CMT turns 20:
Unrivaled precision and stability
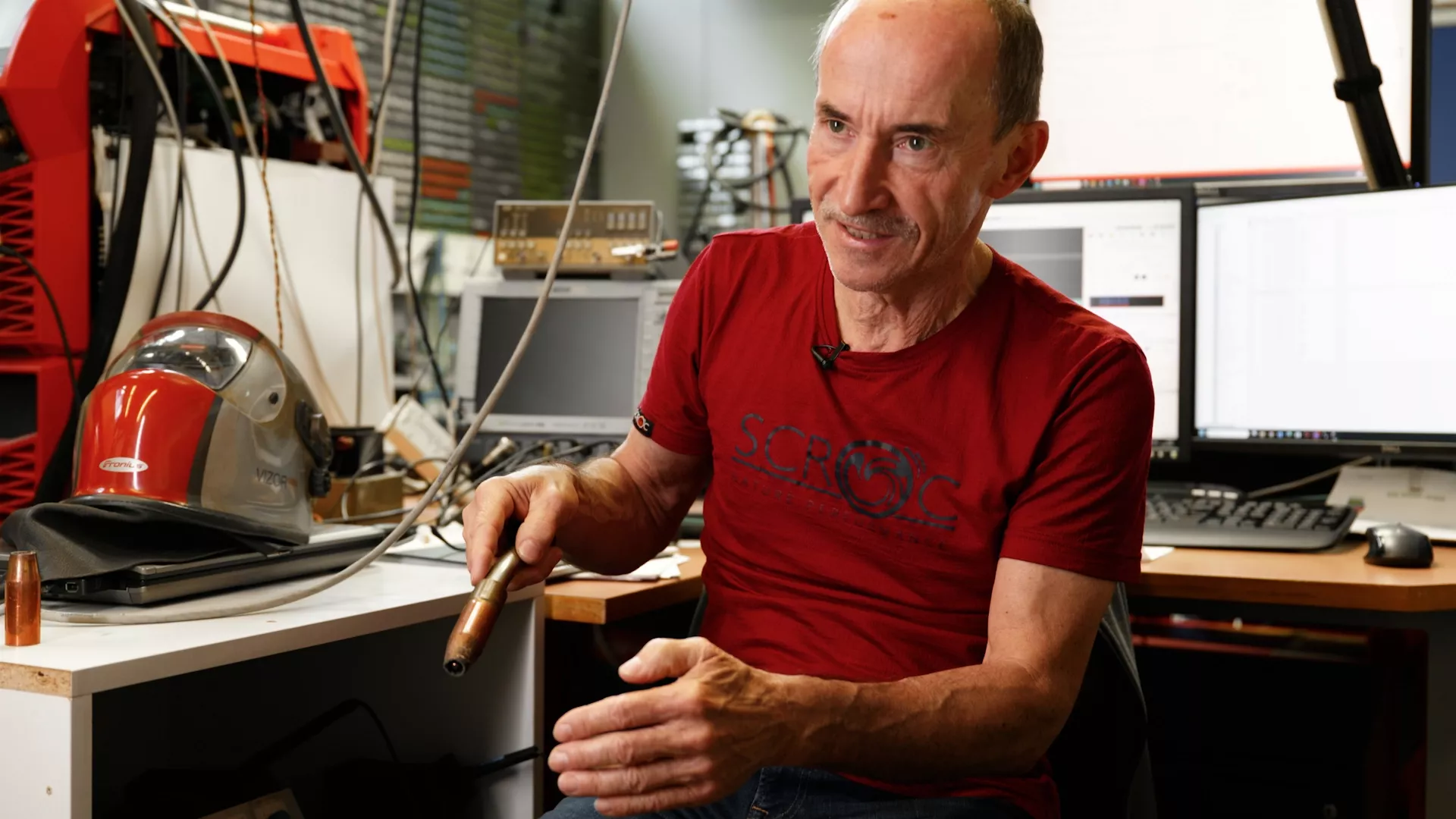
Wherever adhesive or solder had to be used before, CMT now makes welding an option as well—and with virtually no spatter. But that wasn’t the only breakthrough: For the first time in the history of welding, it was now possible to thermally join galvanized steel and aluminum.
It all started with a light bulb
The unique properties mentioned above make the CMT process suitable for almost any application. “Even we would never have expected that,” says Josef “Joe” Artelsmair, still somewhat amazed. After all, he and his colleagues were only supposed to find a solution for the light bulb manufacturer Osram.
In countries with elevated levels of salt in the air, the sockets and contacts of the bulbs would become heavily corroded. In order to make the bulbs more durable in these regions, the idea was to replace the sockets with a different material and use welding rather than soft solder as the joining method. It was a simple idea, but one that wouldn’t work in practice because the welding processes were far too hot—the sockets would always explode.

Gearless motor leads to breakthrough
The idea of repeated, controlled droplet detachment which could possibly even be used to produce continuous weld seams never left Joe Artelsmair’s mind. When the project was taken up again with a larger team some time after the order from Osram, they actually succeeded: A gearless motor made a completely new type of welding possible. “We were overwhelmed by the results,” reports Artelsmair, visibly proud. He and his team can be very proud, because the virtually spatter-free, clean welds speak for themselves in terms of both quality and aesthetics.
Another advantage of the CMT process is the low thermal load on the workpiece. This reduces distortion and deformation, which is an enormous advantage especially when working with sheets as thin as 0.3 millimeters and temperature-sensitive materials. The precise control of the welding process helps to master demanding welding tasks with maximum accuracy.
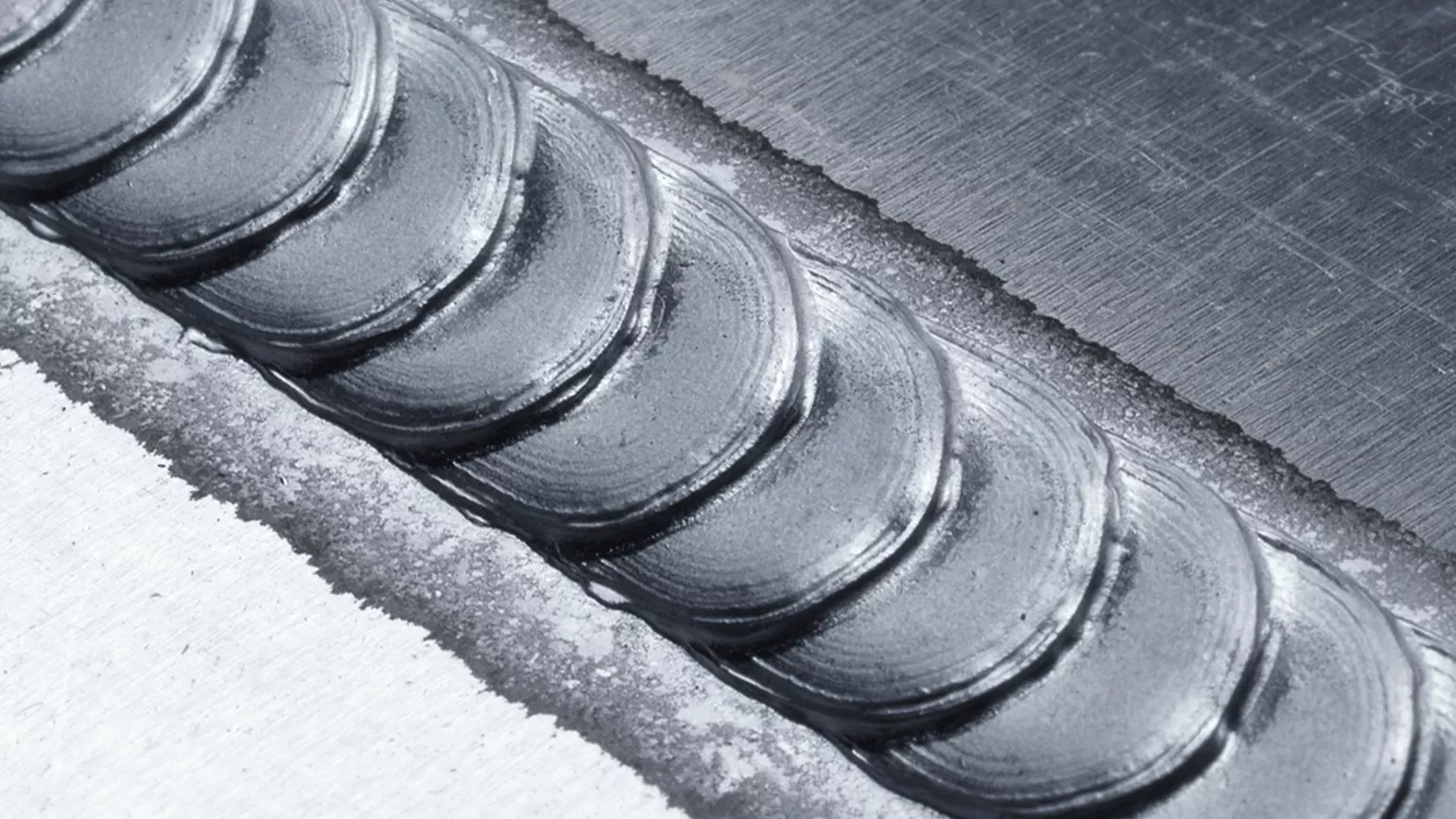
Variety of applications in different industries
“Over the last two decades, CMT has established itself as a versatile welding process that is used in numerous industries. The versatility and creativity with which our customers use CMT to their advantage and to solve their welding challenges sometimes impresses even us,” reports Franziska Eichhorn, Strategic Product Manager, Fronius International. The automotive industry, for example, uses CMT to join thin sheets and lightweight materials such as aluminum, ensuring strong and reliable connections for vehicle frames and components.
CMT has also proven its worth in the aerospace industry, as it enables the welding of high-strength and lightweight materials that are essential for the construction of aircraft and spacecraft. Due to its outstanding stability, the innovative welding process is also used in metal 3D printing or in the electronics industry, where it is used for precision brazing of components.
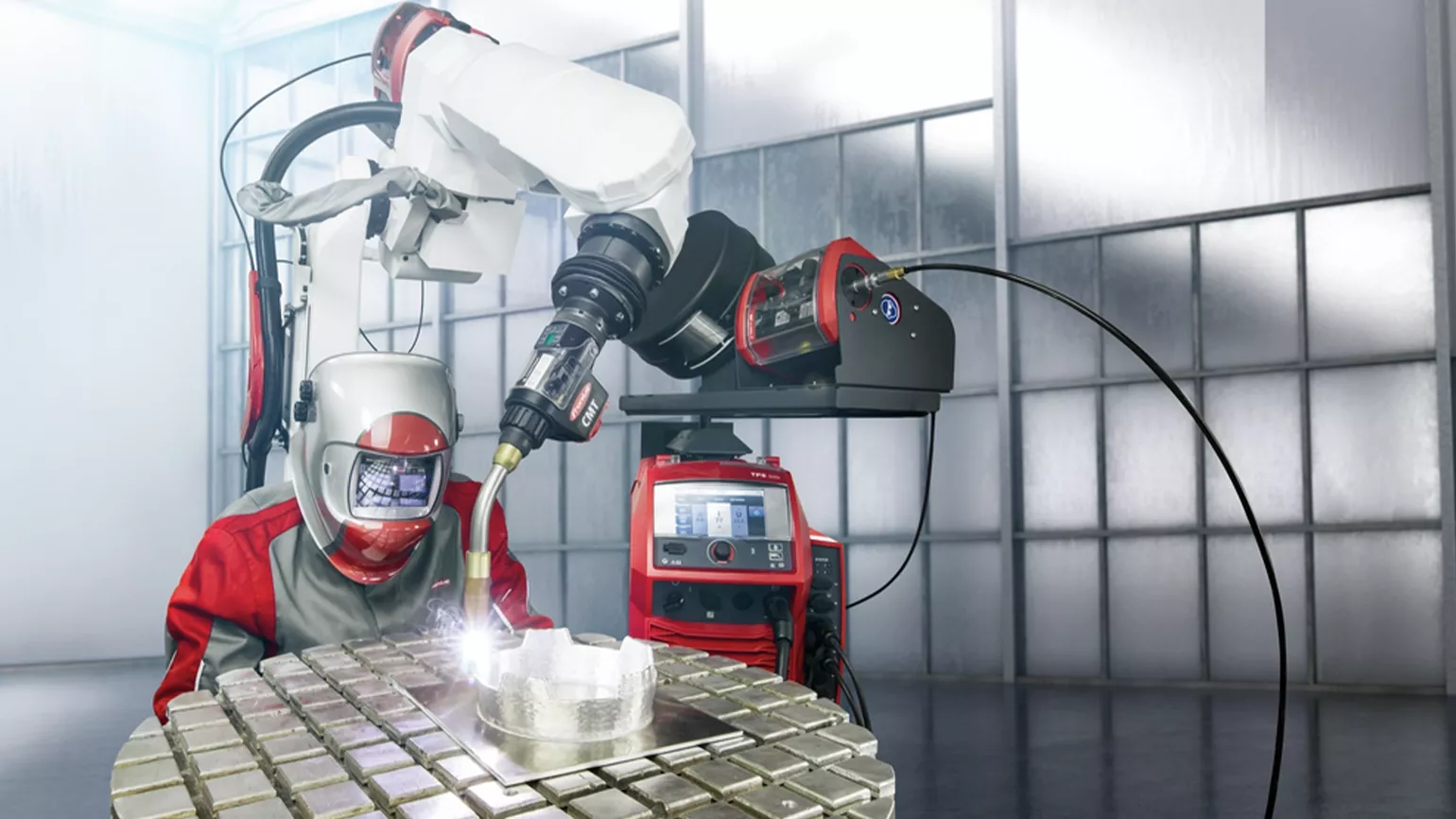
Intelligent gap and edge detection thanks to CMT
CMT's back-and-forth wire movement has also revolutionized robotic welding with the WireSense intelligent assistance system. This significantly improves seam quality and efficiency by detecting inaccuracies and deviations in industrial production and bridging them using the CMT welding process. The welding wire serves as a precise sensor that determines the exact position of the weld and adjusts it dynamically. This saves material, time, and costs, as rework and rejects are reduced.
“The decisive factor is the perfect interaction of the components and the precision with which they are controlled,” emphasizes Eichhorn. “The harmony with which our intelligent welding machines and the Robacta Drive CMT drive unit, i.e. the second wirefeeder directly on the welding torch, work together is still unrivaled today and is constantly being further developed to meet the increasing demands of the industry. And the very best thing about it: CMT can be easily retrofitted to all intelligent Fronius welding machines.”
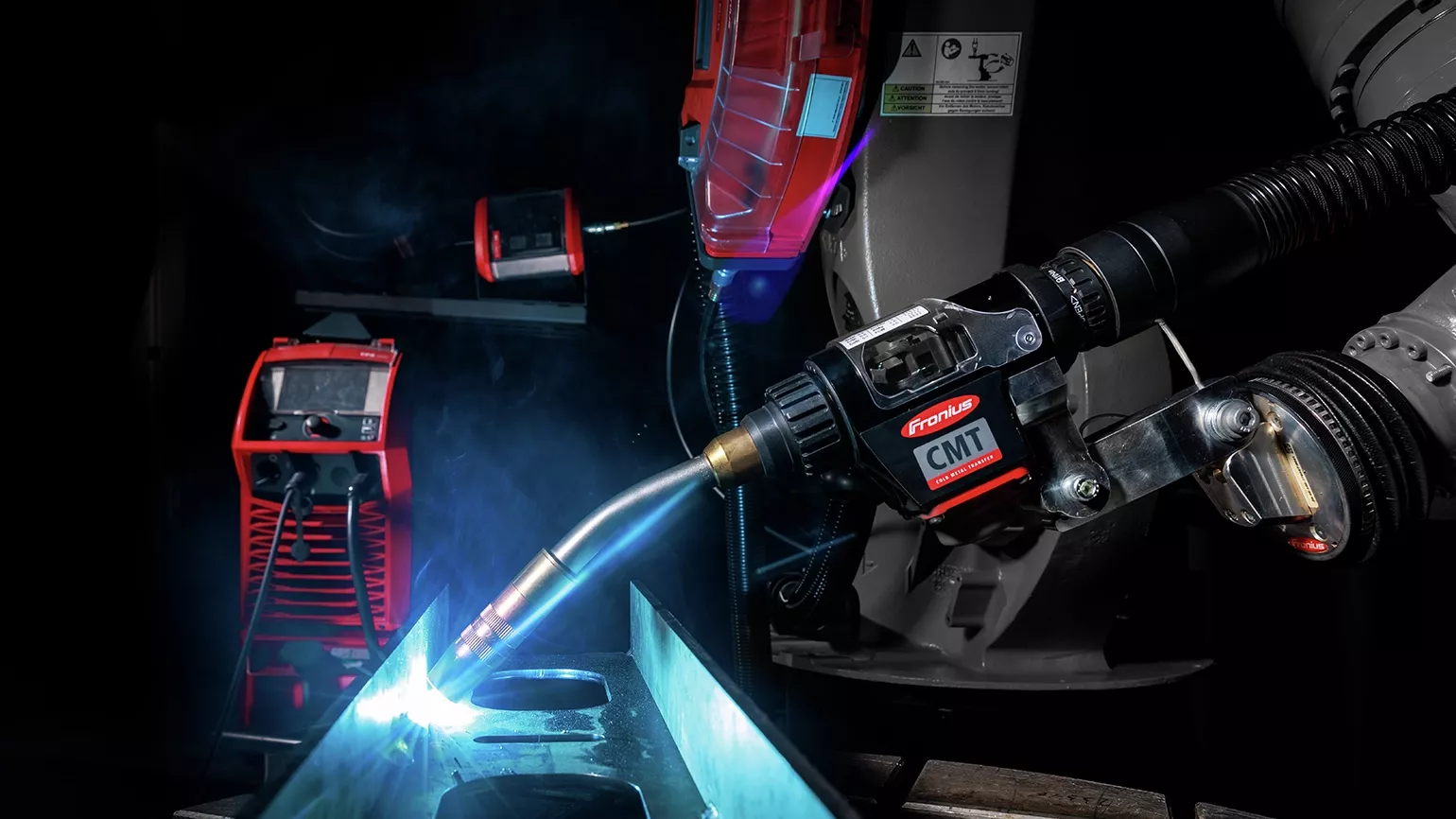
Fit for the future
Over the years, the innovation leader has continued to perfect CMT and develop application-specific, optimized welding characteristics such as CMT Mix, CMT Cycle Step, CMT Cladding, and CMT Braze. LaserHybrid CMT, on the other hand, combines the advantages of laser welding with CMT technology. This combination is particularly impressive for high-strength steels and aluminum components thanks to its high speed, quality, and cost effectiveness. A highly focused laser beam that penetrates the base material with high energy density is immediately followed by the CMT process, which increases the seam volume and reduces the heat input even further.
Fronius refuses to rest on its laurels as an innovation leader in joining technology: The latest achievement is the CMT Additive Pro characteristic curves optimized for metal 3D printing. They take additive manufacturing to a new level.
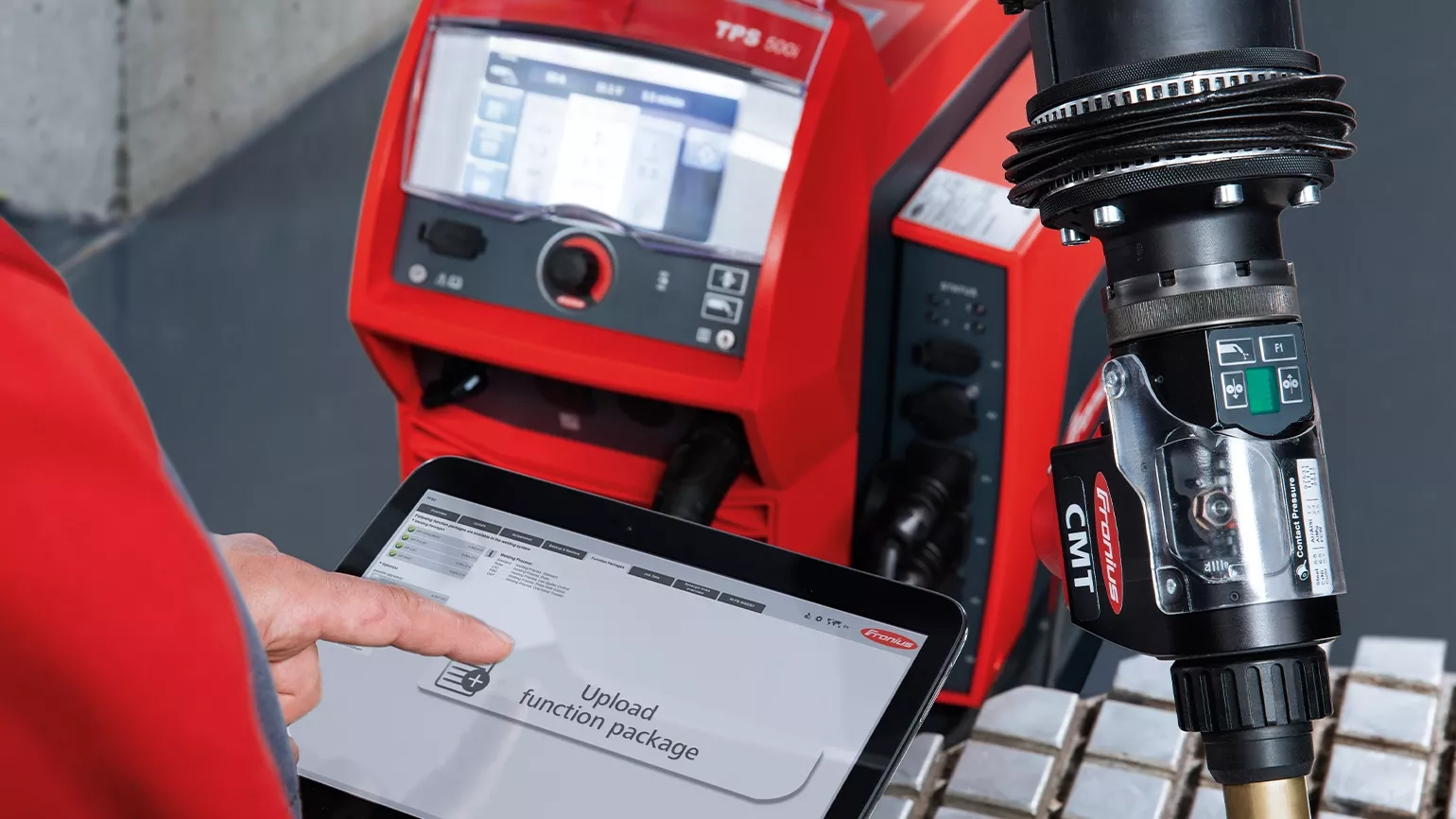
The secret of success? Passion!
We can’t wait to welcome you there and look forward to your visit!