O futuro automotivo com a Magna Presstec
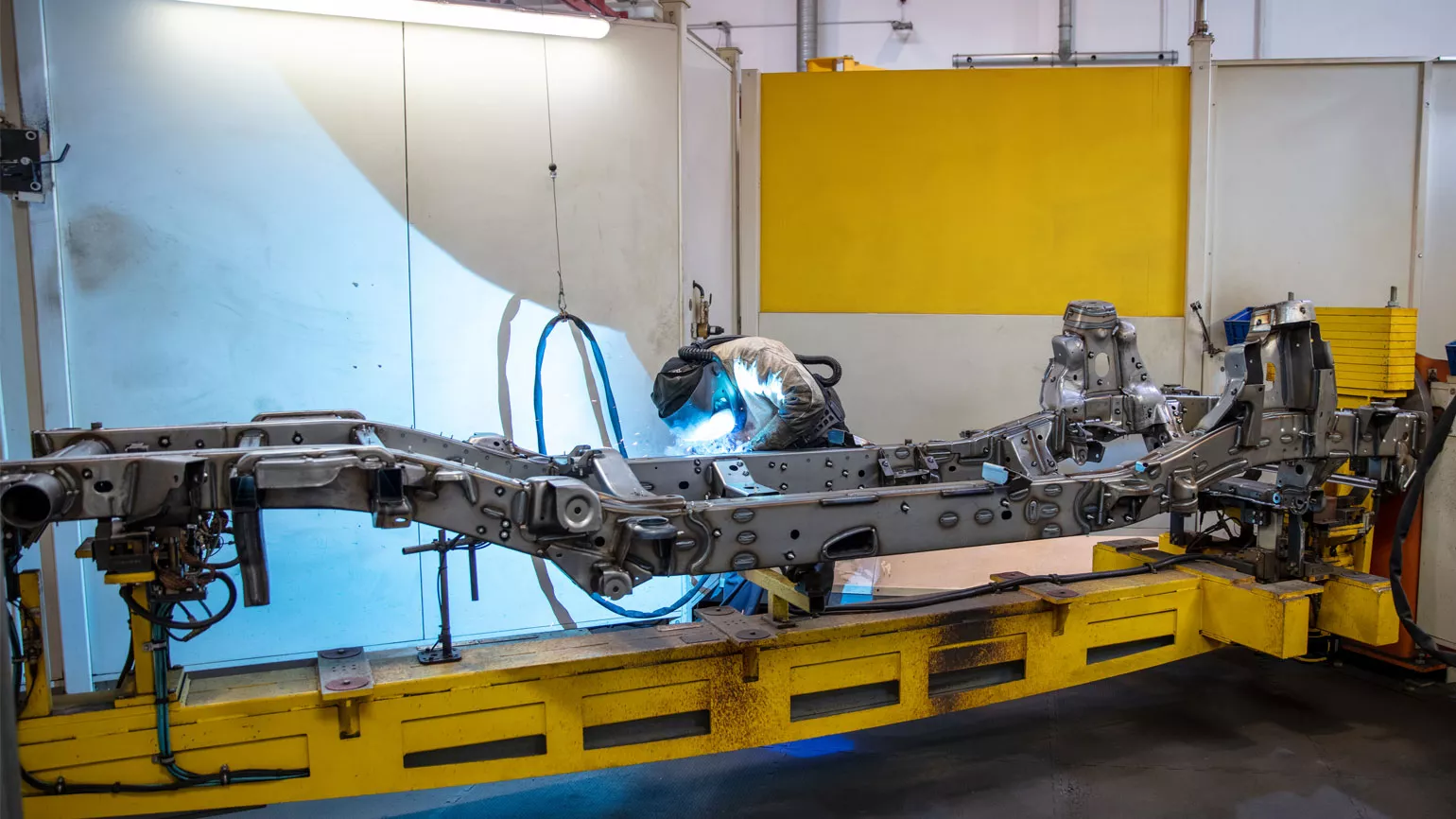
A fornecedora automobilística Magna criou uma ótima infraestrutura de produção perto de Graz: Magna Presstec GmbH em Lebring, a meia hora de carro a sudeste de Graz; fabrica a base do modelo G. A Magna Steyr Fahrzeugtechnik AG & Co KG em Graz, em seguida, faz a finalização do veículo offroad premium.
Base para a classe automobilística superior
„Dentro do Grupo Magna, com seus aproximadamente 158.000 funcionários espalhados ao redor do mundo, a Magna Presstec faz parte do grupo de empresas COSMA (Body and Chassis)“, explica Kurt Hartmann, chefe de qualidade e supervisão de soldagem para a produção de estruturas da linha G da Mercedes. A própria Presstec emprega cerca de 1.200 pessoas, divididas entre as unidades austríacas em Weiz e Lebring e a unidade eslovaca em Bratislava.
O fornecedor automotivo produz componentes de chassis e peças estruturais de alumínio e aço de alta qualidade. „Nossos clientes incluem a VW, Audi, BMW, Daimler e Porsche. Fabricamos com sucesso o futuro automobilístico, com paixão e com responsabilidade pessoal“, conclui Hartmann.
Os veículos offroad de alta tecnologia exigem a mais alta qualidade de costura de solda
O Mercedes G é considerado um dos veículos mais aptos para o offroad do mundo, e também o mais adequado para o uso diário. Sua considerável distância do solo e o ângulo de subida já dão uma ideia disso: o veículo é projetado para suportar as mais adversas condições de offroad.
A força de tração e a durabilidade devem ser garantidas quando o G for submetido a impactos violentos em altas velocidades em terrenos acidentados. Como, por exemplo, em testes contínuos de longo prazo no terreno íngreme do Schöckl, perto de Graz. Os veículos são colocados à prova em um percurso espetacular nas montanhas. Isto deixa claro que até a fabricação do quadro da Classe G merece total atenção. É desnecessário dizer que as mais altas exigências também são colocadas na qualidade das costuras de solda.
Requisitos da Mercedes G para a tecnologia de soldagem
„O aço utilizado é predominantemente uma chapa com uma espessura de 2-4 milímetros, a qual é unida por meio de 657 costuras de solda. O comprimento total das costuras de solda é de 76 metros por quadro. Para nós, o desafio da soldagem é essencialmente construir o chassi de 4,2 metros de comprimento camada por camada, sempre dentro das tolerâncias especificadas pelo cliente, bem como a qualidade superior que nos exigimos“, esclarece Kurt Hartmann.
Por este motivo, existem diferentes requisitos para a tecnologia de junção ao equipar a instalação de produção: era necessária uma alta estabilidade do arco voltaico com penetração de solda perfeita para poder gerar a estabilidade urgentemente necessária da estrutura sólida. Uma melhor qualidade também exige o menor nível de deformação possível e aplicação de calor controlável. Em termos de produtividade, ainda eram necessárias altas velocidades de soldagem.
„O processo PMC (Pulse Multi Control) da Fronius foi capaz de atender perfeitamente as nossas exigências“, assegura Hartmann, ele mesmo, um especialista internacional em soldagem. „A plataforma modular do dispositivo de solda TPS 500i foi um pré-requisito para isto. A operação simples e a conexão sem problemas com o robô completaram o nosso pacote. Atualmente temos 36 desses sistemas de soldagem em uso na linha Mercedes G. Além disso, temos também alguns sistemas TPS 320i para qualquer trabalho de soldagem manual para o controle de qualidade“.
Produção autônoma de picos em detalhe
„Nossa afirmação é que cada quadro é absolutamente o mesmo, os desvios devem ser excluídos“, explica Hartmann. A produção ocorre em um salão de fábrica bem equipado com mais de 100 metros de comprimento. A produção em grande parte autônoma atende aos mais altos padrões e os sistemas de robôs perfeitamente coordenados se conectam sem problemas. Isto possibilita que um quadro G robusto, perfeitamente montado a partir de muitas peças individuais, saia do salão da fábrica a cada 10 minutos.
A produção ocorre em três etapas: a estrutura dianteira e a traseira são produzidas simultaneamente. No início, alguns funcionários equipam os equipamentos de solda. Os componentes são então unidos nas células por robôs de solda. Um robô de manipulação pega os componentes acabados, transporta-os para a próxima célula e os posiciona lá. No final de cada seção há uma célula inacessível para os funcionários. Por um lado, isto serve para soldar as costuras longas. Mas também é utilizada como estação de resfriamento ou como estação complexa, como para apertar: aqui as chapas inferiores são aninhadas com as chapas superiores das vigas longitudinais, posicionadas e soldadas sob pressão.
Por fim, ocorre, na subestrutura, a última etapa da produção: as estruturas dianteira e traseira são unidas. O quadro agora assume sua forma distinta. As etapas finais de trabalho envolvem então a perfuração de pontos de conexão desacoplados para o mecanismo de traslado. Além disso, uma ignição recíproca dispara 192 parafusos sobre a estrutura. Finalmente, a qualidade dos cordões de solda é verificada, qualquer respingo de solda é removido e, se necessário, os cordões de solda são retrabalhados. Finalmente, a tecnologia laser controlada por robô mede a estrutura novamente com muita precisão e verifica se ela atende a todos os critérios de qualidade.
Gerenciamento de dados de soldagem altamente profissional
O procedimento extremamente complexo comprova: a Magna Presstec é mais do que apenas soldagem. A fim de poder garantir o alto grau de automação com qualidade igualmente alta para a linha G, o foco foi a integração desde o início de ferramentas de monitoramento e análise de dados para processos de soldagem. O fornecedor automobilístico estava procurando uma cooperação com especialistas em tecnologia de junção, cujos sistemas e soluções pudessem possibilitar rastreabilidade cem por cento digital nos processos de soldagem:
com a solução de software WeldCube Premium, a Fronius conseguiu pela primeira vez estabelecer um sistema abrangente de gerenciamento de dados de soldagem na produção de um fornecedor Tier1 e demonstrar os benefícios dos vários sistemas de software em uso.
Da garantia de qualidade à manutenção preventiva: As soluções de software WELDCUBE PREMIUM e CENTRAL USER MANAGEMENT
„Na Fronius encontramos um parceiro perfeito“, enfatiza Kurt Hartmann. „WeldCube Premium é um pilar essencial de nossa gestão de qualidade. A rastreabilidade absoluta de cada costura de solda é extremamente importante para nós“. Nas estações de controle de qualidade, os funcionários treinados recebem informações precisas via terminal: existem costuras visíveis ou realmente defeituosas? As áreas sondadas com a Fronius WeldCub são submetidas a uma inspeção visual detalhada e, se necessário, são retrabalhadas. Somente então o quadro G é liberado para outras etapas do processo. Os dados coletados são, dessa forma, utilizados para a otimização dos processos automatizados de soldagem.
O WeldCube Premium registra cada milímetro de solda. Isto facilita a análise dos custos de consumíveis, como gás e arame de soldagem. Mas há claramente mais potencial: um ponto é a Predictive Maintenance (Manutenção preventiva), ou seja, a capacidade de encomendar peças e materiais de desgaste em tempo hábil e em quantidades suficientes.
„A manutenção preventiva usando WeldCube Premium pode nos mostrar economias potenciais, por exemplo, se o gerenciamento de dados de soldagem especificar intervalos de manutenção precisos“, menciona Hartmann. „Nós sempre saberemos exatamente sobre as condições dos tubos de contato, corpo da tocha de solda, tochas de solda e alimentadores. Isto nos permitiria fazer a manutenção do equipamento a tempo de evitar soldas defeituosas, retrabalho ou até mesmo descarte de componentes“.
A Magna Presstec também já está usando a solução Fronius Central User Management (CENTRUM), esta também fornece apoio na gestão da qualidade. Assim, as autorizações de usuário e de soldagem são administradas centralmente. O soldador se autentica na máquina de soldagem com um cartão com chip, isto assegura que somente funcionários treinados específicos possam trabalhar com os parâmetros pretendidos, o que elimina fontes de erro da melhor maneira possível.
Magna Presstec comprova: o gerenciamento de dados de soldagem é prático
Christoph Pangerl, Fronius Key Account Manager responsável pela Magna, tem certeza: „O conhecimento adquirido com a cooperação com a Magna Presstec foi extremamente valioso. Conseguimos incorporá-los diretamente ao desenvolvimento de nossos produtos. E assim tornamos nossas soluções de software acessíveis a uma ampla gama de clientes“. Kurt Hartmann continua o pensamento: „O gerenciamento de dados de soldagem nos ajuda a otimizar nossa tecnologia de união em todas as áreas. A Fronius nos deu uma ferramenta realmente poderosa. Possui um grande potencial. E com o apoio técnico dos especialistas da Fronius, podemos agora utilizar este sistema de forma lucrativa“.