CMT
Cold Metal Transfer
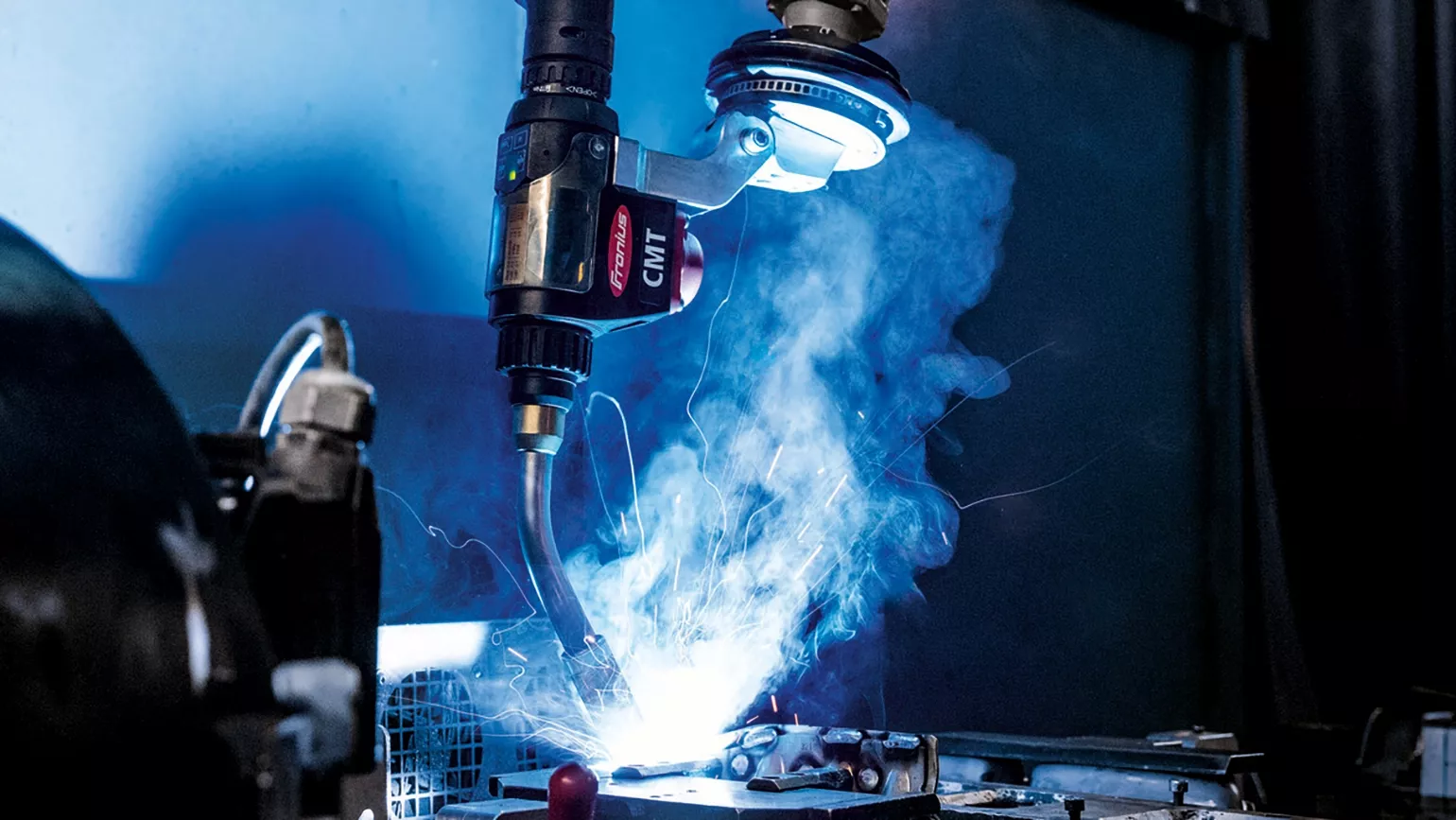
CMT welding process: the most advanced type of droplet detachment
High-speed, low-heat input, virtually spatter-free welding
Wherever adhesive or solder was used before, CMT (Cold Metal Transfer) welding can be used instead. CMT has revolutionized welding technology and expanded the range of possible applications with its reversing wire movement.
The back and forth movement (reversing) of the welding wire—at up to 170 Hertz—produces an exceptionally stable arc. This results in a 33% reduction in heat input and a welding speed almost twice as fast as with conventional dip transfer arc.
The advantages for you
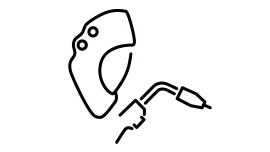
Less rework
/ 99% less spatter*
/ 33% less heat input reduces distortion
/ Spatter-free ignition (SFI)
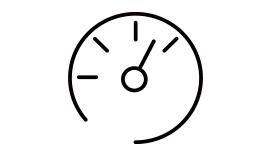
100% higher speed**
/ Same penetration at high speed
/ Fast joining of thin sheets
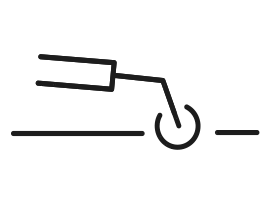
Stable arc
/ 100% CO2 welding
/ Also for high-strength steels
/ Not susceptible to external influences (changes in stickout or workpiece surface)
*Under laboratory conditions
**Compared with standard dip transfer arcDownloads
Special features of CMT
During welding, the wire moves forward and is pulled back again as soon as the short circuit occurs. As a result, the arc only introduces any heat for a very brief period during the arc-burning phase. The result is spatter-free material transfer. The arc remains stable, regardless of the surface characteristics of the workpiece or how quickly the welding specialist works. This means that CMT can be used anywhere and in any position.
Welding does not inevitably have to mean welding spatter and rework. CMT promotes controlled droplet detachment during the short circuit, while the current is kept low. The result is virtually spatter-free material transfer.
*Compared with standard dip transfer arc
Heat input at the lowest level: as soon as the short circuit occurs, the wire is pulled back again during the CMT process. This means that the arc only introduces heat for a very short time.
As a result, CMT enables continuous regulation of the heat input from cold to hot. In addition, higher welding speeds and a wider range of applications* are possible with maximum weld quality.
* Compared with standard dip transfer arc
**1.5 mm steel plate FW, PB 1.5 mm steel plate FW-TJ PB
Result with standard dip transfer arc**
Result with CMT at 2x speed**
*Compared with standard dip transfer arc
**1.5 mm steel plate FW, PB 1.5 mm steel plate FW-TJ PB
Required hardware for CMT
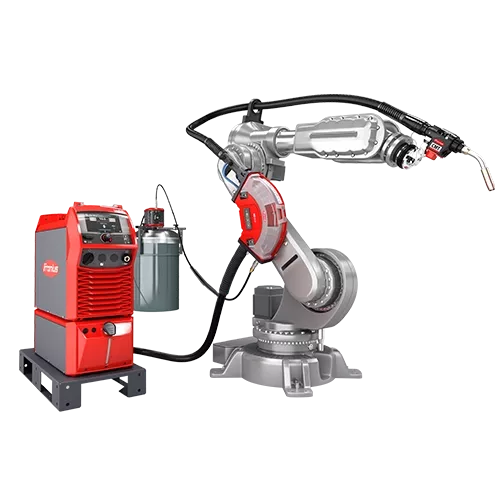
Applications
The CMT process is based on the most advanced type of droplet detachment, made possible by the reversing wire movement.
/ Joint welding (CrNi applications, food industry)
/ Overlay welding
/ Rapid prototyping and Fronius Additive
/ Brazing, specifically with high demands for speed and process stability
/ 100% CO2 welding on steel
/ Root passes
/ Thin and medium sheet range
/ Special joints, e.g., copper, steel aluminum, titanium
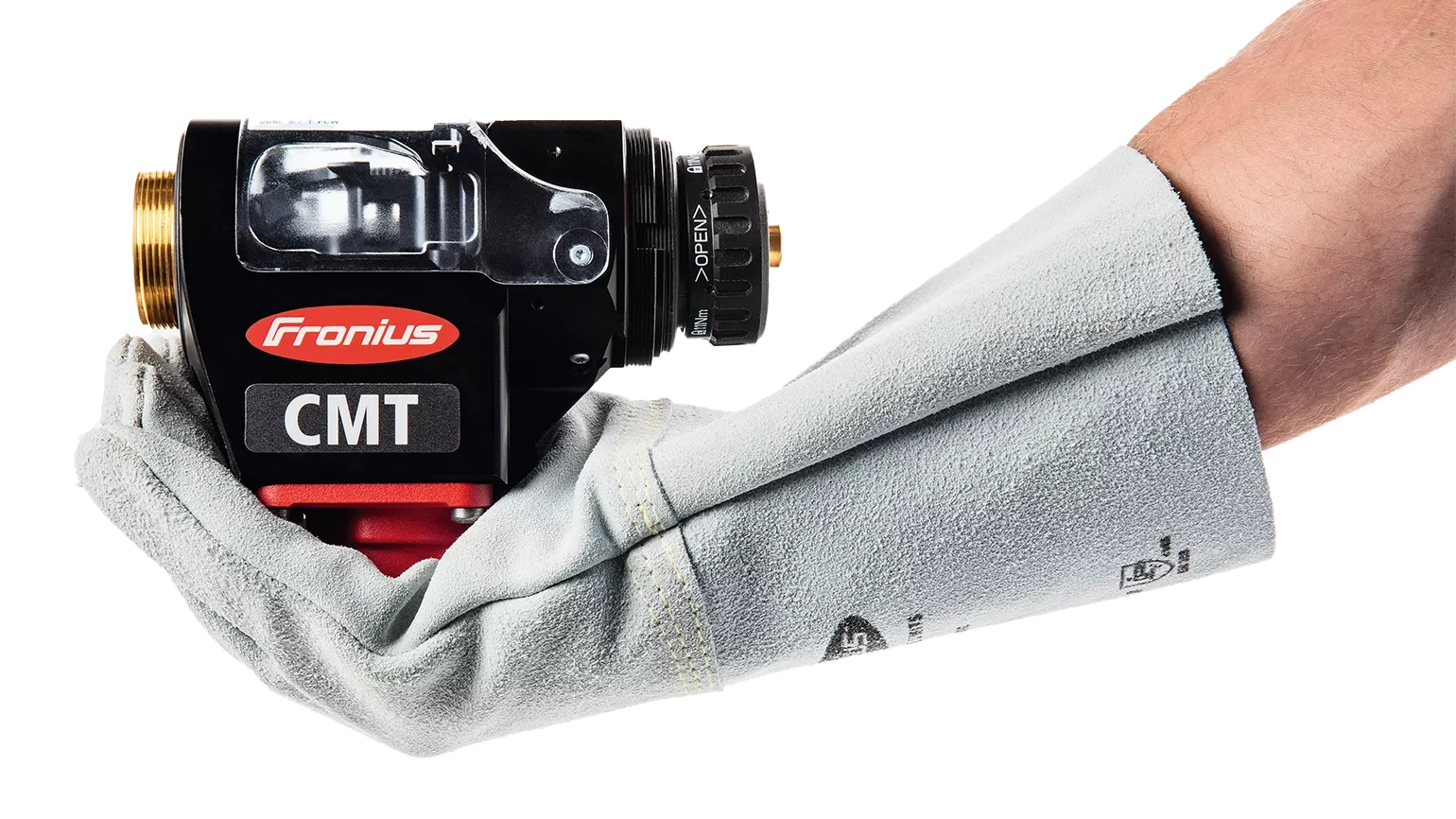
With the CMT welding process, we save several hundred hours of additional manual work each year. This also has a positive effect on our bottom line.
CMT characteristics
CMT AC
Reverse polarity of the wire electrode
The CMT AC process achieves a remarkably low heat input with the same deposition rate by reversing the wire movement and the polarity of the wire electrode. You can easily adjust the positive and negative components with the help of correction parameters and thus achieve extremely precise control over the heat input.
CMT AC is available on the iWave AC/DC with Multiprocess Pro.
The benefits
/ CMT AC is the process with the lowest heat input
/ Excellent gap-bridging ability
/ Ideal for additive welding
/ Highly controllable heat input, especially for additive manufacturing processes
/ Gleaming welds due to reduced magnesium oxides (for AlMg wires)
/ Process with the lowest welding fume emissions
CMT cladding: 75% less dilution of base and filler metals
In conventional overlay welding, the arc fuses a relatively large amount of the base material.
The typical dilution and mixing of base material with filler material reduces the corrosion resistance of the applied layer. However, the base materials are melted to a lesser extent due to the lower heat input of the CMT process. This results in up to 75% less metallurgical mixing of the base and filler materials, and reduces costs for overlay welding.
+ 50% welding speed
CMT Cycle Step
The welding specialist can therefore produce spots of any size and reproduce them precisely—a totally new level of control over the welding process.
Typical applications
- Visible seams with defined seam joining
- Welding of thin sheets with tolerances
- Fine overlay welding
- Additive welding applications
- Support for bonding processes with defined distances (distance points)
- Hold points for bonded joints
- Welding in any position
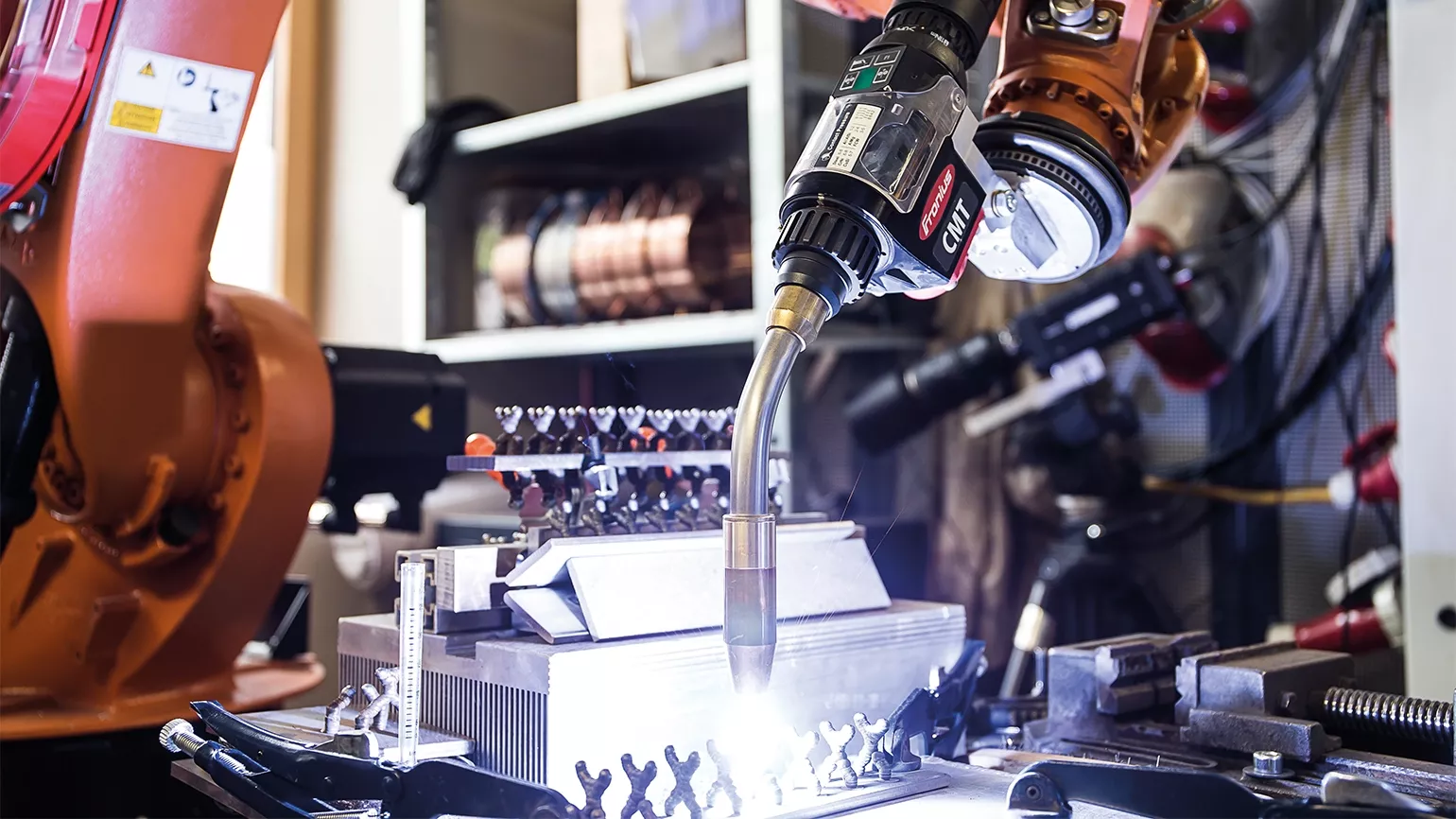
Heat input is also minimal with Cycle Step, and can be effectively controlled. This allows even the thinnest of sheets to be joined and is particularly useful for position welding with gap tolerances. The defined welding cycles also ensure flawless seams in terms of appearance, with clear rippling and without excessive spatter, making Cycle Step ideal for high-quality visible seams.
The differences
- Stitch welding is a time-based process with a defined welding time and pause time.
- CMT Cycle Step is a process based on “droplet numbers”—the number of cycles defines the welding time, followed by the pause time. The interval cycles can also be defined.
Since switching from the standard MAG process to CMT, there has been hardly any spatter to remove. This means that my staff has been able to focus entirely on what matters to our customers in the automotive industry: the quality of the weld.
Aluminum welding with CMT
An investment that pays for itself
Calculated per component, costs can be reduced by up to 43%*, so the higher investment costs involved with CMT are repaid in no time.
* In relation to the Standard Welding Package
Light gauge (≤ 1 mm) aluminum sheets can be welded.
The low heat input of this process means that weld-pool support isn't necessary to keep the weld from dropping through.
Advantages
/ Reduced investment in welding cells: better utilization and useful life of the cells, thanks to higher welding speeds
/ Less rework and fewer rejects thanks to the stable process and reduced spattering
/ Shorter maintenance operations, since contamination from spatter is kept to a minimum
/ Lower gas costs due to reduced welding time. Light gauge (≤ 1 mm) aluminum sheets can be welded.
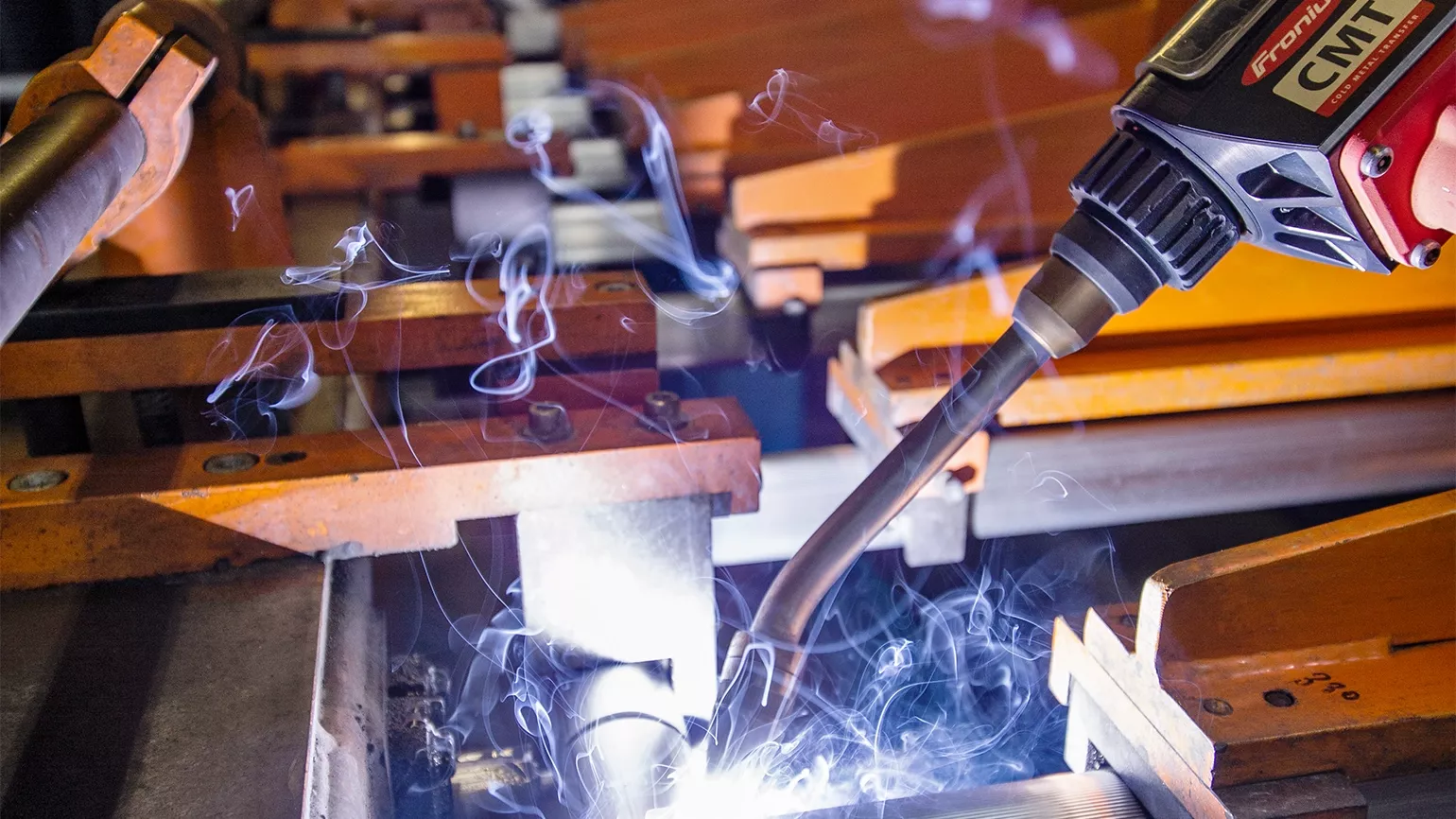
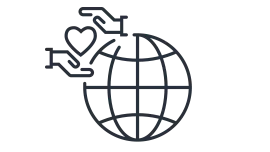
Resource-conserving
This precisely controlled process reduces spatter, and therefore rework, which lets employees work more efficiently.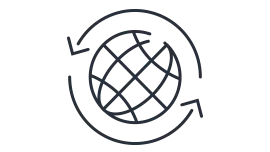
Material-saving
CMT significantly reduces the consumption of wear parts and the number of component rejects, which translates directly into greater savings potential.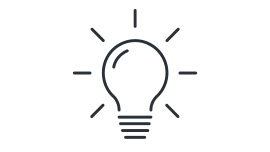