Personal Touch
Better MIG welding outcomes are the result of knowing the particulars about your craft.
-As published by Welding Productivity Magazine
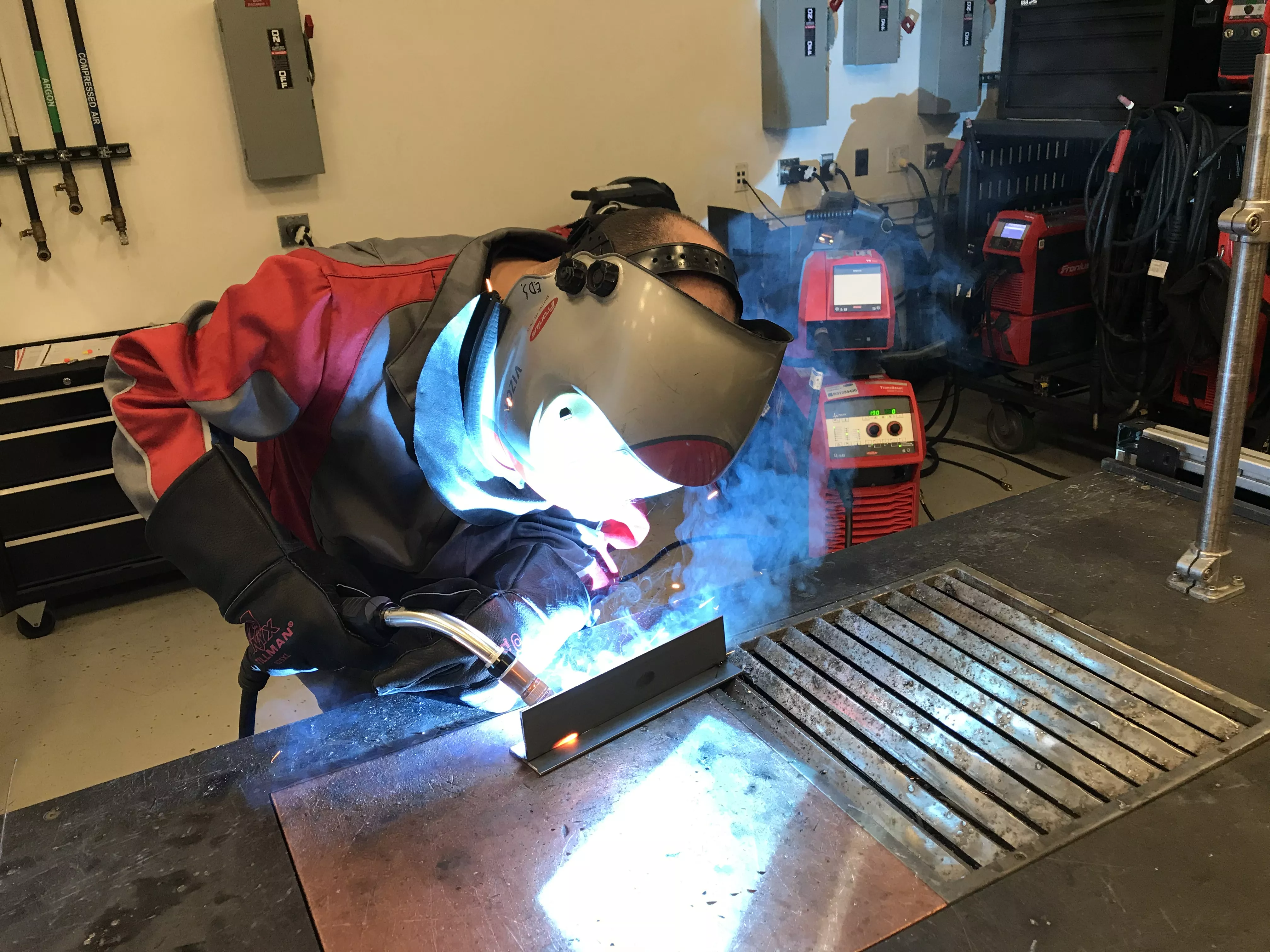
MIG welding is a skill. And just like anything else, you bring along your own style, strengths and limitations when you pick up a welding torch. There are specifics like melting points that can’t be ignored, but the parameters, methods and equipment a welder uses can be quite personal. With so many options available, MIG welding is much more than the “hot glue gun” of welding.
Parameters will differ from welder to welder because you weld at different travel speeds and manipulate the weld pool differently. Whether you’re new to MIG welding or have years behind the torch, understanding the basics can help show you how to personalize the experience and really make your welds shine.
One of the first steps in any welding process is to know your equipment, including the power source. Whether the faceplate is a few dials or a touch screen, know where to adjust the wire feed speed, voltage and inductance/pulse correction. If the equipment allows, know how to change the transfer mode and synergic line. Often the job demands quick results, and knowing how to make adjustments on the fly helps boost confidence and productivity.
Modes of transfer
Gas metal arc welding (GMAW) – also known as MIG welding – encompasses four transfer modes: standard short circuit arc, globular, spray arc and pulse. Knowing how each mode works and when to use them is a key part of welding.
Short circuit arc welding uses low voltage and current, works well with thinner material and is the coldest of the four modes. When the welding wire contacts the base material, it creates a short circuit that deposits the weld material into the weld pool. Short circuit is one of the most common forms of MIG welding and can be used to weld in all positions.
Globular transfer welding is similar to short circuit, but rarely used. With this method the droplet size is much larger than the weld electrode, creating a globule of filler metal that is gravity fed into the weld pool. As such, it’s only usable in the flat or horizontal positions. This mode is the most unstable of the four based on the high heat required and the high spatter ejection that occurs from uncontrolled droplet size.
Spray arc welding works just as it sounds – it sprays molten metal into the weld joint when the filler metal passes through the arc at a higher current and voltage. This allows for only horizontal or flat positions and works best on slightly thicker materials. The high heat necessary for spray arc welding can lead to burn through on thin materials.
Pulse welding is a modified spray arc that uses the best attributes of the other modes. Not all equipment can weld in pulse mode, so know your power source. This mode gets its name from how the current is pulsed to form a single drop of molten material that is then transferred across the arc to the weld pool. The precision of the pulse and arc allows for out-of-position welding and faster travel speeds. Pulsing the current allows for a lower heat input, creating a smaller heat-affected zone, which helps with temperature-sensitive applications.
Speed, voltage and gas
The speed at which the wire is pushed through the torch is called the wire feed speed. On some machines, setting the wire speed is the same as setting the current. On others, it can be done separately. Tuning in the correct speed and voltage can ensure proper penetration and eliminate undercutting. If there isn’t enough material in the joint, increase the wire speed. If the weld pool isn’t fluid enough or it’s too cold, increase the voltage. If you’re experiencing undercutting, decrease the voltage. Understanding how wire speed and voltage work with the way you weld is key to welding your best.
A note about stick-out: Normal stick-out (the amount of wire showing outside the tip) is 15 mm or 5/8 in. If there is enough filler metal but the weld is still too hot, lengthen the stick-out. This decreases the average current, which cools the weld pool.
Entire articles can be written about the proper gas mixtures for each transfer mode and material. It’s a detailed subject, which is why it’s so important. Following base metal and application guidelines often dictates the gas mixture, but there are some easy guidelines to remember. Choosing the right gas mixture and flow rate should be based on the welding transfer mode as well as the material type.
A 100 percent CO2 gas can be used for short circuit and globular transfer welding. However, welding steel with short circuit benefits from an argon-rich mixture of 75 percent to 95 percent. Using a rich argon mix helps to stabilize droplet size and reduce spatter levels.
To weld that same steel using spray arc welding, adjust the CO2/argon mixture to a minimum of 80 percent argon. Balancing the gas mixture and flow rate is critical to achieving a proper spray arc weld.
Torch handling
There are two types of angles when talking about torch handling. One is the angle of the torch to the workpiece, known as the work angle. The other is the travel angle, or how the torch is angled compared to the direction of travel. The travel angle uses either a push or drag motion. Pushing is when the torch points in the direction of travel; dragging is when it points away. Both angles are determined by the type of weld joint, positioning, material thickness and welding process.
Typically, MIG welding uses a push or leading arc, but the degree of push angle depends on the factors mentioned above. For example, when welding 5000 series aluminum, a more forward-leaning angle is necessary for a cleaner weld surface due to the coatings on the metal.
The skill you bring to the torch can be improved by knowing your equipment and your style of welding. Are you quick? Have a steady hand? Whatever the case may be, use that knowledge to personalize your parameters and increase your proficiency.
By Erik Stengline, Welding Application Manager @ Fronius USA LLC, and Rhonda Zatezalo, writer @Crearies Marketing Design.