What is
MIG/MAG Welding?
MIG/MAG welding: The high-speed welding process
MIG/MAG welding is also referred to as gas metal arc welding. A differentiation is made between metal inert gas welding (MIG) and metal active gas welding (MAG). MIG/MAG is currently the most frequently used welding process and allows for particularly high welding speeds. It can be used in a manual, mechanized or robot-supported manner.
MIG/MAG welding: This is how it works
In MIG/MAG welding, a filler metal or welding wire ignites the arc if it touches the component. The consumable wire is used as allowance.
In order to protect the arc from the reactive oxygen in the surroundings, a “shielding gas” also flows through the gas nozzle. This suppresses the oxygen during welding and therefore prevents oxidation on the arc and on the weld pool.
Which gases are used in MIG/MAG welding?
MAG welding uses active gases such as pure CO2 or mixed gases (argon, CO2, O2) in various compositions. These are highly reactive. The MAG process is used for unalloyed, low-alloy and high-alloy materials.
MIG welding, on the other hand, uses inert, i.e. unreactive, gases such as pure argon and helium or mixtures of argon and helium. The process is suitable for welding materials such as aluminum, copper, magnesium and titanium.
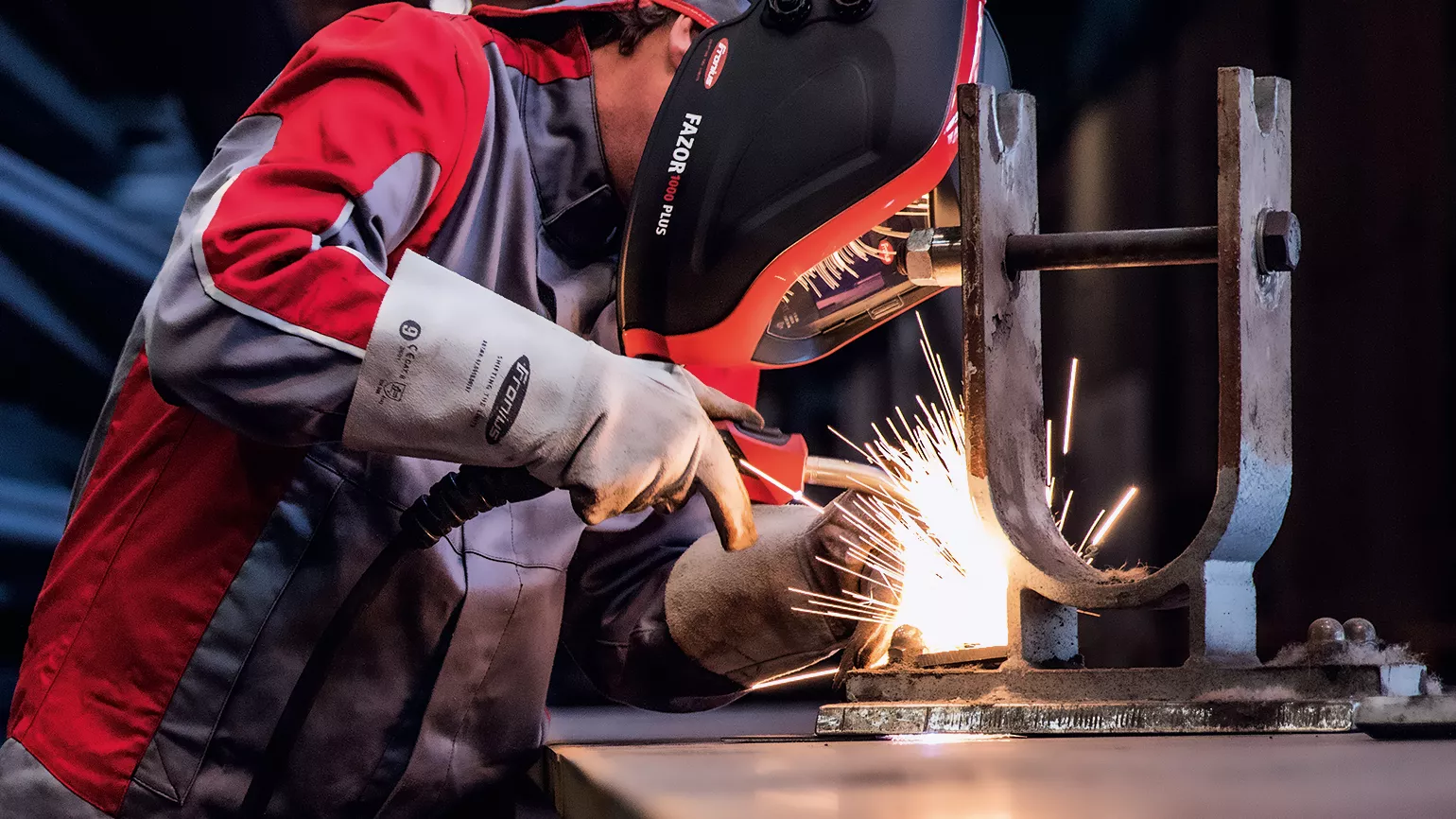
This is how a MIG/MAG welding system is structured:
(1) Mains connection
(2) Power source
(3) Hosepack
(4) Grounding cable
(5) Welding torch
(6) Ground terminal
(7) Workpiece
(8) Filler metal
(9) Shielding gas
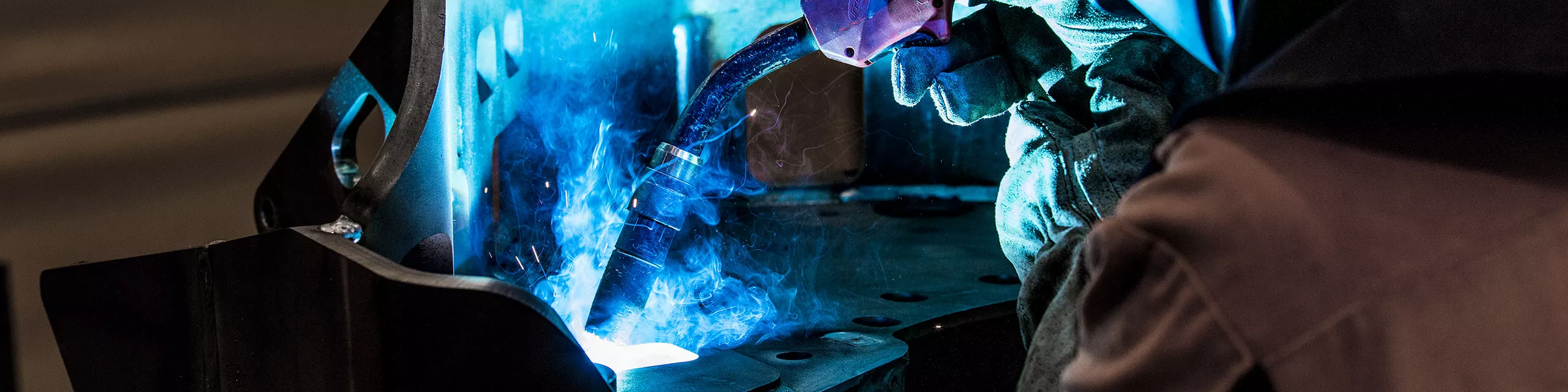
Arc types in MIG/MAG welding
There are various arc types in MIG/MAG welding. They differ in terms of the level of the amperage. In the low power range the arc is susceptible to short circuits; in the higher power range it is free of short circuits.
Dip transfer arc
The arc is ignited by brief contact between the wire electrode and the component. This produces a quickly increasing short circuit current, which liquefies the wire electrode and a droplet detaches. After the short circuit, the arc reignites. The dip transfer arc is used in the lower power range for thinner sheets and allows for welding to be carried out in almost any position. The dip transfer arc is also predominantly used in the root pass.
Intermediate arc
The intermediate arc changes between short circuits and spray transitions at irregular intervals. This results in more spatter. An effective use of this arc is not possible, and therefore it is best to avoid it.
Spray arc
This arc burns constantly without short circuits in the upper power range and is well suited to the welding of thicker sheets. This means that a high deposition rate and deep penetration are possible.
Pulsed arc
The pulsed arc is made up of a base current phase with a low power and a pulsing current phase with high power without short circuits. This means that almost no spatter is produced. In the pulsing current phase, the welding droplets are detached in a targeted manner via a precisely dosed current pulse.
Rotating arc
This arc is even more powerful than the spray arc and is used for thick sheets where a high deposition rate is required. The welding droplet is transferred into the weld pool in a rotating movement. The rotating arc is also referred to as a high performance arc.
Combined arc
This arc consists of a dip transfer arc and a pulsed arc. The necessary penetration and the heat input are generated in the phase of the pulsed arc, while the phase of the dip transfer arc provides for the cooling of the weld pool and makes it easier to manage.
Fronius process variants of MIG/MAG welding
Which materials are suitable for MIG/MAG welding?
The material that is most frequently used in the gas metal arc welding is steel. In addition, aluminum and stainless steel alloys can also be welded well with MIG/MAG.
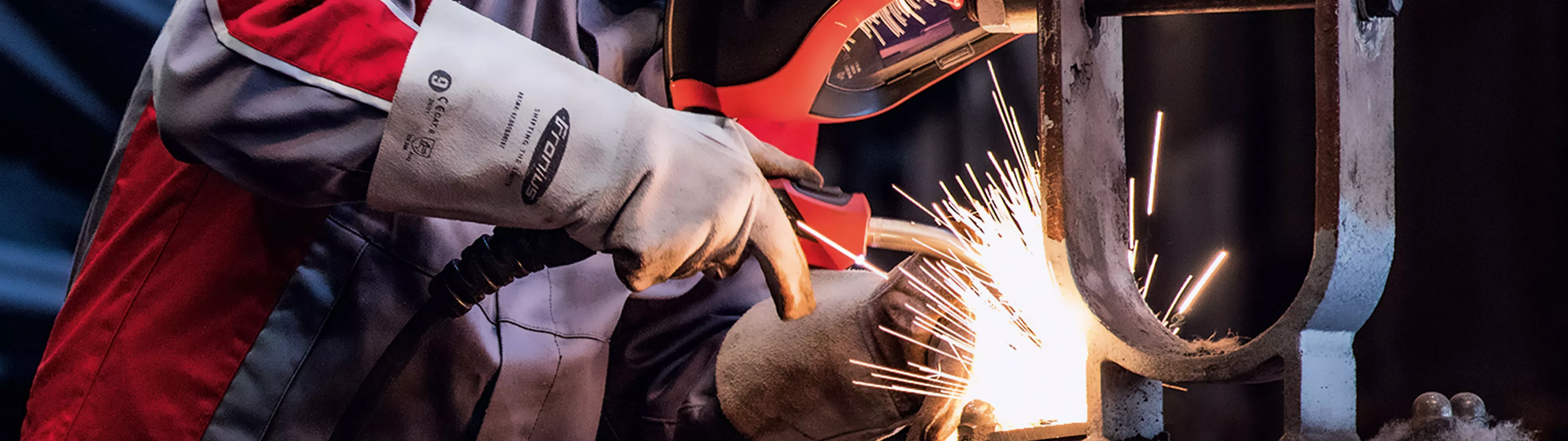