Budúcnosť automobilového priemyslu so spoločnosťou Magna Presstec
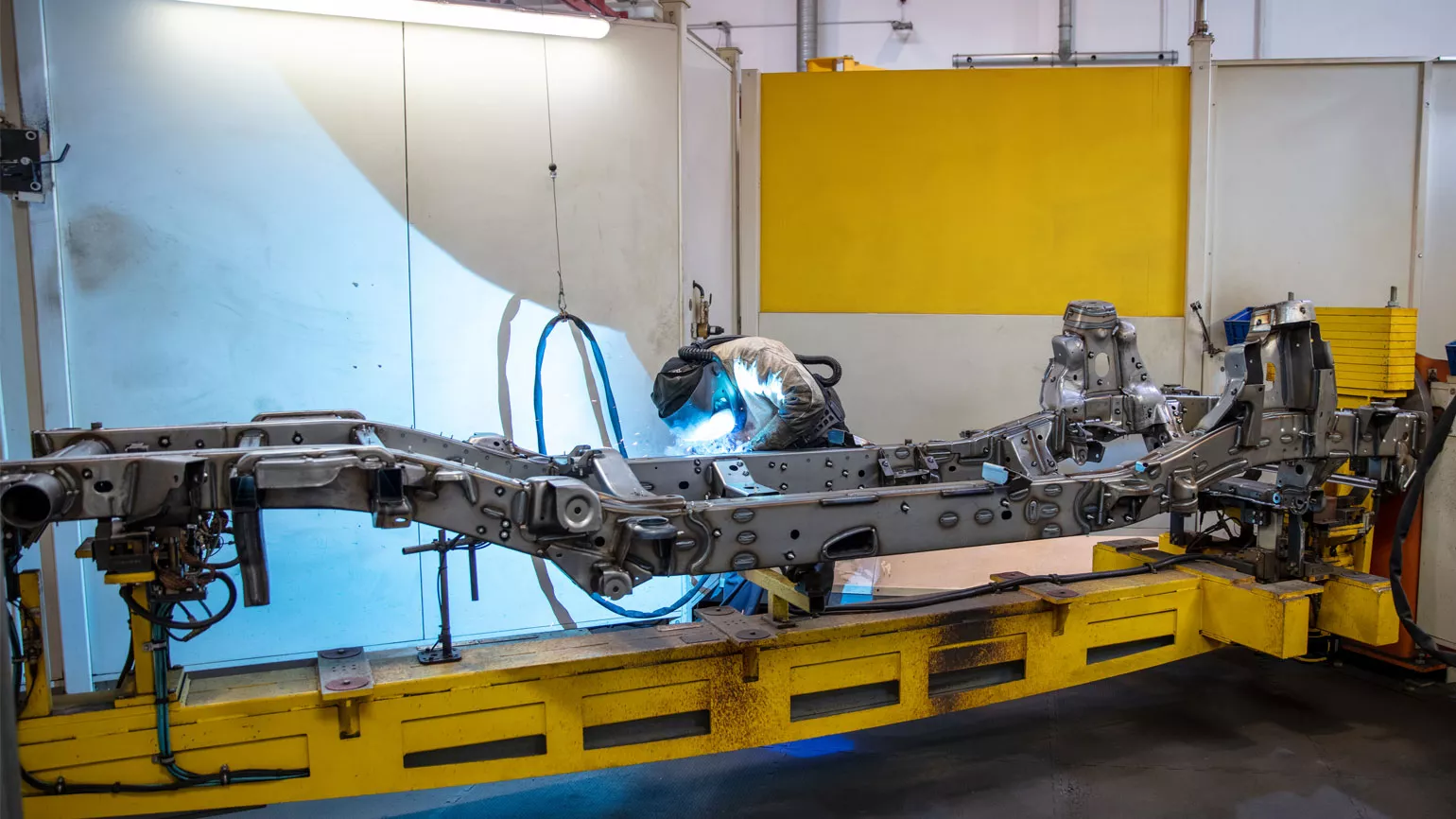
Koncern Magna, ktorý je dodávateľom pre automobilový priemysel, vybudoval v okolí Grazu optimálnu výrobnú infraštruktúru: Spoločnosť Magna Presstec GmbH sídliaca v Lebringu, vzdialenom pol hodiny cesty autom juhovýchodne od Grazu, vyrába základnú konštrukciu vozidiel modelu G. V závode spoločnosti Magna Steyr Fahrzeugtechnik AG & Co KG v Grazi sa potom výroba tohto špičkového terénneho automobilu dokončuje.
Základ pre automobilovú „smotánku“
„V rámci koncernu Magna Group s približne 158 000 zamestnancami po celom svete je spoločnosť Magna Presstec súčasťou skupiny COSMA (Body and Chassis), vysvetľuje Kurt Hartmann, vedúci oddelenia zabezpečenia kvality a dozoru pri zváraní vo výrobe rámov vozidiel Mercedes triedy G. Samotný Presstec zamestnáva približne 1 200 zamestnancov, ktorí pracujú v rakúskych prevádzkach vo Weize a Lebringu, ako aj v slovenskom závode v Bratislave.
Tento dodávateľ pre automobilový priemysel vyrába vysokokvalitné podvozkové komponenty a konštrukčné diely z hliníka a ocele. „Medzi našich zákazníkov patria značky ako VW, Audi, BMW, Daimler či Porsche. Úspešne tu vyrábame budúcnosť automobilového priemyslu. Robíme to s vášňou a osobnou zodpovednosťou,“ pokračuje Hartmann.
Špičkové offroady vyžadujú tú najvyššiu kvalitu zvarových spojov
Mercedes triedy G je považovaný za jedno z najodolnejších terénnych vozidiel na svete, ktoré je zároveň aj jedným z najvhodnejších na každodenné používanie. Napovedá to už jeho vysoká svetlá výška a brodivosť: je navrhnuté tak, aby obstálo aj v tých najnáročnejších terénnych podmienkach.
Pri vystavení prudkým nárazom vo vysokej rýchlosti v neschodnom teréne potrebuje „Géčko“ dobrý ťah a vysokú odolnosť. Ako napríklad pri kontinuálnych dlhodobých testoch v strmom teréne vrchu Schöckl pri Grazi. Vozidlá tam veľmi dôkladne testujú na veľkolepej horskej dráhe. Z toho je jasné, že aj konštrukcii rámov vozidiel triedy G je potrebné venovať maximálnu pozornosť. Asi netreba zdôrazňovať, že najvyššie nároky sa pritom kladú na kvalitu zvarových spojov.
Požiadavky vozidiel Mercedes triedy G na zváraciu techniku
„Používajú sa pri tom oceľové plechy prevažne s hrúbkou 2 až 4 milimetre, ktoré sú zvarené 657 zvarovými spojmi. Celková dĺžka zvaru je 76 metrov na každý rám. Naša zváračská úloha v podstate spočíva v tom, že musíme pozvárať 4,2 metra dlhý rám podvozka vrstvu po vrstve tak, aby spĺňal požiadavky špičkovej kvality a zároveň sa pritom dodržali tolerancie stanovené zákazníkom,“ vysvetľuje Kurt Hartmann.
Z tohto dôvodu sa pri zariaďovaní výrobnej linky kládli rôzne požiadavky na technológiu spájania: vyžadovala sa vysoká stabilita elektrického oblúka s dokonalým závarom, aby bolo možné dosiahnuť nevyhnutne potrebnú stabilitu masívneho rámu. Špičková kvalita si okrem toho vyžadovala aj čo najnižšiu mieru deformácie a kontrolovateľné vnášanie tepla. Z hľadiska produktivity boli ďalej potrebné vysoké rýchlosti zvárania.
„Proces PMC (pulse multicontrol) od spoločnosti Fronius najlepšie spĺňal naše požiadavky,“ ubezpečuje Hartmann, ktorý je sám medzinárodným expertom na zváranie. „Predpokladom preto bola modulárna platforma zváracích systémov TPS 500i. Jednoduchá obsluha a bezproblémové pripojenie na robota boli pre nás príjemným doplnkom k tomuto balíku. V modelovom rade vozidiel Mercedes G momentálne používame 36 týchto zváracích systémov. Okrem toho máme k dispozícii aj niekoľko systémov TPS 320i pre prípadné ručné zváranie na účely kontroly kvality.“
Podrobnosti o autonómnej špičkovej výrobe
Našou ambíciou je, aby bol každý rám úplne rovnaký – odchýlkam musíme zamedziť,“ vysvetľuje p. Hartmann. Výroba prebieha v jednej z najlepšie vybavených výrobných hál, v priestore s dĺžkou vyše 100 metrov. Prevažne autonómna výroba spĺňa tie najvyššie štandardy a dokonale skoordinované robotické systémy do seba hladko zapadajú. Vďaka tomu každých 10 minút opustí výrobnú halu robustný rám modelu G, pozostávajúci z množstva dokonale zvarených dielov.
Výroba prebieha v troch výrobných úsekoch: predná a zadná časť rámu sa vyrábajú súčasne. Na začiatku niekoľko pracovníkov naloží komponenty do zváracích zariadení. Tie sa potom zvárajú zváracími robotmi v robotických bunkách. Manipulačný robot vezme hotové komponenty, prenesie ich do ďalšej bunky a tam ich umiestni do požadovanej polohy. Na konci každého úseku Information Class: Public sa nachádza bunka, ktorá je neprístupná pre zamestnancov. Slúži na zváranie dlhých spojov. Používa sa však aj ako chladiaca alebo komplexná stanica, ako napríklad pri procese stláčania (squeezing): pri ňom spodné polovice pozdĺžnych nosníkov zapadnú do vrchných, umiestnia sa do požadovanej polohy a zvárajú sa pod tlakom.
Nakoniec sa v stanici na konštrukciu podvozkov – poslednom úseku výroby – spojí predná a zadná časť konštrukcie. Rám tak nadobudne svoj charakteristický tvar. V posledných krokoch pracovného postupu sa potom vyrazia jednotlivé spojovacie body pre podvozok. Dodatočne sa k rámu zdvihovým zapaľovaním privarí 192 svorníkov. Následne sa skontroluje kvalita zvarov, odstránia sa prípadné rozstreky pri zváraní a v prípade potreby sa zvary dodatočne upravia. Na záver sa rám ešte raz presne zmeria pomocou laserovej technológie riadenej robotom, aby sa zistilo, či spĺňa všetky kritériá kvality.
Vysoko profesionálna správa zváracích údajov
Tento mimoriadne komplexný výrobný postup jasne preukazuje, že v spoločnosti Magna Presstec ide o oveľa viac ako len o zváranie. Aby bolo možné zaručiť vysoký stupeň automatizácie pri zachovaní rovnakej kvality pre líniu vozidiel G, zamerali sme sa od začiatku na integráciu nástrojov na monitorovanie a analýzu údajov o zváracích procesoch. Dodávateľ pre automobilový priemysel hľadal na spoluprácu expertov na technológiu spájania, ktorých systémy a riešenia by mu umožňovali stopercentnú digitálnu sledovateľnosť zváracích procesov:
Vďaka softvérovému riešeniu WeldCube Premium sa tu spoločnosti Fronius po prvýkrát podarilo vytvoriť komplexný systém správy zváracích údajov vo výrobe dodávateľa prvého stupňa a poukázať na výhody rôznych používaných softvérových systémov:
Od zabezpečenia kvality po predvídavú údržbu: Softvérové riešenia WELDCUBE PREMIUM a CENTRÁLNA SPRÁVA POUŽÍVATEĽOV
„V spoločnosti Fronius sme našli skvelého partnera,“ zdôrazňuje Kurt Hartmann. „WeldCube Premium je základným pilierom nášho manažmentu kvality. Absolútna sledovateľnosť každého jedného zvaru je pre nás nesmierne dôležitá.“Na staniciach kontroly kvality dostávajú vyškolení zamestnanci prostredníctvom terminálu tie najpresnejšie informácie: sú niektoré zvary príliš nápadné alebo sú naozaj chybné? Miesta preskúmané pomocou softvéru Fronius WeldCube sa podrobujú dôkladnej vizuálnej kontrole a v prípade potreby sa dodatočne upravia. Až potom je rám pre „Géčko“ pripravený na ďalšie kroky výrobného procesu. Zozbierané údaje sa potom znovu použijú na optimalizáciu automatizovaných zváracích procesov.
WeldCube Premium zaznamená každý milimeter zvarového spoja. Vďaka tomu je možné ľahko analyzovať náklady na spotrebný materiál, ako je plyn a zvárací drôt. Jeho potenciál je však oveľa väčší: jeho súčasťou je napríklad Predictive Maintenance (predvídavá údržba), teda schopnosť včas a v dostatočnom množstve objednať spotrebné diely a materiály.
„Predvídavá údržba prostredníctvom riešenia WeldCube Premium by mohla znamenať potenciálne úspory nákladov. Napríklad určovaním presných intervalov údržby na základe správy zváracích údajov,“uvažuje p. Hartmann. „Vždy by sme mali presné informácie o stave kontaktných špičiek, nadstavcov, zváracích horákov a podávacích zariadení. Umožňovalo by nám to vykonať včas servis príslušných zariadení, aby sme sa vyhli chybným zvarom, dodatočným úpravám alebo dokonca nepodareným konštrukčným dielom.“
Spoločnosť Magna Presstec už okrem toho používa aj riešenie Central User Management (Centrálna správa požívateľov ) (CENTRUM) od spoločnosti Fronius, ktoré je veľmi nápomocné aj v oblasti manažmentu kvality. Oprávnenia používateľov a zváračské oprávnenia sa spravujú centrálne. Zvárač sa pri prúdovom zdroji overuje pomocou čipovej karty. To zaručuje, že so stanovenými zváracími parametrami môžu pracovať len špeciálne vyškolení zamestnanci, čím sa v maximálnej miere eliminujú zdroje chýb.
Magna Presstec to potvrdzuje: správa zváracích údajov sa ukázala ako veľmi praktická
Christoph Pangerl, manažér pre kľúčových zákazníkov spoločnosti Fronius, ktorý má na starosti spoločnosť Magna, je presvedčený, že: „Poznatky získané na základe spolupráce so spoločnosťou Magna Presstec boli veľmi cenné. Mohli sme ich priamo zapracovať do vývoja našich produktov. Tým sme sprístupnili naše softvérové riešenia širokému okruhu zákazníkov.“Kurt Hartmann na jeho myšlienku nadväzuje: „Predovšetkým správa zváracích údajov nám pomohla pri optimalizácií našej technológie spájania vo všetkých oblastiach. Spoločnosť Fronius nám poskytla skutočne veľmi výkonný nástroj, ktorý má obrovský potenciál. Vďaka technickej podpore odborníkov spoločnosti Fronius môžeme teraz tento systém rentabilne využívať.“
With its WeldCube Premium software package, Fronius was for the first time able to install a comprehensive welding data management system in the production facilities of a Tier 1 supplier, and to demonstrate the benefits of the various software systems being used.
From quality assurance to predictive maintenance:
The WELDCUBE PREMIUM and CENTRAL USER MANAGEMENT software packages
“We've found the perfect partner in Fronius”, enthused Kurt Hartmann. “WeldCube Premium is an important pillar of our quality management system, as the complete traceability of every single weld is incredibly important to us.” Trained operators at the quality control stations are presented with the most accurate information on their terminals: Are there any dubious or real faulty welds? Locations picked out by Fronius WeldCube are subjected to a detailed visual inspection and reworked if necessary. Only then is the G frame released for the next stage in the process. The gathered data are then fed back to help optimize the automated welding processes.
WeldCube Premium charts every millimeter of the weld, making it a simple matter to analyze the cost of consumables such as gas and welding wire. Yet it has much more potential, for example Predictive Maintenance – the ability to order wearing parts and other materials in good time and in sufficient quantities.
“Predictive Maintenance with WeldCube Premium was able to uncover areas of potential savings, for example by having the welding management system specify precise maintenance intervals”, observed Hartmann. “We're always kept fully informed about the condition of contact tips, torch bodies, welding torches and wirefeeders, which means we know exactly when to service the equipment to avoid faulty welds, rework or the scrapping of components.”
Magna Presstec was already a user of the Fronius Central User Management (CENTRUM) system, which it uses in quality management. CENTRUM is where user and welding permissions are centrally managed. Welders use a smart card to identify themselves to the welding system, ensuring that only specially trained operators are allowed to work with the relevant parameters - another way of eliminating potential sources of error.
Magna Presstec has the proof: Welding data management works in the field
Christoph Pangerl, Fronius Key Account Manager for Magna, has no doubts: “The insights gained from the cooperation with Magna Presstec were extremely valuable, as we were able to feed them directly into our product development. It's also allowed us to make our software solutions accessible to a much broader customer base.” Kurt Hartmann continued the theme: “Welding data management in particular has helped us optimize our joining technology in every area. Fronius has given us a really powerful tool that has enormous potential. And with the technical support of Fronius specialists, we've meanwhile been able to deploy the system to improve our bottom line.“