Une qualité optimale grâce à des systèmes d'assistance robotique intelligents
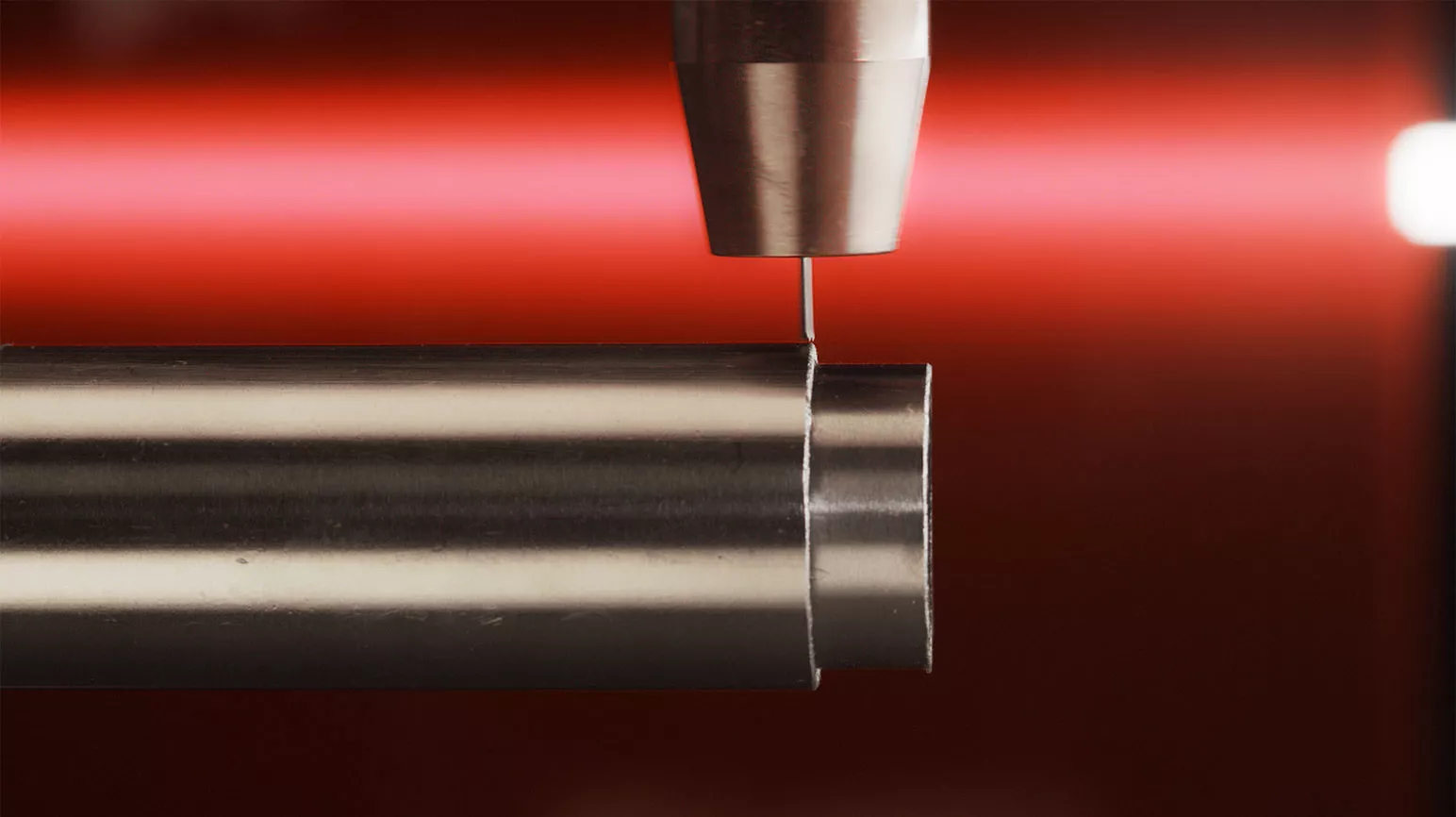
Malgré une technologie robotique avancée et des systèmes interconnectés presque sans faille, des imprécisions et des déviations se produisent régulièrement dans la production industrielle. Dans certains cas, des différences minimes entre les matériaux ou des dispositifs de serrage imprécis peuvent avoir une influence négative sur le résultat du soudage et entraîner des retouches fastidieuses, des rejets de composants coûteux ou des pertes de temps de cycle considérables.
Les intégrateurs ont souvent recours à des systèmes de mesure optique pour éviter de devoir procéder à des réajustements manuels qui prennent beaucoup de temps. Mais les systèmes à laser et à caméra sont coûteux à l'achat et à l'entretien, et nécessitent de l'espace, ce qui limite l'accès au composant. Fronius a la réponse sous la forme de solutions de haute technologie pour les systèmes de soudage intelligents iWave, TPS/i et TPS/i TWIN, qui ne nécessitent ni caméra ni réajustement manuel.
Des soudures parfaites l'une après l'autre malgré les tolérances de serrage et de composants
Le système d'assistance TouchSense a été spécialement développé pour les soudures d'angle. Avant chaque soudure, le robot touche automatiquement les tôles à assembler au début et à la fin de la soudure. Peu importe que ce soit le fil-électrode ou la buse de gaz qui entre en contact : le signal est toujours clairement attribué et correctement transféré. La faible tension du capteur crée un court-circuit lorsque la torche touche la pièce, ce qui permet au robot de déterminer avec précision la position de la soudure et d'ajuster les paramètres de soudage de manière dynamique. Une autre caractéristique utile est l'avertissement immédiat émis en cas de formation d'un pont de projections entre la pointe de contact et la buse de gaz, ce qui permet de le nettoyer rapidement et d'accroître la précision et la qualité de la production.
WireSense - une précision unique grâce à la technologie CMT
L'intelligence de WireSense réside dans sa simplicité. « L'ajout d'un logiciel de commande spécial à notre entraînement CMT hautement sensible et dynamique transforme le fil de soudage en un capteur capable d'identifier les contours ou les écarts d'entrefer sur le composant », explique Philipp Schlor, Strategic Product Manager, Industrial Welding Solutions, chez Fronius International. Pour garantir un contrôle précis du fil de soudage, il suffit d'équiper le système de soudage Fronius d'un système CMT-ready. Le Welding Package, c'est-à-dire le procédé de soudage CMT (Cold Metal Transfer) lui-même, n'est pas nécessaire.
Les systèmes prêts pour CMT se composent d'un dévidoir de fil sur un tambour ou une bobine de fil, d'un tampon de fil et d'un CMT Robacta Drive, c'est-à-dire d'un deuxième dévidoir de fil sur la torche elle-même. Un mouvement inverse du fil, qui se produit à environ 100 Hz, permet au moteur électrique de l'unité d'entraînement de balayer la surface métallique avec le fil. C'est ce balayage à haute fréquence de la pièce qui permet d'atteindre les niveaux de précision nécessaires. Même si la surface à scanner est irrégulière, par exemple si les tôles sont inclinées, le bord peut être détecté et mesuré sans difficulté.
Détection de la position du bord et de la hauteur de l'entrefer
« Notre technologie révolutionnaire WireSense utilise la fonction de balayage du mouvement inversé du fil CMT pour déterminer la position exacte du composant et du bord, ainsi que la hauteur de l'entrefer. Les tôles d'acier, d'acier inoxydable et d'aluminium d'une épaisseur de 0,5 à 20 millimètres peuvent être scannées rapidement et avec précision », souligne M. Schlor. Chaque opération de levage et d'abaissement du composant peut être enregistrée avec une extrême précision par rapport à un point de référence spécifié au début du processus de numérisation. En quelques secondes, le robot a comparé les positions enregistrées avec les positions mesurées, c'est-à-dire qu'il a vérifié les valeurs enregistrées par rapport aux données de position réelles. S'il détecte des différences, le tracé de la soudure est ajusté en conséquence dans le système de coordonnées du robot et la soudure est produite au bon endroit.
« WireSense offre aux intégrateurs de robots une multitude de possibilités d'identifier des solutions de haute qualité pour des tâches de soudage difficiles », explique M. Schlor : »Le bord à souder ne doit pas nécessairement être détecté. Tout bord de référence fixe sur le composant, tel que le bord du composant ou une encoche, peut servir de point de départ à partir duquel le soudage doit s'effectuer à une certaine distance. Ainsi, même les pièces difficiles à détecter, comme une tôle arrondie, peuvent être soudées à la position souhaitée. »
Combler de manière fiable les fuites d'air
Avec WireSense, le fil-électrode devient un capteur de hauteur, ce qui permet de déterminer les entrefers sur les joints de recouvrement à l'aide de la hauteur du bord de la tôle mesurée avec précision. Pour obtenir des résultats parfaits, il est possible de spécifier à l'avance les tâches enregistrées sur le système de soudage Fronius qui doivent être appelées pour différentes tailles d'entrefer. Ainsi, le robot réagit toujours de manière appropriée et soude avec les paramètres de soudage idéaux pour la dimension de l'entrefer en question, ce qui permet d'éviter les erreurs de soudage et les reprises fastidieuses.
SeamTracking: seam tracking during welding
This assistance system plays to its strengths when it comes to manufacturing railroad or construction vehicles. When thick sheets or long seams are being welded, the heat input can lead to component distortion. To ensure the robot still welds in the right location, a system is needed which reliably detects the welding position during welding, such as on a fillet weld or prepared butt weld.
To do so, the robot moves back and forth between the two sheets during welding. The controller converts the actual values identified into signals for the robot controller. The robot then uses these signals to identify the specified welding position, or possible deviations from it, and corrects the path automatically to ensure welding takes place reliably and in the correct location.
Program robots up to 30 percent faster
The key to high quality lies in teaching the correct welding path. The tried-and-tested TeachMode assistance system helps the welder set the weld seam positions on the robot, making the programming process extremely easy. The reversing wire movement prevents the wire from bending in the event of contact with the component and saves the user from having to remove the deformed wire or re-measure the stickout.
Wire-based assistance systems save time, money, and resources
Using the existing wire electrode as a sensor not only reduces expenditure and maintenance costs for additional sensor hardware, but also frees up space as access to the component is not restricted in any way. At the same time, the Fronius assistance systems cut rejects and time-consuming rework because welding is performed reliably at the correct location. Subsequent re-programming of robot paths is also minimized as the robot can correct the weld seam path by itself. All these factors increase efficiency in production while also reducing the amount of time spent and material used.
Video material:
WireSense: https://www.youtube.com/watch?v=C0YawfPs_Tk
TeachMode: https://www.youtube.com/watch?v=95zvimzn0s0
TouchSense & SeamTracking: https://www.youtube.com/watch?v=16rglvD8qLc&t=3s