TRUMPF steigert Effizienz mit neuer LaserHybrid-Schweißanlage
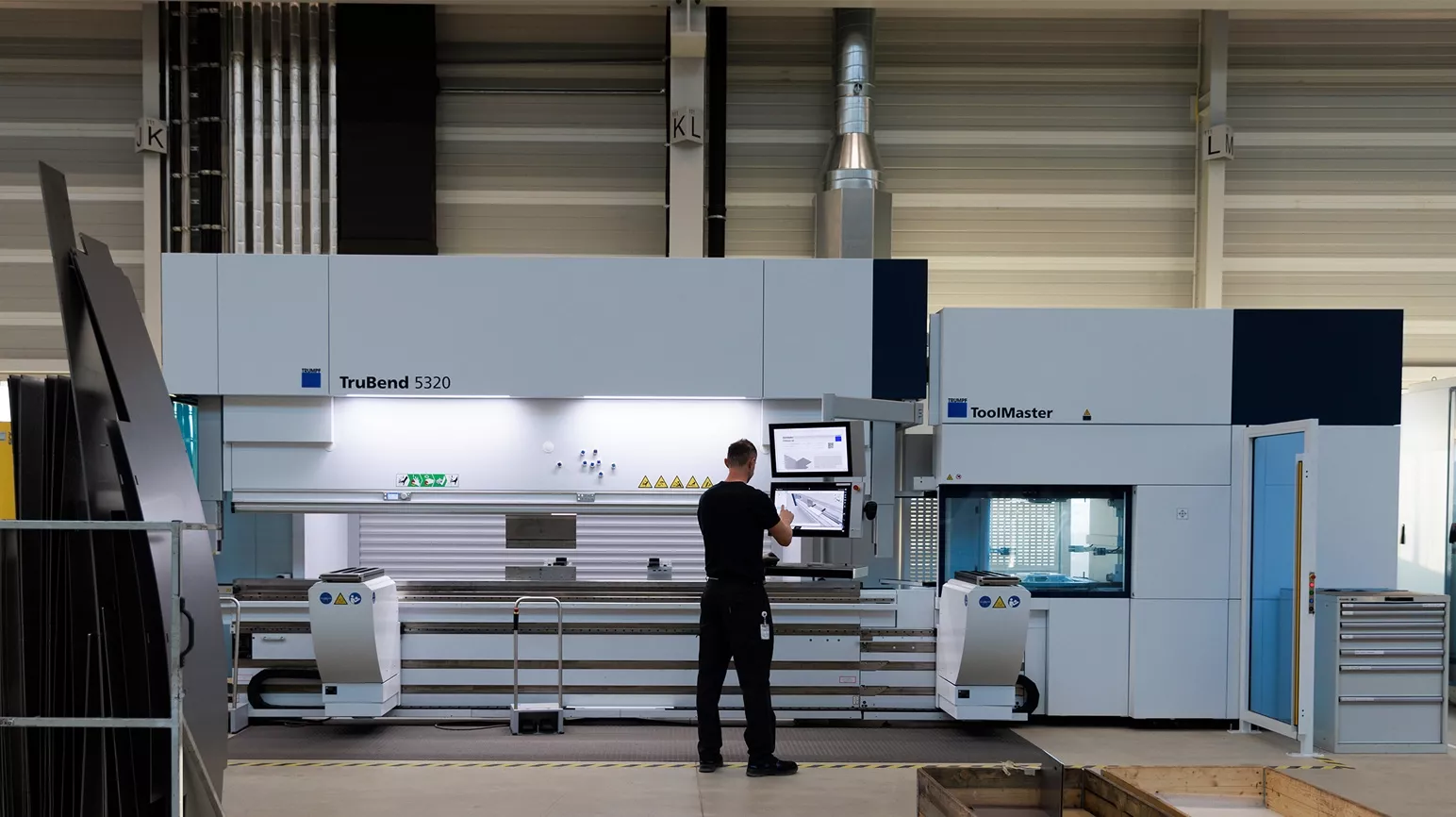
Dank LaserHybrid-Schweißsystem kosteneffizient selbst produzieren statt zukaufen
Trumpf verzeichnete in den letzten Jahren ein signifikantes Wachstum bei Biegemaschinen und erweiterte das Produktportfolio in diesem Sektor kontinuierlich. Die gestiegene Kapazitätsauslastung machte den Zukauf tonnenschwerer Rahmen für Biegemaschinen notwendig, was zu verlängerten Herstellungszeiten, höheren Kosten und eingeschränkter Flexibilität in der Fertigung führte. Geschweißt wurde beim Lieferanten manuell, verbunden mit aufwendiger Nacharbeit: Um im Anschluss an das Handschweißen unerwünschte Aufhärtungen im Stahl zu vermeiden, war ein energieintensiver Weichglühprozess notwendig.
„Beim Weichglühen wird der Stahl in einem Glühofen auf bis zu 800 °C erhitzt. Während des Aufheizens reagiert das Material mit dem Sauerstoff aus der Luft, oxidiert an der Oberfläche und bildet Rost. Deshalb müssen die Bauteile vor dem Lackieren sandgestrahlt werden“, erklärt Thomas Reiter, Fertigungsleiter bei Trumpf. „Dank unserer neuen LaserHybrid-Portalschweißanlage können wir auf den energieintensiven und kostspieligen Glühprozess verzichten. Mithilfe des Lasers erwärmen wir den Stahl entlang der Schweißnaht je nach Material auf 150 °C bis 180 °C und reduzieren dadurch die Abkühlgeschwindigkeit nach dem Schweißen. So vermeiden wir Aufhärtungen, Kaltrisse und Korrosion. Zudem sind wir durch die eigene Produktion unabhängiger und flexibler.“
Der Verzicht auf das Weichglühen erweist sich sowohl ökonomisch als auch ökologisch als vorteilhaft. Die Einsparung an Energie entspricht dem Strombedarf von ungefähr 270 Vierpersonenhaushalten pro Jahr, unter Berücksichtigung eines mittleren Verbrauchs von 3.800 kWh je Haushalt.
Optimale Flankenanbindung und reduzierte Porenbildungstendenz
Das LaserHybrid-Schweißverfahren kombiniert einen auf die Schweißnaht gerichteten Laserstrahl mit einem MSG-Schweißprozess in einer gemeinsamen Prozesszone. Der stark gebündelte Laserstrahl zeichnet sich durch seine extrem hohe Energiedichte aus und dringt beim Schweißen der Maschinenrahmen bis zu 10 mm tief in den Stahl ein. Unmittelbar nach dem Laser folgt der MAG-Prozess, der die Wurzel auffüllt und eine optimale Flankenanbindung gewährleistet. Die zusätzlich eingebrachte Wärme gibt dem Material Zeit zum Ausgasen und reduziert die Porenanfälligkeit im Vergleich zum reinen Laserschweißen. Abhängig von der Blechstärke werden bei Trumpf bis zu 29 Decklagen mit MAG aufgeschweißt.
Effizienzsteigerung und Materialeinsparung
LaserHybrid bietet Trumpf im Vergleich zum reinen MAG-Schweißen entscheidende Vorteile. Reiter erläutert: „Erstens sparen wir bis zu vier Tonnen Schweißdraht und wertvolle Arbeitszeit pro Jahr, da wir besonders bei dünneren Blechstärken auf das aufwendige Anfasen der Blechkanten verzichten können. Die Nahtquerschnitte bleiben dadurch klein und erfordern weniger Zusatzmaterial. Zweitens steigern wir unsere Produktivität dank hoher Schweißgeschwindigkeiten, ermöglicht durch den stabilisierten Lichtbogen, der aus dem Zusammenspiel von LaserHybrid und MAG entsteht. Und drittens reduziert die geringe Streckenenergie den Bauteilverzug.“
Ein vierter Punkt, der sich ebenfalls positiv auf den Verbrauch von Schweißzusatz auswirkt, kommt ebenfalls zum Tragen: Durch das LaserHybrid-Verfahren kann die Schweißnaht weiter nach innen verlegt werden. Dadurch kann beim Kehlnaht-Schweißen näher an die Seitenteile herangefahren und die Schweißfuge schmaler gehalten werden.
Evaluierung und Entscheidung für Fronius
Bevor sich Trumpf für das LaserHybrid-Roboterschweißsystem von Fronius entschied, wurden Konzepte verschiedener Anbieter evaluiert. Ziel war es, die technisch beste und wirtschaftlichste Lösung zu finden. Möglichkeiten, die bis zu 18 Tonnen schweren und 4,5 × 3 × 2 m großen Bauteile beim Schweißen zu umfahren oder sie auf Dreh-/Kipptischen zu positionieren, wurden schnell verworfen. Das von Beginn an favorisierte hauptzeitparallele Rüsten wäre bei diesen Varianten gar nicht oder nur eingeschränkt möglich gewesen.
Deshalb entschied man sich für eine Zwei-Stationen-Portalanlage mit je einem LaserHybrid- und einem MAG-Schweißroboter sowie zwei großen Kipp-Positionierern, die eine waagerechte Bauteilzuführung ermöglichen. Während ein Maschinenrahmen geschweißt wird, kann auf dem freien Positionierer der nächste aufgespannt werden.
„Dreh-/Kipptische würden nicht nur das hauptzeitparallele Rüsten beeinträchtigen. Es bestünde auch die Gefahr von zu hohen Kippmomenten, wenn die Schwerpunkte unserer tonnenschweren Bauteile zu weit von der Dreh- oder Kippachse entfernt lägen. Die Gefahr von Schäden an der Anlage und von Unfällen wäre dann überaus hoch“, erklärt Reiter. „Solche Probleme könnten wir nur durch riesige Dreh-/Kipptische vermeiden. Dann hätten wir aber ein Problem mit der Arbeitshöhe. Wegen der teilweise enorm großen Bauteile bräuchten wir entweder eine zweieinhalb Meter tiefe Grube oder eine Bearbeitungshöhe von mindestens zwei Metern.“
Alles in allem stellte sich die von Fronius vorgeschlagene Variante als die beste heraus. Ausschlaggebend waren mehrere Faktoren: ein vernünftiges Sicherheitskonzept, der Verzicht auf eine Brennerwechselstation durch den Einsatz von zwei Schweißrobotern, die problemlose Schlauchpaketführung, der Einsatz von WireSense für die Nahtsuche und die gute Zugänglichkeit des schlanken MAG-Roboters im Bereich der Ecken. Zudem gewährleistet das hauptzeitparallele Rüsten, ermöglicht durch die beiden Kipp-Positionierer, eine effiziente Produktion. Weitere Pluspunkte, die für Fronius sprachen, waren die langjährige, vertrauensvolle Geschäftsbeziehung, die Offline-Programmierung der Schweißjobs mit Pathfinder und die Kompetenz der Fronius Fachkräfte in der Anlagentechnik.
Kein Werkzeugwechsel erforderlich
Um einen Brennerwechsel und alle damit verbundenen Probleme bei der Schlauchpaketübergabe zu vermeiden, entschieden sich die Expertinnen und Experten von Fronius für eine Portalanlage mit zwei Schweißrobotern. Diese sind jeweils mit einem LaserHybrid- und einem MAG-Schweißkopf ausgestattet und bewegen sich überkopf auf einer Fahrschiene, wobei sie nie gleichzeitig in Betrieb sind. Zuerst übernimmt der LaserHybrid-Roboter das Wurzelschweißen. Anschließend werden die schwer zugänglichen Bereiche und die Decklagen mit dem MAG-Hohlwellenroboter geschweißt.
„Der MAG-Roboter garantiert mit seiner Hohlwelle eine optimale Schlauchpaketführung. Seitlich geführte Schlauchpakete schlenkern oft ungewollt. Sie können beschädigt oder im schlimmsten Fall sogar abgetrennt werden. Zudem besteht die Gefahr, dass solche Schlauchpakete an Bauteilen oder Vorrichtungen hängen bleiben, was die Bewegungsfreiheit von Robotern einschränken kann“, erörtert Reiter.
Anspruchsvoll: zwei Schweißroboter auf einer Fahrschiene
Der Einsatz von zwei Schweißrobotern auf derselben Fahrschiene stellt eine besondere Herausforderung dar. Die Lösung besteht darin, dass immer nur einer am Bauteil schweißt, während der andere in Parkposition bleibt. Für jeden Roboter wurde eine spezifische Programmvorlage erstellt, die sämtliche Bewegungen und Fahrten beinhaltet und als Grundlage für die Programmierung der bauteilspezifischen Schweißaufgaben dient.
Die von Trumpf für die Abnahmebauteile zur Verfügung gestellten Schweißfolgen wurden während der Konstruktionsphase mithilfe von Fronius Pathfinder am digitalen Zwilling simuliert und auf Machbarkeit überprüft. So konnten die Schweißfachkräfte des Auftraggebers schon im Vorfeld auf mögliche Produktionsschwierigkeiten – zum Beispiel Zugänglichkeitsprobleme – aufmerksam gemacht werden. Wolfgang Mitterhauser, Softwaretechniker und Simulationsexperte bei Fronius, setzte besondere Akzente:
„Ich habe den Postprozessor (Parser) erweitert, damit er für den MAG-Schweißroboter spezielle Befehle wie den Einsatz der WireSense-Nahtsuch-Sensorik übersetzen kann. Der Parser überträgt die erstellten Schweißprogramme vom digitalen Zwilling auf die echte Anlage. Die Erweiterungen beinhalten Programmabschnitte, die genau auf das System des Kunden zugeschnitten und in der Standardversion von Pathfinder nicht enthalten sind“, erklärt Mitterhauser.
Dank dieser Erweiterungen können die Anlagenbediener/-innen genau festlegen, welche Informationen in welchem Umfang vom Postprozessor übertragen werden. „Das Ergebnis ist ein Schweißprogramm, das exakt den Anforderungen des Roboters entspricht“, ergänzt Mitterhauser.
Damit ein möglicher Aufprall des Brenners am Bauteil frühzeitig erkannt wird, kann im Pathfinder ein Kollisionssensor angelegt werden. Erkennt das virtuelle Überwachungssystem einen potenziellen Zusammenstoß, wird dies von der Software sofort angezeigt.
Der Schweißdraht als Sensor
Selbst wenn alle Systemkomponenten nahezu perfekt ineinandergreifen, riskiert man ohne Nahtsuch-Sensorik Abweichungen beim Lagenschweißen. Das kann zu Bindefehlern wie Durchbrand oder unzureichenden A-Maßen führen. Fronius WireSense nutzt die Drahtelektrode als Sensor für die Schweißnahtsuche und verzichtet dabei auf optische Messhilfen, die die Bauteilzugänglichkeit des Brenners beeinträchtigen könnten. Durch punktgenaues Abtasten mittels hochfrequent reversierender Drahtbewegungen werden die verschiedenen Bauteilgeometrien erfasst und die Lage der einzelnen Bleche zueinander präzise bestimmt. WireSense kommt ohne zusätzliche Brenner-Anbauteile aus und benötigt weder Kalibrierungs- noch Wartungsarbeiten. Mithilfe dieser innovativen Sensorik profitiert Trumpf von fehlerfreien Schweißnähten und verringerten Produktionskosten.
Intelligente Steuerung aller Abläufe
Die benutzerfreundliche Systemsteuerung HMI-T21 RS ist das Herzstück der Schweißanlage. Sie überwacht und koordiniert alle Peripheriekomponenten wie Roboter, Schweißstromquelle, Kipp-Positionierer und Brennerreinigung. Dank der verfügbaren 3D-Echtzeitansichten können die Schweißfachkräfte von Trumpf sämtliche Roboterbewegungen live auf dem Monitor verfolgen. Dabei haben sie die Möglichkeit, zwischen voreingestellten oder selbst erstellten Ansichten zu wählen und diese zu speichern, um stets eine optimale Darstellung zu gewährleisten.
Ein wesentlicher Bestandteil der innovativen HMI-T21 RS ist ihr Programmeditor. Hier definieren Anlagenbediener/-innen die einzelnen Programmabläufe, weisen sie einer Bearbeitungsstation zu und speichern sie als Ablaufschrittkette ab.
In der Statusleiste werden Stör-, Warn- oder Info-Meldungen in Klartext angezeigt. Sind keine Meldungen vorhanden, werden sämtliche Anlagenzustände und der Programmablauf dargestellt, wobei man in der rechten Spalte den angemeldeten Benutzer sieht.
Mitterhauser: „Die Statusübersicht zeigt den Zustand aller vorhandenen Sensoren an. Kommt es zu einer Störmeldung, können sämtliche Signale mithilfe der HMI überprüft werden.“
Virtuelle Inbetriebnahme und Montage
Aufgrund der gewaltigen Dimensionen von Portal und Positionierer war die bei Fronius übliche Installation und Vorab-Inbetriebnahme des Schweißsystems am eigenen Standort nicht durchführbar. Stattdessen wurde auf eine virtuelle Inbetriebnahme mit Pathfinder zurückgegriffen. Mithilfe dieser Software entstand ein virtuelles Modell – inklusive aller im Schaltplan festgelegten Signale und realistischer Kinematik. Die digitale Nachbildung erlaubte den Softwaretechniker/-innen eine realitätsnahe Simulation des Anlagenbetriebs.
Auch bei der Vorab-Begutachtung durch den Kunden erwies sich Pathfinder als überaus nützlich. Sämtliche Bewegungsabläufe der beiden Schweißroboter und Kipp-Positionierer, die bis zu zehn verschiedene Bauteile aufnehmen können, konnten mithilfe einer Virtual-Reality-Brille realitätsnah erlebt werden.
Während der gesamten Designphase waren die zuständigen Mitarbeiter von Trumpf involviert und leisteten mit ihren Anregungen und Rückmeldungen einen wesentlichen Beitrag zum Erfolg des Projekts.
Die Montage der LaserHybrid-Schweißanlage am Einsatzort erwies sich als besonders anspruchsvoll. Die enormen Ausmaße des Portals und der bis zu 90° schwenkbaren Kipp-Positionierer stellten eine erhebliche logistische Herausforderung dar. Alle Komponenten mussten zur richtigen Zeit am richtigen Ort sein, um unnötige Verzögerungen zu vermeiden. Besonders herausfordernd war die nächtliche Lieferung der beiden Kipp-Positionierer, die aufgrund ihrer Größe teilweise über gesperrte Autobahnen transportiert werden mussten.
Effizienzsteigerung durch Machbarkeitsstudien mit Pathfinder
Die Maschinenbau-Expertinnen und -experten bei Trumpf nutzen die Software nicht nur zum Programmieren und Simulieren neuer Schweißjobs. Neue Bauteile werden virtuell auf ihre Schweißbarkeit hin überprüft: Inwieweit eignet sich die Bauteilgeometrie für automatisiertes Schweißen? Ist die Bauteilzugänglichkeit zufriedenstellend? Besteht die Gefahr von Kollisionen? Müssen Teile manuell geschweißt werden oder ist sogar die Konstruktion zu ändern? Solche umfassenden Machbarkeitsprüfungen und Ablaufsimulationen ersparen Trumpf nun bis zu drei Wochen an Programmierzeit.
Fazit: Richtige Entscheidung
Die neue Fronius LaserHybrid-Schweißanlage verbessert die Schweißnahtqualität der Maschinenrahmen erheblich, steigert die Schweißgeschwindigkeit und spart durch die Möglichkeit der Offline-Programmierung und Simulation wertvolle Arbeitszeit.
Thomas Reiter zeigt sich zufrieden: „Wir produzieren mittlerweile knapp 1.500 Biegemaschinen pro Jahr. Dank unseres neuen Roboterschweißsystems sind wir nicht nur wirtschaftlicher, sondern auch deutlich flexibler in Bezug auf die Lieferzeiten, da wir ab sofort nicht mehr auf den Zukauf von Maschinenrahmen-Komponenten angewiesen sind. Auch hinsichtlich der Produktionskapazität haben wir jetzt mehr Möglichkeiten.“