Excellence Through Execution the Enerfab Way
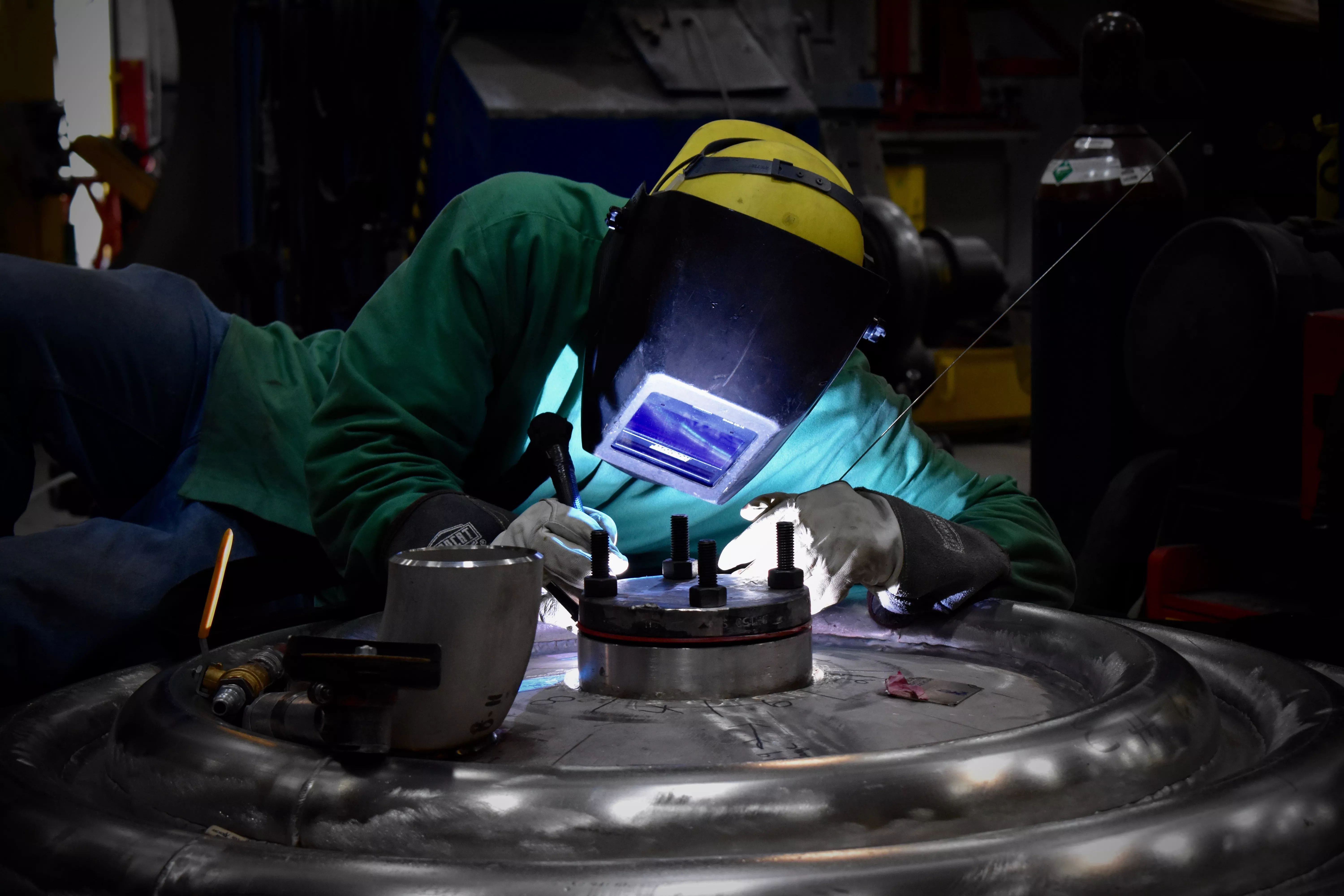
Since 1901 Enerfab has been pushing the boundaries of fabrication excellence and customer service. Through innovative technology and proprietary processes they lead the market in specialized vessels, tanks, kettles, and more for a variety of industries. In their 115+ years of experience they’ve learned to recognize other thought leaders and when Fronius opened their U.S. headquarters in 2002, Enerfab was one of the first to embrace the newest welding technology. The precision arc and consistency of weld quality first drew Enerfab to Fronius equipment, and in the years since, the longevity, safety, and performance of this technology have been vital to their operations.
High-pressure vessels and specialty alloys need exacting standards for weld quality and a close attention to safety. Enerfab’s commitment to safety has earned 63 zero-injury safety awards as of 2017. This dedication is found at every level from the fabrication floor to the conference rooms where all internal meetings begin with a safety moment. Keeping safe processes as a baseline company-wide lets them focus on their customer’s needs during fabrication.
Enerfab develops a partnership with the client that begins with the concept of each new project. With industries including refining, chemical, petrochemical, and food storage, this requires a certain level of detailed listening to meet their diverse customer needs. Enerfab’s goal is to understand those needs and become part of the team from concept to execution. Through surveys they ask whether they’ve met this goal and the most frequent response is something Enerfab can be proud of. Frequently customers say Enerfab knows their projects at least as well — if not better than — the customer themselves in terms of specifications and quality standards.
This level of understanding is one reason Enerfab can offer their rapid response service which helps customers recover from a shut-down level event that can cost hundreds of thousands of dollars a day and in some cases much more. The fast turnaround fabrication is done at the Enerfab headquarters in Cincinnati where all of their departments are on hand to troubleshoot issues and resolve them quickly. An example of a rapid response project was the fabrication of a six-foot diameter by sixty-foot-long stainless-steel vessel complete with insulation, ladders and platforms, that took less than twenty days to produce. They attribute some of their rapid response success to the Fronius TPS technology that allows them to customize and store weld waveforms. Since they’ve already done the hard work of finding what works with their designs and alloys, this technology allows them to call up those parameters as needed. When asked how they can handle regular production as well as emergency fabrication, James Ferguson, Chief Marketing Officer at Enerfab, said “It’s the quality of our people and our processes that allow us to meet our production deadlines and still rapidly respond to customer emergencies without sacrificing quality or safety.”
The welding engineers at Enerfab worked closely with the Fronius team to develop customized waveforms for some of the specific nickel-based alloys they use. Ben Sprengard, Director of Quality Assurance at Enerfab is a degreed welding engineer with a masters degree in metallurgy. He spoke in depth about the specific alloys they work with daily and why they continue to use Fronius equipment. “This equipment is completely customizable,” he said, when discussing the waveforms. Since Enerfab uses all the standard weld processes–FCAW, GTAW, SMAW, and GMAW– the ability to use one machine for everything works well for them. They work with both cladded and solid metals ranging in thicknesses from 3/16”-7”. Most of their welding is mechanized (or automated) GMAW-P with an engineer monitoring the process at the weld site.
When asked what their biggest welding challenge was, the response was both surprising and familiar: a lack of skilled welding personnel. Everyone in the fabrication industries has felt the pinch as older craftsmen and women retire without young people to fill the holes. Enerfab is using technology such as tablet interfaces to lure the younger generations. They plan to incorporate more digital monitoring for common issues like heat-input, and the touch-screen interface of the TPSi line from Fronius. Though their original TPS machines are still performing well, switching to TPSi will give them access to newer, advanced processes. These changes will help them watch how each weld performs and entice new younger welders while supporting the experience and skill of their seasoned experts.
In the past five years alone Enerfab has worked millions of labor hours. Their tank and vessel fabrication shops are capable of handling up to 800,000 pounds of vessels or equipment and they hold several ASME Stamp of Quality. With their years of challenges and successes behind them Enerfab continues to lead their industry with a focus on safety, quality, and customer satisfaction. To learn more about Enerfab, visit enerfab.com. To learn more about Fronius welding technology, visit www.fronius.us
Written by Rhonda Zatezalo, freelance writer for the fabrication industry www.rhondazatezalo.com