálkového ovladače doladit různé parametry – například pomocí funkce AVC (Arc-Voltage-Control) bod startu a vzdálenost hořáku od dílu.“
SpeedClad 2.0 – oceněný a velmi rychlý
Rychlejší, efektivnější, úspornější: Se systémem SpeedClad 2.0 nastavuje společnost Fronius nové standardy při navařování součástí ventilů. Ve srovnání s pulzními procesy TIG s horkým drátem, které se používají v celém odvětví, je SpeedClad 2.0 výrazně úspornější. Inovace zaujme vysokým odtavným výkonem, ohromující rychlostí a nízkou spotřebou ochranného plynu. Vzhledem k vynikajícím výsledkům byl proces oceněn cenou Excellence in Welding Award od American Welding Society. Slavnostní předání cen se konalo 13. září 2023 na veletrhu FABTECH v Chicagu. Porotu přesvědčily následující skutečnosti: Odtavný výkon slitiny na bázi niklu používané při navařování se zvýšil z 1,63 kg (3,59 lb) až na 6 kg (13,23 lb) / h, přičemž společnost Fronius nyní používá 1,6mm drát (0,063 in) namísto 1,14mm drátu (0,045 in). Rychlost svařovací vzrostla z 33 cm (13 in) / min na 135 cm (53 in) / min a průměrný pulzní proud se zvýšil z 240 ampérů na 460 ampérů. To zaručuje všem zákazníkům společnosti Fronius ideální vnos tepla při současném snížení spotřeby argonu z 516 l /kg až na 140 l/kg. Díky zcela nově vyvinutému systému hořáků lze plátovat výrazně užší otvory dílů: 100 mm (3,94 in) namísto 150 mm (5,91 in). Výchozím bodem pro optimalizaci procesu navařování byl vzorec pro vnos tepla: vnos tepla = volty x ampéry x 60 / rychlost svařování.
Fronius Welding Automation má v genech udržitelnost, a proto je mnoho jejích inovací spojeno nejen s technickými vylepšeními, ale také s nižší spotřebou spotřebního materiálu – včetně procesu SpeedClad 2.0.
V portfoliu jsou také systémy pro podélné a obvodové svary a robotizované svařování
Jako dodavatel řešení vyrábí společnost Fronius Welding Automation nejen zařízení pro navařování, ale také mechanizované a robotizované svařovací systémy pro všechna průmyslová odvětví.
Příklady zahrnují systémy pro svařování podélných a obvodových svarů, svařovací traktory a robotická zařízení Handling-to-Welding. Kolaborativní systémy, inteligentní senzory, softwarová řešení pro správu dat a offline programování včetně simulace svařování otevírají ekonomické možnosti pro kovozpracující společnosti již od velikosti dávky jednoho kusu. Ve spolupráci se zákazníkem jsou analyzovány příslušné požadavky na svařovací techniku. Následuje koncepce individuálního řešení.
Za tímto účelem je k dispozici modulární systém standardizovaných komponent. Prodej svařovacích systémů řešíme jako projekt, počínaje studií proveditelnosti přes plánování, inženýring a výrobu až po uvedení do provozu. Od roku 1975 se používá více než 3 500 instalovaných systémů u více než 2 000 zákazníků ve 45 různých zemích. Na provozní ploše více než 11 000 metrů čtverečních se přibližně 150 odborníků společnosti Fronius stará o svařovací výzvy zákazníků.
Více informací o společnosti Fronius Welding Automation naleznete zde: https://www.fronius.com/cs-cz/czech-republic/perfect-welding/svet-svarovani/automatizace.