Trumpf yeni LaserHybrid kaynak sistemi ile verimliliği artırıyor
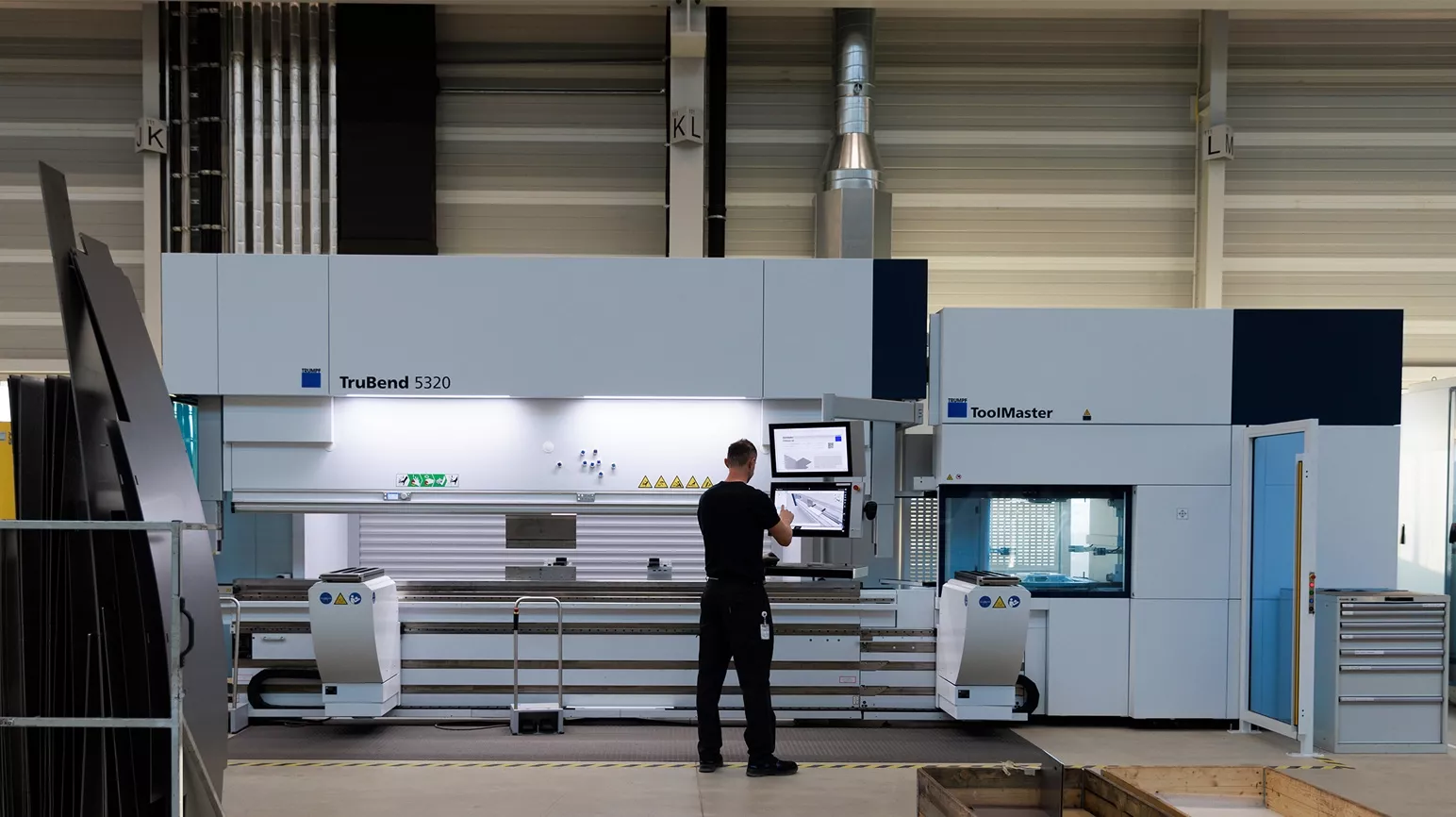
LaserHybrid kaynak sistemi sayesinde satın almak yerine şirket içinde uygun maliyetli üretim
Trumpf, son yıllarda bükme makinelerinde önemli bir büyüme kaydetti ve bu sektördeki ürün portföyünü aralıksız olarak genişletti. Artan kapasite kullanımı, bükme makineleri için birkaç ton ağırlığında çerçevelerin satın alınmasını gerekli kıldı, bu da daha uzun üretim sürelerine, daha yüksek maliyetlere ve üretimde sınırlı esnekliğe yol açtı. Kaynak işlemleri, tedarikçinin tesislerinde manuel olarak ve zaman alan ek işlemlerle yapılıyordu: Manuel kaynaktan sonra çelikte istenmeyen sertleşmeyi önlemek için enerjisi yoğun bir yumuşak tavlama işlemi gerekliydi.
"Tavlama sırasında çelik, bir tavlama fırınında 800 °C'ye kadar ısıtılır. Isıtma esnasında malzeme havadaki oksijenle reaksiyona girer, yüzeyde oksitlenir ve pas oluşturur. Bu nedenle parçaların boyanmadan önce kumlanması gerekir," diye açıklıyor Trumpf Üretim Müdürü Thomas Reiter. "Yeni LaserHybrid kaynak sistemimiz sayesinde, enerji kullanımı açısından yoğun ve maliyetli tavlama işleminden vazgeçebiliyoruz. Lazer kullanarak, kaynak dikişi boyunca çeliği malzemeye bağlı olarak 150 °C ile 180 °C arasında ısıtıyoruz ve böylece kaynak sonrası soğuma hızını azaltıyoruz. Bu sayede sertleşmeyi, soğuk çatlakları ve korozyonu önlüyoruz. Ayrıca kendi üretimimiz sayesinde daha bağımsız ve esnek hareket etme imkanına sahibiz."
Tavlama işleminden vazgeçmenin hem ekonomik hem de ekolojik açıdan avantajlı olduğu kanıtlanmıştır. Enerji tasarrufu, hane başına ortalama 3.800 kWh tüketim dikkate alındığında, yılda yaklaşık 270 dört kişilik hanenin elektrik ihtiyacına karşılık gelmektedir.
Optimum yan bağlanma ve daha az gözenek oluşum eğilimi
LaserHybrid kaynak işlemi, kaynak dikişine yönelik bir lazer ışını ile MSG kaynak işlemini ortak bir işlem bölgesinde birleştirir. Yüksek derecede odaklanmış lazer ışını, son derece yüksek enerji yoğunluğu ile karakterize edilir ve makine çerçevelerini kaynaklarken çeliğin 10 mm derinliğine kadar nüfuz eder. Lazerden hemen sonra, kök pasosunu dolduran ve optimum yan bağlanma sağlayan MAG işlemi uygulanır. Oluşan ilave sıcaklık, malzemeye gaz çıkışı için zaman kazandırır ve saf lazer kaynağına kıyasla gözenek hassasiyetini azaltır. Sac kalınlığına bağlı olarak, Trumpf'ta MAG kullanılarak 29 adede kadar kapak pasosu kaynaklanır.
Artan verimlilik ve malzeme tasarrufu
LaserHybrid offers Trumpf decisive advantages over MIG/MAG-only welding. Reiter explains: “For one, we save up to four tons of welding wire and valuable working time every year, as we can skip the time-consuming process of chamfering the sheet edges, especially on thinner sheets. This keeps the weld cross-sections small and cuts down on filler metal. Secondly, we increase our productivity thanks to high welding speeds, which come as a result of the stabilized arc that LaserHybrid creates in conjunction with MIG/MAG. And thirdly, the low energy per unit length reduces component distortion.”
Dolgu malzemesi tüketimi üzerinde de olumlu bir etkisi olan bir diğer avantaj da bu alanda öne çıkıyor. LaserHybrid prosesi, kaynak dikişinin daha da içeriye doğru hareket ettirilmesini sağlıyor. Bu sayede, kaynak dikişinde yan parçalara daha fazla yaklaşabilir ve kaynak dikişini daha dar tutabilirsiniz.
Fronius için değerlendirme ve karar verme
Trumpf, Fronius'un LaserHybrid robotik kaynak sistemini seçmeden önce, farklı sağlayıcıların konseptlerini değerlendirdi. Amaç, en iyi teknik ve en ekonomik çözümü bulmaktı. Ağırlığı 18 tona kadar çıkan ve 4,5 × 3 × 2 m boyutlarındaki iş parçalarının kaynak sırasında hareket ettirilmesi ya da pozisyoner üzerinde konumlandırılması seçenekleri ivedilikle bir kenara bırakıldı. Başından beri tercih edilen üretim süresine paralel kurulum, bu varyantlarla hiç mümkün olmayacak ya da sadece sınırlı ölçüde mümkün olacaktı.
Bu nedenle, bir LaserHybrid ve bir MAG kaynak robotunun yanı sıra yatay bileşen beslemesini sağlayan iki büyük eğimli konumlandırıcıya sahip iki istasyonlu bir gantry sistemi lehine karar verildi. Bir makine şasisinde kaynak yapılırken, diğeri serbest konumlandırıcıya entegre edilebilir.
"Pozisyonerler sadece üretime paralel kurulumu olumsuz etkilemekle kalmaz. Ayrıca, birkaç ton ağırlığındaki bileşenlerimizin ağırlık merkezlerinin pivot veya devirme ekseninden çok uzakta olması durumunda aşırı devirme torku riski ortaya çıkacaktı. Bu durumda sistemin zarar görmesi ve kaza riski son derece yüksek olacaktı," diye açıklıyor Reiter. "Bu tür sorunları ancak büyük pozisyonerler kullanarak önleyebilirdik. Ancak o zaman da çalışma yüksekliğiyle ilgili bir sorunumuz olurdu. Bazı iş parçalarının devasa boyutları nedeniyle ya iki buçuk metre derinliğinde bir çukura ya da en az iki metrelik bir işleme yüksekliğine ihtiyacımız olurdu."
Sonuç olarak, Fronius tarafından önerilen varyantın en iyisi olduğu konusunda mutabık kaldık. Bu noktada belirleyici olan birkaç faktör vardı: mantıklı bir güvenlik konsepti, iki kaynak robotu kullanılarak torç değiştirme istasyonunun ortadan kaldırılması, sorunsuz hortum paketi kılavuzu, dikiş tespiti için WireSense kullanımı ve ince MAG robotunun köşe alanında iyi erişilebilirliği. Buna ek olarak, iki eğilebilir konumlandırıcı ile mümkün kılınan üretime paralel kurulum, verimli üretim sağlar. Fronius lehine diğer artı noktalar, uzun süredir devam eden güvene dayalı iş ilişkisi, kaynak işlerinin Pathfinder ile çevrimdışı programlanması ve Fronius uzmanlarının sistem teknolojisindeki uzmanlığıydı.
Alet değişikliği gerektirmez
Torçları değiştirmek zorunda kalmamak ve hortum paketini aktarırken ortaya çıkan tüm sorunları önlemek için Fronius uzmanları iki kaynak robotlu bir gantry sistemi kullanmaya karar verdi. Bunların her biri bir LaserHybrid ve bir MAG kaynak kafası ile donatılmıştır ve hiçbir zaman aynı anda çalışmamaları için hareketli bir ray üzerinde hareket ederler. İlk olarak, LaserHybrid robotu kök pasosunu devralır. Sonrasında ise ulaşılması zor alanlar ve kapak katmanları MAG içi boş mil robotu kullanılarak kaynaklanır.
"MAG robotu, içi boş mili sayesinde optimum hortum paketi yönlendirmesini garanti eder. Yanal olarak yönlendirilen hortum paketleri genellikle istemsizce döner. Hasar görebilir ya da en kötü durumda kopabilirler. Ayrıca bu tür hortum paketlerinin, robotların hareket özgürlüğünü kısıtlayabilecek iş parçalarına veya cihazlara takılma riski de var ." diyor Reiter.
Gelişmiş: Tek hat üzerinde iki kaynak robotu
Aynı hat üzerinde iki kaynak robotunun kullanılması özel bir zorluk teşkil etmektedir. Çözüm, bir seferde sadece bir kişi kaynak yaparken diğerinin durağan pozisyonda kalmasıdır. Her robot için tüm hareketleri içeren ve iş parçasına özgü kaynak görevlerinin programlanması için temel teşkil eden özel bir program şablonu oluşturulmuştur.
Kabul bileşenleri için Trumpf tarafından sağlanan kaynak sıraları, Fronius Pathfinder kullanılarak tasarım aşamasında dijital ikiz üzerinde simüle edilmiş ve uygulanabilirlik açısından kontrolden geçirilmiştir. Bu sayede müşterinin kaynak uzmanları, erişilebilirlik sorunları gibi potansiyel üretim zorluklarından önceden haberdar edildi. Fronius'ta yazılım mühendisi ve simülasyon uzmanı olarak çalışan Wolfgang Mitterhauser özel bir odak noktası belirledi:
"Son işlemciyi (ayrıştırıcı) MAG kaynak robotu için WireSense dikiş izleme sensörlerinin kullanımı gibi özel komutları çevirebilecek şekilde genişlettim. Ayrıştırıcı, dijital ikizden oluşturulan kaynak programlarını gerçek sisteme aktarır. Eklentiler, tam olarak müşterinin sistemine göre uyarlanmış ve Pathfinder'ın standart versiyonunda yer almayan program bölümlerini içeriyor," diye açıklıyor Mitterhauser.
Bu eklentiler sayesinde, sistem operatörleri son işlemciden tam olarak hangi bilgilerin ne ölçüde aktarılacağını belirleyebilirler. Mitterhauser,"Sonuç olarak robotun gereksinimlerini tam olarak karşılayan bir kaynak programı ortaya çıktı,” diye ekliyor.
Pathfinder'da bir çarpışma sensörü oluşturulabilir, böylece torcun bileşen üzerindeki olası bir etkisi erken bir aşamada algılanır. Sanal izleme sistemi olası bir çarpışmayı fark ederse, yazılım bunu hemen gösterir.
Sensör görevi gören kaynak teli
Tüm sistem bileşenleri neredeyse mükemmel bir şekilde çalışsa bile, dikiş izleme sensörleri olmadan katman kaynağı sırasında sapma riski vardır. Bu, yanma veya yetersiz A boyutları gibi birleştirme hatalarına yol açabilir. Fronius WireSense, kaynak dikişi algılaması için kaynak telini bir sensör olarak kullanır ve torca bileşen erişimini engelleyebilecek optik ölçüm yardımcılarını ortadan kaldırır. Çeşitli bileşen geometrileri algılanır ve yüksek frekanslı ters tel hareketleri aracılığıyla münferit sacların birbirlerine göre konumu hassas bir şekilde belirlenir. WireSense ek torç parçası gerektirmez ve kalibrasyon veya bakım çalışmasına ihtiyaç duymaz. Bu yenilikçi sensör teknolojisi sayesinde Trumpf, kusursuz kaynak dikişlerinden ve daha düşük üretim maliyetlerinden yararlanabiliyor.
Tüm süreçlerin akıllı kontrolü
Kullanıcı dostu HMI-T21 RS sistem kontrolü, kaynak sisteminin en önemli parçasıdır. Robot, kaynak akımı kaynağı, eğimli konumlandırıcı ve torç temizleme sistemi gibi tüm çevresel bileşenleri izler ve koordine eder. Mevcut 3D gerçek zamanlı görüntüler sayesinde, Trumpf'ın kaynak uzmanları tüm robot hareketlerini monitörden canlı olarak takip edebiliyor. Önceden ayarlanmış veya özelleştirilmiş görünümler arasında seçim yapabiliyor ve her zaman en uygun görüntüyü sağlamak için bunları kaydedebiliyor.
Yenilikçi HMI-T21 RS'in önemli bir bileşeni de program editörüdür. Burada, sistem operatörleri münferit program dizilerini tanımlıyor, bunları bir işleme istasyonuna atıyor ve bir süreç zinciri olarak kaydediyor.
Hata, uyarı veya bilgi mesajları durum çubuğunda düz metin olarak görüntülenir. Herhangi bir mesaj yoksa, tüm sistem durumları ve program sırası görüntülenir ve oturum açan kullanıcı sağ sütunda gösterilir.
Mitterhauser: "Duruma genel bakış"mevcut tüm sensörlerin durumunu gösterir. Bir arıza mesajı varsa, HMI yardımıyla tüm sinyaller kontrol edilebilir."
Sanal devreye alma ve montaj
Gantry ve pozisyonerin devasa boyutları nedeniyle Fronius'un kaynak sistemini kendi şubesinde kurması ve ön devreye alması mümkün değildi. Bunun yerine Pathfinder ile sanal devreye alma yöntemi kullanıldı. Bu yazılım, devre şemasında tanımlanan tüm sinyalleri ve gerçekçi kinematiği içeren sanal bir model oluşturmak için kullanıldı. Dijital kopya sayesinde yazılım teknisyenleri sistemin çalışmasını gerçekçi bir şekilde simüle edebildi.
Pathfinder, müşterinin ön değerlendirmesi sırasında da son derece yararlı olduğunu kanıtladı. On adede kadar farklı bileşeni tutabilen iki kaynak robotu ve devirme pozisyonerlerinin tüm hareket dizileri, sanal gerçeklik gözlükleri yardımıyla gerçekçi bir şekilde deneyimlenebildi.
İlgili Trumpf çalışanları tüm tasarım aşaması boyunca sürece dahil oldular ve öneri ve geri bildirimleriyle projenin başarısına önemli katkıda bulundular.
LaserHybrid kaynak sistemini sahada kurmak son derece zorlayıcı oldu. Portalın devasa boyutları ve 90°'ye kadar döndürülebilen eğilebilir konumlandırıcı, ciddi bir lojistik zorluk oluşturdu. Gereksiz gecikmeleri önlemek için tüm bileşenlerin doğru zamanda doğru yerde olması gerekiyordu. Boyutları nedeniyle kısmen kapalı otoyollar üzerinden taşınması gereken iki devirme pozisyonerinin gece teslimatı oldukça zorlayıcı oldu.
Pathfinder ile fizibilite çalışmaları sayesinde verimlilik artışı
Trumpf'taki makine mühendisliği uzmanları, yazılımı yeni kaynak işlerini programlamak ve simüle etmekten daha fazlası için kullanıyor. Yeni parçaların kaynak yapılabilirliği sanal olarak kontrol edilir: Bileşen yapısı otomatik kaynak için ne ölçüde uygun? Bileşen erişilebilirliği rahat mı? Çarpışma riski var mı? Parçaların manuel olarak kaynaklanması veya tasarımın değiştirilmesi gerekiyor mu? Bu tür kapsamlı fizibilite testleri ve süreç simülasyonları artık Trumpf'a üç haftaya kadar programlama süresi kazandırıyor.
Sonuç: Doğru karar
Yeni Fronius LaserHybrid kaynak sistemi, makine çerçevelerinin kaynak dikişi kalitesini önemli ölçüde iyileştirir, kaynak hızını artırır ve çevrimdışı programlama ve simülasyon seçeneği sayesinde çalışma süresinden ciddi tasarruf sağlar.
Thomas Reiter son derece memnun: "Şu anda yılda yaklaşık 1.500 bükme makinesi üretiyoruz. Yeni robot kaynak sistemimiz sayesinde sadece daha ekonomik olmakla kalmıyor, aynı zamanda makine çerçeveleri bileşenlerini satın almaya artık bağımlı olmadığımız için teslimat süreleri açısından da çok daha esnek hale geliyoruz. Artık üretim kapasitesi açısından da daha fazla seçeneğimiz var."