Dump trucks for tough construction site conditions
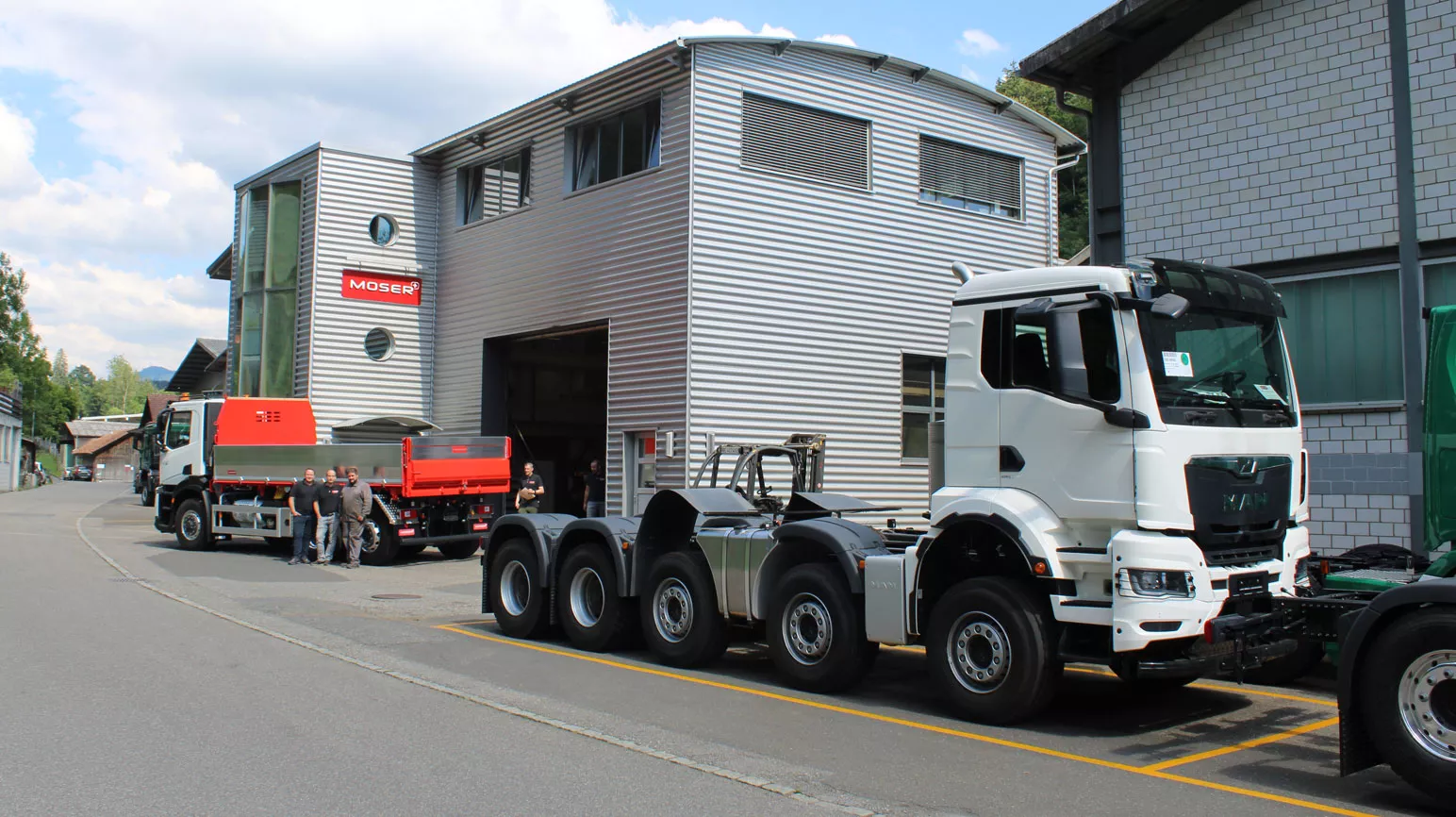
Poids propre réduit : « Toujours une charge d’avance »
L’entreprise Moser AG fabrique des superstructures pour des camions d’un poids total compris entre 18 et 40 tonnes, ces derniers pouvant accueillir plus de 25 tonnes de charge utile. « Dans notre secteur, il est essentiel de transporter un maximum de charge à chaque trajet. Pour que nos clientes et clients puissent transporter autant de matière que possible, nous construisons des bennes et des systèmes de chargement d’une légèreté maximale, sans pour autant faire de compromis sur la solidité, la résistance ou la facilité d’utilisation », souligne Stefan Rolli, directeur des opérations chez Moser AG.
En fonction de la taille et du nombre d’essieux des camions auxquels elles sont destinées, les superstructures produites à Steffisburg pèsent généralement entre 3 et 4,5 tonnes. « En utilisant nos superstructures, plus légères que celles de nos concurrents, nos clients gagnent souvent entre 500 et 700 kg de charge utile par trajet. L’efficacité des véhicules est dont nettement plus élevée, et nous sommes fidèles à notre devise, "Toujours une charge d’avance" », déclare Stefan Rolli.
La proximité avec les clients favorise la production sur mesure
Les superstructures fabriquées sur mesure par Moser AG, selon les exigences individuelles des clients, conviennent à tous les types de camions courants. L’entreprise bernoise est particulièrement fière de produire l’intégralité de ses bennes et systèmes de chargement sur son propre site de Steffisburg, à partir de la livraison des tôles et profilés :
« Nous sommes aujourd’hui la seule entreprise de Suisse qui produit des superstructures d’utilitaires pour le secteur de la construction à un tel degré d’intégration verticale. Nous avons le contrôle sur tous les processus de production essentiels et nous sommes proches de nos clients, ce qui nous permet d’apporter des réponses rapides et flexibles aux demandes spécifiques », explique le directeur des opérations chez Moser, Stefan Rolli.
Chaque année, plus de 200 camions quittent l’usine de Steffisburg ; il faut en moyenne 6 à 8 semaines pour produire une nouvelle benne.
Aperçu des processus de production
Dans les grandes lignes, les processus de production chez Moser AG se divisent comme suit : les camions sont d’abord mesurés dans le moindre détail à leur arrivée. Après la construction des superstructures à l’aide de systèmes de CAO, suivie de la préparation des travaux, la prochaine étape consiste à découper les tôles sur une installation de découpe plasma CNC, à les plier sur une presse CNC et à poursuivre leur traitement mécanique dans un centre d’usinage CNC.
Dans les ateliers métallurgiques de Moser AG, les composants sont soudés ensemble afin de fabriquer les bennes dans leur forme brute. Les superstructures sont ensuite nettoyées par sablage, puis peintes. Une fois le système hydraulique installé, les opérations de pré-assemblage et de montage final ont lieu. Avant que le camion ne quitte l’enceinte de Moser AG à Steffisburg pour accomplir ses nouvelles missions, il est d’abord soumis à un scrupuleux contrôle final.
De l’acier et de l’aluminium jusqu’à 70 mm
Pour produire ses superstructures de camions, Moser soude de l’acier de construction S355 traditionnel, des aciers de S690 à S700 et Hardox 450 de différentes épaisseurs comprises entre 3 mm et 70 mm. La tôle d’acier Hardox 450 de 4 mm d’épaisseur est la plus utilisée.
Les tôles d’aluminium usinées à Steffisburg sont généralement épaisses de 2 mm, les tôles striées en aluminium ont une épaisseur de 3/4,5 mm ou 3/6,5 mm. Des alliages d’aluminium relativement légers sont notamment utilisés pour les parois latérales des bennes. Ils sont extrudés à l’aide d’un moule développé par Moser AG, tandis que le système de profilé en aluminium Moser MAP permet une construction modulaire des parois latérales. Les tôles en aluminium sont également utilisées pour les garde-boues, les caches et les marchepieds.
Focus on MAG manual welding – frequent out-of-position welding
The vast majority of welds at Moser AG are welded manually using the GMAW process. In addition to considerable welding speeds, this process delivers high deposition rates, while relatively little energy per unit length is input into the dumper parts to be welded.
For series production parts or repetitive processes, such as welding the subframes of the dumper bodies, a gantry system with a welding robot is used in Steffisburg. The gantry system makes it possible to turn the entire dumper so it is in the appropriate welding position.
“The characteristics of the weld are provided by the WPS. For the thicknesses of the fillet welds, we generally adhere to the A dimension, i.e., the thickness of the thinnest sheet element multiplied by 0.7,” explains Stefan Rolli.
To withstand the high loads in day-to-day use on construction sites, many welds are welded with a root pass and up to two final runs. In addition to fillet welds, butt welds – with and without an air gap – are also very frequently used. One task that the welders at Moser AG are regularly confronted with is out-of-position welding: from “classic” vertical-up seams on the pipe and sheet metal to overhead welds.
Four generations of Fronius devices
Moser AG has been using Fronius welding systems for 24 years. Today, around 35 devices from four different Fronius generations are used daily in Steffisburg: the Fronius VarioSynergic 4000, the VarioStar 457, the TransSynergic 5000, plus the Fronius TPS 500i since 2018.
Fronius TPS 500i: efficiency through precisely adjustable welding characteristics
“Speed and flexibility in manufacturing are crucial for us, especially in the current situation. By using the Fronius TPS 500i and its welding characteristics, we have significantly increased welding speeds in all key areas. At the same time, there has been a noticeable reduction in the amount of rework required on the welds. Overall, the TPS 500i not only makes the welding processes considerably more efficient, but also the downstream work steps, which subsequently has a positive effect on our entire manufacturing process,” says Moser operations manager Stefan Rolli.
The welding specialists at Moser AG frequently use the PMC Fronius Welding Package in the PMC Universal, PMC Dynamic, and PMC Mix variants on their TPS-500i devices. PMC stands for Pulse Multi Control and is a further development of the pulsed arc.
“In general, the PMC characteristics feature a stable, dynamic, and low-spatter pulsed arc. The excellent welding speeds of the TPSi are made possible predominantly by their high processor performance and the corresponding measuring and control speeds,” explains Fritz Loosli, the application engineer and customer adviser at Fronius responsible for Moser AG. The PMC characteristics provide two stabilizer and two correction parameters: an arc length stabilizer and a penetration stabilizer, as well as arc length control and pulse correction.
Up to 40 percent faster welding of vertical-up seams
The welding specialists at Moser AG use the PMC Mix characteristic, among others, because it permits the welding of vertical-up seams without the usual oscillating motion. Overall, up to 40 percent faster welding speeds are possible with the PMC Mix process for vertical-up seams. The technical basis for this characteristic is the process change between a pulsed and dip transfer arc, i.e., the cyclical change between a hot and a cold supporting process phase. The heat input into the material is reduced by this process.
Steel Root is another characteristic that is often used by the welding specialists at Moser AG. This characteristic excels at bridging gaps of 2 to 3 millimeters in size when welding dumper parts. A soft and stable arc is a typical feature of the Steel Root characteristic. The detachment of relatively large droplets creates a viscous weld pool, which can be used to weld larger gaps with ease.
The PMC Dynamic welding characteristic is used at Moser for horizontal fillet welds. It delivers a relatively aggressive arc with high pressure and concentrated focus. Your advantage: High welding speeds with low energy input enable low-distortion welding results and save valuable resources such as gas, filler metal and working hours.
Aside from this, Moser still uses tried-and-tested standard arcs for many welding processes. As a rule, aluminum parts are welded with a conventional pulsed arc.
User-friendliness on the welding system and directly on the welding torch
In addition to its welding characteristics, the TPS 500i’s high degree of user-friendliness also helps to make welding processes simpler, faster, and more efficient. The large clear text display on the TPSi is adapted to the welding environment. It is easy and intuitive to use in the respective local language, even when wearing gloves.
In connection with the user-friendliness of their equipment, it is essential for the welding specialists at Moser AG to be able to make adjustments directly on the welding torch: “Dump trucks are components that can’t exactly be moved back and forth quickly and easily, so our employees move around the components. To give our welders maximum freedom of movement, all our welding systems are equipped with 10 meter-long hosepacks,” explains Stefan Rolli.
The welders use lightweight PullMig welding torches in the JobMaster version with their TPS-500i devices. The water-cooled welding torches are equipped with a small electric motor in the torch handle, which ensures smooth wirefeeding through the 10 meter-long hosepack.
Fewer trips – greater efficiency
With the “EasyJob” JobMaster setting, users have the option of saving up to five welding jobs directly on the welding torch and rapidly switching between individual jobs. Being able to call up all the important welding jobs for their day-to-day work directly on the welding torch means they save themselves numerous trips between the welding system and the component. This makes day-to-day work not only more convenient, but also significantly more efficient.
“We have been using Fronius welding systems for 24 years because we see Fronius as a partner who stands for quality, reliability, sound advice, and innovative products. The ongoing technical developments, such as the TPS 500i most recently with its welding characteristics, contribute significantly to our performance, especially in terms of the speed and flexibility of our manufacturing process. The welding systems from Fronius help us to provide our customers in the Swiss construction site sector with the quality they rightfully demand from us,” concludes Moser operations manager Stefan Rolli.