Circumferential welding systems
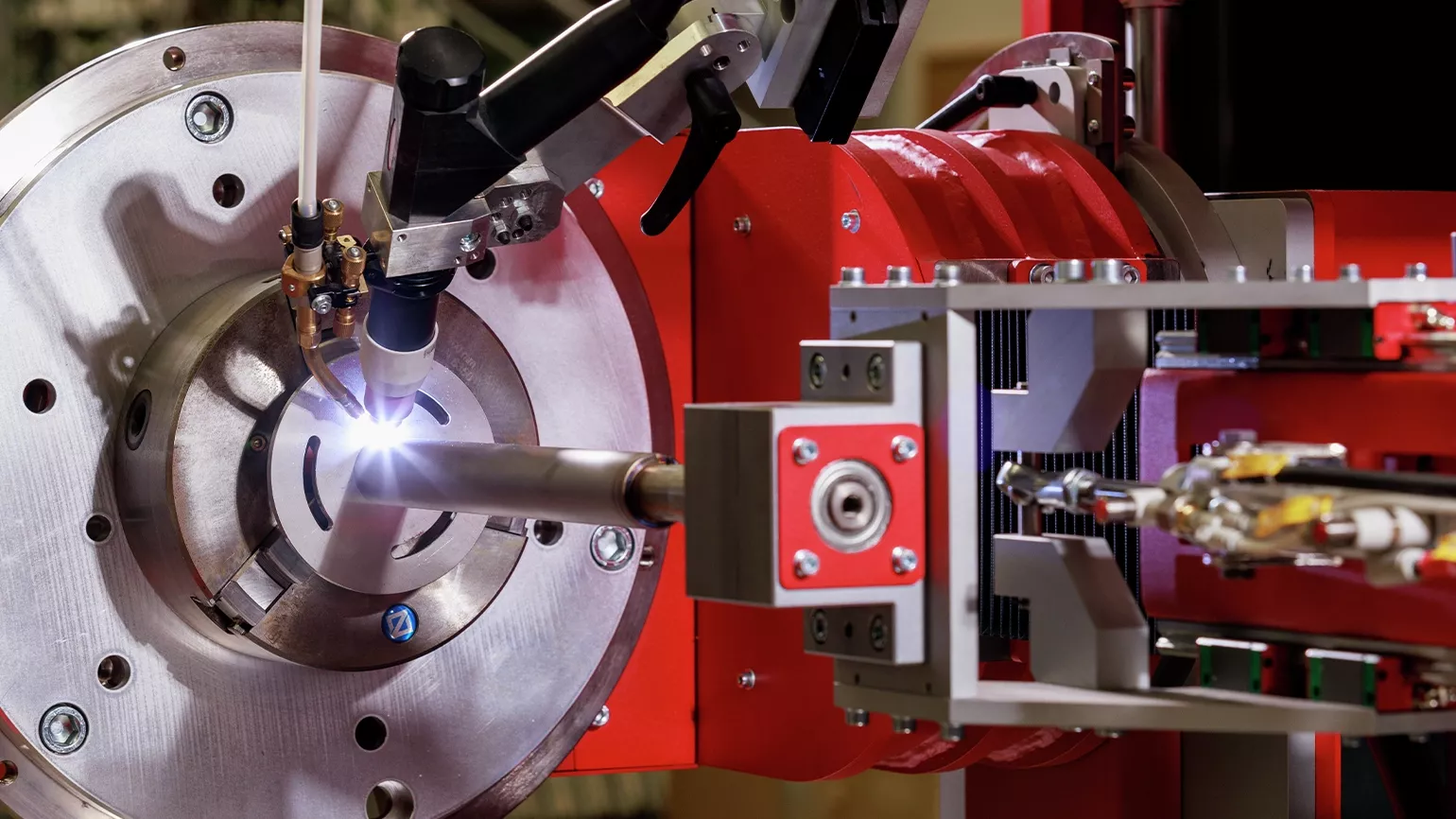
We have the right welding system for every application. Our solutions are the ultimate in precision and efficiency, meeting the full scope of requirements for quality and reliability in tank, vessel, and pipeline construction in particular.
We also offer custom solutions that stand up to any challenge. Working with our mechanized circumferential welding systems, you can weld components of very different sizes and weight classes—thanks to systems ranging from compact welding cells for smaller components through to robust systems for heavy workpieces.
Cutting-edge technology and premium materials deliver top results, making our welding systems incredibly versatile, simple to use, and easy to maintain. Even welds, high process stability, and less rework are just a few of the advantages—and you can benefit too.
Applications
Cylindrical vessels and components are used in many different industries, e.g., for storing liquids or processing bulk materials.
The modular design of our circumferential welding systems makes them an ideal solution for components with a diameter of 50 mm to 6 m and length of up to 25 m.
Base materials:
Steel, stainless steel, aluminum, duplex, nickel-based alloys
Industries:
- Pipeline and vessel construction
- Mechanical and equipment engineering
- Food, chemical, and pharmaceutical industries, etc.
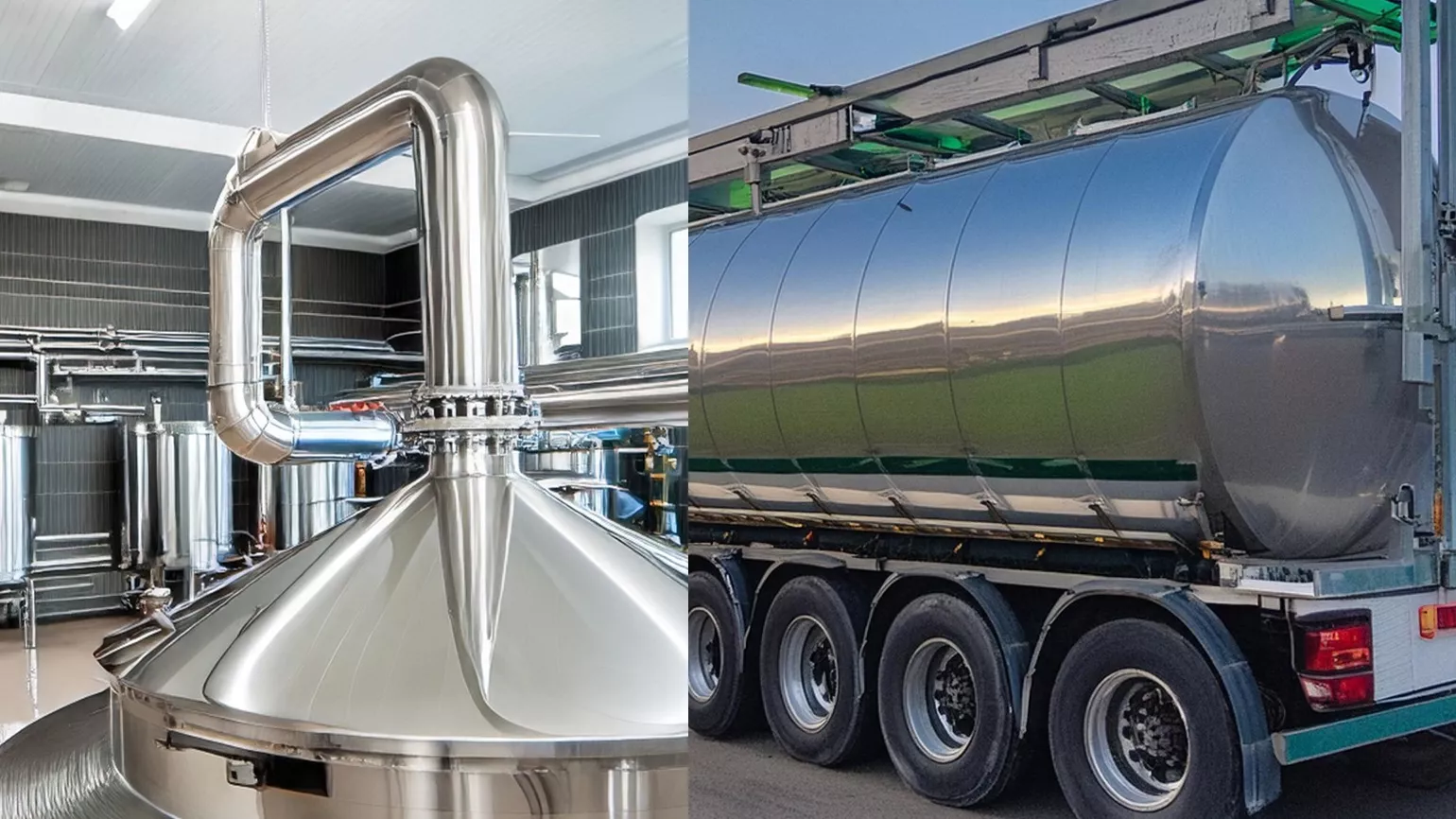
Select the right system for your application
FCW Smart—a cobot isn’t always a must
The advantages for you:
/ Low investment costs
/ Simple, user-friendly operation and programming
/ Motorized welding torch axes (AVC/OSC)
/ CE-compliant safety housing with automatic glare protection
/ Multiprocess
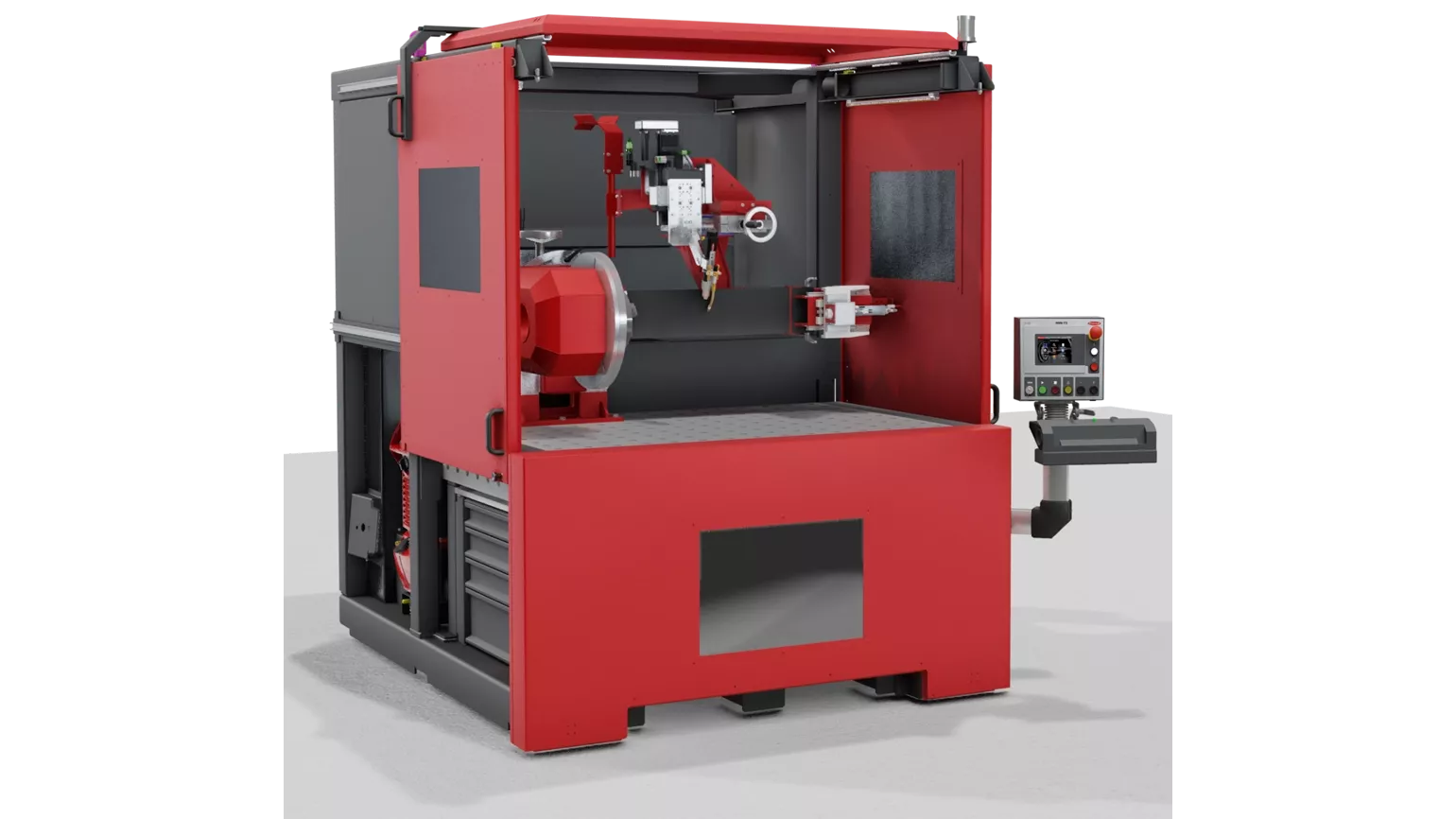
FCW Smart Lean variant
The advantages for you:
/ Cost-optimized solution
/ Little space needed
/ Simple, user-friendly operation and programming
/ Motorized welding torch axes (AVC/OSC)
/ Multiprocess
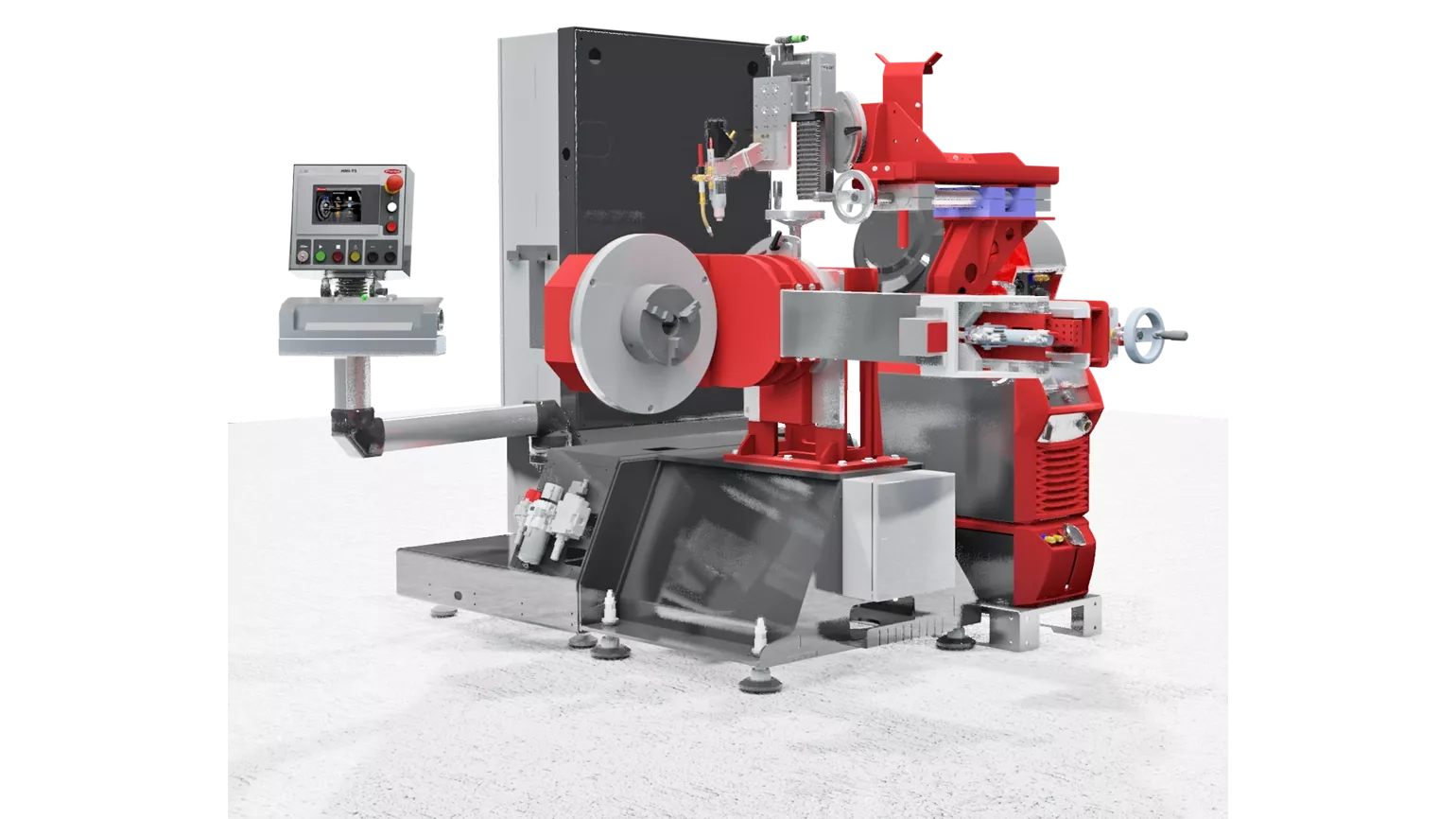
System overview
FCW Compact
Efficient welding for a wide range of applications
Versatile functions paired with a compact design: our FCW Compact circumferential welding system is the perfect solution for vessel and pipeline construction. The system takes up very little space, making it a precise and efficient choice for welding different components such as pipes, flanges, and vessels.
The advantages for you
/ Versatility: The FCW Compact is designed as a modular welding system that can take on a wide range of jobs. From MIG/MAG, CMT, and TIG through to ArcTig and plasma, this system supports many different welding processes.
/ Compact design: Despite offering a wealth of functions, the FCW Compact takes up very little space. It can be configured for component lengths up to 6 m and component diameters up to 800 mm.
/ Second welding head unit as an optional extra: The FCW Compact system can be equipped with a second, independently controlled welding head unit to make work even more flexible.
/ Tailstock with electropneumatic clamping system: The tailstock fixes components securely in place during the welding process.
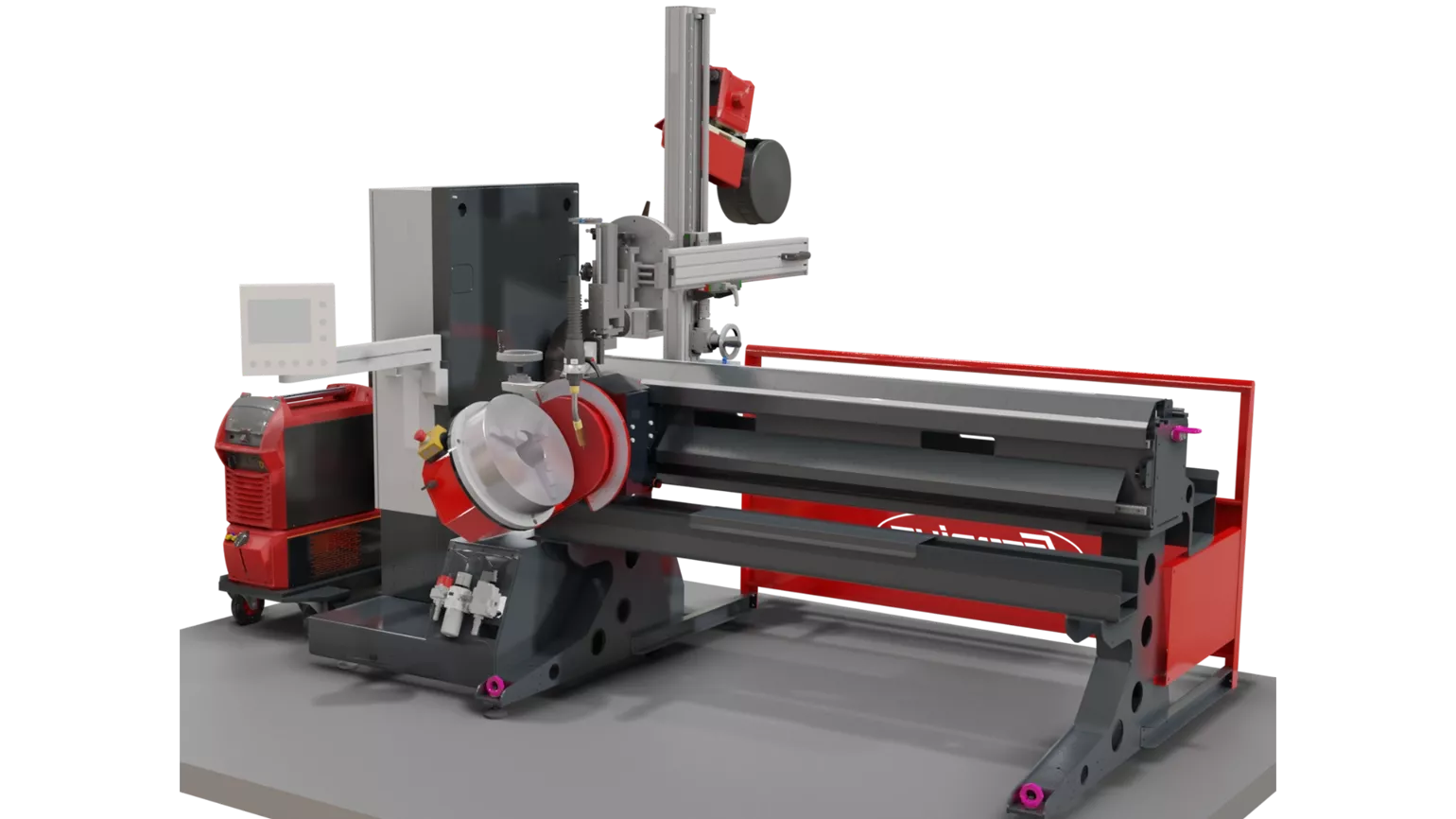
Modular concept
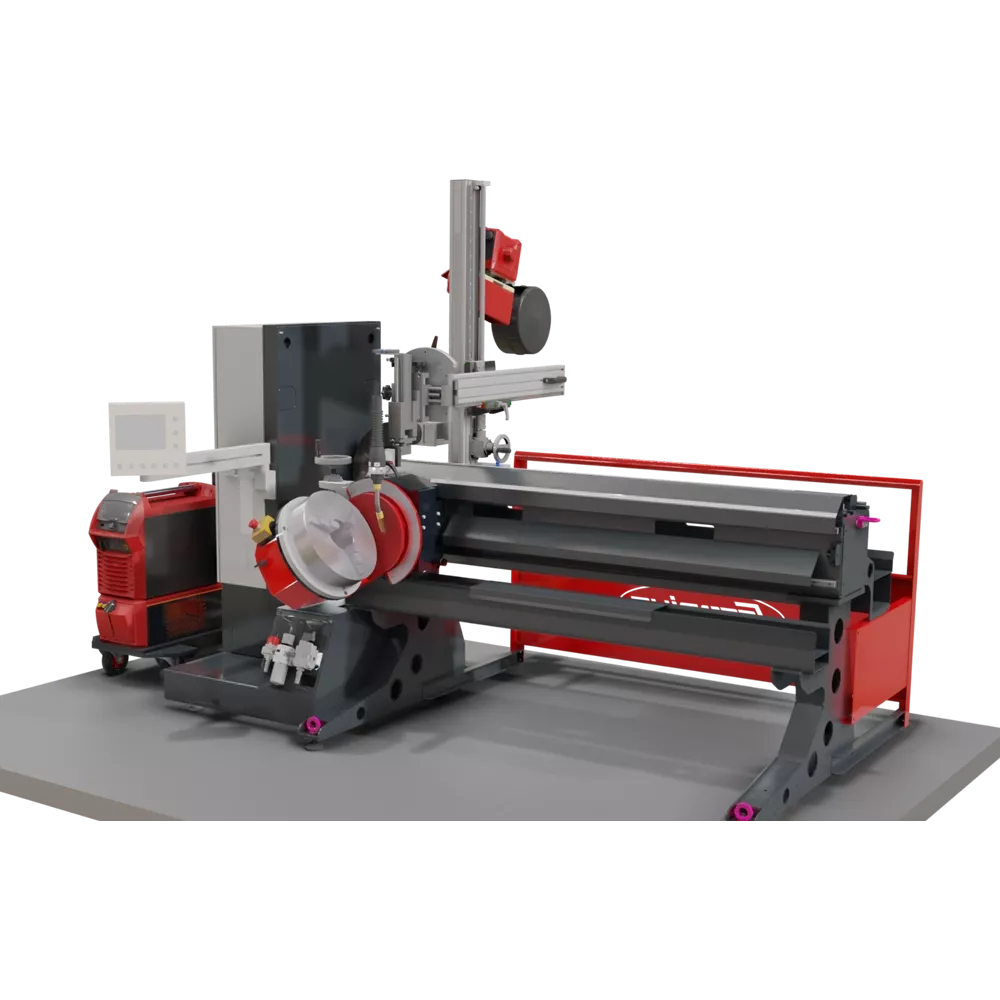
FMW – Multi welding system
Our Multi welding system makes it possible to combine universal welding applications in a single system. Different welding processes are also available on an individual basis and new processes can be added as required. Our Multi welding system is the number one choice in sectors where different types of components (pipes, flanges, reducers, fittings, valves, etc.) and different metal alloys play a significant role, such as the food, plant construction, and energy technology industries.
In addition to the intuitive HMI, the Multi welding system lets you switch between welding processes in next to no time. Equipped with quick-release fasteners, welding torches can also be changed in seconds. Developing customer-specific sequence controls and programming the welding process has never been so easy, both saving time and opening up completely new possibilities.
The advantages for you
/ Modular design: Fronius put a great deal of thought into the concept behind the Multi, with its highly modular design allowing the welding system to be adapted perfectly to suit customers’ needs. Components with a diameter of up to 1,200 mm and length of up to 12 m can be welded without any difficulty.
/ Freely configurable: Choose between six different sizes to suit the dimensions of the components. A selection of rotating units and manipulators makes every system an individual customer solution.
/ Wide range of welding processes: Depending on the application, you can also choose from a range of suitable welding processes (TIG cold wire, TIG hot wire, ArcTig, plasma, MIG/MAG, CMT, etc.).
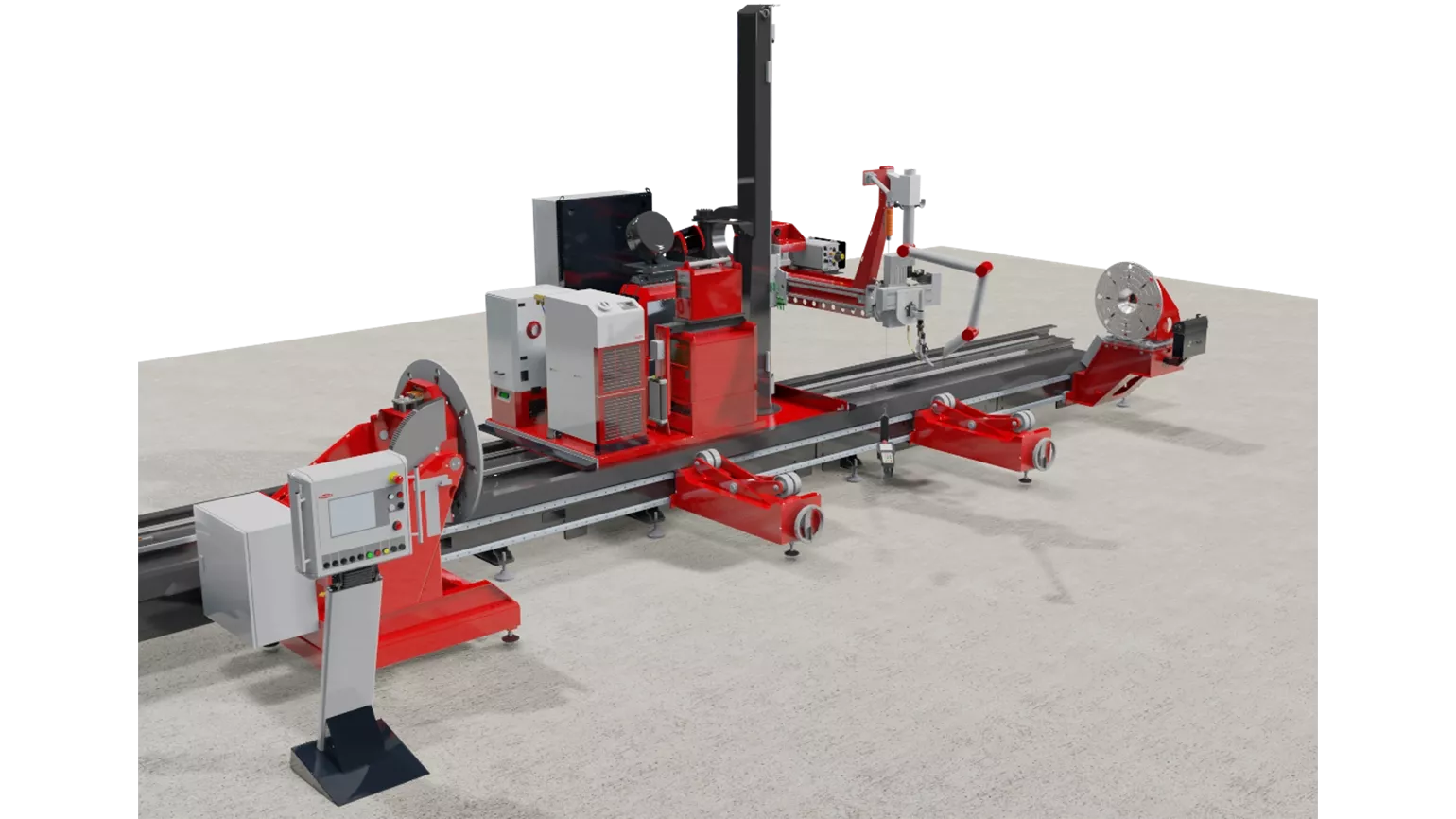
System overview
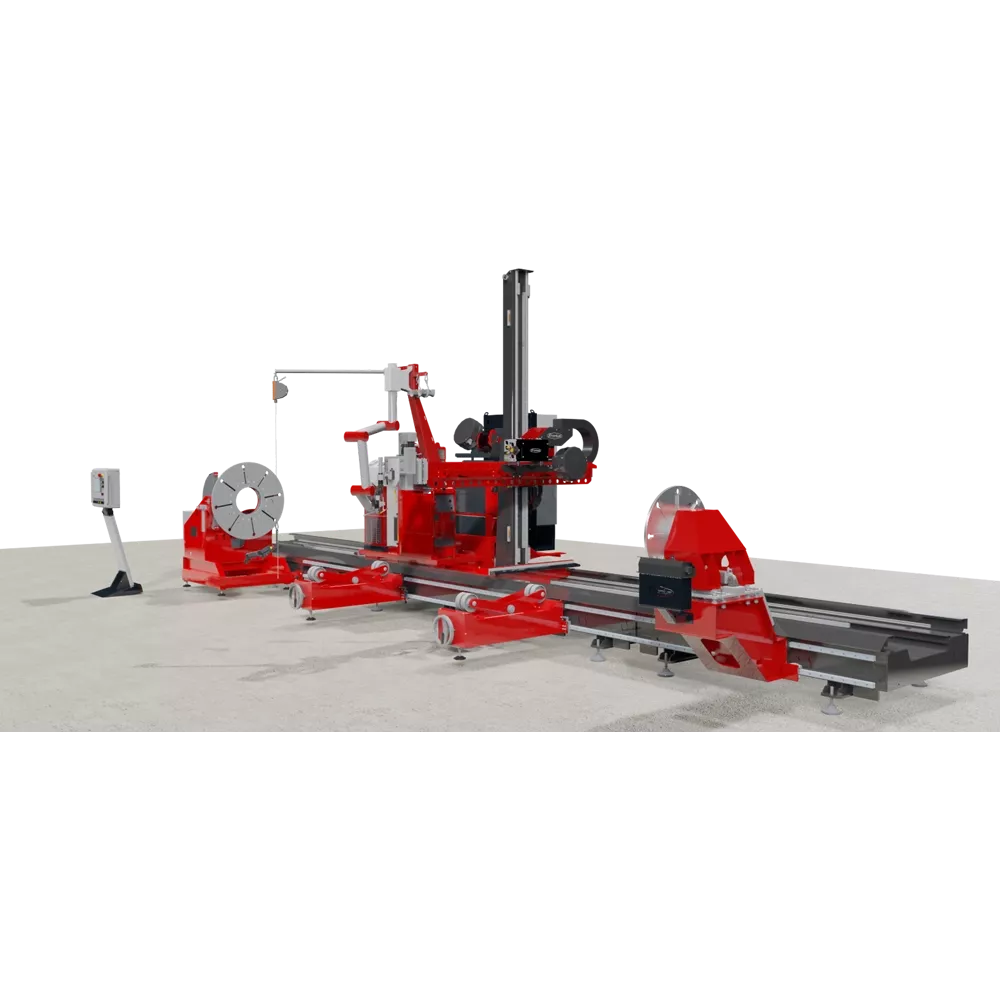
FCW Heavy
Modular system concept
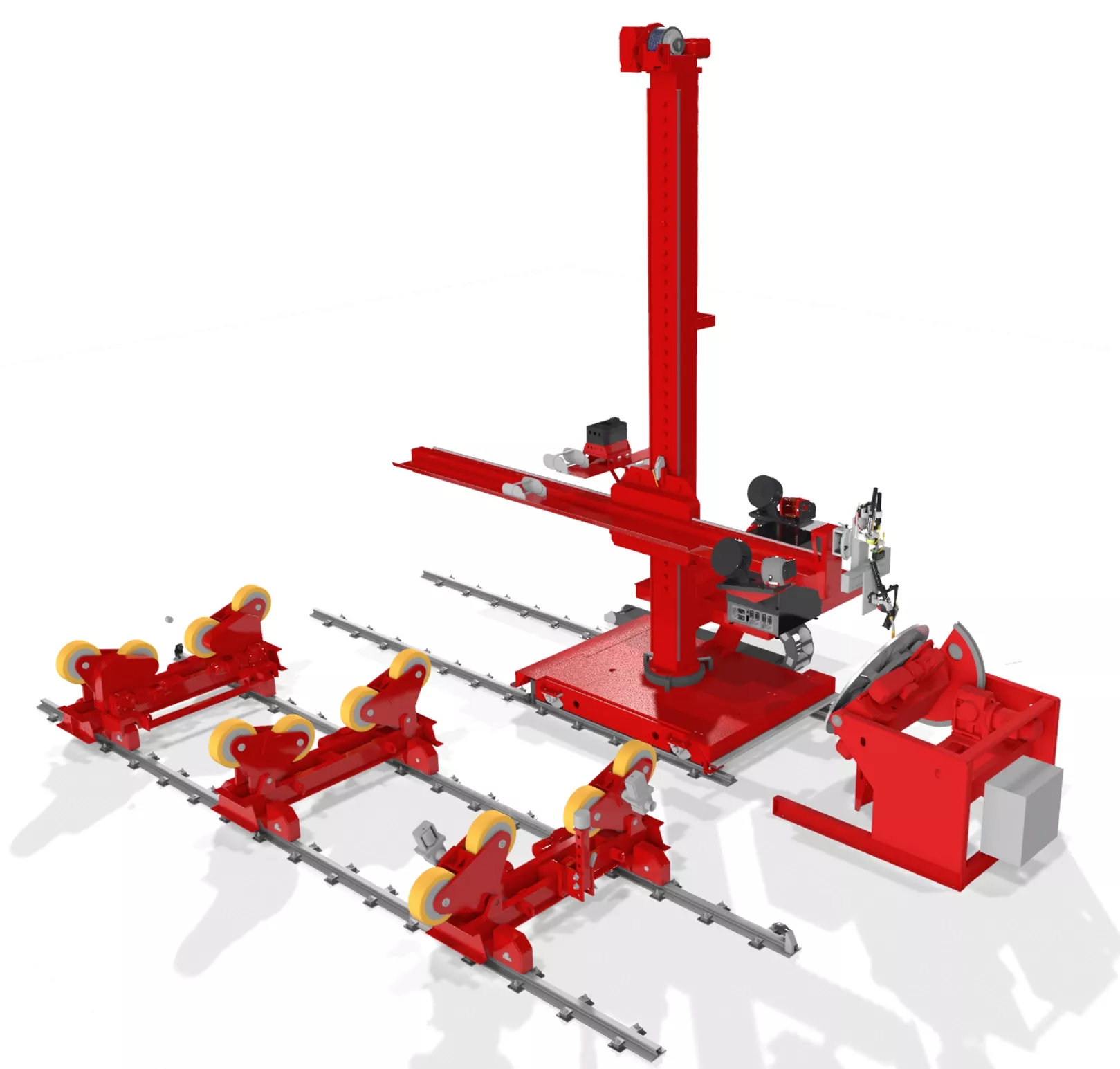
Precisely tailored to your application:
A wide range of standardized components enables versatile solutions. Read on for a few practical examples:
FCW Heavy Stationary
Application
Welding components in the PC position (e.g., CrNi vessels in the food industry)
Configuration
/ Permanently mounted machine carrier
/ Horizontal rotary table
/ Motorized carriage for welding torch positioning
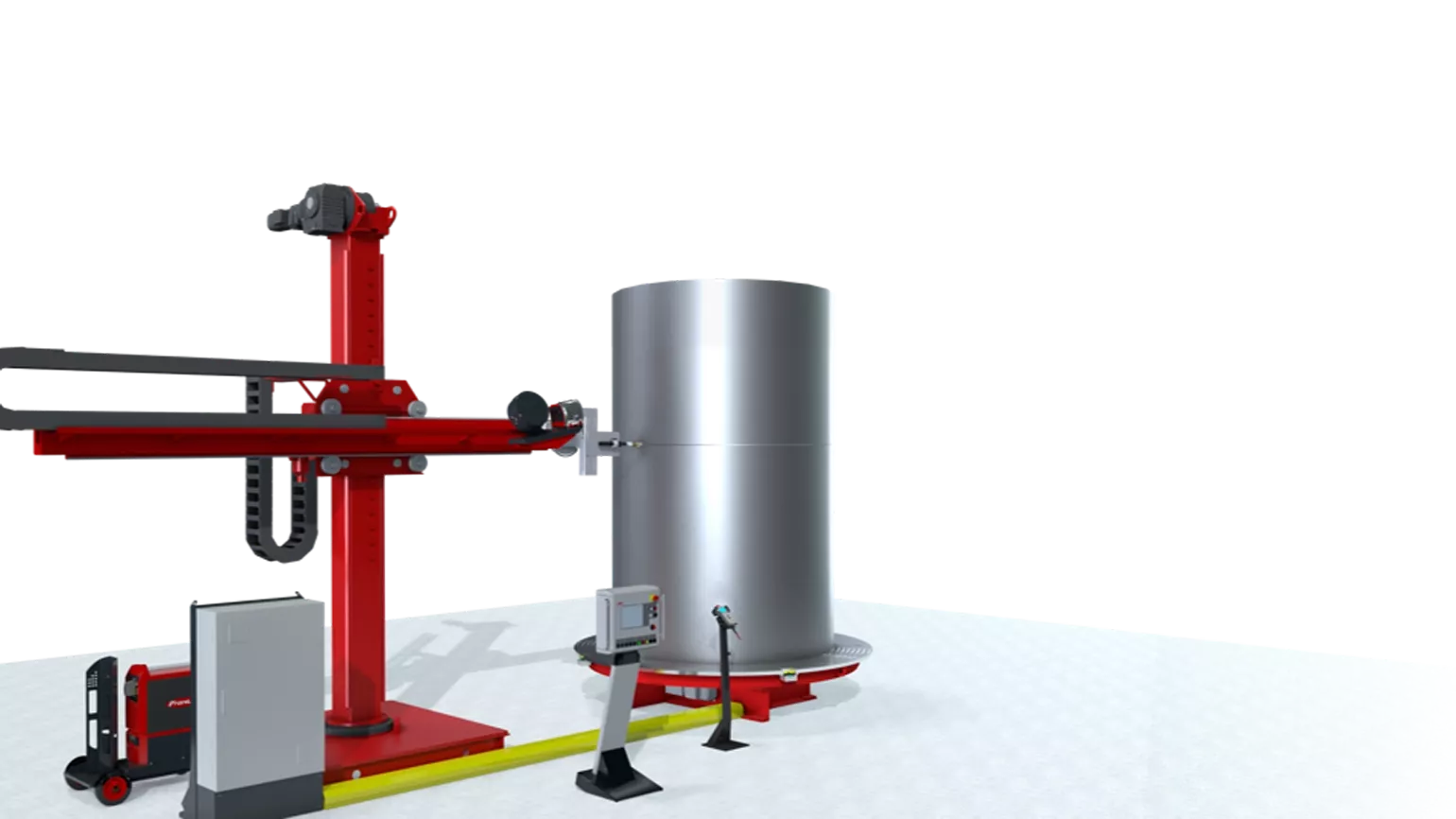
FCW Heavy Motion
Application
Welding vessels and fixtures in the PA/PB position
Configuration
/ Column and boom with motorized base on rails
/ Movable roller blocks on rails
/ Welding head with motorized horizontal/vertical carriage
/ Tactile seam tracking system
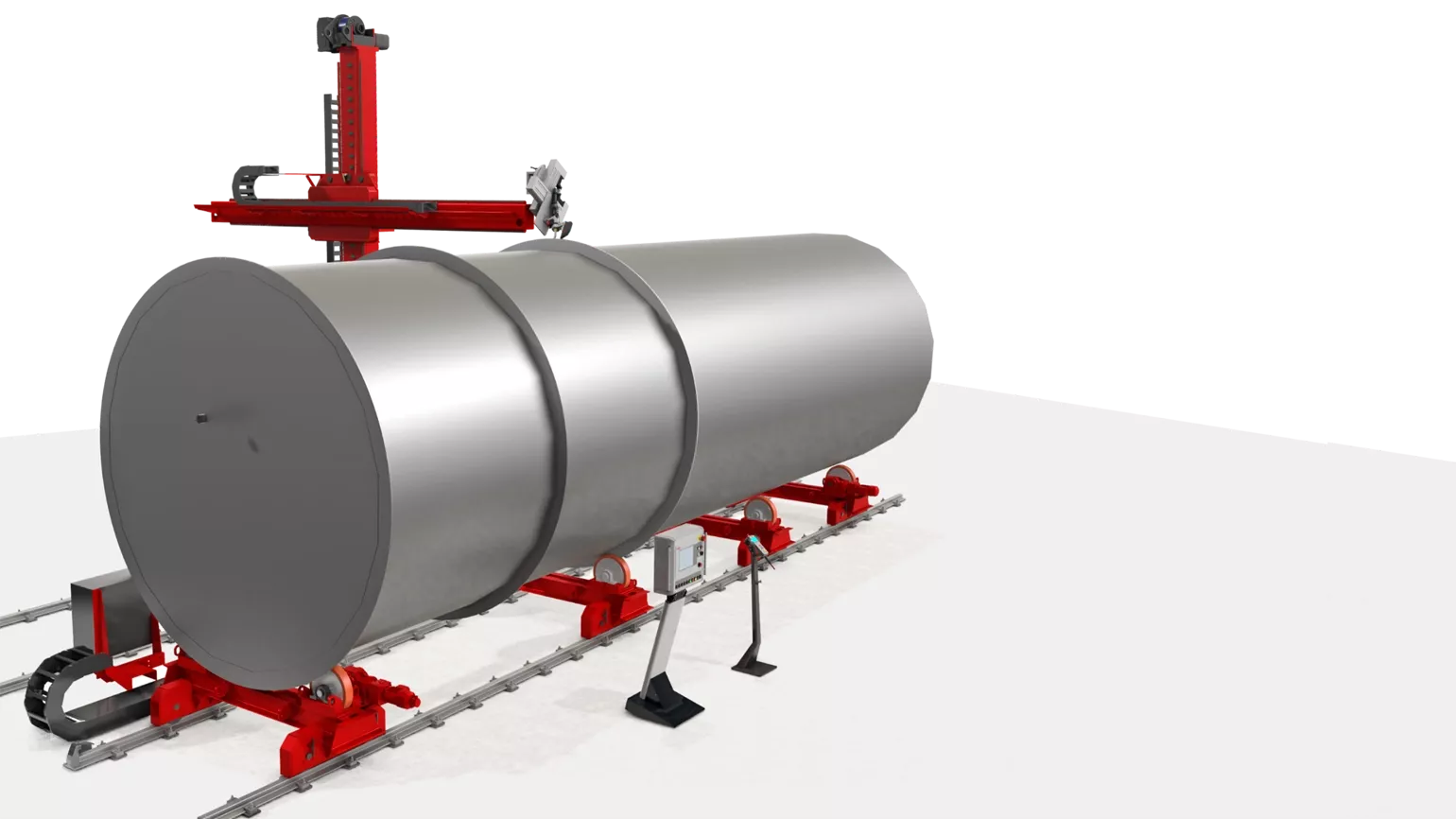
FCW Heavy Extended
Application
Dual-station operation for final assembly of vessels and fixtures (pipe-flange connections)
Configuration
/ Column and boom with motorized base on rails
/ Movable roller blocks on rails
/ Turn/tilt positioner
/ Welding head with motorized horizontal/vertical carriage and torch change system
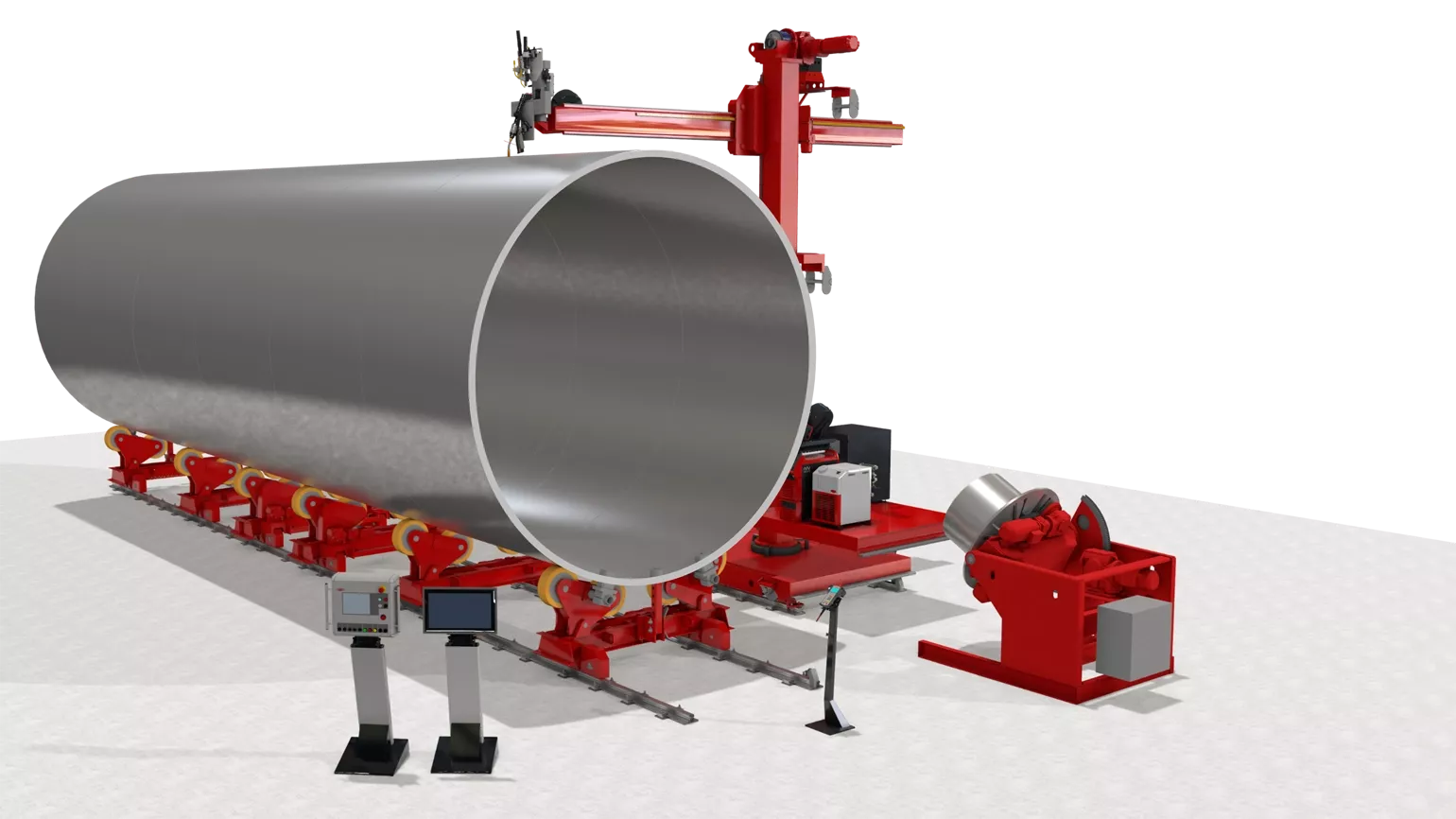