3x speed boost and higher quality welds with Fronius TPS/i
Anderson Dahlen, United States
Anderson Dahlen, Inc is a premier stainless steel and specialty alloy fabricators, specializing in custom fabrication for the food and chemical industries, among others.
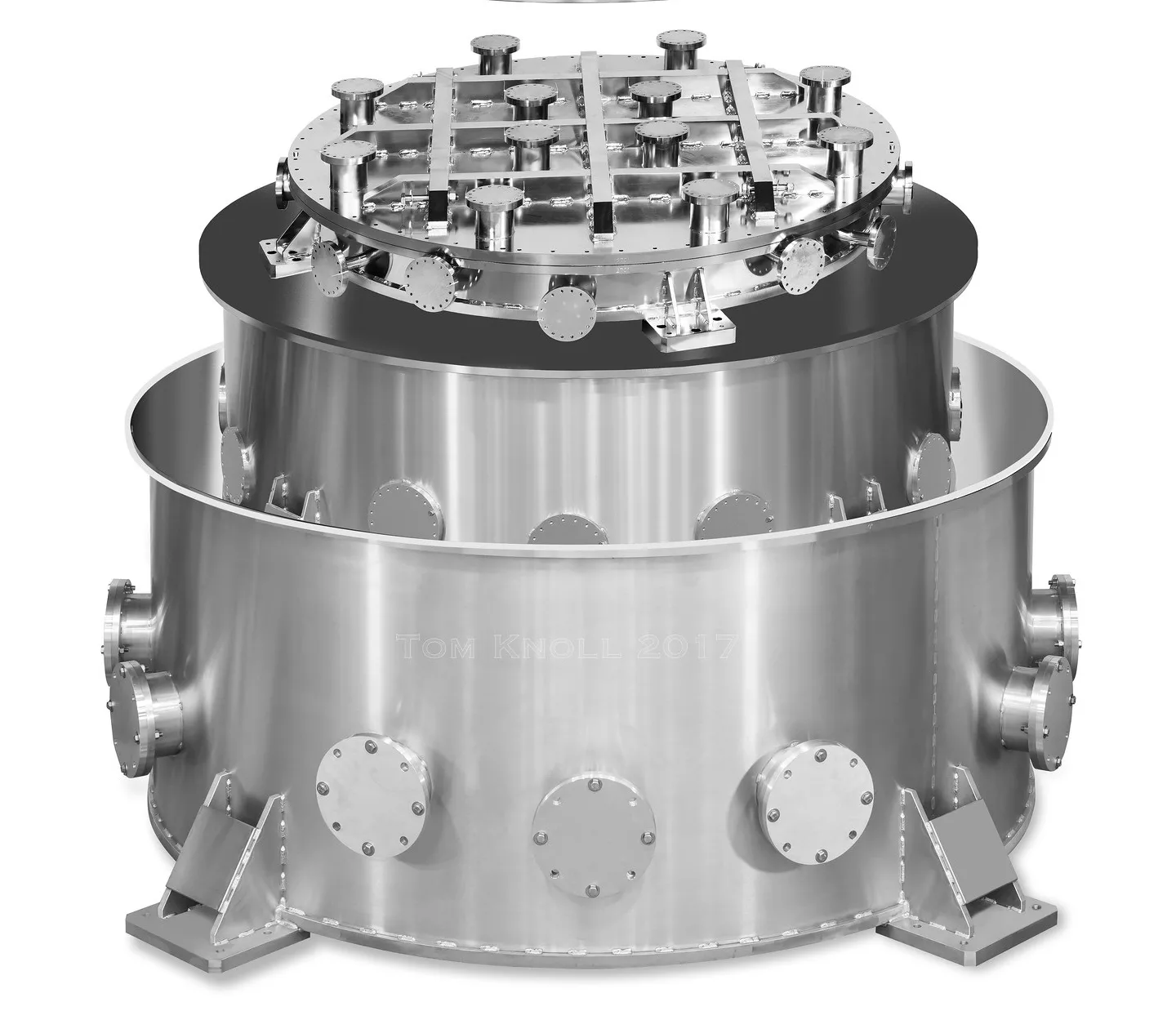
Contact
Downloads
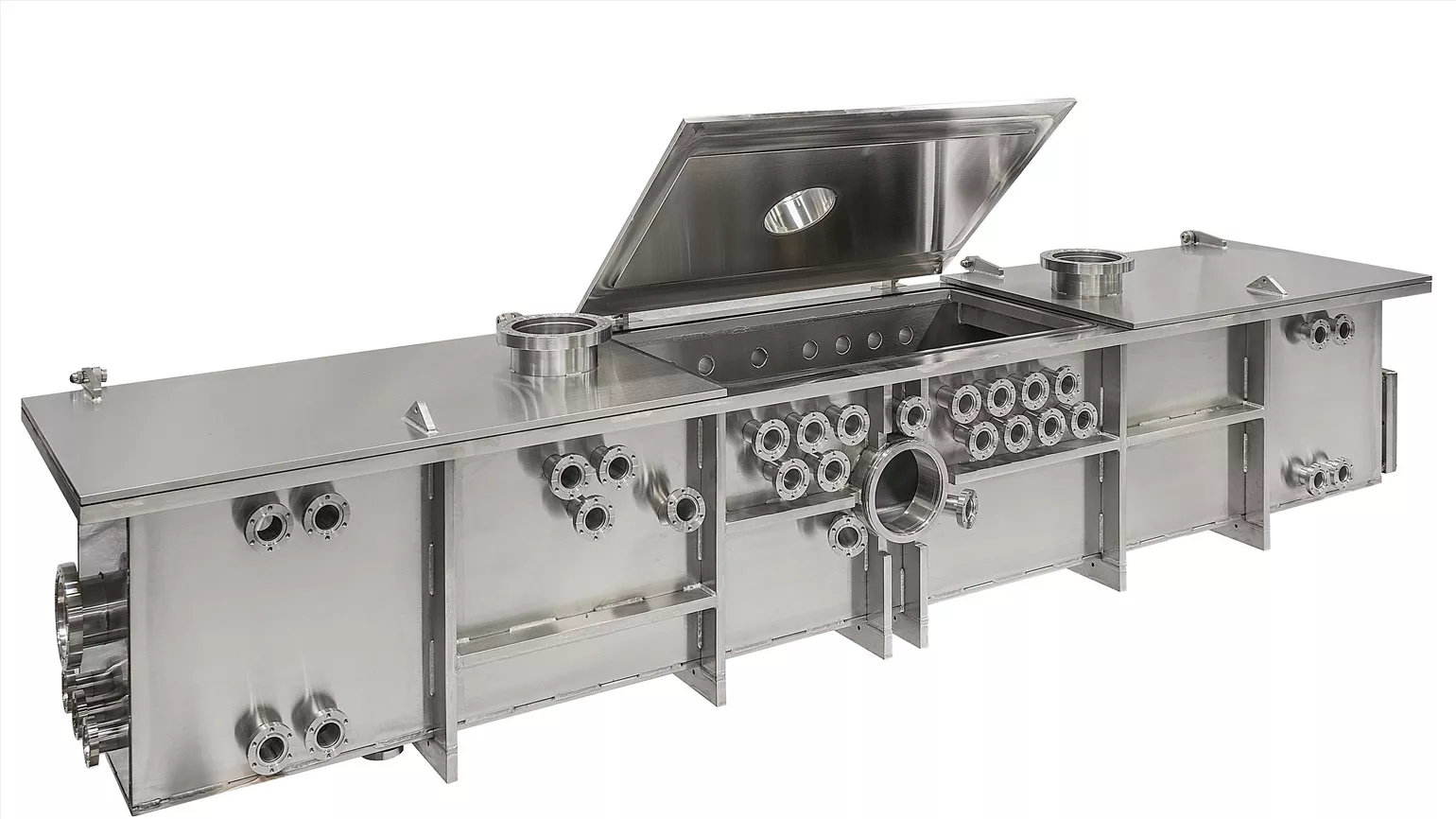
Anderson Dahlen, Inc
“I couldn’t believe how consistent and precise the arc was, in getting to know the machine, one of the first welds I made was on a large frame with open root welds. For this application, we would typically roll the frame to weld in position. With the Fronius we were able to weld all the seams without moving the frame. That was pretty much the beginning for me and it’s just spiraled from there.”
-Troy Stokes, Welding Supervisor
REQUIREMENT
Originally focused on stainless steel, they’ve incorporated many specialty alloys into their work. One of the applications required small stainless steel welds with minimal rework,since the welds would have to be ground down and blended to an aesthetic finish.One recent challenge included vacuum chambers with varying wall thicknesses of 1-2 inches made of aluminum. Due to the large size of the chambers, all welds were done in position. For this application, the ability to switch between previously saved job programs right on the torch helped to increase production times. It also reduced the need for repairs because each job was tested prior to saving.This meant their weld professionals could work at a higher efficiency overall.
SOLUTION
Fronius TPS/i. The GMAW machine boasted a consistent, precise arc, which seemed to fit the needs of the project. That first machine outperformed their expectations on more than the original challenge, traditionally a GTAW operation, they now use TIG far less, and mostly for specialty projects. In some cases, by using the Fronius GMAW processes they’ve been able to increase their production speeds by three times their previous output, especially with automated welding. One such automated application required vacuum chambers fabricated of 304 stainless steel. Each vessel, chamber, and chamber door were welded on the turntable with the TPS/i. The project was completed faster than usual due to a lack of repair work and a decrease in down-time. “I couldn’t believe how many quality welds we could make at a time, and without going through as many consumables,” said Stokes. “That’s really the root of what we fell in love with,that consistency.”
Their plans for increasing their automated welding include purchasing more TPS/i welders, and modifying some of their current equipment to work with the Fronius machines.“We’re getting ready to run seven gauge stainless tanks on our manipulator with the Fronius torches. Previously, with competitor machines, it took at least two passes at low travel speeds to do these tanks, one on the inside and one on the outside. We’re hoping to complete this application in one pass and triple the travel speed. That will go a long way for the bottom line.”