The perfect partner for overlay welding: Fronius Welding Automation
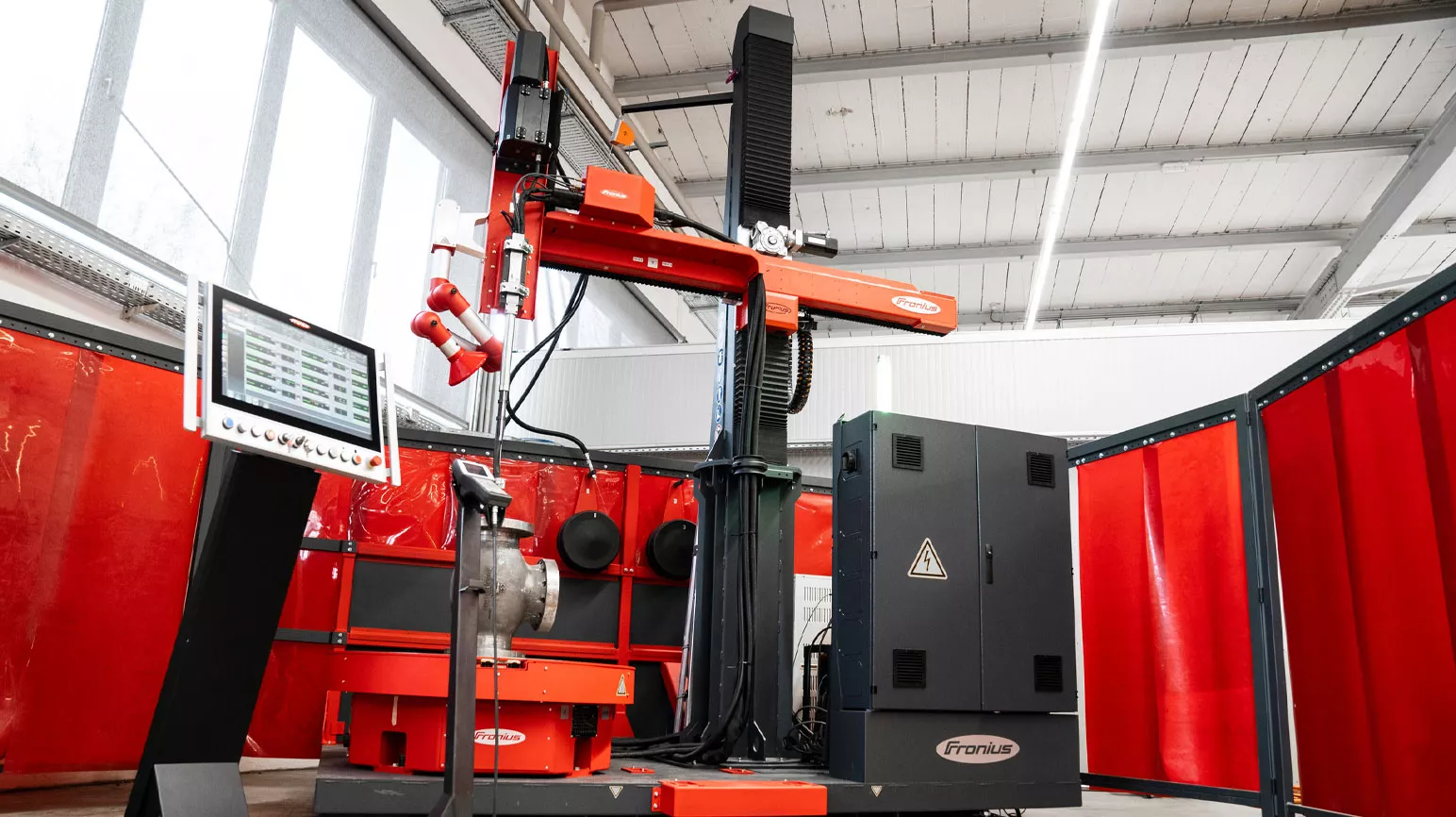
Supporting customers throughout the product life cycle
From planning, engineering, manufacturing and commissioning to the maintenance and servicing of overlay welding systems, customers can rely on Fronius Welding Automation to support them with its global service and partner network. All systems are manufactured in accordance with international compliance standards to ensure safety and reliability. Technical commissioning by Fronius experts and the preliminary acceptance by buyers from the oil and gas industry take place at the production site in Steinhaus, Austria. The systems are then delivered, installed on site and finally accepted by international customers in the onshore and offshore sector. The comprehensive Fronius commissioning service includes expert training sessions and process optimizations at the start of production.
Realistic welding tests and feasibility studies
Every new overlay welding project at Fronius Welding Automation begins with feasibility studies and welding tests. Overlay welding is a highly complex process. In addition to the base material of the components to be surfaced, parameters such as amperage, wire speed, welding speed, filler metal, shielding gas, ambient temperature, and humidity also play a decisive role. Even minor deviations can have unwanted effects on the welding result. This is why welding tests should be as realistic as possible—with components, filler metals, and shielding gases that will also be used when the system goes into live operation. If possible, the tests should also be carried out under the same climatic conditions that prevail at the intended place of use. If these conditions cannot be achieved, the welding parameters must be adapted and optimized in line with the production environment during commissioning. Ideally, these tests should be done by Fronius experts to avoid any nasty surprises.
Anton Leithenmair, Head of Fronius Welding Automation: “We need an open, trusting exchange of information from the outset to ensure that overlay welding systems are customized to customer requirements. Are there any specifications regarding the filler metal and shielding gas? What about the local climatic conditions? One particularly important factor is being able to carry out our welding tests with original components rather than resorting to dummies. This is the only way our systems can deliver the desired welding results, even under the harsh conditions of continuous operation.”
Complete solutions for the oil and gas industry
Fronius Welding Automation draws on a wealth of experience to devise innovative ideas for new system solutions. Over a period of more than forty years, the company has developed application-basestems that are either used as standard or modified to meet special customer requirements.
Compact Cladding Cell (CCC)—Smart and user-friendly
With a footprint of approximately 6 m² (64.5 ft²), the Compact Cladding Cell mounted on a transportable platform is “the” compact solution for overlay welding. It was developed as a cost-effective inner cladding solution for valve components. The maximum bore depth and largest possible component diameter are 1 m (39 in), the highest component weight is 2,500 kg (5,511.56 lb). Despite its compactness, the system is an extremely powerful overlay welding system. It stands out for its ease of use, precise movement sequences, and comprehensive data recording options. The ergonomic design includes a wire spool holder at a comfortable user height, welding torch quick-change system, and power sources on a rail. Plus, the CCC boasts innovative software functions, maximum process security, and ultimate reliability in continuous operation. The HMI system controls offer next-level ease of use with a 21-inch touch display, real-time process visualization, multi-user management, and much more. For applications requiring the highest possible productivity, SpeedClad 2.0 is the process of choice.
Endless Torch Rotation System (ETR)—Almost unlimited possibilities
The ETR system was developed for larger, more complex components and has been an established solution for many years. Its key feature is an endlessly rotating welding head. This makes it possible to weld components with different bores and bore angles up to an internal diameter of 1 m (39 in). The welding torch and the wire feeder rotate together around the bore axis. Components are centered automatically, which shortens set-up times considerably and saves production costs. If there is a risk of the torch colliding with the component, the electropneumatic collision detection system stops all axes of movement and protects the welding torch against damage. Most recently, Fronius has enhanced its successful ETR system with the even more flexible ETR Ultimate system. In addition to overlay welding tasks, this versatile system also makes it possible to join larger components with challenging geometries and difficult seams. As with the Compact Cladding Cell, both the ETR and ETR Ultimate systems come with the convenient 21-inch system controls with touch display, real-time process visualization, and multi-user management as standard. The same applies to the welding torch quick-change system, which is designed to save time. If necessary, the welding torch and positioner move in sync in both the ETR and ETR Ultimate, while the SpeedClad 2.0 delivers maximum productivity for the overlay welding process here as well.
All parameters live and at a glance
The HMI-T21 system controls are ready for Industry 4.0 with a large, intuitive 21-inch touchscreen, multi-user accounts with individually assigned authorizations, process visualization in real time, on-the-fly parameter adjustments, and innovative functions such as X-Ray View, Component Editor, Bore-to-Bore Advanced, actual value monitoring in real time, and STEP file import. And, of course, the system offers remote maintenance capabilities. The X-Ray view provides a transparent outline of the component to give the operator an excellent overview. The Bore-to-Bore-Advanced function offers assistance when several offset transverse bores with non-90° angles or flanges with bores are to be surfaced. All relevant welding parameters are displayed live in the system-integrated actual value monitoring.
A service that meets every need
The welding professional creates components step by step in the Component Editor via the HMI-T21 touchscreen. The height and diameter are defined by inputting the relevant dimensions, and the various components appear in real time as 3D graphics on the screen. In addition to cylindrical shapes, flat and conical shapes are also possible. There are also options to model bores and extensions, such as flanges. The CNC technology now integrated at Fronius creates scope for even more component geometries than before, including intersection bores on conical components.
The welding processes are programmed in the Program Editor. Operators select the individual sections of the components and define the welding sequence. One especially helpful aspect is that the welding torch can be shown at the starting point.
All welding parameters are defined in the Weld Editor. The system offers a selection of jobs with fixed parameters that can be adjusted at any time—even on-the-fly—in the Weld Adjust menu. AVR (Actual Value Recording) records the actual values of the welding current, voltage, wire speed, gas quantity, and welding position during the welding processes in table form. The PC software packages Data Logger HMI and Data Viewer HMI are optionally available for graphical evaluations and analyses.
Once the home position of the welding torch has been calibrated, it moves independently to the starting point for each overlay welding application. Siegfried Wiesinger, overlay welding expert at Fronius, explains: “The remote control can be used to fine-tune a range of parameters even just before igniting the arc—for example, the AVC (Arc Voltage Control) function adjusts the starting point and distance of the welding torch to the component.“
SpeedClad 2.0—Award-winning and blazing fast
Faster, resource efficient, more economical—with SpeedClad 2.0, Fronius is setting new standards in overlay welding of valve components. SpeedClad 2.0 is much more cost-effective than the pulsed TIG hot wire processes. This innovation stands apart thanks to its high deposition rate, impressive speed, and low shielding gas consumption. In recognition of its exceptional results, the process was awarded the Excellence in Welding Award by the American Welding Society at FABTECH in Chicago on September 13, 2023. The jury was impressed by the deposition rate of the nickel-based alloy used in overlay welding being increased from 1.63 kg (3.59 lb) to up to 6 kg (13.23 lb)/h, with Fronius now using a 1.6 mm wire (0.063 in) in place of the 1.14 mm (0.045 in) wire. The welding speed rose from 33 cm (13 in)/min to 135 cm (53 in)/min, and the average pulsed current went from 240 amperes to 460 amperes. All Fronius customers are guaranteed the ideal heat input while simultaneously reducing argon gas consumption from 516 l/kg to as little as 140 l/kg. The fully re-developed welding torch system allows cladding of significantly narrower component diameters of 100 mm (3.94 in) instead of 150 mm (5.91 in). The heat input formula served as the starting point for the optimized cladding process: heat input = volts x amperes x 60 / welding speed.
Sustainability is part of Fronius Welding Automation’s genetic makeup, which is why many of its innovations not only deliver technical improvements but also reduce consumables—just as the SpeedClad 2.0 process does.
Longitudinal and circumferential seam welding systems and robotic welding systems also in the range
As a solution provider, Fronius Welding Automation not only produces overlay welding systems but also mechanized welding systems and robotic welding systems for all industries.
These include longitudinal and circumferential seam welding systems, welding carriages, and handling-to-welding robotic welding systems. Collaborative systems, intelligent sensor technology, software solutions for data management, and offline programming including welding simulation open up profitable welding opportunities for metal processing companies starting with a single batch. The specific requirements for the welding technology are analyzed together with the customer. This is followed by the creation of an individual solution.
To do this, Fronius has a construction kit of standardized components at its disposal. Starting with the feasibility study and continuing with planning, engineering, manufacturing, and start-up, the sale of welding systems is handled as a project. Since 1975, more than 3,500 installed systems have been used across 45 different countries with over 2,000 customers. Covering an area of more than 11,000 square meters (118,400 sq. ft), around 150 employees take on the welding technology challenges presented by their customers.
Take a look for yourself at the new and proven solutions for cladding and 3D metal printing. The Fronius team are looking forward to showing these innovations at the ADIPEC trade show in Abu Dhabi, on 4th to 7th of November 2024, Hall 14, Stand 14316.