Perfect weld seams 24/7 – for SMEs too
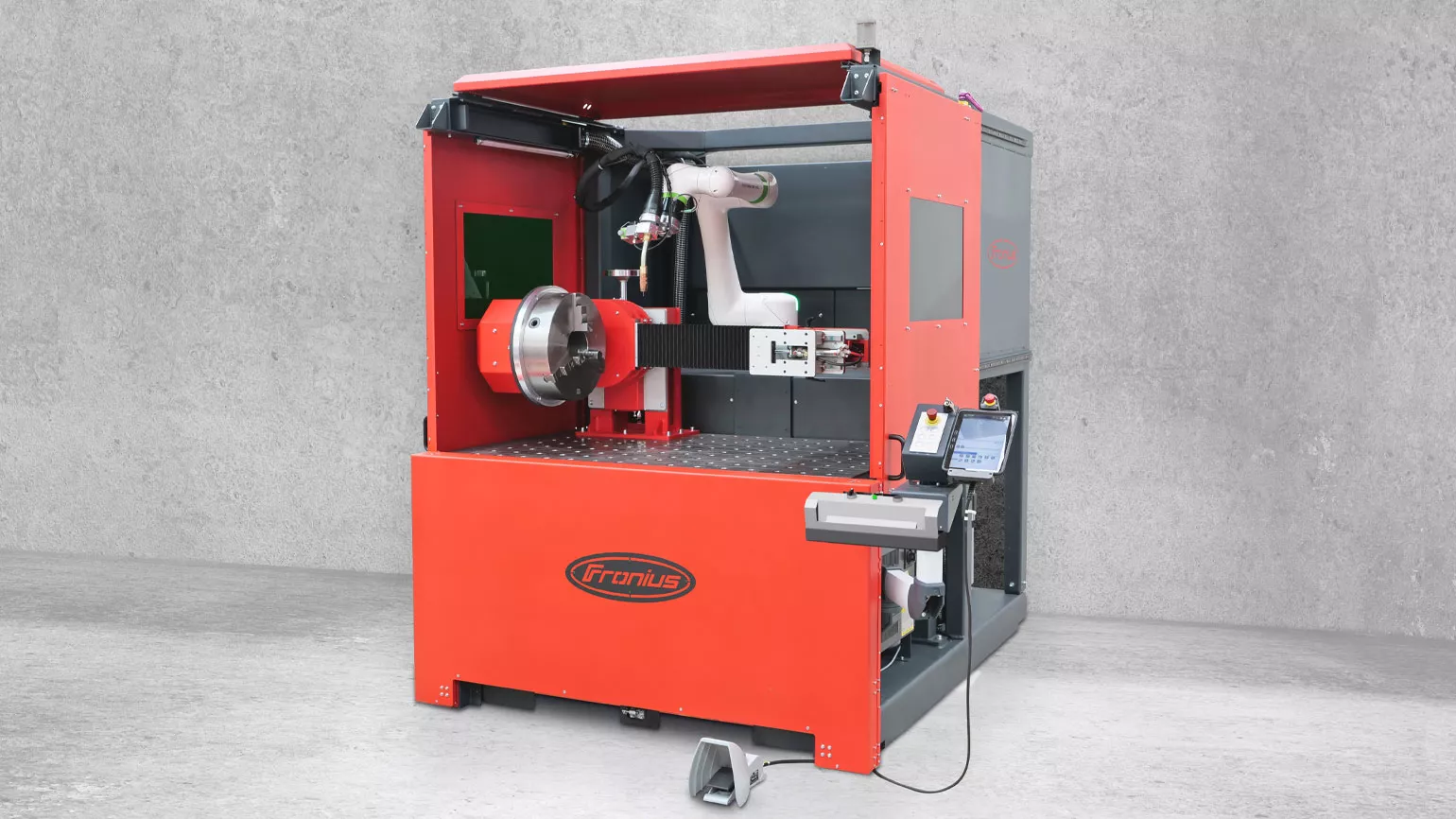
Although automated welding processes achieve significantly more consistent welding results, small and medium-sized businesses frequently still struggle with automation. High acquisition costs for welding robots and professional programming expertise are at odds with small batch sizes. The CWC-S Cobot welding cell from Fronius provides a solution to this mismatch.
Consistent welding quality – from batches of just one unit
Thanks to precise torch movements with a repeatability of +/- 0.04 millimeters, weld reproducibility is guaranteed in the Cobot welding cell every time – even in series if necessary. Intelligent Fronius welding technology controls the welding process and records all welding data as required. The WeldCube data management software – optionally available with the welding cell – serves to store and evaluate these data.
Teach Cobots – with no programming experience
“Programming a CWC-S is intuitive and can be quickly learned by any welding specialist; programming know-how is not required. Components can even be loaded and welding programs started by trainees,” explains Christian Neuhofer, Product Manager at Fronius Welding Automation. “This saves on personnel costs and frees up professional welders for more challenging work – making their job more attractive.” This is an advantage that should not be underestimated when searching for skilled workers to add to the team.
Specify the welding path at the touch of a button
The welding torch is manually guided to the starting points, position points, and end points on the component and these are confirmed by pressing a button. The software uses this information to calculate the welding contours and welding sequence, while the required welding parameters can also be selected quickly using predefined characteristics. Motion commands such as “pendulum parameters” or “weld job” can be inserted by means of dragging and dropping on the touchscreen of the Cobot control.
Before starting the welding process, the operator can simulate the welding sequence once again to detect and correct possible interference contours. Once the CWC-S is fully programmed, it welds component after component with consistent quality and at a regular speed.
Equipment and starter packages
The welding cell’s standard equipment includes a Fanuc Cobot CX10 iA with a reach of 1,249 millimeters and a payload of 10 kilograms, and a welding table with a working area of 1,500 x 1,000 x 700 millimeters. Operator safety is ensured by a pneumatic glare shield, sliding side doors with viewing windows, and an extraction hood.
Users can choose between the tried-and-tested Fronius Welding Packages Standard, Pulse, LSC (Low Spatter Control), PMC (Pulse Multi Control), and CMT (Cold Metal Transfer) depending on the intended area of use, while the TPS 320i or TPS 400i welding systems are available for the Cobot, subject to the package selected.
The standard equipment can of course be supplemented with special starter packages or the user-friendly WeldConnect app, for example. Further options include an extraction system, a rotary unit including tailstock, or the option of crane loading.