Power supplies: the hidden heroes of the modern world
By Steve Zatezalo
Almost everything electrical in our lives depends on a device to convert standard electrical power into specialized energy the device can use safely. When we added computers to these power supplies, the entire world changed. In the welding world, synergic welding was born and, to this day, continues to revolutionize the way we weld.
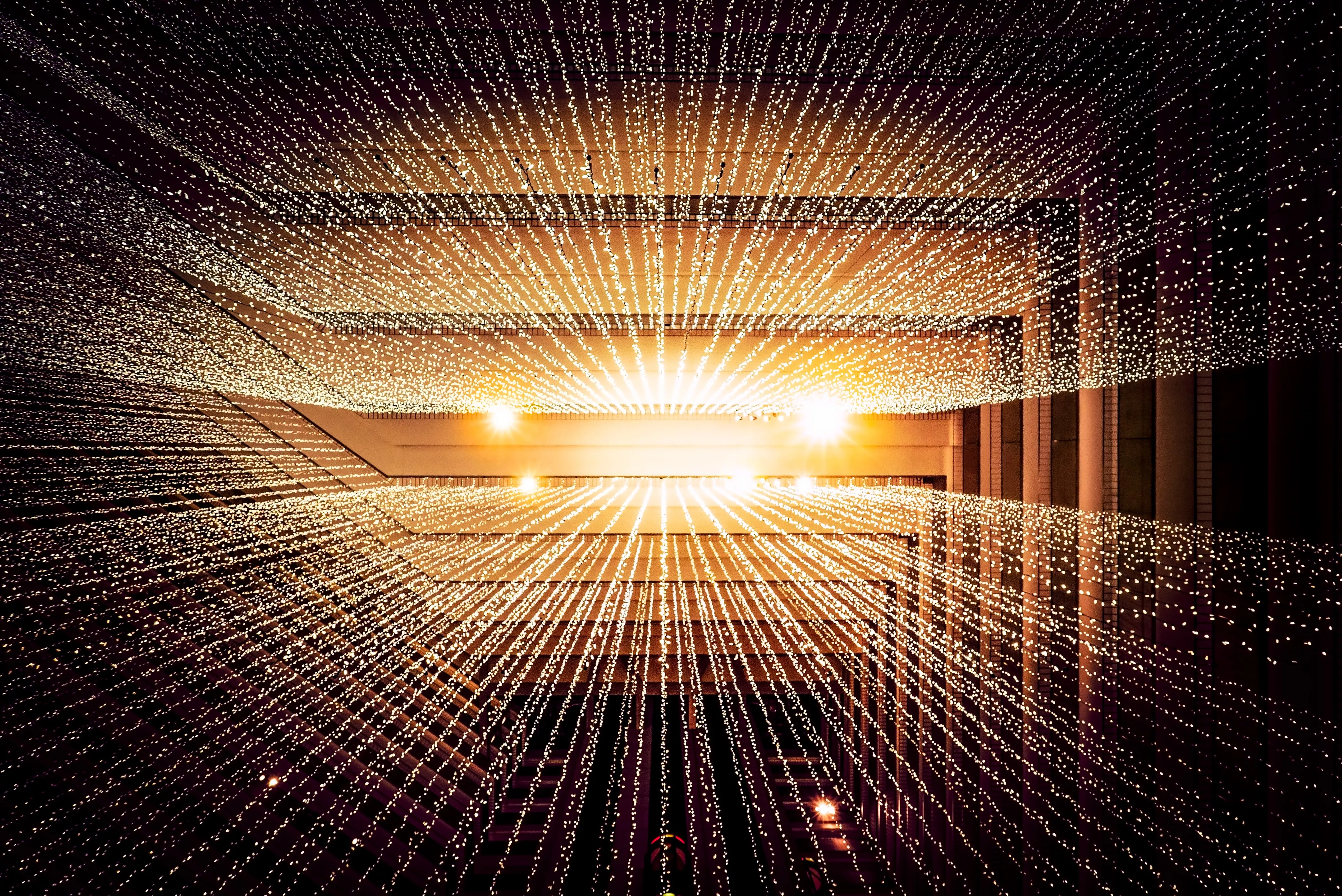
But what exactly is synergic welding?
At its simplest, synergic welding uses high-speed electronics and computer software to control the welding arc precisely through electrical feedback. Practically, the welding power supply changes the internal arc settings to ensure that the arc is more stable, accurate and uses only the energy needed to perform the job. It almost sounds like the welding professional is no longer needed, but nothing could be further from the truth. In actuality, the welding power supply watches the arc through electronic sensors. It only makes changes when the sensors detect a need to do so. The experience and capability of the person holding the welding torch (or dialing in a robotic weld) will reduce the changes so that the only thing the power supply worries about are environmental factors that are often beyond the welder’s control. Like a high-end race car, the final performance is as dependent on the driver as on the equipment being used. If your goal is to achieve the highest quality, most profit-making welds, then you want to ensure you have top welders using top equipment.
One of the most common questions concerning the quality of the synergic power supply: is one better than another? The simple answer: absolutely. Three things can help determine this: Component Quality, Processor/Bus Speed, and Software.
Unfortunately, rating these components often requires a high level of technical skill or deep access to the architecture. Lucky for us, there is an easier way, weld with it and see how it performs for yourself.
A machine that excels in all three of these traits will be
easy to set up and almost immediately demonstrate a smooth arc and high-quality
finish. A couple of good examples are the Fronius TPS/i or the Fronius
TransSteel. But the real test comes when the arc is tried under less than
ideal conditions. In this case, you will
see the arc trying to maintain stability and establish a quality bead to the
limits of physics.
Now, suppose you’re using a machine with cheap electronics, a slow processor, or poor software. In that case, you will immediately see the difference. Too often, poor welding is blamed on the welders performing the job when the actual culprit is the equipment that’s being used.
Intelligent welding?
Synergic welding has opened yet another door in recent years, the idea of Intelligent Welding. The Fronius TPSi’s Pulse Multi Control (PMC) and Low Spatter Control (LSC) are two excellent examples of this sort of technology.
Standard pulse and CV waveforms are concerned with the stability and quality of the arc. PMC and LSC take this computer control to the next level and interpret the electronic feedback to go beyond just the stability of the arc. Stabilizers are introduced to the process. They look at the electrical pattern of the weld and actively modify the arc to ensure characteristics such as penetration and arc length are as consistent as possible through the length of the entire weld.
Ease of use is another advantage that synergic welding brings to welding. Many of us have lived and died based on a painted mark on the dial of the welding machine. That mark represented the ‘ideal’ settings that have worked for the job we need to get done. But when the job changes or the material isn’t quite right, we struggle to get the arc just right.
Synergic welding has computerized these paint marks giving you a starting point by simply selecting the material, gas, wire, and dialing in the thickness of your plate. From here, you have a starting point that allows you to dial in a stable arc and are producing a good bead in seconds. When the job changes, you dial in the new starting point and are back to work delivering both quality and quantity. Such simple use speaks to a confident set-up by both experienced and inexperienced welders, because let's face it, if the technology presented to you requires an advanced degree to use, why would you want to use it?
Synergic welding is finally becoming a standard part of the welding language.
More and more welder supply companies are starting to present their version of this solution.
At Fronius, we jumped into the technology well over 20 years ago. We’ve used that time to master it and deliver a series of products that make this not only powerful to the industry but approachable and easy to use for anyone that chooses to pick up the torch. All of our welding platforms, TPSi, TransSteel, TransPocket, AccuPocket, and MagicWave, have this synergic technology at the core. We set the standard that others strive to achieve.
But don’t just believe it, give us a call and try for yourself.