COMMON CHALLENGES
OF WELDING HEAVY COMPONENTS
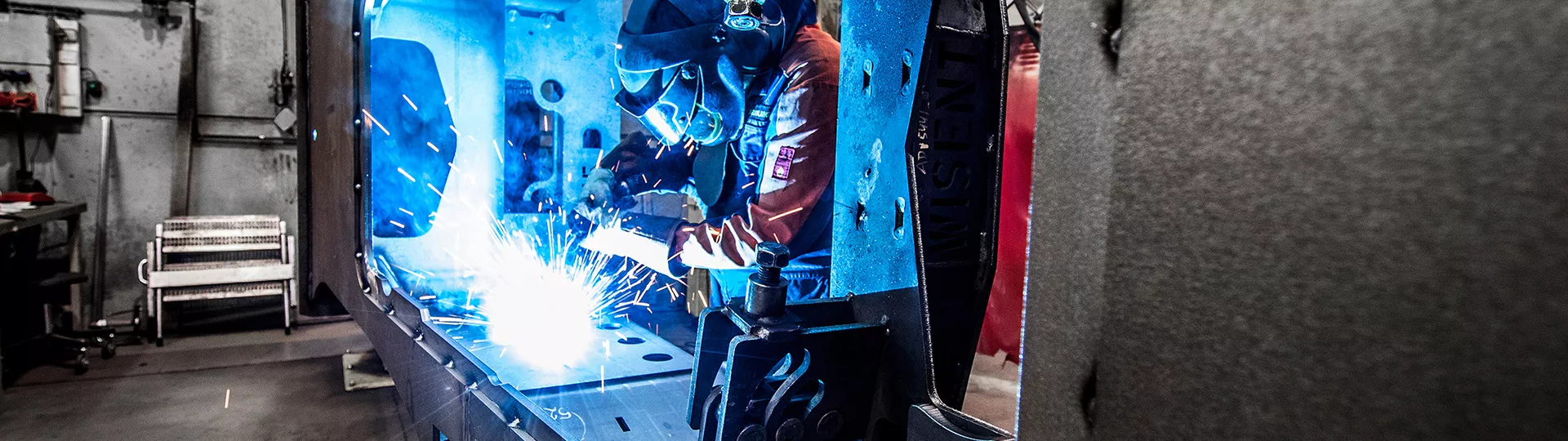
Manufacturing heavy-duty machinery components come with a unique set of welding challenges, such as long seam lengths, joint inconsistencies, multiple weld layers, and thick base materials. Other factors to consider are welder skill level, torch angles, transfer modes, material contamination, and other overlooked elements. You also want to avoid safety issues, welder fatigue and minimize rework that can quickly become expensive and detrimental to your profit.
Welding challenges
Welders are an essential part of any manufacturing operation and yet, one of the most overlooked. Challenges that are faced every day include keeping long weld seams consistent while facing welder fatigue. Any resulting inconsistencies may require rework. It’s a domino effect, costing time and money.
A simple solution is to provide them with a lightweight torch, but some seams are too long to be completed without stops and restarts. Specific best practices can make these weld starts and stops blend effortlessly.
In addition, varied material thicknesses, from thick to thin, provide a set of challenges that may involve pre-heat, multiple weld passes, or consideration of the best mode of transfer for the application.
HOW DO YOU ACHIEVE ALL THIS?
Our application engineers gathered their expertise to offer you practical and applicable solutions for these and other challenges:
- Download the technical article on how to tackle the challenges
- Calculate how much rework is costing your operation with our cost saving calculator
- Attend the webinar with welding demonstrations on achieving the best weld results
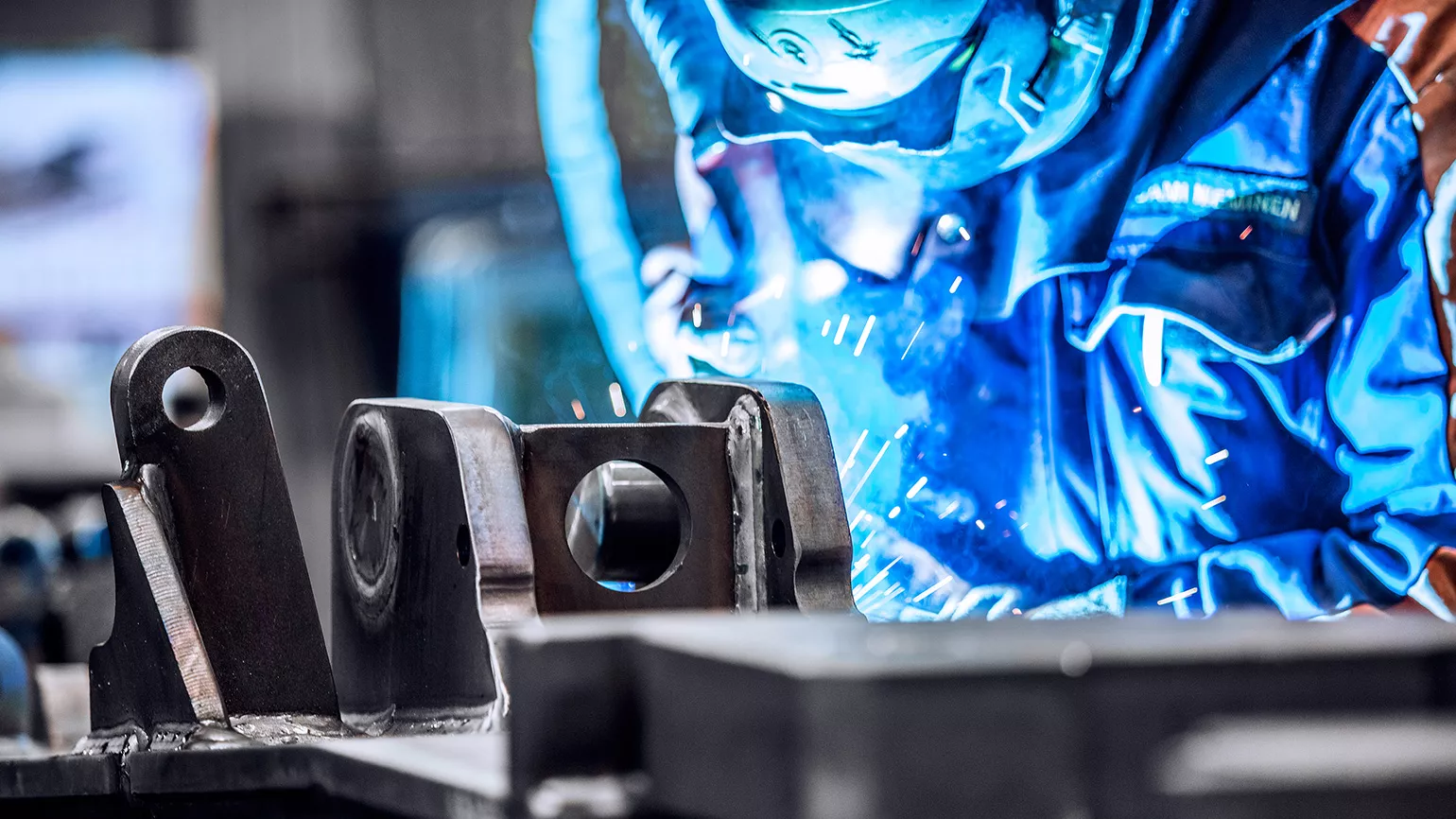
DO YOU KNOW YOUR POTENTIAL SAVINGS?
OUR COST SAVINGS CALCULATOR HELPS YOU TO SEE HOW ADJUSTMENTS TO REWORK AFFECTS PRODUCTION
Just enter your basic production data, adjust the sliders to reflect rework information and make adjustments for production increases.
If you like the information from the calculator, just get in touch with your Fronius expert. We’ll help you find your potential and improve your welding production sustainably.
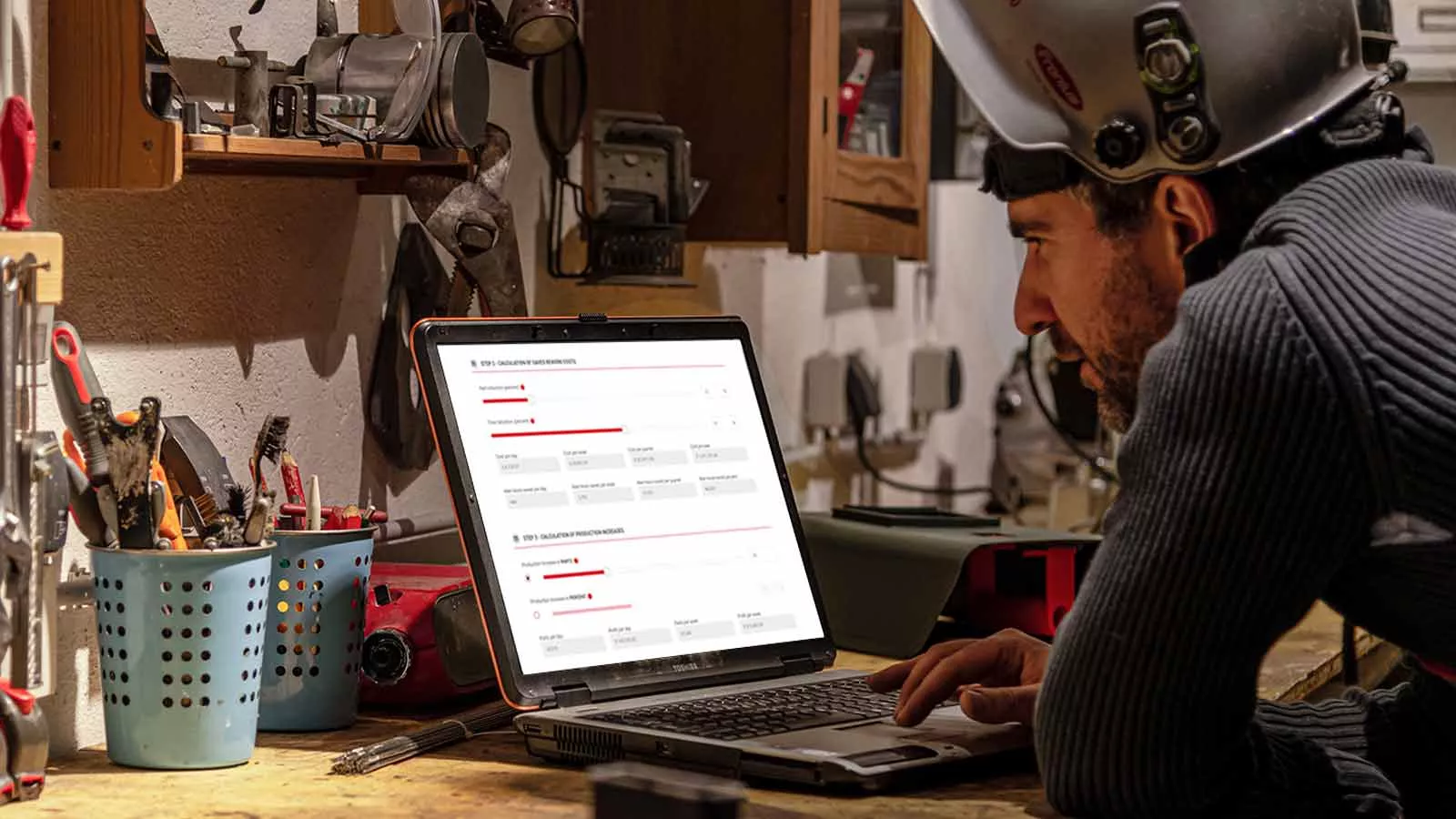
Webinars to achieve the best weld results
Some practices are used
every day in the welding industry; find out which are best practices and why
they are the right choice.
Attend the webinar with
welding demonstrations on achieving the best weld results, with live Q&A.
Explore our product solutions
Contact
What's your welding challenge in manufacturing heavy-duty machinery components?
Contact us for a free consultation.