Speed boosts with quality upgrades
Anderson Dahlen gains a 3x speed boost and higher quality welds with the Fronius TPS/i.
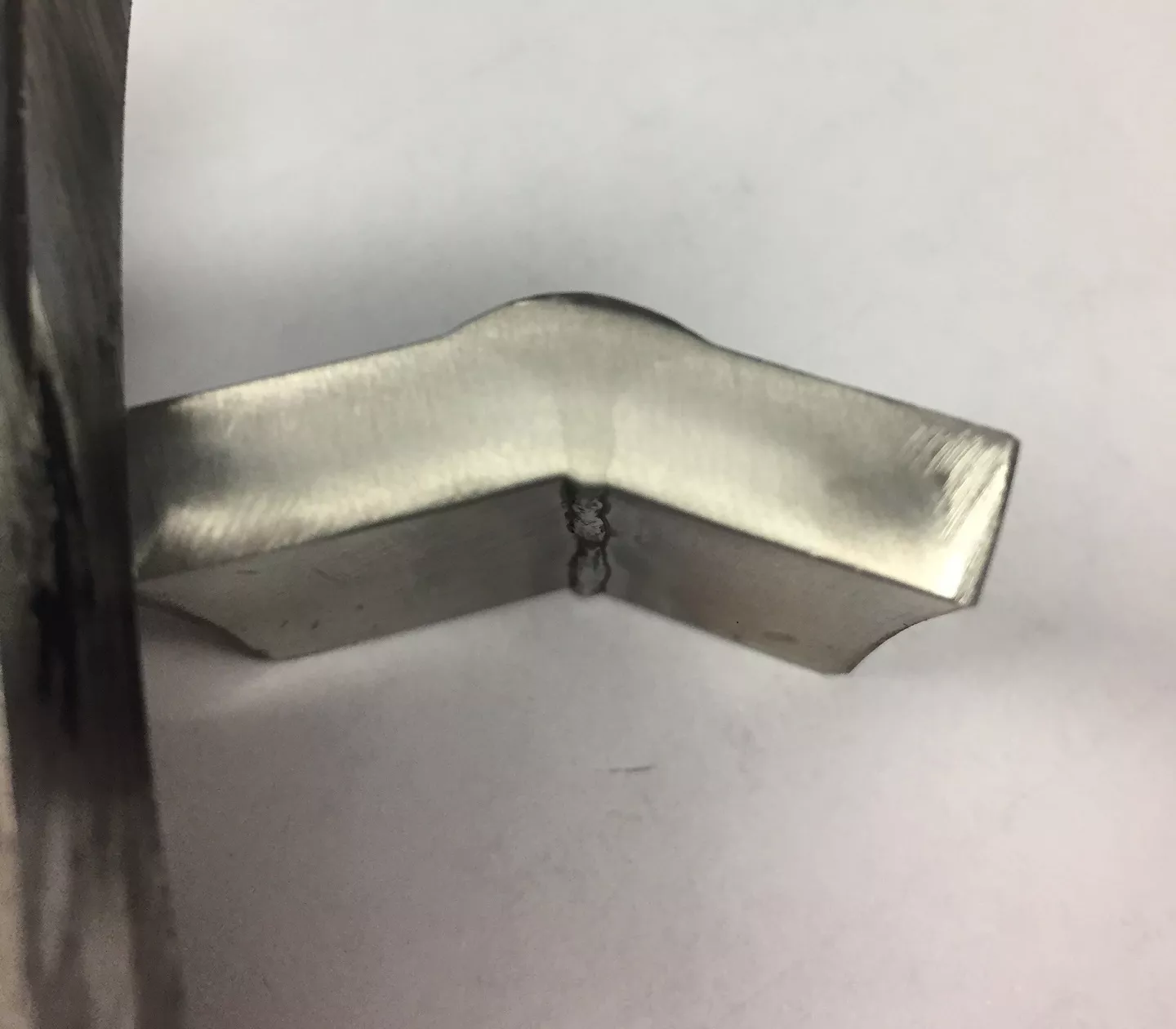
Attending a large industry trade show, you expect the exhibitors to assure you that their product can solve your challenge. Sometimes they’re right, and you get what you expect, other times they’re wrong, and you end up with something that doesn’t quite do what you thought it would. Rarely do you walk away with something that ends up exceeding your expectations. This happened for Tom Knoll, president of Anderson Dahlen, three years ago at FABTECH.
Anderson Dahlen specializes in custom fabrication for the food and chemical industries, among others. Originally focused on stainless steel, they’ve incorporated many specialty alloys into their work. At FABTECH that year, Knoll was looking for equipment that would solve specific welding challenges. One of the applications required small stainless steel welds with minimal rework, since the welds would have to be ground down and blended to an aesthetic finish. After talking with several exhibitors he took a chance on the Fronius TPS/i. The GMAW machine boasted a consistent, precise arc, which seemed to fit the needs of the project.
Once the machine was at the shop, it was up to Troy Stokes, one of the company’s weld supervisors, to test the machine.
“I couldn’t believe how consistent and precise the arc was,” said Stokes. “In getting to know the machine, one of the first welds I made was on a large frame with open root welds. For this application, we would typically roll the frame to weld in position. With the Fronius we were able to weld all the seams without moving the frame. That was pretty much the beginning for me and it’s just spiraled from there.”
That first machine outperformed their expectations on more than the original challenge. Since then Anderson Dahlen has found the versatility of the Fronius machines and their GMAW processes to excel in more applications than they anticipated. Traditionally a GTAW operation, they now use TIG far less, and mostly for specialty projects. In some cases, by using the Fronius GMAW processes they’ve been able to increase their production speeds by three times their previous output, especially with automated welding.
One such automated application required vacuum chambers fabricated of 304 stainless steel. Each vessel, chamber, and chamber door were welded on the turntable with the TPS/i. The project was completed faster than usual due to a lack of repair work and a decrease in down-time. “I couldn’t believe how many quality welds we could make at a time, and without going through as many consumables,” said Stokes. “That’s really the root of what we fell in love with, that consistency.”
That consistency has helped Anderson Dahlen step more boldly into automation. A recent project included 5/16 inch walled vessels constructed of 316 stainless steel. In the past, welding the cone and dome onto the shell took several passes to complete. With the TPS/i, they were able to finish those welds in a single pass. Happy with the increase in production, they looked next to increasing their travel speeds.
They had explored sub-arc welding to reduce production times, but the thin walls of the vessel were a problem. Their top certified welding inspectors (CWIs) worked closely with the manufacturer of the sub-arc machine to develop parameters that would provide 100% penetration and travel speeds in the mid-20s. The manufacturer told them it wasn’t possible using sub-arc without blow-thru or poor penetration, unless they fabricated a copper retainer to hold back the weld puddle.
Certain they could increase the travels speeds, Stokes set up the Fronius TPS/i to run weld tests using the Pulse Multi Control process (PMC). This process offers optimized pulse welding and penetration stabilization for both manual and robotic or automated welding. The test, a single bevel joint for cone to shell attachment, showed that higher travels speeds were necessary to stay ahead of the puddle; slower speeds actually provided less penetration. Since the interior of the part required a food grade finish, they needed a specific root profile to meet the requirements. Testing showed that using a ceramic backer to create a radius in the profile of the root reinforcement would give them the best results. The backer made the final grinding easier and helped solve issues with variances in part fit up. With travel speeds around 26 inches per minute they had the penetration and profile they were looking for, and speeds almost three times faster than they’d achieved previously. This helped cement their move into automated GMAW welding.
Though Anderson Dahlen is seeing a lot of success with their automated welding, they’ve also achieved substantial production increases with their manual welding. One recent challenge included vacuum chambers with varying wall thicknesses of 1-2 inches made of Alpase M1 aluminum, a type of cast plate. Due to the large size of the chambers, all welds were done in position. For this application, the ability to switch between previously saved job programs right on the torch helped to increase production times. It also reduced the need for repairs because each job was tested prior to saving. This meant their weld professionals could work at a higher efficiency overall.
“That's one of the nice things about Fronius,” says Stokes. “You can store all the programs in the machine. It’s real easy to go from one job to the next just by changing your program. You do a little leg work up front and some testing to make sure the welds are good, and then you can just let the welder go. It’s phenomenal. And you can access all of it right from the gun too.”
Stokes is referring to the ability to save up to one thousand parameter sets in the TPS/i memory bank. These “jobs” can be named with memorable titles, rather than just numbers, and can be easily accessed through the available JobMaster torch. This feature allows for easy job changes while welding current projects, and also saves time with repeat customer jobs in the future.
When asked what the future might hold for Anderson Dahlen, as an employee of nineteen years, Troy Stokes has a good idea of what works. He’s certain automation offers the company some of the best opportunities. “There are areas we could take advantage of now that we have such consistency in the arc and because of how well the machines operate. I think we can go down that road a lot further.”
Their plans for increasing their automated welding include purchasing more TPS/i welders, and modifying some of their current equipment to work with the Fronius machines.
“We’re getting ready to run seven gauge stainless tanks on our manipulator with the Fronius torches. Previously, with competitor machines, it took at least two passes at low travel speeds to do these tanks, one on the inside and one on the outside. We’re hoping to complete this application in one pass and triple the travel speed. That will go a long way for the bottom line.”
And when it comes to business that bottom line is a solid indicator of success.
Written by Rhonda Zatezalo.
Rhonda Zatezalo writes freelance articles for the welding industry / www.rhondazatezalo.com