Caminhões basculantes para condições difíceis em canteiros de obras
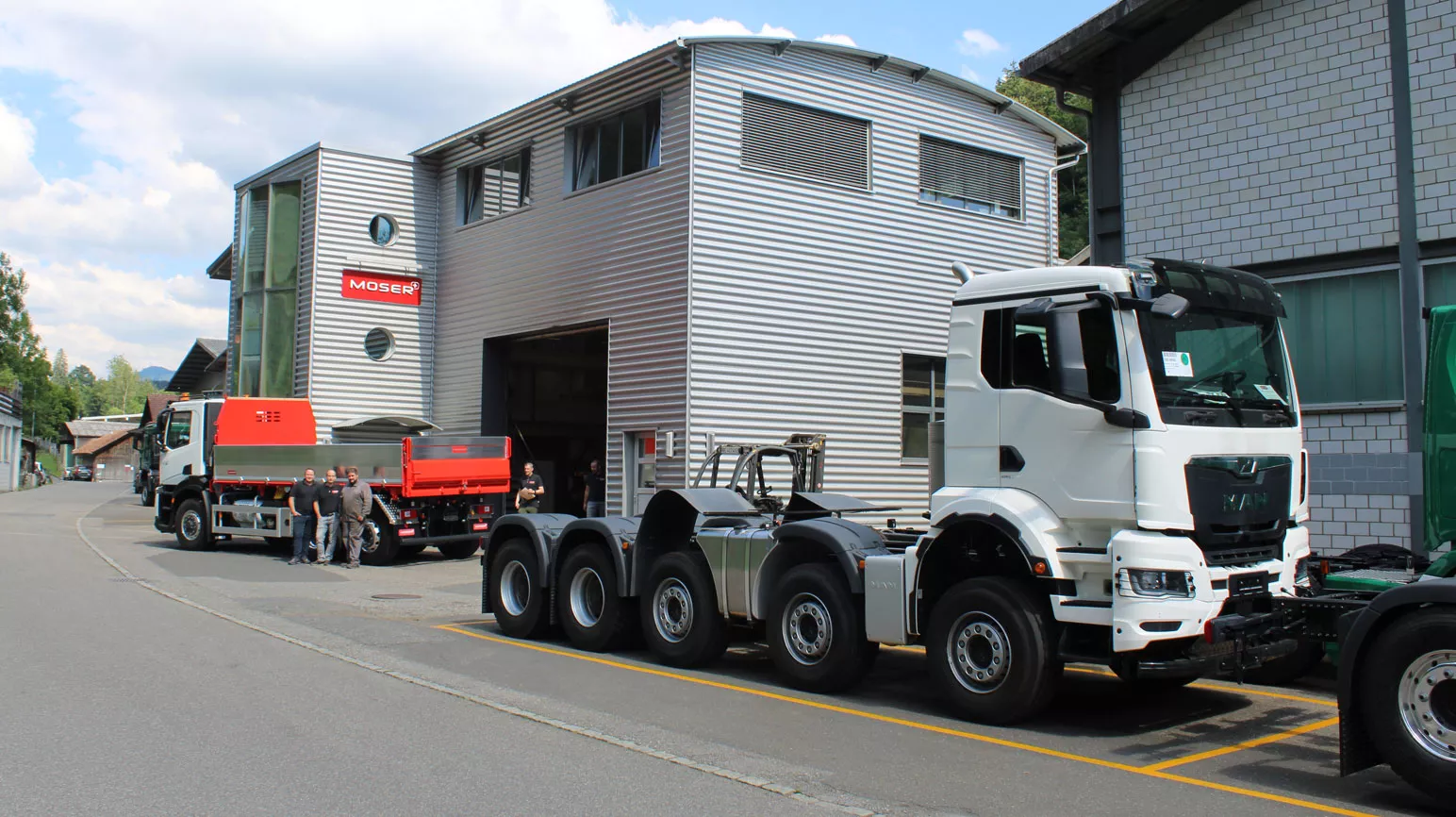
Peso de tara reduzido: "Sempre uma carga à frente"
A Moser AG fabrica superestruturas de veículos para caminhões com peso total entre 18 e 40 toneladas, sendo que os caminhões de 40 toneladas são capazes de transportar mais de 25 toneladas de carga útil. "Os maiores volumes de transporte possíveis por viagem são a principal prioridade em nosso setor. Para permitir que nossos clientes transportem o máximo de material possível com um peso total especificado, projetamos nossos dumpers e sistemas de carregamento para serem os mais leves possíveis, sem comprometer a resistência, a durabilidade ou a facilidade de uso", enfatiza Stefan Rolli, gerente de operações da Moser AG.
Dependendo do tamanho e do número de eixos do veículo em questão, as superestruturas de caminhões produzidas em Steffisburg geralmente pesam entre 3 e 4,5 toneladas. "O benefício em termos de carga útil para nossos clientes com o uso de nossas superestruturas mais leves, em comparação com as da concorrência, costuma ser de 500 a 700 kg por viagem. Isso resulta em um uso muito mais eficiente dos veículos, de acordo com nosso lema 'Sempre uma carga à frente'", diz Stefan Rolli.
A proximidade com o cliente favorece a personalização
As superestruturas feitas sob medida pela Moser AG para atender às necessidades individuais dos clientes se adaptam a todos os tipos comuns de caminhões. A empresa, da região do Cantão de Berna, orgulha-se particularmente do fato de que todos os dumpers e sistemas de carregamento - desde a chapa metálica e os perfis fornecidos - são produzidos na unidade da empresa em Steffisburg.
"Atualmente, somos a única empresa na Suíça que fabrica superestruturas de veículos comerciais para o setor de canteiros de obras com um índice de produção líquida real tão alto. O controle sobre todos os principais processos de produção e a proximidade com nossos clientes significam que podemos responder a solicitações especiais com muita rapidez e flexibilidade", explica o gerente de operações da Moser, Stefan Rolli.
Mais de 200 caminhões saem da fábrica de Steffisburg todos os anos, e o tempo de fabricação de um novo dumper é de 6 a 8 semanas, em média.
Visão geral dos processos de fabricação
Os processos de fabricação na Moser AG são essencialmente divididos nas seguintes etapas: Os caminhões são medidos minuciosamente após a entrega. Depois que as superestruturas são projetadas com a ajuda do CAD e do planejamento de produção, as próximas etapas envolvem o corte das chapas em uma máquina de corte a plasma CNC, a dobragem com uma prensa dobradeira CNC e o processamento mecânico adicional em um centro de usinagem CNC.
Nas oficinas de metalurgia da Moser AG, os componentes são soldados entre si, finalizando a forma bruta. As superestruturas do caminhão são então jateadas e pintadas. Após a instalação do sistema hidráulico, são realizadas a pré-montagem e a montagem final. Antes de um caminhão e sua nova superestrutura deixarem a Moser AG em Steffisburg para seu novo destino, ele é submetido a uma inspeção final completa.
Soldas em todos os componentes
"As soldas são encontradas em praticamente todos os nossos componentes. No uso diário em canteiros de obras, elas precisam resistir a choques, vibrações e torções - por exemplo, quando pedras pesando várias toneladas atingem o dumper a partir da caçamba de uma carregadeira. Como as costuras defeituosas têm consequências graves, nossas exigências em relação ao profissionalismo de nossos soldadores e ao equipamento que eles usam são extremamente altas", enfatiza Stephan Zingg, engenheiro de projeto da Moser AG. É dada atenção especial a soldas perfeitas nos componentes de suporte de carga, como a subestrutura ou o chassi do dumper.
Aço e alumínio até 70 mm
Na Moser, o aço de construção S355 convencional, os aços de S690 a S700 e o Hardox 450 em várias espessuras, de 3 mm a 70 mm, são soldados na fabricação das superestruturas dos caminhões. O material usado com mais frequência é a chapa de Hardox 450 com 4 mm de espessura.
As chapas de alumínio processadas em Steffisburg geralmente têm uma espessura de 2 mm, e as chapas de alumínio quadriculadas têm 3/4,5 mm ou 3/6,5 mm de espessura. Por último, mas não menos importante, ligas de alumínio relativamente leves são usadas para as paredes laterais dos dumpers. Elas são extrudadas usando um molde de fundição desenvolvido pela Moser AG, e o sistema de perfil de alumínio MAP Moser permite a construção modular das paredes laterais. Outras áreas de aplicação para chapas de alumínio incluem para-lamas, coberturas e estribos.
Focus on MAG manual welding – frequent out-of-position welding
The vast majority of welds at Moser AG are welded manually using the GMAW process. In addition to considerable welding speeds, this process delivers high deposition rates, while relatively little energy per unit length is input into the dumper parts to be welded.
For series production parts or repetitive processes, such as welding the subframes of the dumper bodies, a gantry system with a welding robot is used in Steffisburg. The gantry system makes it possible to turn the entire dumper so it is in the appropriate welding position.
“The characteristics of the weld are provided by the WPS. For the thicknesses of the fillet welds, we generally adhere to the A dimension, i.e., the thickness of the thinnest sheet element multiplied by 0.7,” explains Stefan Rolli.
To withstand the high loads in day-to-day use on construction sites, many welds are welded with a root pass and up to two final runs. In addition to fillet welds, butt welds – with and without an air gap – are also very frequently used. One task that the welders at Moser AG are regularly confronted with is out-of-position welding: from “classic” vertical-up seams on the pipe and sheet metal to overhead welds.
Four generations of Fronius devices
Moser AG has been using Fronius welding systems for 24 years. Today, around 35 devices from four different Fronius generations are used daily in Steffisburg: the Fronius VarioSynergic 4000, the VarioStar 457, the TransSynergic 5000, plus the Fronius TPS 500i since 2018.
Fronius TPS 500i: efficiency through precisely adjustable welding characteristics
“Speed and flexibility in manufacturing are crucial for us, especially in the current situation. By using the Fronius TPS 500i and its welding characteristics, we have significantly increased welding speeds in all key areas. At the same time, there has been a noticeable reduction in the amount of rework required on the welds. Overall, the TPS 500i not only makes the welding processes considerably more efficient, but also the downstream work steps, which subsequently has a positive effect on our entire manufacturing process,” says Moser operations manager Stefan Rolli.
The welding specialists at Moser AG frequently use the PMC Fronius Welding Package in the PMC Universal, PMC Dynamic, and PMC Mix variants on their TPS-500i devices. PMC stands for Pulse Multi Control and is a further development of the pulsed arc.
“In general, the PMC characteristics feature a stable, dynamic, and low-spatter pulsed arc. The excellent welding speeds of the TPSi are made possible predominantly by their high processor performance and the corresponding measuring and control speeds,” explains Fritz Loosli, the application engineer and customer adviser at Fronius responsible for Moser AG. The PMC characteristics provide two stabilizer and two correction parameters: an arc length stabilizer and a penetration stabilizer, as well as arc length control and pulse correction.
Up to 40 percent faster welding of vertical-up seams
The welding specialists at Moser AG use the PMC Mix characteristic, among others, because it permits the welding of vertical-up seams without the usual oscillating motion. Overall, up to 40 percent faster welding speeds are possible with the PMC Mix process for vertical-up seams. The technical basis for this characteristic is the process change between a pulsed and dip transfer arc, i.e., the cyclical change between a hot and a cold supporting process phase. The heat input into the material is reduced by this process.
Steel Root is another characteristic that is often used by the welding specialists at Moser AG. This characteristic excels at bridging gaps of 2 to 3 millimeters in size when welding dumper parts. A soft and stable arc is a typical feature of the Steel Root characteristic. The detachment of relatively large droplets creates a viscous weld pool, which can be used to weld larger gaps with ease.
The PMC Dynamic welding characteristic is used at Moser for horizontal fillet welds. It delivers a relatively aggressive arc with high pressure and concentrated focus. Your advantage: High welding speeds with low energy input enable low-distortion welding results and save valuable resources such as gas, filler metal and working hours.
Aside from this, Moser still uses tried-and-tested standard arcs for many welding processes. As a rule, aluminum parts are welded with a conventional pulsed arc.
User-friendliness on the welding system and directly on the welding torch
In addition to its welding characteristics, the TPS 500i’s high degree of user-friendliness also helps to make welding processes simpler, faster, and more efficient. The large clear text display on the TPSi is adapted to the welding environment. It is easy and intuitive to use in the respective local language, even when wearing gloves.
In connection with the user-friendliness of their equipment, it is essential for the welding specialists at Moser AG to be able to make adjustments directly on the welding torch: “Dump trucks are components that can’t exactly be moved back and forth quickly and easily, so our employees move around the components. To give our welders maximum freedom of movement, all our welding systems are equipped with 10 meter-long hosepacks,” explains Stefan Rolli.
The welders use lightweight PullMig welding torches in the JobMaster version with their TPS-500i devices. The water-cooled welding torches are equipped with a small electric motor in the torch handle, which ensures smooth wirefeeding through the 10 meter-long hosepack.
Fewer trips – greater efficiency
With the “EasyJob” JobMaster setting, users have the option of saving up to five welding jobs directly on the welding torch and rapidly switching between individual jobs. Being able to call up all the important welding jobs for their day-to-day work directly on the welding torch means they save themselves numerous trips between the welding system and the component. This makes day-to-day work not only more convenient, but also significantly more efficient.
“We have been using Fronius welding systems for 24 years because we see Fronius as a partner who stands for quality, reliability, sound advice, and innovative products. The ongoing technical developments, such as the TPS 500i most recently with its welding characteristics, contribute significantly to our performance, especially in terms of the speed and flexibility of our manufacturing process. The welding systems from Fronius help us to provide our customers in the Swiss construction site sector with the quality they rightfully demand from us,” concludes Moser operations manager Stefan Rolli.