Our TPS/i TWIN Systems
Intelligent Tandem Welding
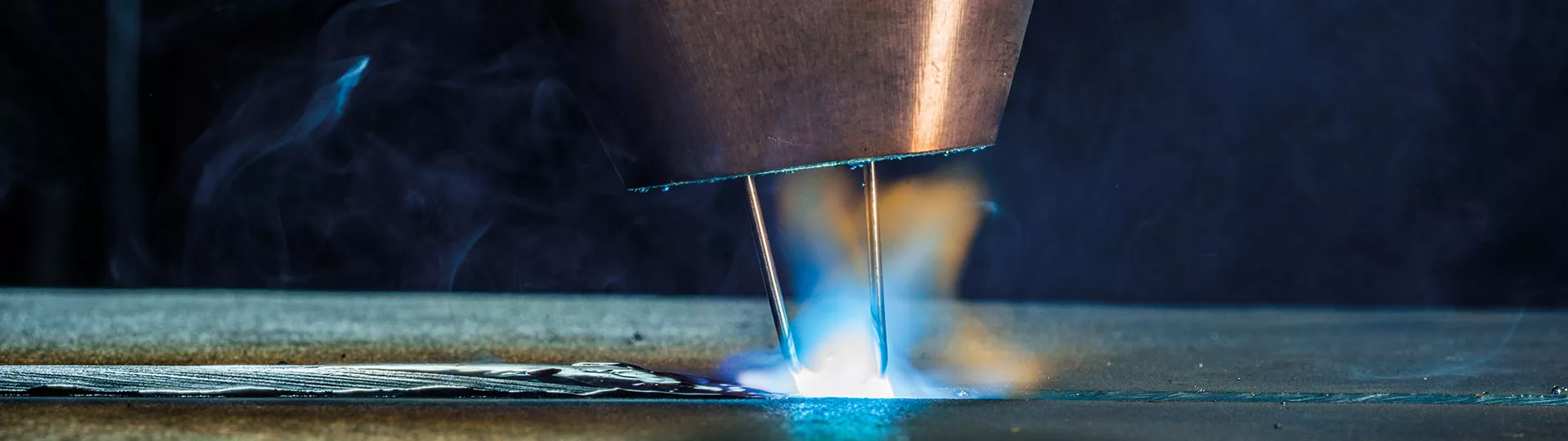
Tandem welding has never been so easy
Consistently high welding speed with reliable penetration and deposition rates of up to 25 kg/h—our TPS/i TWIN systems have got you covered.
Our newest development with intelligent welding processes that automatically adjust welding parameters and welding variables in the background provide maximum control and time savings—supported by robot assistance systems and automatic change and cleaning systems.
TPS/i TWIN systems are adapted to the respective application area on a modular basis. Whereas a push system is the ideal solution for steel applications, a PushPull solution is recommended for aluminum. If you want to achieve the absolute maximum when it comes to welding speed and process stability, look no further than the CMT TWIN process.
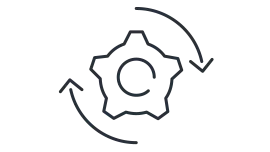
Self-regulating process
Only adjust the most necessary aspects
Achieve better results automatically: During the welding process, our system regulates the welding parameters and welding variables independently in the background to keep both arcs perfectly regulated at all times.
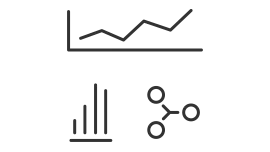
Smart assistance systems
Support that saves you time
TeachMode, TouchSense, SeamTracking, WireSense and short circuit detection within the gas nozzle: Our assistance systems simplify handling of the welding system and thereby increase welding efficiency.
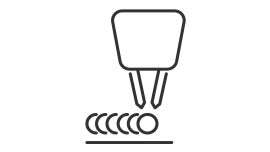
High deposition rate
Up to 25 kg/h
Processing large, heavy components has never been easier. This is possible thanks to the power of 2 TPS/i power sources in one system, leading to particularly high deposition rates and excellent gap-bridging ability.
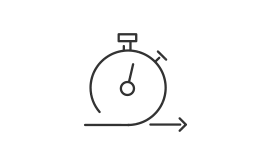
High-speed welding
Welding speeds of up to 4 m/min
Fast welding without loss of quality: This is par for the course owing to the high deposition rate—just like the reliable penetration and notch-free welds.
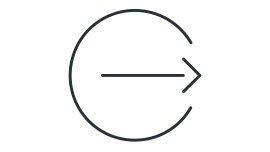
Totally stable welding
Continuous production with a long service life
High level of process reliability thanks to reliable wirefeeding. The highly dynamic TWIN Drive unit and wire buffers ensure, amongst other things, maximum stability.
Downloads
TWIN systems at a glance
TWIN PUSH | TWIN PUSH/PULL | CMT TWIN |
Welding process: PMC TWIN Field of application: Steel Typical welding tasks: Axles, rims, bogie frames and steel beams |
Welding process: PMC TWIN Field of application: Aluminum Typical welding tasks: Aluminum profiles, carriage construction, containers, pressure vessels, tanks |
Welding process: CMT TWIN and PMC TWIN Field of application: Light gage sheet, aluminum, nickel-based alloys, high-strength steel Typical welding tasks: Axle production, exhaust systems, hydraulic cylinders, mobile crane booms, pressure vessels |
System design
The TWIN welding processes
PMC TWIN
PMC (Pulse Multi Control) is a further development of the pulsed arc from Fronius. It provides the technological basis for the PMC TWIN process and is available with different characteristics as is typical from Fronius.
As a result, the right process properties can be accessed directly depending on the application scenario.
Reliable penetration
Achieve the desired weld quality with maximum reliability:
With the TWIN process, even greater penetration is achieved despite its tremendous speed.
High deposition rate
One weld is enough: Thanks to the high deposition rate of the TWIN system, welds that require multiple layers are a thing of the past.
CMT TWIN
CMT (Cold Metal Transfer) is a welding process developed by Fronius that provides the technological basis for the CMT TWIN process.
By combining different processes, benefits such as high speed, a gap-bridging ability and few spatters are brought together in one process. The process is also available with different characteristics to ensure users have the right process properties for their application at their fingertips.
Achieve the perfect result at top speed
Reliable penetration without notches: Thanks to the high deposition rate, the tandem process enables speeds of up to 330 cm/min. This allows you to weld 2.5 times faster than with just one arc.
Gap-bridging ability
Four times the welding speed and optimal gap-bridging ability with TWIN welding despite a 3 mm gap!