Como as variantes de controle de processo estão revolucionando a soldagem dos componentes de exaustão: Formulários complexos - Costuras rápidas de solda
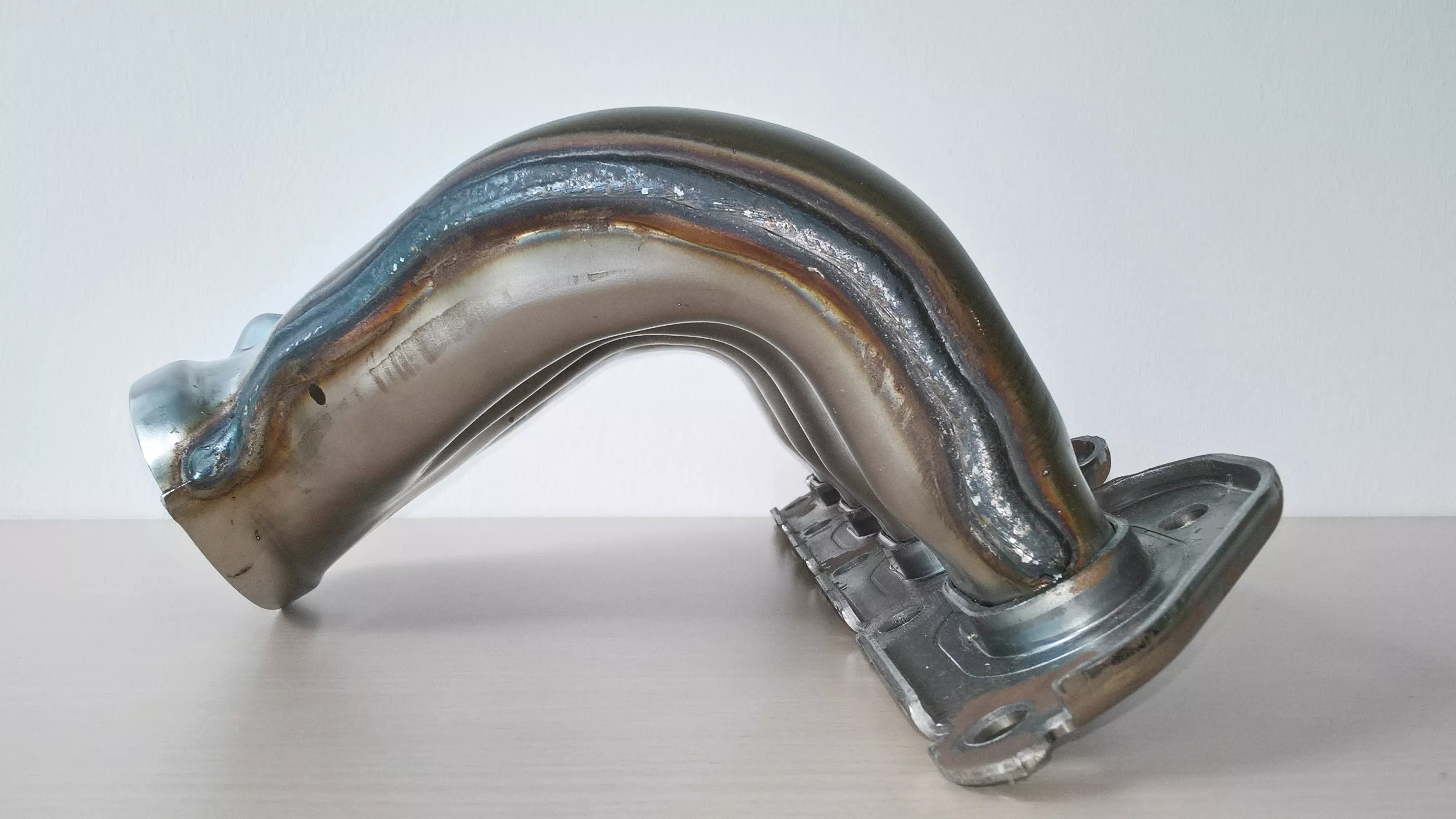
Os sistemas xhaust extraem os gases de combustão do motor e os limpam. Durante este processo, eles devem resistir tanto às altas temperaturas quanto à corrosão. As exigências impostas aos componentes individuais determinam de que material eles devem ser feitos.
A soldagem automatizada de gás metálico ativo (MAG) é o processo mais freqüentemente utilizado para unir componentes de exaustão. O coletor de escape é particularmente desafiador para o processo de soldagem: os raios apertados dos componentes forçam o robô a reduzir a velocidade de soldagem. Entretanto, a quantidade de energia direcionada ao componente deve ser mantida a um mínimo e o processo de soldagem deve permanecer estável e reprodutível.
Eletrônicos de Alta Eficiência abrem novas possibilidades
Assim como o coletor de escape, outros componentes também trazem seus próprios desafios. O tipo e a espessura do material utilizado baseia-se nas exigências impostas ao grupo de componentes correspondente - por este motivo, o processo de soldagem também deve ser adaptado para se adequar aos respectivos componentes. A Fronius possui uma gama de diferentes variantes de controle de processo para soldagem MAG que possibilitam a soldagem consistente de componentes complexos. A eletrônica de alto desempenho das modernas fontes de energia permite aos usuários adaptar o arco de forma controlada e, portanto, obter os melhores resultados.
O modo "Low Spatter Control" (LSC) é particularmente adequado para soldar componentes de exaustão. Com base em um arco de transferência por imersão, é eficiente em termos energéticos e livre de respingos. Isto é conseguido pelo sistema de soldagem que controla precisamente o curto-circuito: A fonte de energia detecta com precisão o eletrodo de arame que se aproxima da piscina de solda e regula o desprendimento da gota dentro da piscina de solda de tal forma que ele acontece com uma potência menor. Isto significa que a entrada de calor no componente é baixa e quase nenhum respingo é criado. Isto é ideal para unir componentes com pequenas espessuras de parede e geometrias de juntas variáveis - tais como em coletores de escape. Além disso, a LSC garante alta estabilidade durante a difícil reorientação da tocha de solda e, portanto, altas velocidades de soldagem.
Uma outra variante de processo é o "Pulse Multi Control", também conhecido como PMC. Este arco pulsado modificado é caracterizado por um desprendimento de gotas precisamente regulado e de baixa dispersão. O PMC cria um arco potente e estável e, por exemplo, durante a soldagem fora de posição, oferece altas taxas de deposição e boa controlabilidade do pool de solda ao mesmo tempo. Os usuários podem, portanto, evitar imperfeições, tais como undercuts e soldagem de forma estável e reprodutível. Esta variante é particularmente adequada para componentes sujeitos a tolerâncias e com grandes variações na espessura da parede - condições que se aplicam a uma série de componentes de exaustão. Mesmo nestas situações, o PMC garante penetração suficiente e uma capacidade de ponte de fendas. Os fornecedores automotivos utilizam regularmente este processo para soldar os coletores de escape. Na prática, o PMC permite o uso de velocidades de soldagem consideravelmente mais altas, aumentando assim a produtividade.
Ainda mais elevado, mais fino!
Entretanto, os desafios que a indústria automotiva poderá enfrentar no futuro poderão mudar o foco para outras variantes de processo. Uma tendência significativa no setor é o desenvolvimento de veículos cada vez mais leves. O menor peso reduz o consumo de combustível, enquanto a economia de material também reduz os custos de fabricação. Isto também afeta o projeto dos componentes de escape. Os materiais de base resistentes à temperatura e os metais de enchimento utilizados permitem que os componentes sejam fabricados a partir de materiais cada vez mais finos. Os componentes com espessuras de parede de 0,8 milímetros podem, portanto, tornar-se padrão no futuro. O processo CMT (Cold Metal Transfer) é frequentemente utilizado para este tipo de aplicação. O processo combina um arco de transferência por imersão regulado com um eletrodo de arame que se desloca para frente e para trás. O resultado é uma entrada de calor particularmente baixa e um processo de soldagem incrivelmente estável, que permite até mesmo aos usuários alcançar resultados ótimos ao soldar componentes muito finos.