Parés pour l’avenir grâce aux techniques de soudage robotisées intelligentes
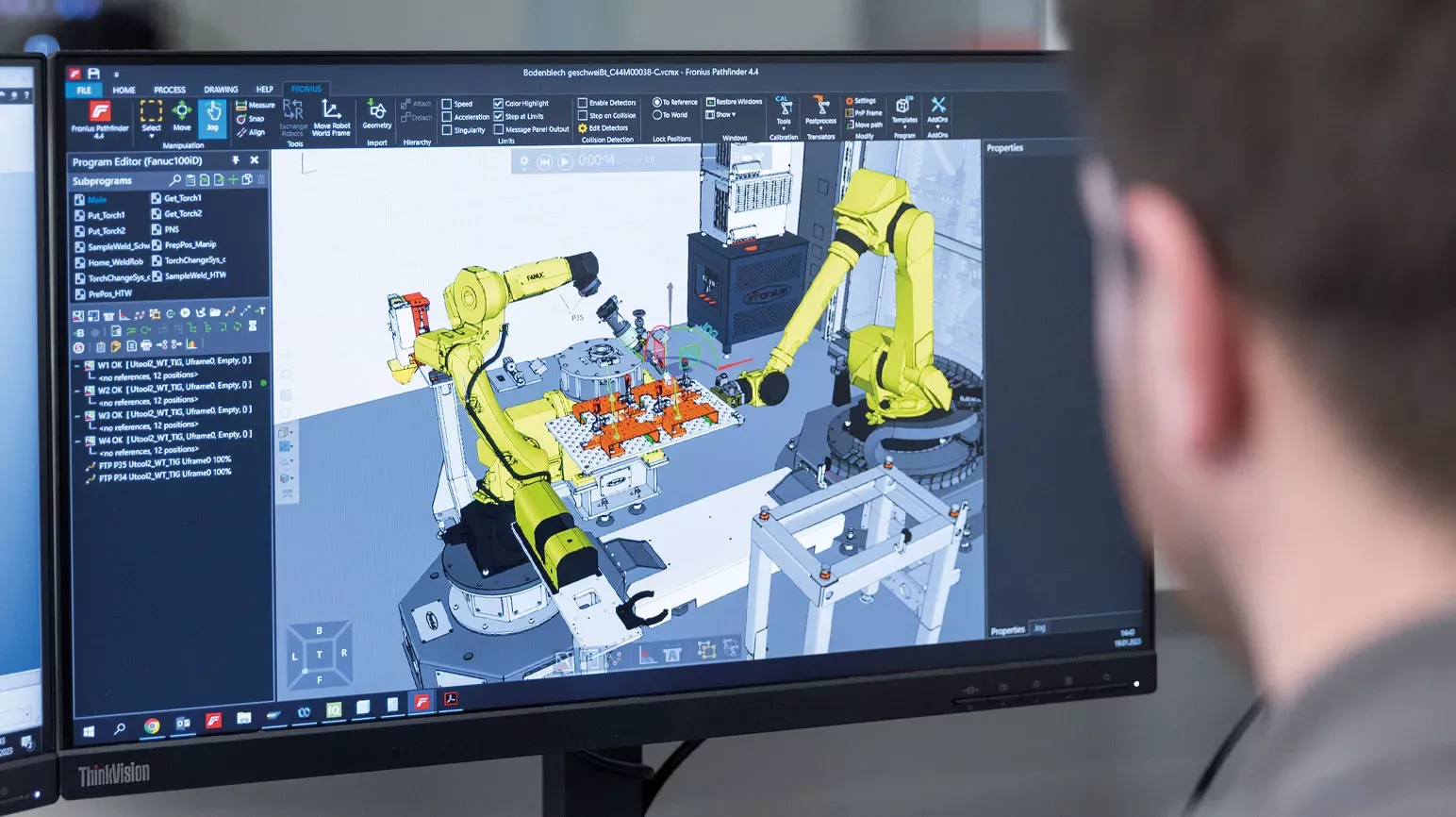
Auparavant, tous les composants des appareils de mesure et de réglage produits à Graz étaient soudés à la main. En effet, pour les lots de petites tailles, entre 1 et 400 unités, des installations de soudage robotisé semblaient peu rentables. Les hausses permanentes du chiffre d’affaires, la pénurie de main d’œuvre croissante sur le marché du travail national et les technologies robotisées innovantes – qui rendent désormais le soudage automatique rentable, même sur des lots de petite taille – ont conduit l’entreprise high tech à investir dans une installation de soudage robotisé moderne. Les spécialistes de la mesure et du réglage exigeaient une rentabilité élevée associée à de la flexibilité à tous les niveaux : pour le nombre, la forme et la taille des composants, pour leur positionnement et pour l’utilisation de différents modes opératoires de soudage.
Dominik Santner, COO d’Anton Paar GmbH, souligne : « La pénurie de main d’œuvre et la hausse permanente des quantités produites requièrent de nouvelles solutions dans la production. Cette nouvelle cellule de soudage robotisé représente un grand pas dans l’automatisation de notre production. Si nous avions continué à souder manuellement nos capteurs de production, nous aurions eu beaucoup de mal à atteindre les quantités de pièces prévues dans les années à venir. »
Autonomie de soudage et diversité des composants
Dès le début, les experts d’Anton Paar ont misé sur l’autonomie de l’installation : une fois équipé, le système de soudage devait être en mesure d’exécuter un ordre complet du début à la fin, en une seule fois – par exemple le soudage d’un lot de différents objets, comme un boîtier d’oscillateur, un support principal ou des dispositifs de contre-refroidissement. Le tout en autonomie parfaite, sans intervention des spécialistes du soudage.
Des composants différents par leur forme, leur poids et leur taille, diverses options de prise en main, de positionnement et de dépose, la possibilité d’utiliser deux modes opératoires de soudage (TIG et MIG/MAG) pour un même composant, ainsi que l’utilisation nécessaire de gaz de formation avec les corps cylindrique pour protéger les composants contre les colorations : tous ces facteurs ont fait que la construction de l’installation fut un défi particulier pour l’équipe d’ingénierie et de programmation.
« Nous étions à la recherche d’un partenaire fiable, très similaire à nous en termes de précision et de qualité. Il devait être réellement à l’écoute, répondre à nos attentes et proposer des solutions durables. Des solutions qui nous confèreraient des avantages concurrentiels au cours des années », déclare Daniel Moik, Department Manager Joining Technologies. « Fronius International répondait à ces critères de partenariat durable. En collaboration étroite avec nos techniciens, l’équipe de Welding Automation a mis au point une cellule de soudage robotisé conforme en tous points à nos exigences. Par ailleurs, Fronius est disposé à faire évoluer l’installation avec nous et à l’adapter à de nouveaux besoins. »
Synonyme d’efficacité : Fronius Pathfinder
Chez Anton Paar, les nouvelles soudures sont programmées hors-ligne, en dehors du système de soudage, et pas directement sur l’installation comme c’est généralement le cas. Au lieu d’interrompre les opérations de soudage en cours, on continue à souder, ce qui permet d’augmenter la productivité. Pour y parvenir, les techniciens de soudage importent les données CAO des composants des appareils de mesure à souder dans le Fronius Pathfinder®. On teste ensuite divers scénarios d’assemblage, on définit des séquences de soudage et on les optimise au cours de simulations.
Ces opérations concernent les trajectoires, les angles de placement de la torche de soudage, les déports de la torche dans les coins et toutes les réorientations du robot de soudage. Le Pathfinder détecte les dépassements de la portée du robot, appelés limites d’axes. Comme les opérateurs du logiciel corrigent le lieu de dépose de la pièce à souder et la positionnent à portée du bras du robot de soudage, ils évitent à l’avance de potentielles collisions de la torche de soudage avec différents bords de composants.
Les sources d’erreurs sont détectées en temps utile
Si des corrections de trajectoire sont nécessaires, les points de programmation concernés peuvent facilement être déplacés par glisser-déposer. Si un déplacement jusqu’au composant doit être modifié, les professionnels appuient brièvement sur « Réinitialisation ». Le robot virtuel se rend alors en position de base pour débuter un nouveau déplacement. En mode de fonctionnement réel, il faudrait dégager le robot, ce qui prend du temps, le placer en position de base à l’aide de la commande du robot et redémarrer le processus de programmation. Ayant opté pour le logiciel de programmation et de simulation hors-ligne Pathfinder, les experts d’Anton Paar gagnent non seulement un temps précieux pour les opérations de soudage, mais peuvent aussi détecter au préalable les sources d’erreurs.
Dès qu’un programme de soudage est terminé dans le Pathfinder, il est traduit dans le code spécifique au robot de soudage Fanuc par un post-processeur. Il peut alors être envoyé à l’installation de soudage par transfert de données – par exemple via une connexion LAN. La fonction « Détermination de la durée de cycle », qui tient compte des vitesses de soudage, des temps de pré-débit de gaz et de remplissage des cratères finaux, constitue un point fort du système et une aide efficace pour toute la planification de production. Par rapport à la programmation avec la commande du robot, le Pathfinder permet d’économiser jusqu’à 90 % de temps – en fonction de la géométrie des composants et des exigences en termes de techniques de soudage.
Sur mesure pour Anton Paar
Pour souder ces nombreux composants différents, Anton Paar dispose de flux de travail qui lui sont spécifiques, dont les 3 flux principaux qui illustrent parfaitement la flexibilité énorme en termes de diversité de composants.
Flux de travail 1 : Les composants sont soudés sur le manipulateur. On retire une palette chargée de composants du rayonnage à palettes et on la dépose sur un plateau de réception. Par la suite, le robot de manipulation prépare une pince adaptée pour récupérer les composants. 6 pinces différentes sont rangées dans ce que l’on appelle une « gare à pinces ». Une fois équipé, le robot de manipulation récupère les composants et les fixe dans un dispositif de blocage spécifique, déjà placé sur le manipulateur. Les composants sont toujours pris l’un après l’autre, puis soudés et replacés sur la palette.
Flux de travail 2 : Les composants sont soudés immédiatement sur les palettes. Le robot de manipulation transporte les palettes en dehors du rayonnage à palettes et les positionne devant le robot de soudage. Pendant le soudage, le robot de manipulation et le robot de soudage peuvent alors exécuter ensemble des mouvements coordonnés et réaliser ainsi des soudures simples, mais aussi des soudures à géométrie complexe.
Flux de travail 3 : Les composants sont récupérés individuellement, amenés en position par le robot de manipulation et se déplacent de manière synchronisée avec le robot pendant le soudage (Coordinated Motion).
Pour que l’installation sache quoi faire
En
dehors de la technologie de soudage innovante de Fronius, des commandes, de la
mesure du Tool-Center-Point (TCP), de la station de nettoyage de la torche et
du boîtier, le système de soudage robotisé se compose de 7 modules de base
dont la collaboration est commandée par un logiciel : un robot de
manipulation, un robot de soudage, un manipulateur avec unité de gaz de
formation, un magasin à palettes avec deux rayonnages, une gare à pinces,
un système de changement de torche et un plateau de réception de palettes à
l’intérieur de l’installation. Les étapes suivantes sont nécessaires pour que
les modules mentionnés ci-dessus interagissent avec précision pendant les
cycles de travail :
On
place tout d’abord les palettes et les composants ensemble dans la commande de
système HMI-T21 RS. Le spécialiste du soudage lui donne 4 informations
importantes : (1) le type de palette, (2) le type, (3) le nombre et (4) la
position des composants sur la palette – par exemple combien de supports
principaux ou boîtiers d’oscillateurs se trouvent à quel endroit sur quelle
palette. S’il s’agit d’une palette de déport, la position du composant est
calculée à partir des distances de déport des composants les uns par rapport
aux autres. La position du premier composant est déterminante. Un déport peut
correspondre par exemple à 200 mm sur les coordonnées y et + 200 mm
sur les coordonnées x. Les palettes fabriquées par Anton Paar se composent de
plaques perforées de plusieurs centimètres d’épaisseur et fonctionnent comme un
système enfichable. Elles se trouvent dans un magasin à palettes composé de
deux rayonnages et sont construites de sorte à pouvoir accueillir chacune
des différentes pièces. Les positions de dépose et de réception des différents
composants sont souvent variables en fonction des propriétés des pièces et de
la pince du robot de manipulation.
Pour
chaque type de flux de travail, la commande du robot contient un programme de
robot hiérarchiquement supérieur, où les programmes de soudage créés avec
Pathfinder sont archivés. Si une palette est placée sur l’HMI pour le flux de
travail 2 (les composants sont soudés directement sur la palette),
celle-ci filtre les programmes de soudage robotisé correspondants et le
spécialiste du soudage d’Anton Paar peut choisir facilement parmi tous ceux qui
sont disponibles pour le flux de travail 2, et attribuer à la palette le
programme de soudage requis. Il est également possible de ne pas utiliser
qu’un seul programme de soudage, mais de créer toute une chaîne de
travail. On peut par exemple commencer par créer un programme TIG pour une
palette, suivi par un programme MAG (par ex. CMT) dans la chaîne actuelle. Dans
ce cas, l’installation de soudage robotisé traiterait les deux programmes
l’un après l’autre en changeant automatiquement de process de soudage. Par
ailleurs, les experts d’Anton Paar peuvent ajouter certaines étapes spéciales à
la procédure HMI. Le système connaît par exemple l’étape spéciale
« Tourner le composant », qui peut être utilisée si nécessaire entre
les deux modes opératoires de soudage (TIG et CMT).
Si
une pince spécifique est nécessaire pour déplacer les palettes, comme décrit
dans le flux de travail 1, les opérateurs de l’installation doivent la
sélectionner dans le système. Comme mentionné plus haut, 6 pinces
différentes sont disponibles au total, toutes rangées dans une « gare à
pinces ».
Programmer
les positions de préhension et de dépose
La
séquence de manipulation classique en elle-même (récupérer la palette, la
mettre en position pour le soudage, la rapporter et la déposer) est un
programme standard qui ne nécessite aucune intervention de l’opérateur. Dans le
jargon technique, on parle d’une fonction « encapsulée ». Il suffit
d’indiquer les positions de préhension.
Lorsqu’un
nouveau composant est « inséré » sans être reconnu par l’une des
stations de dépose ou de réception, la marche automatique se met en pause. Le
spécialiste du soudage est invité à démarrer un processus de programmation avec
la commande du robot – le Fanus iPendant – et obtient pour cela des
instructions étape par étape de la part du logiciel de l’installation. Ainsi,
le système « apprend » la position de préhension/dépose nécessaire
pour la station concernée (par ex. pour le plateau de dépose intermédiaire).
Elle est sauvegardée dans un registre et disponible immédiatement pour la
procédure de manipulation. La marche automatique peut ensuite être poursuivie
jusqu’à la station suivante. Si le composant y est aussi inconnu, il faut
également programmer cette position. Une fois toutes les stations traitées
selon le schéma décrit ci-dessus, le robot de manipulation transporte tous les
autres composants identiques de manière entièrement automatique à travers
l’installation, sans interruption.
Si
7 composants sont prévus pour une palette mais que celle-ci n’en
contient que 3, cela n’est pas un problème pour l’installation. Elle détecte
une « préhension à vide » et se déplace automatiquement jusqu’à la
position du composant suivant.
Sur mesure : la palette de programmation
En
plus de l’affectation de déport par défaut qui privilégie des formes de
composants simples, Anton Paar s’est fixé l’objectif de pouvoir déposer jusqu’à
30 composants métalliques sur n’importe quels emplacements de palettes.
Fronius a exaucé ce souhait avec la fonction « palette de
programmation ». Lorsque celle-ci est sélectionnée, la position de chaque
composant sur la palette peut être programmée séparément.
« Ces
deux variantes – palette de déport et palette de programmation – nous
offrent une flexibilité maximale dans le montage des composants »,
explique le Dr. Ingo Riemenschneider, Department Manager Production
Automation. « Il n’est pas toujours judicieux de définir des positions de
composants selon des distances de déport. Il existe des composants que nous
devons fixer dans différentes orientations en raison de leurs formes
complexes. »